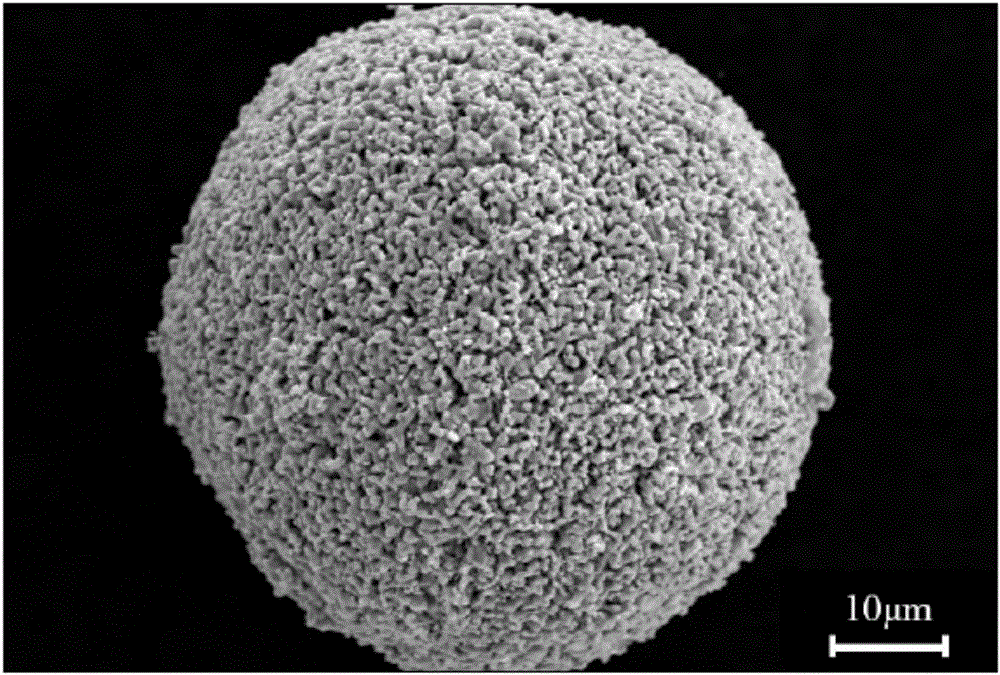
本發(fā)明為涉及一種制備鐵基合金粉的方法、其粉末和燒結(jié)體,尤指一種制備多孔球狀鐵基合金粉的方法、其粉末和燒結(jié)體。
背景技術(shù):
:粉末冶金(PowderMetallurgy)為金屬材料常見的制造技術(shù)之一,其中又以鐵為主原料的粉末的應(yīng)用范疇最廣,其依據(jù)制備的方式大致可分為預(yù)合金粉末、擴散合金粉末、混合粉末或以上粉末的混合物等。上述各種形式粉末的平均粒徑皆為大約70μm,屬于粗粉末,具有較大的顆粒間隙,顆粒間隙大將使得燒結(jié)成品中的孔隙的尺寸也較大,此大孔隙導(dǎo)致機械性質(zhì)變差。另外,相較于細粉末,粗粉末因擴散距離較大,導(dǎo)致在燒結(jié)階段時合金的均質(zhì)性較差,此外,因粗粉末的表面積較小,使得燒結(jié)驅(qū)動力變低,導(dǎo)致燒結(jié)效率較差、燒結(jié)密度較低,進而影響該成品的質(zhì)量。當(dāng)采用細鐵粉,以羰基鐵粉為例,雖粉末具有高比表面積,燒結(jié)性高,易燒至高密度,但此種粉末的流動性差,使得在干壓成形時難以流入模穴,所以不易自動化;又因制作羰基鐵粉需采用高溫、高壓的化學(xué)反應(yīng)工藝,所以其還具有高成本的缺點。而其他如水噴霧法,雖也可制作細鐵粉,但也有流動性差的問題,此外,其他傳統(tǒng)生產(chǎn)細鐵粉的合格率低,成本仍偏高。鑒于上述問題,中國臺灣發(fā)明專利公告第I294318以及德國專利公開第DE102006027851號所示的“燒結(jié)硬化粉末及其燒結(jié)體”,其揭示一種燒結(jié)硬化粉,該燒結(jié)硬化粉包含有鐵、碳、鎳、鉻、鉬,鐵為其主成分,且合金比例以重量百分比可表示為碳含量:0.1-0.8%,鎳含量:3.5-12.0%,鉻含量:0.1-7%,鉬含量:2.0%以下,該燒結(jié)硬化粉使用0.1~30μm的細粉,如羰基鐵粉,經(jīng)噴霧造粒后的粉末具流動性可供干壓成形用,且燒結(jié)后的密度高、合金元素的均質(zhì)性佳。據(jù)此,可利用該燒結(jié)硬化粉以粉末冶金工藝制得一具有高密度的燒結(jié)體,該燒結(jié)體可不經(jīng)淬火的熱處理而僅以低溫回火處理,即可達到良好的機械性質(zhì)。然而,該燒結(jié)硬化粉因使用羰基鐵粉,還是具有成本高的問題,若所用的羰基鐵粉含有碳時其硬度高,也會造成壓縮性差、生胚密度低、模具易磨耗等問題,不利于工業(yè)上的應(yīng)用。技術(shù)實現(xiàn)要素:本發(fā)明的主要目的,在于提供一種制備多孔球狀鐵基合金粉的方法、其粉末和燒結(jié)體,以解決現(xiàn)有粉末冶金工藝中,使用細鐵粉制作具高密度、高機械性質(zhì)、均勻顯微組織的粉末冶金鐵基合金工件成本過高的問題。為達上述目的,本發(fā)明提供一種制備多孔球狀鐵基合金粉的方法,包含下列步驟:步驟1:將一氧化鐵粉與一含金屬的粉末混合形成一混合粉末;步驟2:對該混合粉末進行一噴霧造粒工藝,使該混合粉末形成一球狀噴霧造粒粉;以及步驟3:將該球狀噴霧造粒粉置于一還原環(huán)境并加熱至一低于700℃的還原溫度,以得到一多孔球狀鐵基合金粉,該多孔球狀鐵基合金粉具有一大于0.9m2/g的比表面積。本發(fā)明所述的制備多孔球狀鐵基合金粉的方法,其中,該氧化鐵粉為三氧化二鐵粉或四氧化三鐵粉。本發(fā)明所述的制備多孔球狀鐵基合金粉的方法,其中,該氧化鐵粉具有一介于0.1μm至5μm之間的平均粒徑。本發(fā)明所述的制備多孔球狀鐵基合金粉的方法,其中,該含金屬的粉末選自于一金屬元素粉、一金屬合金粉以及一金屬氧化物粉所組成的群組。本發(fā)明所述的制備多孔球狀鐵基合金粉的方法,其中,該金屬元素粉所用金屬元素選自于鎳、鉬、鎢以及銅所組成的群組。本發(fā)明所述的制備多孔球狀鐵基合金粉的方法,其中,該金屬合金粉為包括至少一合金用金屬元素的一鐵系合金粉,該合金用金屬元素選自于鉻、硅、釩、錳以及鈮所組成的群組。本發(fā)明所述的制備多孔球狀鐵基合金粉的方法,其中,該金屬氧化物粉選自于氧化鎳粉、氧化鉬粉、氧化鎢粉以及氧化銅粉所組成的群組。本發(fā)明所述的制備多孔球狀鐵基合金粉的方法,其中,該多孔球狀鐵基合金粉包括重量百分比小于7wt%的鎳以及至少一重量百分比分別小于1wt%的強化元素,其余為鐵,其中,該強化元素選自于鉬、鉻、釩、鎢、碳、銅、鈮、錳及硅所組成的群組。為達上述目的,本發(fā)明還提供一種多孔球狀鐵基合金粉,為上述制備多孔球狀鐵基合金粉的方法制造得到。為達上述目的,本發(fā)明更提供一種鐵基合金燒結(jié)體,為使用上述制備多孔球狀鐵基合金粉的方法得到的多孔球狀鐵基合金粉經(jīng)由一燒結(jié)工藝得到。本發(fā)明發(fā)現(xiàn)在低于700℃的還原溫度對該球狀噴霧造粒粉進行還原后,可得到外觀為球狀且具有大量孔洞的多孔球狀鐵基合金粉,其中,球狀的特性可提高流動性,以利干壓成形時容易進入模穴;而多孔結(jié)構(gòu)可提供高比表面積,可幫助燒結(jié)反應(yīng),因而得到高燒結(jié)密度。由于本發(fā)明采用該氧化鐵粉,其成本較羰基鐵粉或其他細鐵粉為低,且還原溫度低,故可達到降低成本的功效。另一方面,當(dāng)該含有金屬的粉末采用一合金元素粉時,因還原溫度較低,該合金元素粉不會擴散至鐵粉的內(nèi)部,無法均質(zhì)化,故可保留還原后鐵粉的低硬度及高壓縮性,較容易得到高生胚密度,而高生胚密度又有助于得到高燒結(jié)密度。此外,又因為本發(fā)明方法的還原溫度低,可添加一些碳粉,如石墨粉或碳黑粉,這些碳有助于一部分的氧化鐵粉及金屬氧化物粉還原,且不會擴散至鐵粉的內(nèi)部,故也可避免壓縮性降低的問題。相對地,一般制作還原鐵粉時使用高溫還原時,雖還原速度快,但卻會造成粉末硬度提高,導(dǎo)致壓縮性降低,以及燒結(jié)性變差,無法燒結(jié)至高密度等問題。附圖說明圖1為本發(fā)明一實施例的步驟流程圖。圖2為實施例1的多孔球狀鐵基合金粉的電子顯微鏡照片。具體實施方式涉及本發(fā)明的詳細說明及技術(shù)內(nèi)容,請參閱圖1所示一實施例的步驟流程圖。如圖所示,本發(fā)明為一種制備多孔球狀鐵基合金粉的方法、其粉末和燒結(jié)體,該方法包含下列步驟:步驟1:將一氧化鐵粉與一含金屬的粉末混合形成一混合粉末。該氧化鐵粉可為三氧化二鐵(Fe2O3)或四氧化三鐵(Fe3O4),且平均粒徑介于0.1μm至5μm之間,該含金屬的粉末可為一金屬元素粉、一金屬合金粉、一金屬氧化物粉或其組合,該金屬元素粉可為鎳(Ni)、鉬(Mo)、鎢(W)、銅(Cu)或其組合,該金屬合金粉為包括至少一合金用金屬的一鐵系合金粉,該合金用金屬可為鉻(Cr)、硅(Si)、釩(V)、錳(Mn)、鈮(Nb)或其組合,如Fe-Si、Fe-Cr-Mn粉等,而該金屬氧化物粉可為氧化鎳(NiO)、氧化鉬(MoO3)、氧化鎢(WO3)、氧化銅(CuO)、氧化亞銅(Cu2O)或其組合。步驟2:對該混合粉末進行一噴霧造粒工藝,使該混合粉末形成一球狀噴霧造粒粉。步驟3:將該球狀噴霧造粒粉置于一還原環(huán)境并加熱至一還原溫度,該還原溫度低于700℃,以得到一多孔球狀鐵基合金粉,該多孔球狀鐵基合金粉具有一大于0.9m2/g的比表面積,于本發(fā)明的一實施例中,該多孔球狀鐵基合金粉的該比表面積為介于0.9m2/g和20m2/g之間。該還原環(huán)境可為一純氫氣氣氛、一裂解氨氣氣氛或其他含氫氣氛,該還原溫度較佳地介于500℃至700℃之間,該多孔球狀鐵基合金粉的粒徑介于5μm至80μm之間,且該多孔球狀鐵基合金粉的該比表面積大于0.9m2/g。于本發(fā)明的一實施例中,該多孔球狀鐵基合金粉可進一步含有重量百分比小于7wt%的鎳以及至少一重量百分比分別小于1wt%的強化元素,而其余為鐵(Fe)。該強化元素可為鉬、鉻、釩、鎢、碳、銅、錳、鈮或硅等元素,其中,鉬、鉻、釩、鎢、碳、銅、鈮、錳或硅的重量百分比小于1wt%,如此一來,可提供強化的功效。于本發(fā)明中,該多孔球狀鐵基合金粉的成分可為各種商用鐵基合金,并根據(jù)該氧化鐵粉與該含金屬的粉末的比例以及所選用的該含金屬的粉末的種類調(diào)配得到。于本發(fā)明的一實施例中,該氧化鐵粉與該含金屬的粉末還可進一步和一碳粉混合,該碳粉可為一石墨粉或一碳黑粉,將有助于一部分的該氧化鐵粉或該金屬氧化物粉還原,因該還原溫度較低,碳將不會擴散至鐵粉的內(nèi)部,故可避免壓縮性降低的問題。進一步具體說明本發(fā)明制備多孔球狀鐵基合金粉的方法的內(nèi)容,請續(xù)參閱下述依據(jù)本發(fā)明方法進行的具體實施例以及非采本發(fā)明方法進行的對比例,表1所示為各實施例及對比例的化學(xué)組成,表2所示為各實施例和對比例的工藝條件、還原得到的多孔球狀鐵基合金粉的粒徑、比表面積、生胚密度(%)和燒結(jié)密度(%)。在以下各實施例和對比例中,該還原環(huán)境是采用氫氣氣氛。表1各實施例和對比例所使用的化學(xué)組成(wt%)編號Fe2O3Fe3O4NiONi316L不銹鋼MoC組成191.1--4.9--3.50.5--組成293--5.4----0.61組成3--97--2--0.50.5表2實施例1至4和對比例1至3的工藝條件、粒徑、比表面積和生胚密度與燒結(jié)密度實施例1~2:是采用組成1的混合粉末,其中三氧化二鐵粉末的平均粒徑為0.3μm,316L不銹鋼粉含有17wt%的鉻、10.4wt%的鎳、2.2wt%的鉬、1.6wt%的錳、0.6wt%的硅,且其平均粒徑為8μm,鉬粉的平均粒徑為3μm,此混合粉末加入黏結(jié)劑、塑化劑及水后,經(jīng)該噴霧造粒工藝后得到球狀的噴霧造粒粉,經(jīng)由剖面檢查無中空大孔洞。將此噴霧造粒粉末分別于600℃、650℃的還原溫度下,經(jīng)過3小時進行還原,所得到的多孔球狀鐵基合金粉,比表面積分別為4.55m2/g和3.20m2/g,生胚密度在70%以上,壓縮性佳,而燒結(jié)密度分別達98.9%和97.9%。圖2為實施例1的多孔球狀鐵基合金粉的電子顯微鏡照片,由照片可清楚看到,該多孔球狀鐵基合金粉是 呈良好的球狀,且具有大量的微細孔洞,保留了大量的表面積,也即保留了大量的燒結(jié)驅(qū)動力。經(jīng)由剖面檢查此微細孔洞與還原后的細鐵粉均勻分布,心部無中空大孔,所以流動性佳,適合干壓成形用。實施例3:是采用組成2的混合粉末,于600℃的還原溫度下,經(jīng)過3小時進行還原,所得到的多孔球狀鐵基合金粉,比表面積為2.56m2/g,生胚密度在70%以上,壓縮性佳,而燒結(jié)密度達94.6%。由高倍率電子顯微鏡可清楚看到該多孔球狀鐵基合金粉是呈良好的球狀,且具有大量的孔洞。實施例4:是采用組成3的混合粉末,于700℃的還原溫度下,經(jīng)過3小時進行還原,所得到的多孔球狀鐵基合金粉,比表面積為1.26m2/g,而燒結(jié)密度達95.6%。該多孔球狀鐵基合金粉是呈良好的球狀,且具有大量的孔洞。對比例1~2:是采用組成1的混合粉末,于750℃、800℃的還原溫度下,經(jīng)過3小時進行還原所得到的鐵基合金粉,比表面積僅為0.20m2/g和0.08m2/g,生胚密度分別為79.2%及79.4%,比實施例高,但燒結(jié)密度卻僅91.5%和89.7%。該鐵基合金粉雖略呈球狀,但幾乎不具孔洞,所以比表面積小,燒結(jié)驅(qū)動力低。對比例3:是采用組成2的混合粉末,于750℃的還原溫度下,經(jīng)過3小時進行還原,所得到的鐵基合金粉,比表面積僅為0.86m2/g,生胚密度為73.1%,燒結(jié)密度僅92.6%。綜上所述,本發(fā)明發(fā)現(xiàn)在低于700℃的還原溫度對該球狀噴霧造粒粉進行還原后,可得到外觀為球狀且具有大量孔洞的多孔球狀鐵基合金粉,其中,球狀且心部無中空大孔洞的特性可提高流動性,以利干壓成形時容易進入模穴;而多孔性可提供高比表面積,可幫助燒結(jié)反應(yīng),因而得到高燒結(jié)密度。此外,因還原溫度低,合金元素及碳尚未與鐵反應(yīng)形成合金,所以粉末硬度仍低,壓縮性佳。其次,由于本發(fā)明采用該氧化鐵粉,經(jīng)本發(fā)明的工藝后其整體成本仍遠較常用的羰基鐵粉或其他細鐵粉為低,故可達到降低成本的功效。另一方面,當(dāng)該含有金屬的粉末采用一合金用的元素粉如鎳粉時,因還原溫度較低,該合金元素粉無法均質(zhì)化,故可保留該氧化鐵粉的低硬度及高 壓縮性,較容易得到高生胚密度,而高生胚密度又有助于得到高燒結(jié)密度。此外,又因為本發(fā)明方法的還原溫度低,可添加一些碳粉,如石墨粉或碳黑粉,這些碳有助于將一部分的氧化鐵粉及金屬氧化物粉還原,且不會擴散至鐵粉的內(nèi)部而形成高硬度的鋼,故可避免壓縮性降低的問題。相對地,使用高溫還原時雖還原速度快,但卻會造成粉末硬度提高,導(dǎo)致壓縮性降低,燒結(jié)密度偏低的問題。當(dāng)然,本發(fā)明還可有其它多種實施例,在不背離本發(fā)明精神及其實質(zhì)的情況下,熟悉本領(lǐng)域的技術(shù)人員可根據(jù)本發(fā)明作出各種相應(yīng)的改變和變形,但這些相應(yīng)的改變和變形都應(yīng)屬于本發(fā)明權(quán)利要求的保護范圍。當(dāng)前第1頁1 2 3