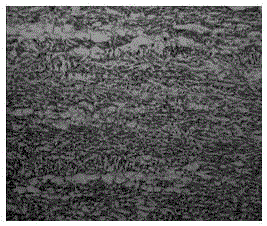
本發(fā)明涉及結(jié)構鋼及其生產(chǎn)方法,尤其涉及一種低屈強比Q550D低合金高強結(jié)構鋼及生產(chǎn)方法。技術背景屈強比,是指鋼材的屈服強度與抗拉強度的比值。該指標是衡量鋼材強度儲備的重要系數(shù)。通常,鋼鐵材料的屈強比較高時,表明該種材料的抗變形能力較強,不易在外力作用下發(fā)生塑性變形。因此可以在機械結(jié)構設計過程中節(jié)約材料、減輕結(jié)構的重量;但同時,材料抗外力沖擊的能力較差,發(fā)生脆性破壞的風險也較大,材料的可靠性也較低。鋼鐵材料的屈強比較低時,表明該種材料的塑性較好,具有較強的抗外力沖擊能力,材料的可靠性也較高。因此,為確保鋼鐵材料的可靠性,避免脆性斷裂事情的發(fā)生,國家對鋼鐵材料的屈強比有明確的要求,即:一般碳素鋼屈強比為0.6-0.65,低合金結(jié)構鋼為0.65-0.75。低合金高強結(jié)構鋼在煤炭行業(yè)應用廣泛。煤炭行業(yè)綜采設備主要包括“兩機一架”,即:采煤機、刮板運輸機和液壓支架。其中,液壓支架占煤炭綜采設備的比重近50%。據(jù)統(tǒng)計,一套中高端支架用鋼通常在4800~8800噸,其中,鋼板約占支架總重的90%。過高的設備重量,不利于現(xiàn)場生產(chǎn)的靈活組織,因此,為滿足生產(chǎn)現(xiàn)場靈活組織、調(diào)度的需要,很多大型煤炭機械制造企業(yè)根據(jù)現(xiàn)場實際,迫切要求鋼鐵企業(yè)提供屈服強度在550MPa以上且-20℃沖擊功滿足GB/T1591-2008要求的Q550D鋼種,確保生產(chǎn)出的液壓支架在滿足安全生產(chǎn)前提下,大幅降低支架用鋼量;同時,由于煤炭機械作業(yè)環(huán)境十分惡劣,要求Q550D鋼種兼具良好的抗沖擊性能和抗震性能。鋼材產(chǎn)品的力學性能主要取決于鋼中的組織構成,對于Q550D而言,為確保該鋼種的屈服強度和抗拉強度滿足GB/T1591-2008要求,就必須要確保鋼中的貝氏體和鐵素體比例。貝氏體是指過冷奧氏體在中溫范圍內(nèi)形成的由鐵素體和滲碳體組成的非層狀組織,該組織通常具有較高的力學強度,但韌性較差,在較大的外力沖擊下,容易發(fā)生斷裂。鐵素體是碳溶解在α-Fe中的間隙固溶體,該組織具有良好的塑性和韌性,但強度和硬度都很低,同時冷加工硬化緩慢,可以承受較大減面率的拉拔。因此,當鋼中的貝氏體含量較多時,鋼材主要體現(xiàn)出力學強度較大,但韌性較差的特點,屈強比偏高;反之,當鋼中的鐵素體含量較多時,鋼材主要體現(xiàn)出力學強度較小,但韌性較強的特點,屈強比偏低。鋼材產(chǎn)品較低的力學性能或較高的屈強比,都無法滿足煤炭機械制造用戶對于鋼材產(chǎn)品的要求。因此,只有合理控制鋼中鐵素體和貝氏體含量比例,才能確保Q550D產(chǎn)品的力學性能和屈強比均能夠滿足GB/T1591-2008和用戶的要求。目前,國內(nèi)許多鋼鐵企業(yè)已成功開發(fā)出Q550D低合金高強鋼系列產(chǎn)品。其主要做法是在冶煉過程中,向鋼中加入一定量的B元素,由于B是一種表面活性元素,能夠吸附在奧氏體晶界上,延緩γ→α的轉(zhuǎn)變,其在奧氏體晶界的偏聚阻礙鐵素體的形核而有利于貝氏體的形成。因此,B元素對鐵素體生成的延緩要比對貝氏體延緩大得多,相關鋼鐵企業(yè)正是利用B元素能夠有效提高鋼淬透性的特點,促進鋼中奧氏體向貝氏體的轉(zhuǎn)變,最大限度的提高Q550D內(nèi)部貝氏體組織含量,確保Q550D的力學強度。現(xiàn)有的Q550D產(chǎn)品雖然在力學性能方面已經(jīng)能夠完全滿足煤炭機械企業(yè)的要求,但相關產(chǎn)品的屈強比普遍在0.86~0.94范圍內(nèi),超出國家規(guī)定的0.65~0.75的范圍,無法滿足用戶要求。這是由于B元素雖然能夠有效提升鋼的淬透性能,但其作用機制卻十分復雜,對鋼板淬透性的作用也較難控制,不利于鋼中貝氏體和鐵素體含量比例的準確控制。根據(jù)試驗分析結(jié)果,鋼中的貝氏體含量往往能夠達到90%以上,導致鋼材力學強度偏大,韌性偏弱,屈強比較高。根據(jù)數(shù)值模擬及現(xiàn)場試驗的結(jié)果表明:當Q550D鋼鐵素體和貝氏體含量的比例達到0.10~0.35范圍時,能夠確保力學強度滿足GB/T1591-2008要求的前提下,屈強比有效降低到0.8以下。此外,通過實驗室研究還發(fā)現(xiàn):在鋼中不含B元素,以及在現(xiàn)有的Q550D成分體系下,如果要確保鋼中奧氏體向貝氏體的轉(zhuǎn)變,需要將鋼板溫度降低到530℃以下的同時,確保淬火冷速達到20℃/s以上。而鐵素體的開始轉(zhuǎn)變溫度在840℃以下,在700℃左右時將停止轉(zhuǎn)變,并且在不同冷速下,均可以實現(xiàn)奧氏體向該組織的轉(zhuǎn)變。因此,在鋼中不含B元素的前提下,如果能夠確保合適的鋼板溫度和足夠的淬火冷速,就能夠?qū)崿F(xiàn)對Q550D內(nèi)部貝氏體和鐵素體含量的有效控制,并最終滿足用戶對于該類產(chǎn)品力學性能和屈強比的雙重要求。技術實現(xiàn)要素:本發(fā)明所要解決的技術問題是提供一種低屈強比Q550D低合金高強結(jié)構鋼及其生產(chǎn)方法,該鋼種不加入B元素,通過在線調(diào)整開冷溫度和冷卻速度,實現(xiàn)鋼中鐵素體和貝氏體的含量比例在0.15~0.45范圍內(nèi),確保Q550D強度滿足要求的同時,屈強比控制在0.8以下,滿足用戶需求。解決上述技術問題的技術方案為:一種低屈強比Q550D低合金高強結(jié)構鋼,鋼中各元素質(zhì)量百分比Wt%分別為:C=0.04~0.09,Mn=1.40~1.70,Nb=0.040~0.065,Ti=0.010~0.030,Cr=0.15~0.30,Mo=0.15~0.30,Als≥0.015,其它為Fe和生產(chǎn)過程中不可避免的殘余元素和雜質(zhì)。上述的一種低屈強比Q550D低合金高強結(jié)構鋼,所述鋼中C元素優(yōu)選為:0.05~0.09Wt%;Mn元素優(yōu)選為:1.45~1.70Wt%;Nb元素優(yōu)選為:0.045~0.060Wt%。一種低屈強比Q550D低合金高強結(jié)構鋼的生產(chǎn)方法,包括鐵水預脫硫→轉(zhuǎn)爐冶煉→LF精煉→RH精煉→連鑄→加熱爐加熱→控制軋制→(DQ+ACC)冷卻工藝步驟;所述DQ+ACC冷卻工藝中,鋼板的開冷溫度為750~770℃,鋼板的終冷溫度為200~300℃,冷卻時間在30s以下。上述的一種低屈強比Q550D低合金高強結(jié)構鋼的生產(chǎn)方法,所述加熱爐加熱工藝中,板坯在加熱爐內(nèi)的加熱時間為4~5h,加熱終了時刻的表面溫度控制在1100~1190℃范圍內(nèi);所述控制軋制采用CR方式軋制,開軋溫度為930~1050℃,一階段終軋溫度>950℃,二階段開軋溫度≤920℃,二階段開軋時的待溫厚度為鋼板成品厚度的3倍以上,精軋累計壓下率≥66%,終軋溫度控制在800~860℃范圍內(nèi)。上述的一種低屈強比Q550D低合金高強結(jié)構鋼的生產(chǎn)方法,所述轉(zhuǎn)爐冶煉工藝中控制鋼中的氧含量在600ppm以下,控制出鋼下渣量在鋼水量的0.01%以下,確保鋼水的潔凈度;所述LF精煉工藝中精煉時間控制在35min以上,精煉結(jié)束前10~15min加入鈮鐵和鈦鐵合金進行微合金化,有效控制鋼中夾雜物級別總和不超過1.5級;所述連鑄工藝中鋼水過熱溫度控制在10~35℃范圍內(nèi),拉速全程控制在0.8~1.0m/min范圍內(nèi);鑄坯下線堆垛緩冷處理。本發(fā)明之所以不向鋼中加入硼鐵合金,主要基于以下考慮:向Q550D中加入定量的硼鐵合金,是為了充分利用B元素能夠有效提高鋼淬透性的特性,即:B是一種表面活性元素,能夠吸附在奧氏體晶界上,延緩γ→α轉(zhuǎn)變的作用,其在奧氏體晶界的偏聚阻礙鐵素體的形核而有利于貝氏體的形成;因此,該元素對鐵素體生成的延緩要比對貝氏體延緩大得多、相關鋼鐵企業(yè)正是利用B元素的這一特點,最大限度的確保Q550D內(nèi)部形成足夠的貝氏體組織,提升Q550D的強度。但是,研究表明:B元素在鋼中的溶解度雖然較低,作用機制卻十分復雜,對鋼板淬透性的作用也較難控制,不利于Q550D最終穩(wěn)定比例鐵素體和貝氏體復相組織的獲得。本發(fā)明利用冷速的控制,彌補不添加B造成的鋼板淬透性不足的問題,實現(xiàn)精準控制Q550D內(nèi)部組織的含量比例,進而獲得優(yōu)異的屈強比。本發(fā)明為確保鋼板力學性能滿足GB/T1591-2008的要求,采用了控制軋制+(DQ+ACC)冷卻的工藝流程,各工藝流程的參數(shù)設定范圍主要是在參照相關冶金原理的基礎上,通過大量現(xiàn)場試驗得到的,分析如下:a、將板坯經(jīng)加熱爐加熱之后的表面溫度控制在1100~1190℃之間可以降低加熱過程中氧化鐵皮的產(chǎn)生,便于除鱗箱除鱗;而且在此溫度范圍內(nèi),原始奧氏體晶粒尺寸不會急劇長大,便于細化晶粒;b、第一階段軋制溫度控制在950℃以上是為了保證鋼板的變形在奧氏體再結(jié)晶溫區(qū)進行,通過反復再結(jié)晶細化晶粒;將二階段的開軋溫度定在920℃以下是為了保證其變形是在未再結(jié)晶溫區(qū)內(nèi)進行,從而避開部分再結(jié)晶溫區(qū),減少混晶現(xiàn)象;控制鋼板二階段軋制時的厚度為成品厚度的3倍以上,便可以獲得累積壓下率≥66%,以此獲得足夠的相變形核點(位錯)和驅(qū)動力(變形能);終軋溫度控制在800~860℃可以保證鋼板在較低的溫度下進行變形,減少高溫階段發(fā)生的回復等降低位錯密度的現(xiàn)象;而且在此終軋溫度條件下鋼板進入(DQ+ACC)設備進行控制冷卻時的溫度可以控制在750℃~770℃(大約為此鋼的Ar3點附近),此時鋼板的組織主要仍為奧氏體,并生成含量為15%~30%的鐵素體組織,從而為確保Q550D的低屈強比性能創(chuàng)造有利的條件。c、實際生產(chǎn)說明鋼板出ACC時的終冷溫度控制在200~300℃附近,此時,鋼板內(nèi)部剩余的奧氏體組織轉(zhuǎn)化為貝氏體組織,鋼中最終的組織構成為鐵素體+貝氏體,鐵素體與貝氏體的比值控制在0.2~0.43,可以保證鋼板的強度符合國標要求的前提下,屈強比穩(wěn)定控制在0.8以下。本發(fā)明的有益效果為:本發(fā)明低屈強比Q550D低合金高強結(jié)構鋼,通過合理的成分設計,消除了B元素對鋼基體的不良影響,在保證強度的前提下,采用純凈鋼水、優(yōu)化控溫軋制及(DQ+ACC)控制冷卻工藝,得到理想的F+B組織及配比,且晶粒均勻細小,力學性能滿足GB/T1591-2008的要求,同時相關產(chǎn)品屈強比穩(wěn)定控制在0.8以下,滿足煤炭機械制造用戶要求,在同類企業(yè)中具有較強的競爭優(yōu)勢。附圖說明圖1為實施例1所生產(chǎn)的Q550D的500×顯微組織圖;圖2為實施例2所生產(chǎn)的Q550D的500×顯微組織圖;圖3為實施例3所生產(chǎn)的Q550D的500×顯微組織圖;圖4為實施例4所生產(chǎn)的Q550D的500×顯微組織圖;圖5為實施例5所生產(chǎn)的Q550D的500×顯微組織圖;圖6為實施例6所生產(chǎn)的Q550D的500×顯微組織圖。具體實施方式本發(fā)明一種低屈強比Q550D低合金高強結(jié)構鋼,鋼中各元素的質(zhì)量百分含量Wt%分別為:C=0.04~0.09,優(yōu)選0.05~0.09;Mn=1.40~1.70,優(yōu)選1.45~1.70;Nb=0.040~0.065,優(yōu)選0.045~0.060;Ti=0.010~0.030;Cr=0.15~0.30;Mo=0.15~0.30;Als≥0.015;其它為Fe和生產(chǎn)過程中不可避免的殘余元素和雜質(zhì);本發(fā)明一種低屈強比Q550D低合金高強結(jié)構鋼的生產(chǎn)方法,采用鐵水預脫硫、轉(zhuǎn)爐冶煉、LF精煉、RH精煉、連鑄、加熱爐加熱、控制軋制、(DQ+ACC)冷卻工藝步驟,其中:轉(zhuǎn)爐冶煉工藝中控制鋼中的O含量在600ppm以下,控制出鋼下渣量在鋼水量的0.01%以下,確保鋼水的潔凈度;LF精煉工藝中精煉時間控制在35min以上,精煉結(jié)束前10~15min加鈮鐵和鈦鐵進行微合金化,有效控制鋼中夾雜物級別總和不超過1.5級;連鑄工藝中鋼水過熱溫度控制在10~35℃范圍內(nèi),拉速全程控制在0.8~1.0m/min范圍內(nèi);鑄坯下線堆垛緩冷處理;板坯在加熱爐內(nèi)的加熱時間為4~5h,加熱終了時刻的表面溫度(出爐溫度)控制在1100~1190℃范圍內(nèi);控制軋制工藝中采用CR方式軋制,開軋溫度為930~1050℃;一階段終軋溫度>950℃;二階段開軋溫度≤920℃,二階段開軋時的待溫厚度為鋼板成品厚度的3倍以上,精軋累計壓下率≥66%,終軋溫度控制在800~860℃范圍內(nèi);采用DQ(直接淬火)+ACC(快速冷卻)冷卻方式控制冷卻,鋼板的開冷溫度為750~770℃,鋼板的終冷溫度為200~300℃,冷卻時間在30s以下。以下通過具體實施例1~6對本發(fā)明做進一步說明:實施例1~6選用260mm大斷面連鑄坯以保證壓縮比,生產(chǎn)厚度規(guī)格為20~30mm的Q550D成品鋼,在煉鋼生產(chǎn)過程中LF精煉工藝中精煉時間控制在35min以上,全程微正壓操作防止鋼水吸氮;采用石灰、鋁線、鋁粒等造白渣脫硫,快速成渣,脫硫過程合理控制氣量,嚴禁采用大氣量攪拌;采用錳鐵、硅鐵、鋁線、鈦鐵進行成分調(diào)整,在LF后期成白渣脫硫后進行Als調(diào)整,精煉結(jié)束前10~15min加鈮鐵和鈦鐵進行微合金化,成分調(diào)整完成后取樣前軟吹時間不低于3min;出站S≤0.010%以下,Ca≥25ppm,有效控制鋼種夾雜物級別總和不超過1.5級;連鑄工藝中澆注過程中全程保護性澆鑄,使用二冷區(qū)電磁攪拌和動態(tài)輕壓下,鋼水過熱溫度穩(wěn)定控制在10~35℃范圍內(nèi),拉速全程控制在0.8~1.0m/min范圍內(nèi);鑄坯下線堆垛緩冷,冷卻時間大于24h。實施例1:生產(chǎn)厚度規(guī)格為30mm的Q550D成品鋼,化學組成如表1所示,軋制及冷卻工藝如表2所示,力學性能檢測結(jié)果如表3所示。表1實施例1的化學成分(Wt%,余量為Fe)爐次號CMnNbTiCrMoAls實施例10.041.400.0400.0100.150.150.015表2實施例1的控軋+(DQ+ACC)工藝表3實施例1的力學性能實施例2:生產(chǎn)厚度規(guī)格為25mm的Q550D成品鋼,化學組成如表4所示,軋制及冷卻工藝如表5所示,力學性能檢測結(jié)果如表6所示。表4實施例2的化學成分(Wt%,余量為Fe)爐次號CMnNbTiCrMoAls實施例20.071.550.0530.0200.230.230.020表5實施例2的控軋+(DQ+ACC)工藝表6實施例2的力學性能實施例3:生產(chǎn)厚度規(guī)格為20mm的Q550D成品鋼,化學組成如表7所示,軋制及冷卻工藝如表8所示,力學性能檢測結(jié)果如表9所示。表7實施例3的化學成分(Wt%,余量為Fe)爐次號CMnNbTiCrMoAls實施例30.091.700.0650.0300.300.300.025表8實施例3的控軋+(DQ+ACC)工藝表9實施例3的力學性能實施例4:生產(chǎn)厚度規(guī)格為30mm的Q550D成品鋼,化學組成如表10所示,軋制及冷卻工藝如表11所示,力學性能檢測結(jié)果如表12所示。表10實施例4的化學成分(Wt%,余量為Fe)爐次號CMnNbTiCrMoAls實施例40.071.600.0570.0210.240.250.020表11實施例4的控軋+(DQ+ACC)工藝表12實施例4的力學性能實施例5:生產(chǎn)厚度規(guī)格為20mm的Q550D成品鋼,化學組成如表13所示,軋制及冷卻工藝如表14所示,力學性能檢測結(jié)果如表15所示。表13實施例5的化學成分(Wt%,余量為Fe)爐次號CMnNbTiCrMoAls實施例50.081.650.0550.0250.260.270.025表14實施例5的控軋+(DQ+ACC)工藝表15實施例5的力學性能實施例6:生產(chǎn)厚度規(guī)格為20mm的Q550D成品鋼,化學組成如表16所示,軋制及冷卻工藝如表17所示,力學性能檢測結(jié)果如表18所示。表16實施例6的化學成分(Wt%,余量為Fe)爐次號CMnNbTiCrMoAls實施例60.091.700.0600.0300.300.300.028表17實施例6的控軋+(DQ+ACC)工藝表18實施例6的力學性能當前第1頁1 2 3