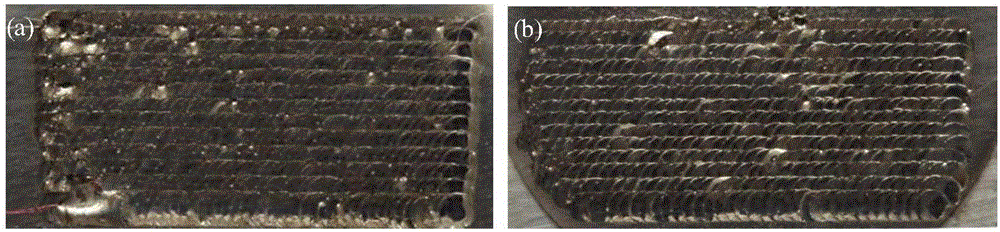
本發(fā)明屬于復(fù)合涂層
技術(shù)領(lǐng)域:
,尤其涉及一種鐵基非晶-納米晶復(fù)合涂層及其制備方法。
背景技術(shù):
:熔覆金屬涂層是鋼鐵防護(hù)的主要方法,但是國內(nèi)外常見Zn、Al及Zn-Al涂層對Cl-敏感,抗蝕性不高,已不能完全滿足惡劣環(huán)境的需求,高性能非晶涂層的研究與應(yīng)用引起了各國材料界的密切關(guān)注。Fe基非晶合金涂層因具有高硬度、優(yōu)異的耐磨抗腐性能等優(yōu)點(diǎn),已被應(yīng)用于船舶、核電、石油等領(lǐng)域。激光熔覆(LaserCladding)是一種具有能量密度高、熱輸入低、冷卻速度快等優(yōu)點(diǎn)的表面改性技術(shù),是非晶涂層制備過程中常用方法。近年來,國內(nèi)外研究者對鐵基非晶涂層做了廣泛研究,大部分研究者采用高純度的非晶態(tài)自熔性合金粉末通過激光熔覆技術(shù)制備非晶-納米晶復(fù)合涂層,但是非晶粉末的使用,不可避免地導(dǎo)致涂層中形成孔隙,降低涂層的耐蝕性,并且現(xiàn)有激光熔覆技術(shù)制備得到的非晶-納米晶復(fù)合涂層中非晶含量較低,也會導(dǎo)致涂層的耐蝕性能差。例如美國北德克薩斯大學(xué)的Katakam教授采用激光熔覆在AISI4130鋼基體表面制備Fe48Cr15Mo14C16B6Y2非晶涂層,所得涂層的穩(wěn)定性高,但因涂層中較多納米晶的存在,涂層非晶含量低,導(dǎo)致涂層的耐蝕性能較差。技術(shù)實(shí)現(xiàn)要素:有鑒于此,本發(fā)明的目的在于提供一種非晶-納米晶復(fù)合涂層及其制備方法,本發(fā)明提供的制備方法得到的復(fù)合涂層非晶含量高、耐蝕性能良好。為了實(shí)現(xiàn)上述發(fā)明目的,本發(fā)明提供以下技術(shù)方案:一種鐵基非晶-納米晶復(fù)合涂層的制備方法,采用激光熔覆將熔煉合金涂覆在基體材料上,得到復(fù)合涂層,所述熔煉合金包括44~45wt%的Fe、8~9wt%的Co、10~15wt%的Cr、25~27wt%的Mo、3~5wt%的C、1~2wt%的B和1~3wt%的Y。優(yōu)選的,所述熔煉合金為熔煉合金錠或熔煉合金板。優(yōu)選的,所述激光熔覆的脈沖頻率為0.5~1.5Hz。優(yōu)選的,所述激光熔覆的激光能量密度為97~111J/mm2。優(yōu)選的,所述激光熔覆的激光功率為15~25w。優(yōu)選的,所述激光熔覆的脈沖寬度為3~7ms。優(yōu)選的,所述激光熔覆的脈沖能量為6~10J。優(yōu)選的,所述激光熔覆的光束為圓形,所述光束的直徑為0.2~0.4mm。優(yōu)選的,所述基體材料為低碳合金鋼。本發(fā)明提供了以上技術(shù)方案制備得到的鐵基非晶-納米晶復(fù)合涂層,在元素組成上,所述復(fù)合涂層包括44~45wt%的Fe、8~9wt%的Co、10~15wt%的Cr、25~27wt%的Mo、3~5wt%的C、1~2wt%的B和1~3wt%的Y;所述復(fù)合涂層的非晶的含量為69~93%。本發(fā)明提供的鐵基非晶-納米晶復(fù)合涂層的制備方法,采用激光熔覆將包括44~45wt%的Fe、8~9wt%的Co、10~15wt%的Cr、25~27wt%的Mo、3~5wt%的C、1~2wt%的B和1~3wt%的Y的熔煉合金涂覆在基體材料上,得到復(fù)合涂層。本發(fā)明提供的方法,熔覆過程采用熔煉合金,避免采用激光熔煉常規(guī)原材料高純度的非晶態(tài)自熔性粉末,進(jìn)而避免產(chǎn)生非晶態(tài)自熔性粉末所形成的孔隙,確保得到結(jié)構(gòu)致密的復(fù)合涂層,提高復(fù)合涂層的耐蝕性能;所采用的熔煉合金的非晶形成能力強(qiáng),經(jīng)熔覆得到的涂層中非晶含量高,采用的熔煉合金中含有3~5wt%的C和1~2wt%的B,類金屬元素C和B原子半徑較小,與合金中的其他組分形成較大的原子半徑差,增大合金體系的負(fù)混合焓,提高熔覆過程中非晶形成能力,限定含量的Co和Y金屬元素顯著抑制合金體系的非均勻形核,提高熔覆過程中的組織均勻性,以較高比例添加Cr和Mo更進(jìn)一步提高非晶的耐蝕性能;采用激光熔覆將熔煉合金涂覆到基體材料表面,避免使用非晶體自熔性粉末,降低成本,并且無需添加高純度的合金元素也無需通過貴金屬和稀土元素的大量添加,提高非晶形成能力,降低制備成本。本發(fā)明實(shí)施例的結(jié)果表明,按照本申請技術(shù)方案得到的復(fù)合涂層的稀釋率低于27.2%,非晶含量達(dá)到69~93%,在3.5%NaCl溶液中耐腐蝕性能明顯優(yōu)于316L不銹鋼。附圖說明下面結(jié)合附圖和具體實(shí)施方式對本發(fā)明作進(jìn)一步詳細(xì)的說明。圖1為本發(fā)明激光熔覆過程熔覆材料和基體材料裝配示意圖;圖2為本發(fā)明實(shí)施例1和3提供的復(fù)合涂層的表面形貌圖;圖3為本發(fā)明實(shí)施例1和3提供的復(fù)合涂層的橫截面形貌圖;圖4為本發(fā)明實(shí)施例1、4和5提供的復(fù)合涂層的XRD圖;圖5為本發(fā)明實(shí)施例2~4提供的復(fù)合涂層的XRD圖;圖6為本發(fā)明實(shí)施例1提供的復(fù)合涂層的SEM形貌圖,其中,a-復(fù)合涂層橫截面SEM形貌,b-熔覆區(qū)SEM形貌,c-復(fù)合涂層界面SEM形貌,d-熔合區(qū)SEM形貌;圖7為本發(fā)明提供的復(fù)合涂層與超音速火焰噴涂制備的涂層SEM形貌對比圖,其中,a-本發(fā)明激光熔覆制備的涂層,b-超音速火焰噴涂制備的涂層;圖8為本發(fā)明實(shí)施例3提供的復(fù)合涂層的TEM形貌圖,其中a-復(fù)合涂層TEM形貌,b-復(fù)合涂層電子衍射花樣;圖9為本發(fā)明實(shí)施例1、4和5提供的復(fù)合涂層沿熔深方向的硬度分布圖;圖10為本發(fā)明實(shí)施例2~4提供的復(fù)合涂層沿熔深方向的硬度分布圖;圖11為本發(fā)明實(shí)施例1、4和5提供的復(fù)合涂層以及316L不銹鋼的動(dòng)電位極化曲線;圖12為本發(fā)明實(shí)施例2~4提供的復(fù)合涂層以及316L不銹鋼的動(dòng)電位極化曲線。具體實(shí)施方式本發(fā)明提供了一種鐵基非晶-納米晶復(fù)合涂層的制備方法,采用激光熔覆將熔煉合金涂覆在基體材料上,得到復(fù)合涂層,所述熔煉合金包括44~45wt%的Fe、8~9wt%的Co、10~15wt%的Cr、25~27wt%的Mo、3~5wt%的C、1~2wt%的B和1~3wt%的Y。本發(fā)明提供的方法,熔覆過程采用熔煉合金,避免采用激光熔煉常規(guī)原材料高純度的非晶態(tài)自熔性粉末,進(jìn)而避免產(chǎn)生非晶態(tài)自熔性粉末所形成的孔隙,確保得到結(jié)構(gòu)致密的復(fù)合涂層,提高復(fù)合涂層的耐蝕性能;所采用的熔煉合金的非晶形成能力強(qiáng),經(jīng)熔覆得到的復(fù)合涂層中非晶含量高,提高復(fù)合涂層的耐蝕性能。本發(fā)明采用激光熔覆將熔煉合金涂覆在基體材料上,得到復(fù)合涂層。在本發(fā)明中,所述基體材料優(yōu)選為低碳合金鋼,本發(fā)明對所述低碳合金鋼的來源沒有特殊要求,采用本領(lǐng)域技術(shù)人員所熟知的低碳合金鋼即可。本發(fā)明優(yōu)選采用砂紙對所述基體材料進(jìn)行打磨,去除所述基體材料的氧化層;本發(fā)明對所述打磨方式?jīng)]有特殊要求,采用本領(lǐng)域技術(shù)人員所熟知的打磨方式即可,在本發(fā)明的實(shí)施例中,具體采用粒度為1000~3000目的砂紙對所述基體材料進(jìn)行打磨。完成打磨后,本發(fā)明優(yōu)選采用無水乙醇對所述基體材料進(jìn)行清洗,以期得到潔凈的基體材料;本發(fā)明對所述清洗沒有特殊要求,以能得到潔凈的基體材料為準(zhǔn)。得到潔凈的基體材料后,本發(fā)明優(yōu)選吹干所述基體材料。在本發(fā)明中,所述熔煉合金包括44~45wt%的Fe、8~9wt%的Co、10~15wt%的Cr、25~27wt%的Mo、3~5wt%的C、1~2wt%的B和1~3wt%的Y。在本發(fā)明中,所述熔煉合金優(yōu)選包括44.5wt%的Fe、8.5wt%的Co、14wt%的Cr、26wt%的Mo、3wt%的C、1wt%的B和3wt%的Y。在本發(fā)明中,所述熔煉合金優(yōu)選為熔煉合金錠或熔煉合金板。本發(fā)明對所述熔煉合金的尺寸沒有特殊要求,以能適合所采用的熔覆設(shè)備即可。在本發(fā)明的實(shí)施例中,所述熔煉合金的尺寸具體為20mm×20mm×0.2mm。本發(fā)明優(yōu)選采用真空電弧熔煉法制備所述熔煉合金。在本發(fā)明中,所述真空電弧熔煉法優(yōu)選為將所述Fe、Co、Cr、Mo、C、B和Y合金元素的原料置于真空熔煉爐后,抽真空至1×10-2Pa后更換2~3次高純氬氣調(diào)節(jié)真空度為1×10-1Pa進(jìn)行熔煉得到所述熔煉合金,所述熔煉優(yōu)選采用熔煉一次翻轉(zhuǎn)一次的方式,在本發(fā)明中,所述熔煉的次數(shù)優(yōu)選為3次。本發(fā)明對所述真空電弧熔煉法沒有特殊要求,采用本領(lǐng)域技術(shù)人員所熟知的真空電弧熔煉法即可。得到熔煉合金后,本發(fā)明優(yōu)選對所述熔煉合金進(jìn)行打磨和清洗,本發(fā)明對所述打磨和清洗沒有特殊要求,采用以上對所述基體材料進(jìn)行的打磨和清洗方式即可。本發(fā)明對所述基體材料和所述熔煉合金進(jìn)行打磨和清洗為了充分去除所述基體材料和所述熔煉合金表面的氧化層,得到潔凈的基體材料和潔凈的熔煉合金,以期提高所述基體材料和所述熔煉合金良好結(jié)合。得到所述基體材料和所述熔煉合金后,采用激光熔覆將熔煉合金涂覆在基體材料上,得到復(fù)合涂層。在本發(fā)明中,所述激光熔煉的脈沖頻率優(yōu)選為0.5~1.5Hz,進(jìn)一步優(yōu)選為0.8~1.4Hz,最優(yōu)選為1.0Hz。在本發(fā)明中,所述激光熔覆的激光能量密度優(yōu)選為97~111J/mm2,進(jìn)一步優(yōu)選為100~110J/mm2,最優(yōu)選為105J/mm2。在本發(fā)明中,所述激光熔覆的激光功率優(yōu)選為15~25w,進(jìn)一步優(yōu)選為18~24w,最優(yōu)選為19.2w。在本發(fā)明中,所述激光熔覆的脈沖寬度優(yōu)選為3~7ms,進(jìn)一步優(yōu)選為4~6ms。在本發(fā)明中,所述激光熔覆的脈沖能量優(yōu)選為6~10J,進(jìn)一步優(yōu)選為7~8J。在本發(fā)明中,所述激光熔覆的光束優(yōu)選為圓形。在本發(fā)明中,所述光束的直徑優(yōu)選為0.2~0.4mm,進(jìn)一步優(yōu)選為0.3mm。本發(fā)明對實(shí)施所述激光熔覆的設(shè)備沒有特殊要求,采用本領(lǐng)域技術(shù)人員所熟知的激光熔覆設(shè)備即可,在本發(fā)明的實(shí)施例中,具體采用意大利SISMA公司生產(chǎn)的L80型Nd:YAG脈沖激光機(jī)。在熔覆過程中,本發(fā)明優(yōu)選采用電腦控制器進(jìn)行熔覆方向和熔覆速度的設(shè)置。在本發(fā)明中,所述熔覆方向優(yōu)選為同一方向,避免往復(fù),利于熔覆層的疊加。在本發(fā)明中,所述熔覆速率優(yōu)選為12~24mm/min,進(jìn)一步優(yōu)選為15~21mm/min。在熔覆過程中,本發(fā)明優(yōu)選采用側(cè)吹惰性氣體的方式對所述熔覆過程進(jìn)行保護(hù),進(jìn)一步優(yōu)選為采用側(cè)吹A(chǔ)r氣。在本發(fā)明中,所述側(cè)吹優(yōu)選以氣體流與所述合金材料的表面成30~60°,進(jìn)一步優(yōu)選為45~50°。在本發(fā)明中,所述側(cè)吹的氣體流速優(yōu)選為15~30L/min,進(jìn)一步優(yōu)選為20~25L/min。在本發(fā)明中,所述熔覆的搭接率優(yōu)選為25~75%,進(jìn)一步優(yōu)選為40~60%。本發(fā)明,優(yōu)選采用激光表面聚焦的方式。下面結(jié)合實(shí)施例對本發(fā)明提供的方法進(jìn)行詳細(xì)的說明,但是不能把它們理解為對本發(fā)明保護(hù)范圍的限定。實(shí)施例1將Fe-C、Fe-B、Fe-Cr、Co、Mo和Y這6種原料各20克放置于真空爐內(nèi)的銅模上,這6種原料的組分如表1所示。先將真空爐的真空抽至1×10-2Pa,更換3次高純氬氣后,調(diào)節(jié)真空至1×10-1Pa,進(jìn)行合金的熔煉,為了使合金熔煉均勻,重復(fù)熔煉3次,每次熔煉結(jié)束將合金進(jìn)行翻轉(zhuǎn),采用隨爐冷卻的方式降溫,得到成分為Fe44.5Co8.5Cr14Mo26C3B1Y3的熔煉合金。將得到的熔煉合金切割成20mm×20mm×0.2mm的試樣,選用2mm厚的低碳合金鋼作為基體材料。采用砂紙對熔煉合金試樣和低碳合金鋼的表面進(jìn)行打磨,去除表面的氧化層后,用無水乙醇清洗后干燥得到潔凈的熔煉合金試樣和潔凈的低碳合金鋼。將熔煉合金作為熔覆材料置于基體材料表面,激光器于熔覆材料上方進(jìn)行熔煉過程,熔覆材料與基體材料的放置位置如圖1所示。熔覆過程采用側(cè)吹A(chǔ)r方式,氣體流量為15L/min,側(cè)吹角度為45°,采用激光表面聚焦的方式完成激光熔煉,其中圓形光斑直徑為0.3mm,熔煉搭接率為50%。激光熔覆過程中,激光功率為17.6w,脈沖頻率為1.5Hz,脈沖寬度為5.0ms,激光能量密度為97J/mm2,脈沖能量為6.8J,限定熔覆速率為0.3mm/s,疊加率為50%。在此工藝參數(shù)的條件下制備得到復(fù)合涂層。表1熔煉合金制備原料組分(質(zhì)量百分比)實(shí)施例2采用與實(shí)施例1相同的方式制備熔煉合金,得到的熔煉合金組分與實(shí)施例1中合金組分一致,按照如實(shí)施例1方式進(jìn)行熔煉得到復(fù)合涂層,與實(shí)施例1的區(qū)別在于,激光熔覆過程中,激光功率為19.2w,脈沖頻率為0.5Hz,脈沖寬度為5.0ms,激光能量密度為104J/mm2,脈沖能量為7.3J,限定熔覆速率為0.3mm/s,疊加率為50%。實(shí)施例3采用與實(shí)施例1相同的方式制備熔煉合金,得到的熔煉合金組分與實(shí)施例1中合金組分一致,按照如實(shí)施例1方式進(jìn)行熔煉得到復(fù)合涂層,與實(shí)施例1的區(qū)別在于,激光熔覆過程中,激光功率為19.2w,脈沖頻率為1.0Hz,脈沖寬度為5.0ms,激光能量密度為104J/mm2,脈沖能量為7.3J,限定熔覆速率為0.3mm/s,疊加率為50%。實(shí)施例4采用與實(shí)施例1相同的方式制備熔煉合金,得到的熔煉合金組分與實(shí)施例1中合金組分一致,按照如實(shí)施例1方式進(jìn)行熔煉得到復(fù)合涂層,與實(shí)施例1的區(qū)別在于,激光熔覆過程中,激光功率為19.2w,脈沖頻率為1.5Hz,脈沖寬度為5.0ms,激光能量密度為104J/mm2,脈沖能量為7.3J,限定熔覆速率為0.3mm/s,疊加率為50%。實(shí)施例5采用與實(shí)施例1相同的方式制備熔煉合金,得到的熔煉合金組分與實(shí)施例1中合金組分一致,按照如實(shí)施例1方式進(jìn)行熔煉得到復(fù)合涂層,與實(shí)施例1的區(qū)別在于,激光熔覆過程中,激光功率為20.8w,脈沖頻率為1.5Hz,脈沖寬度為5.0ms,激光能量密度為111J/mm2,脈沖能量為7.8J,限定熔覆速率為0.3mm/s,疊加率為50%。采用MR5000型倒置顯微鏡的方式觀察所得到的復(fù)合涂層表面形貌以及橫截面形貌,實(shí)施例1制備得到的復(fù)合涂層的表面形貌如圖2(a)所示,橫截面形貌如圖3(a)所示。實(shí)施例3制備得到的復(fù)合涂層的表面形貌如圖2(b)所示,橫截面形貌如圖3(b)所示。由圖2和圖3可知,復(fù)合涂層成形良好,與基體材料呈現(xiàn)典型冶金結(jié)合。根據(jù)橫截面形貌圖測試涂層厚度h、熔深H,并以此為基礎(chǔ)計(jì)算得到稀釋率,其中涂層厚度h、熔深H以及稀釋率如表2所示。采用Empyrean型X射線衍射儀,限定Cu靶,電壓為40KV,電流為40mA,衍射速度為4°/min對復(fù)合涂層表面以及熔煉合金進(jìn)行物相分析,結(jié)果如圖4和圖5所示,由圖4和圖5可知,XRD圖譜中均出現(xiàn)“饅頭狀”的漫衍射峰,表明表面涂層沒有晶化,是非晶態(tài)的。采用SV3400型環(huán)境掃描電子顯微鏡分析復(fù)合涂層組織及微觀結(jié)構(gòu),按照實(shí)施例1制備得到的復(fù)合涂層的SEM顯微組織形貌如圖6所示,由圖6可知復(fù)合涂層主要包括重結(jié)晶區(qū)、熔合區(qū)和熔覆區(qū),重結(jié)晶區(qū)為呈板條狀馬氏體組織,熔合區(qū)為沿外延生長的樹枝晶,熔覆區(qū)主要由非晶基體與細(xì)小晶粒組成;圖7表明,本發(fā)明所形成的涂層沒有明顯孔隙的生成,而通過超音速火焰噴涂制備的涂層在低倍形貌下就可見明顯的孔隙。采用TecnaiG2F20S-TWIN型透射電鏡觀察復(fù)合涂層的微觀組織,進(jìn)行觀察前對試樣進(jìn)行離子減薄,離子減薄的電壓和角度為3KeV和4°,按照實(shí)施例3制備得到的復(fù)合涂層的TEM形貌如圖8所示,由圖8可知涂層的內(nèi)部組織比較均勻,微觀組織襯度均一,其電子衍射花樣特點(diǎn)是中心有一漫散的中心斑點(diǎn)及漫散環(huán),納米晶的衍射花樣為多晶體的同心漫散射環(huán),白色的基體上彌散分布著黑灰色的納米晶,晶粒尺寸為15~35nm。采用WT-401MVD型數(shù)顯顯微硬度計(jì)沿復(fù)合涂層最大熔深方向測量復(fù)合涂層的硬度分布,測試過程中加載載荷為100gf,加壓時(shí)間為10s,測量間距為0.05mm,結(jié)果如圖9和圖10所示。由圖9和圖10可知,涂層的硬度明顯高于基體;隨脈沖功率的升高,涂層的硬度逐漸降低;隨脈沖頻率的增加,涂層的硬度先增大后減??;當(dāng)脈沖功率為19.2W、脈沖頻率為1.0Hz時(shí),平均顯微硬度高達(dá)1295HV,約為基體材料的9倍。采用CHI650E型電化學(xué)工作站測試復(fù)合涂層和316L不銹鋼在質(zhì)量濃度3.5%的NaCl溶液中的耐腐蝕性能,其中試樣為工作電極,Pt電極為輔助電極,飽和甘汞電極為參比電極。測試前,將試樣在3.5%NaCl溶液中浸泡30min至開路電位穩(wěn)定;測試時(shí),初始電位為-1.0V,終止電位為1.5V,掃描速度為1mv/s;每組試驗(yàn)至少測量3次,保證結(jié)果具有重復(fù)性。測試結(jié)果如圖11和圖12所示。由圖11和圖12可知,制備得到的復(fù)合涂層表現(xiàn)出比316L不銹鋼更為優(yōu)異的耐腐蝕性,這是由于復(fù)合涂層結(jié)構(gòu)致密、非晶含量高及穩(wěn)定鈍化膜的形成所導(dǎo)致的。表2復(fù)合涂層的稀釋率以及非晶含量實(shí)施例熔深/μm熔高/μm稀釋率/%非晶含量/%實(shí)施例15617524.283實(shí)施例24417020.693實(shí)施例37219327.289實(shí)施例419819550.478實(shí)施例528623754.769以上所述僅是本發(fā)明的優(yōu)選實(shí)施方式,應(yīng)當(dāng)指出,對于本
技術(shù)領(lǐng)域:
的普通技術(shù)人員來說,在不脫離本發(fā)明原理的前提下,還可以做出若干改進(jìn)和潤飾,這些改進(jìn)和潤飾也應(yīng)視為本發(fā)明的保護(hù)范圍。當(dāng)前第1頁1 2 3