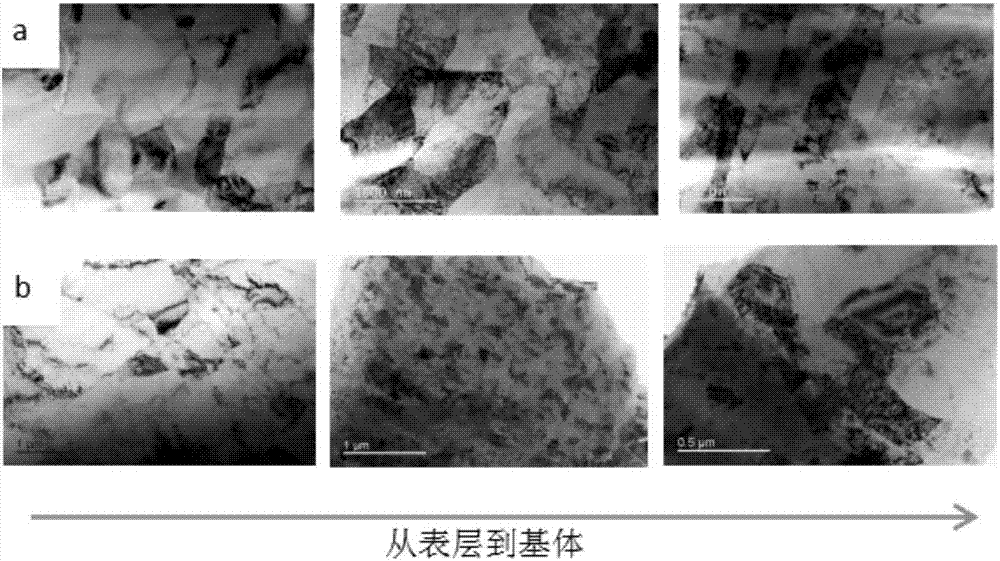
本發(fā)明涉及一種提高金屬梯度結(jié)構(gòu)強度和塑性匹配度的方法,屬于材料加工
技術(shù)領(lǐng)域:
。
背景技術(shù):
:表面納米化技術(shù)主要是采用簡單的動力裝置,為數(shù)量眾多的硬質(zhì)小金屬圓球提供足夠的動能,使圓球以一定速度連續(xù)不斷地撞擊被加工樣品表面,使樣品表面一定深度區(qū)域的材料發(fā)生劇烈塑性變形,進而使得樣品表面形成一定厚度的細化組織層。表面納米化技術(shù)利用高能噴丸對金屬材料的表面進行機械處理,使其沿厚向獲得納米晶/超細晶及粗晶層的梯度組織,克服了目前三維大尺寸納米晶體材料制備的技術(shù)困難,又將納米材料的優(yōu)異性能應(yīng)用到了傳統(tǒng)工程材料的表面改性技術(shù)中,具有很大的工業(yè)應(yīng)用價值。但由于加工過程中噴丸速度快,擊打能量較高,一方面經(jīng)處理后的材料表面會出現(xiàn)粗糙度變大的問題,這將大大影響表面納米化板材的表面質(zhì)量,增加后續(xù)加工工藝成本,另一方面還存在強度升高,塑性降低過多,二者匹配度不好的問題。軋制變形是一種常見的壓力加工方式,這種變形是在軋機上操作,將金屬樣件通過一對旋轉(zhuǎn)軋輥的間隙,因為受到軋輥的壓縮使材料截面減小、長度增加,這也是生產(chǎn)金屬板材最常用的生產(chǎn)方式。中國專利申請201410078163.1通過對鎳系不銹鋼光亮板進行軋制參數(shù)的控制來降低成品帶鋼材表面的粗糙度,拋丸后再進行酸洗、浸泡等多道次工藝操作后再行軋制,然而軋制總變形率不低于70%,變形量太大,可能會破壞原有的組織。技術(shù)實現(xiàn)要素:針對現(xiàn)有技術(shù)中高能噴丸后金屬板材粗糙度增加,強度升高而塑性降低過多的問題,本發(fā)明提供了一種提高金屬梯度結(jié)構(gòu)強度和塑性匹配度的方法,對高能噴丸表面納米化處理后的金屬板材采用可控的軋制變形,降低樣品表面粗糙度的同時保持原有高能噴丸處理后樣品的硬度梯度效果、細晶/納米晶組織,保留原有的加工硬化、細晶強化,然后在低溫下短時間回復(fù)退火,既保持細晶組織,又使晶粒內(nèi)部位錯部分回復(fù),增大位錯儲存能,提高表面納米化金屬板材的強度與塑性的匹配度。本發(fā)明的技術(shù)方案如下:一種提高金屬梯度結(jié)構(gòu)強度和塑性匹配度的方法,具體步驟為:首先對表面清潔的 金屬板材進行高能噴丸表面納米化處理,然后對表面納米化處理后的板材進行軋制,軋制壓下量為12%~30%,最后在50~100℃下退火30~60min。本發(fā)明中所述的金屬板材為本
技術(shù)領(lǐng)域:
常用的金屬板材,可為純金屬或合金板材,可選自鋁合金板或銅板。優(yōu)選地,所述的高能噴丸表面納米化處理采用3~5mm的鋼丸,轉(zhuǎn)速為25m/s,處理時間為15~30min。優(yōu)選地,所述的軋制壓下量為12%~20%。優(yōu)選地,所述的軋制過程中的軋制速度為5~40m/s。本發(fā)明中的軋制壓下量的計算公式為:軋制壓下量(%)=(軋前厚度-成品厚度)/軋前厚度×100%。本發(fā)明對表面納米化處理后的金屬板材進行可控的軋制變形,控制軋制壓下量在12%~30%范圍內(nèi),使得軋制過程中板材表面凸起部分在進入軋輥后被壓扁、擴充至凹坑處,因變形量控制得當(dāng),引入的位錯還不足以使樣品表面組織發(fā)生回復(fù)、再結(jié)晶,相應(yīng)的溫升也不明顯,因此軋制后金屬板材沿厚向的硬度最大值并未出現(xiàn)大幅下降,可保持原有高能噴丸處理后樣品的硬度梯度效果、細晶或納米晶組織,保留原有的加工硬化、細晶強化等,同時降低板材的粗糙度,提高表面質(zhì)量。在軋制變形之后,本發(fā)明繼續(xù)對處理成品進行真空低溫短時間退火,既保持細晶組織,又使晶粒內(nèi)部位錯部分回復(fù),增大位錯儲存能,提高表面納米化金屬板材的強度與塑性的匹配度。本發(fā)明工藝簡單,無污染,易操作,適合于大規(guī)模批量化生產(chǎn),制備的金屬板材具有表面粗糙度較低兼強度與塑性匹配度高的梯度組織結(jié)構(gòu),滿足實際應(yīng)用的需求。附圖說明圖1為粗晶鋁(cg)、高能噴丸表面納米化處理后的鋁合金板(rasp)及噴丸加軋制處理后的鋁合金板(rasp+roll)的截面硬度梯度分布圖。圖2為高能噴丸表面納米化處理后的鋁合金板(a)及噴丸加軋制處理后的鋁合金板(b)的截面透射電子組織圖。圖3為粗晶銅(cg)、高能噴丸表面納米化處理后的銅板(rasp)及噴丸加軋制處理后的銅板(rasp+roll)的截面硬度梯度分布圖。圖4為高能噴丸表面納米化處理后的銅板的截面透射電子顯微鏡圖。圖5為噴丸加軋制處理后的銅板的截面透射電子顯微鏡圖。圖6為粗晶鋁合金(cg)和高能噴丸表面納米化處理后的鋁合金板(rasp)的工程應(yīng)力-應(yīng)變曲線。圖7為高能噴丸表面納米化處理后的鋁合金板(rasp)及噴丸加軋制處理(rasp+roll)后的鋁合金板和噴丸加軋制加退火的屈服強度和斷裂延伸率的匹配圖。圖8為高能噴丸表面納米化處理后的鋁合金板(rasp)及噴丸加軋制處理(rasp+roll)后的鋁合金板和噴丸加軋制加退火的抗拉強度和斷裂延伸率的匹配圖。具體實施方式下面結(jié)合實施例和附圖對本發(fā)明作進一步詳述。實施例1①切割:制備一塊厚度為10mm的退火態(tài)6063鋁合金板,保證上下底面平行;②表面清潔:常溫,使用酒精等有機溶劑去除板材上下兩面的油脂。③表面納米化處理:選擇5mm的gcr15的鋼丸。高能噴丸設(shè)備轉(zhuǎn)速25m/s,處理時間15min。④平輥軋制:兩輥四輥聯(lián)軋機(兩輥φ400mm×350mm;四輥冷軋:φ100mm/φ380mm×350mm)。對表面納米處理后的板材,進行軋制,保持較小的道次變形量,總變形量12%,4道次,軋制速度為5m/s。樣品厚度依次從10mm,到9.5mm,到9.0mm,到8.8mm。⑤低溫短時間退火:真空退火爐對噴丸和軋制后得到的成品分別在50℃,75℃,100℃下退火30min,60min,然后隨爐冷卻。⑥實驗數(shù)據(jù)對比參考:測最高硬度、硬度梯度、表面粗糙度等性能指標(biāo)及組織,如表1及圖1和圖2所示。表1粗晶鋁、高能噴丸表面納米化處理后的鋁合金板及噴丸加軋制處理后的鋁合金板的粗糙度與最高硬度粗晶鋁高能噴丸高能噴丸+軋制12%粗糙度ra/μm22.1168.543.0最高硬度/hv0.232.666.257.0圖1為粗晶鋁(cg)、高能噴丸表面納米化處理后的鋁合金板(rasp)及噴丸加軋制處理后的鋁合金板(rasp+roll)的截面硬度梯度分布圖。從圖1可以看出,高能噴丸后表層硬度提高,整個硬度呈梯度分布,軋制后表層硬度稍微降低,但仍比基體硬度高,所以仍呈梯度分布。圖2為高能噴丸表面納米化處理后的鋁合金板(a)及噴丸加軋制處理后的鋁合金板(b)的截面透射電子組織圖。圖2的組織圖也可清楚觀察出噴丸加軋制處理后,原有的梯度組織特征仍較為明顯。實施例2①切割:制備一塊厚度為4.7mm的退火態(tài)99.99wt%純銅板,保證上下底面平行;②表面清潔:常溫,使用酒精等有機溶劑去除板材上下兩面的油脂。③表面納米化處理:選擇3mm的gcr15的鋼丸。高能噴丸設(shè)備轉(zhuǎn)速25m/s,處理時間30min。④平輥軋制:兩輥四輥聯(lián)軋機(兩輥φ400mm×350mm;四輥冷軋:φ100mm/φ380mm×350mm)。對表面納米處理后的板材,進行軋制,保持較小的道次變形量,總變形量30%,7道次,軋制速度為40m/s。樣品厚度從4.7mm降至3.3mm。⑤低溫短時間退火:真空退火爐對噴丸和軋制后得到的成品分別在50℃,75℃,100℃下退火30min,60min,然后隨爐冷卻。⑥實驗數(shù)據(jù)對比參考:測最高硬度、硬度梯度、表面粗糙度等性能指標(biāo)及組織,如表2及圖3和圖4所示。表2粗晶銅、高能噴丸表面納米化處理后的鋁合金板及噴丸加軋制處理后的表面納米化處理后的銅板的粗糙度與最高硬度粗晶銅高能噴丸高能噴丸+軋制30%粗糙度ra/μm7.0110.115.0最高硬度/hv0.276118123圖3為粗晶銅(cg)、高能噴丸表面納米化處理后的銅板(rasp)及噴丸加軋制處理后的銅板(rasp+roll)的截面硬度梯度分布圖。從圖3可以看出,高能噴丸后表層硬度提高,整個硬度呈梯度分布。軋制后表層硬度稍微降低,但仍比基體硬度高,所以仍呈梯度分布。圖4為高能噴丸表面納米化處理后的銅板的截面透射電子組織圖,圖5為噴丸加軋制處理后的銅板的截面透射電子組織圖,從圖4和圖5的組織圖也可清楚觀察出噴丸加軋制處理后,原有的梯度組織特征仍較為明顯。實施例3①切割:制備一塊厚度為12mm的退火態(tài)6063鋁合金板,保證上下底面平行;②表面清潔:常溫,使用酒精等有機溶劑去除板材上下兩面的油脂。③表面納米化處理: 選擇5mm的gcr15的鋼丸。高能噴丸設(shè)備轉(zhuǎn)速25m/s,處理時間15min。④平輥軋制:兩輥四輥聯(lián)軋機(兩輥φ400mm×350mm;四輥冷軋:φ100mm/φ380mm×350mm)。對表面納米處理后的板材,進行軋制,保持較小的道次變形量,總變形量50%,8道次。樣品厚度從12mm,軋到6mm。表3粗晶鋁、高能噴丸表面納米化處理后的鋁合金板及噴丸加軋制處理后的鋁合金板的粗糙度與最高硬度粗晶鋁高能噴丸高能噴丸+軋制50%粗糙度ra/μm22.1168.522.0最高硬度/hv0.232.666.254.0如表3所示,高能噴丸后硬度提高,經(jīng)軋制處理后表面粗糙度大幅度降低,但最高硬度略有下降。同時高能噴丸后的硬度梯度組織基本已被破壞掉,硬度從表面至心部基本保持一致,再無明顯梯度分布。實施例1~2與實施例3對比可知,軋制變形量應(yīng)控制12%~30%范圍內(nèi),軋制變形量過大時,破壞高能噴丸后的硬度梯度組織。實施例4①切割:制備一塊厚度為10mm的退火態(tài)6063鋁合金板,保證上下底面平行;②表面清潔:常溫,使用酒精等有機溶劑去除板材上下兩面的油脂。③表面納米化處理:選擇5mm的gcr15的鋼丸。高能噴丸設(shè)備轉(zhuǎn)速25m/s,處理時間15min。④平輥軋制:兩輥四輥聯(lián)軋機(兩輥φ400mm×350mm;四輥冷軋:φ100mm/φ380mm×350mm)。對表面納米處理后的板材,進行軋制,保持較小的道次變形量,總變形量20%,4道次,軋制速度為5m/s。樣品厚度依次從10mm,到9.5mm,到9.0mm,到8.5mm,到8mm。⑤低溫短時間退火:真空退火爐對噴丸和軋制后得到的成品分別在50℃,75℃,100℃下退火30min,60min,然后隨爐冷卻。⑥實驗數(shù)據(jù)對比參考:測拉伸等性能指標(biāo),如表4,圖7和圖8所示。對比例1①切割:制備一塊厚度為10mm的退火態(tài)6063鋁合金板,保證上下底面平行;②表面清潔:常溫,使用酒精等有機溶劑去除板材上下兩面的油脂。③低溫短時間退火:真空退火爐對鋁合金板分別在50℃,75℃,100℃下退火30min,60min,然后隨爐冷卻。 ⑥實驗數(shù)據(jù)對比參考:測拉伸等性能指標(biāo),如表4中的cg系列所示。對比例2①切割:制備一塊厚度為10mm的退火態(tài)6063鋁合金板,保證上下底面平行;②表面清潔:常溫,使用酒精等有機溶劑去除板材上下兩面的油脂。③表面納米化處理:選擇5mm的gcr15的鋼丸。高能噴丸設(shè)備轉(zhuǎn)速25m/s,處理時間15min。④低溫短時間退火:真空退火爐對噴丸后得到的成品分別在50℃,75℃,100℃下退火30min,60min,然后隨爐冷卻。⑥實驗數(shù)據(jù)對比參考:測拉伸等性能指標(biāo),如表4中的rasp系列、圖7和圖8所示。表4粗晶鋁合金、高能噴丸表面納米化處理后的鋁合金,噴丸加軋制處理后的鋁合金及粗晶和噴丸及噴丸加軋制在不同條件下退火的斷裂延伸率、屈服強度和抗拉強度圖6為粗晶鋁(cg)和高能噴丸表面納米化處理后的鋁合金板(rasp)的工程應(yīng)力-應(yīng)變曲線。圖7為高能噴丸表面納米化處理后的鋁合金板(rasp)及噴丸加軋制處理(rasp+roll)后的鋁合金板和噴丸及噴丸加軋制在不同條件下退火的屈服強度和斷裂延伸率的匹配圖。圖8為高能噴丸表面納米化處理后的鋁合金板(rasp)及噴丸加軋制處理(rasp+roll)后的鋁合金板和噴丸及噴丸加軋制在不同條件下退火的抗拉強度和斷裂延伸率的匹配圖。從表4和圖6中可以看出,高能噴丸后屈服強度從44.9mpa提高至100.4mpa,提高了1.23倍,抗拉強度也從99.8mpa提高至110.4mpa,增加了10.6%,而斷裂延伸率從39.4%下降到9.8%,降低了75.1%??梢姼吣車娡韬箐X合金板的強度和塑性的匹配度低。從表4、圖7和圖8中可看出,噴丸經(jīng)過軋制后屈服強度從100.4mpa降低至81.2mpa,但抗拉強度從110.4mpa提高至114.1mpa,斷裂延伸率從9.8%提高至18.2%,強度和塑性的匹配度提高,但屈服強度下降過多。噴丸加軋制樣品在100℃下退火60min,使屈服強度增加至89.2mpa,抗拉強度提高至120.9mpa,斷裂延伸率稍微有點降低至16%,強度和塑性的匹配度得到提高。綜上所述,金屬板通過噴丸加軋制在恰當(dāng)?shù)膮?shù)下低溫退火既可以減小金屬板的表面粗糙度,又可以提高強度和塑性的匹配度。當(dāng)前第1頁12