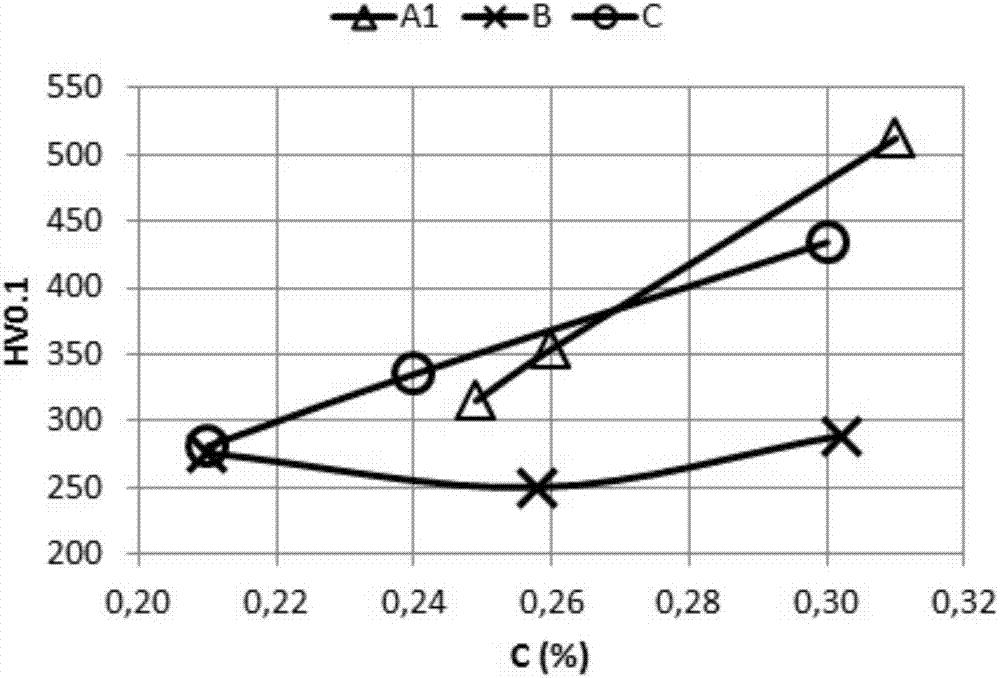
發(fā)明領域本發(fā)明涉及預合金化鐵基粉末。本發(fā)明特別涉及包括少量合金元素的預合金化鐵基粉末,以成本有效地制造燒結零件,特別是齒輪。背景在工業(yè)中,通過壓實和燒結金屬粉末組合物制成的金屬產品的應用變得越來越廣泛。生產具有各種形狀和厚度的許多不同產品。質量要求不斷提高,同時希望降低成本。使用單軸壓制的粉末冶金(pm)技術能夠成本有效地制造部件,尤其是在長序列中制造復雜部件時,因為不需要昂貴的機械加工就可制造凈形狀(netshape)或近凈形狀部件。但是,使用單軸壓制的pm技術的一個缺點在于,燒結零件表現出一定孔隙度,這可能不利地影響該零件的機械性質。pm工業(yè)內的發(fā)展因此涉及基本沿兩個不同的發(fā)展方向克服孔隙度的負面影響。一個方向是通過將粉末壓實至較高生坯密度(gd)、促進燒結至高燒結密度(sd)和/或在生坯體(greenbody)收縮至高sd的條件下進行燒結來降低孔隙量。也可以通過不同種類的表面致密化操作除去部件表面區(qū)域(在此孔隙度對機械性質最有害)的孔隙以消除孔隙度的負面影響。另一發(fā)展路徑集中于添加到鐵基粉末中的合金元素。合金元素可作為混合粉末添加;完全預合金化到基礎鐵粉中;或通過所謂擴散結合法結合到基礎鐵粉的表面上。碳通常以石墨形式混入以避免粉末硬度的有害提高和可壓縮性的降低(如果預合金化)。其它常用合金元素是銅、鎳、鉬和鉻。但是,合金元素,尤其是鎳、銅和鉬的成本使得這些元素的添加不那么有吸引力。在廢料再循環(huán)過程中銅也會累積,因此此類再循環(huán)材料不適用于不需要銅或需要最低限度銅的許多鋼等級。由于低成本和優(yōu)異的可硬化效應,鉻更有吸引力。us4266974公開了僅含錳和鉻作為有意加入的合金元素的在所要求保護的范圍外的合金粉末的實例。這些實例含有2.92%的鉻及0.24%的錳,4.79%的鉻及0.21重量%的錳,或0.55%的鉻及0.89重量%的錳。jp59173201公開了含有鉻、錳和鉬的低合金鋼粉的還原退火方法。一個實例顯示具有1.14重量%的鉻含量和1.44重量%的錳含量作為僅有的有意加入的合金元素的粉末。在us6348080中公開了鉻、錳和鉬基預合金化鋼粉。wo03/106079公開了具有比us6348080中描述的鋼粉低的合金元素含量的鉻、錳和鉬合金化鋼粉。該粉末適合在高于大約0.4重量%的碳含量下形成貝氏體結構。近年來,工業(yè)中對通過pm工藝制造用于汽車用途的部件,如齒輪和同步轂(synchronizationhub)表現出提高的興趣,因為此類部件在長序列(longseries)中制造并通常具有適合這種制造法的尺寸和形狀。但是,已經表明,難以獲得對此類部件而言足夠的強度和硬度以耐受此類部件經受的惡劣環(huán)境。為了克服這些問題,必須采用附加工藝步驟,如表面致密化,以獲得足夠的表面硬度和尺寸公差(dimensionaltolerance)。也遇到與燒結部件的硬化相關的問題,因為在采用通過在常壓下氣體滲碳接著在油中淬火的傳統(tǒng)表面硬化工藝時,該部件中的孔隙率使得難以控制表面硬化層深度。此外,pm齒輪的傳統(tǒng)表面硬化造成含有氧化敏感的合金元素,例如鉻的粉末材料氧化的問題。因此,需要用于制造針對高負荷狀況(stressfulconditions)的pm部件的改進的材料和方法。發(fā)明概述能夠更好控制pm零件的表面硬化層深度以及將cr合金材料的氧化問題減至最低的一種備選的表面硬化法是低壓滲碳(lpc)和隨后高壓氣淬(hpgq)。結合高溫真空燒結與通過lpc-hpgq法熱處理的爐技術提供成本有效地制造優(yōu)質pm部件,如齒輪和同步轂的優(yōu)異可能性。這種技術也非常適用于加工成本有效的鉻合金粉末鋼材料。用于例如齒輪和同步轂的此類粉末材料的關鍵特征是高可壓縮性(能夠壓實至高部件密度)、高純度(以避免夾雜物對機械性質的有害作用)和對lpc-hpgq法優(yōu)化的可硬化性(以在氣淬(gasquenching)后在齒輪中提供所需微結構)。本發(fā)明包括旨在具有所有上述關鍵特征的新型低成本低(lean)預合金化鐵基粉末。因此,盡管該合金粉末中的合金元素含量低并且與傳統(tǒng)油淬火相比hpgq的冷卻速率相對較低,但該材料的可硬化性足以提供通過該新型方法制成的pm部件,如齒輪和同步轂的優(yōu)異性質。術語低壓滲碳在本文中也意在包括低壓碳氮共滲(carbonitriding)。詳述在本發(fā)明的第一方面中,提供一種預合金化鐵基粉末,其由下列成分構成:-0.7-0.9重量%的鉻(cr);-0.2-0.4重量%的鉬(mo);-0.01-0.15重量%的錳(mn);-最多0.20重量%的氧(o);-最多0.05重量%的碳(c)-少于0.05重量%的氮(n)-最多0.3的其它不可避免的雜質;和-余量鐵(fe)。在第一方面的一個實施方案中,提供一種預合金化鐵基粉末,其中o量為最多0.15重量%。在第一方面的另一實施方案中,提供一種預合金化鐵基粉末,其中mn的量為0.09-0.15重量%。在第一方面的另一實施方案中,提供一種預合金化鐵基粉末,其中mn的量為0.01-0.09重量%。在第一方面的另一實施方案中,提供一種預合金化鐵基粉末,其中如根據astmb796-02測得,其最長維度大于100微米的夾雜物的數量為最多1.0/cm2。在第一方面的另一實施方案中,提供一種預合金化鐵基粉末,其中如根據astmb796-02測得,其最長維度大于150微米的夾雜物的數量為最多0.0/cm2。在本發(fā)明的第二方面中,提供一種鐵基粉末混合物,其包含或含有:-根據第一方面或實施方案的預合金化鐵基粉末;-所述鐵基粉末混合物的0.2-0.7重量%的量的石墨;-任選地,所述鐵基粉末混合物的最多1重量%的量的潤滑劑;-任選地,所述鐵基粉末混合物的最多1重量%的量的機械加工性增強劑;和-任選地,硬相材料。在本發(fā)明的第三方面中,提供一種制造燒結部件的方法,其包含步驟:-a)提供根據權利要求8的鐵基粉末混合物;-b)將所述鐵基粉末混合物轉移到壓實模具中;-c)在至少600mpa的壓實壓力下將所述鐵基粉末混合物壓實成生壓坯(greencompact);-d)從模具中推出所述生壓坯;-e)對所述生壓坯施以燒結步驟;-f)任選進一步增密(densify)所述燒結部件;-g)在含碳氣氛中在最多40毫巴,優(yōu)選最多20毫巴的壓力下對所述燒結部件施以低壓滲碳(lpc);-h)在10至30巴的壓力下和以至少5℃的冷卻速率從大約850-1000℃的溫度到至少低于大約300℃對所述滲碳部件施以高壓氣淬hpgq;和-i)任選在空氣中在150-300℃的溫度下對所述淬火部件施以回火。在本發(fā)明的第三方面的一個實施方案中,提供一種方法,其中推出后的生壓坯(來自上述步驟d)具有至少7.10克/立方厘米,優(yōu)選至少7.15克/立方厘米,最優(yōu)選至少7.20克/立方厘米的生坯密度。在本發(fā)明的第三方面的一個實施方案中,提供一種方法,其中所述燒結步驟包括在還原氣氛中或在在最多20毫巴壓力下的真空中在1000℃至1350℃,優(yōu)選1200℃至1350℃的溫度下燒結。在本發(fā)明的第三方面的一個實施方案中,提供一種方法,其中燒結過程中的還原氣氛含有氫氣。在本發(fā)明的第三方面的一個實施方案中,步驟f)由表面致密化或熱等靜壓(hotisostaticpressing,hip)構成。在本發(fā)明的第三方面的一個實施方案中,提供一種方法,其中低壓滲碳步驟包括在含有c2h2、ch4和c3h8的至少一種的氣氛中滲碳。在本發(fā)明的第三方面的一個實施方案中,提供一種方法,其中所述低壓滲碳步驟進一步包括在含氨氣氛中滲碳。在本發(fā)明的第四方面中,提供通過第三方面或實施方案獲得的部件。在本發(fā)明的第五方面中,提供一種燒結部件,其由下列成分構成:-0.7-0.9重量%的鉻(cr),-0.2-0.4重量%的鉬(mo),-0.01-0.15重量%的錳(mn),-0.2-1.0重量%的碳(c)-最多0.15重量%的氧(o),-最多1.0%,優(yōu)選低于0.5重量%,最優(yōu)選低于0.3重量%的非o的不可避免的雜質-余量鐵(fe)在本發(fā)明的第五方面的一個實施方案中,提供一種燒結部件,其特征在于所述部件是齒輪。在本發(fā)明的第五或第四方面的一個實施方案中,提供一種燒結部件,其特征在于齒輪齒表面微硬度為至少700hv0.1,且齒輪齒芯(gearteethcore)硬度為300-550hv0.1。鐵基預合金化鋼粉的制備可通過含有指定量合金元素的鋼熔體在保護性或非保護性氣氛中的水霧化制造鋼粉。可進一步對該霧化粉末施以如經此引用并入本文的us6,027,544中所述的還原退火法。該鋼粉的粒度可以為任何尺寸,只要其與壓制和燒結或粉末鍛造法相容。在優(yōu)選的粒度分布中,如根據ss-en24-497測得,20重量%或更少的粉末高于150微米,且最多30重量%或更少的粉末低于45微米。在另一優(yōu)選粒度分布中,10重量%或更少的粉末高于75微米且至少30重量%或更多的粉末低于45微米。鋼粉的含量鉻cr用于通過固溶體硬化(solidsolutionhardening)增強該基質。cr還提高燒結體的可硬化性和耐磨性。但是,高于鐵基粉末的0.9重量%的cr含量會降低該鋼粉的可壓縮性。低于0.7重量%的cr含量對所需性質,如可硬化性和耐磨性的作用不足。低于0.7重量%cr時,獲得僅微不足道的可壓縮性提高。鉬mo,如同cr,通過固溶體硬化增強該基質并提高可硬化性。但是,與cr相比,mo對鋼粉的可壓縮性具有較低負面影響并對燒結部件具有較高可硬化性作用。但是,mo相對昂貴。因此mo含量為該鐵基粉末的0.2-0.4重量%。錳mn,如同cr,提高鋼粉的強度、硬度和可硬化性。但是,低mn含量通常合意,且高于0.15重量%的含量會不利地增加鋼粉中的含錳夾雜物的形成,也會由于固溶體硬化和提高的鐵素體硬度而對可壓縮性具有負面影響。如果mn含量低于0.01重量%,獲得如此低含量的成本不合理地高。對于mn的正面作用比負面作用占優(yōu)勢的一些用途,0.09-0.15重量%的較高mn區(qū)間是合意的。對于另一些用途,例如承受高負荷的部件,較低mn含量是合意的,如在0.01-0.09重量%區(qū)間內的mn含量。氧o優(yōu)選為最多0.20重量%,以防止與鉻和錳形成氧化物,因為這些氧化物損害該粉末的強度和可壓縮性。由于這些原因,o優(yōu)選為最多0.15重量%。該鋼粉中的碳c應該為最多0.05重量%,更高含量會不可接受地降低該粉末的可壓縮性。由于相同原因,氮n應保持少于0.05重量%。包括o、c和n的不可避免的雜質的總量應小于1.0重量%,優(yōu)選地,除o、c和n外的不可避免的雜質的總量應該最多0.3重量%以不損害鋼粉的可壓縮性或充當有害夾雜物的前體(former)。部件如齒輪或同步轂用于例如汽車用途的前提條件是高的防故障可靠性,這尤其與高和受控疲勞強度相關聯。為了獲得所需性質,不僅合金元素cr和mo的精確和謹慎的組合是重要的,該鋼粉中的夾雜物的低數量和受控最大尺寸也是重要的。該新型預合金化鐵基粉末的特征在于最長維度大于100微米的夾雜物的數量為最多1.0/cm2。最長維度大于150微米的夾雜物的數量為最多0.0/cm2,如根據astmb796-02測得。鐵基粉末混合物組合物在壓實之前,將該鐵基鋼粉與石墨和潤滑劑混合。以該組合物的0.2-0.7重量%的量加入石墨,并以該組合物的0.05-1.0重量%的量加入潤滑劑。在某些實施方案中,可以各自以最多2重量%的量加入粉末形式的銅和/或鎳。石墨為了提高該燒結部件的強度和硬度,在基質中引入碳。碳以石墨形式以該組合物的0.2-0.7重量%的量添加。少于0.2重量%的量會導致太低的強度,高于0.7%的量會導致太高的硬度、不足的伸長和損害最終部件的可機械加工性。獲得300-550hv0.1的芯硬度所需的在鐵基粉末混合物的0.2-0.7重量%區(qū)間內的確切石墨量取決于部件尺寸和冷卻速率并可由本領域技術人員確定。銅和/或鎳銅cu和鎳ni是粉末冶金技術中常用的合金元素。cu和ni會通過固溶體硬化提高強度和硬度。cu也促進燒結過程中燒結頸的形成,因為cu在達到燒結溫度之前熔融,以提供比固態(tài)燒結快得多的所謂的液相燒結。在某些實施方案中,cu和/或ni可以各自以最多2重量%的量添加到該鐵基粉末混合物中。潤滑劑將潤滑劑添加到該組合物中以促進壓實和壓實部件的推出。少于該組合物的0.05重量%的潤滑劑的添加具有微不足道的作用,高于該鐵基粉末混合物的1重量%的添加會造成壓實體的低密度。潤滑劑可選自金屬硬脂酸鹽、蠟、脂肪酸及其衍生物、具有潤滑作用的低聚物、聚合物和其它有機物。其它物質可以加入其它物質,如硬相材料和機械加工性增強劑,如mns、mos2、caf2、不同種類的礦物等。制造燒結部件的方法固結將該鐵基粉末混合物轉移到模具中并通過例如至少600mpa的單軸壓實壓力施以固結至至少7.10克/立方厘米,優(yōu)選至少7.15克/立方厘米,最優(yōu)選至少7.20克/立方厘米的生坯密度。燒結所得壓實生坯部件進一步在還原氣氛,如90體積%氮氣和10體積%氫氣中在大氣壓下或在減壓下(在例如最多20毫巴壓力下的所謂真空燒結)在1000-1350℃,優(yōu)選1200-1350℃的溫度下燒結15分鐘至120分鐘。在真空燒結的一個優(yōu)選實施方案中,使用氫氣或氫氣和氮氣的混合物作為低壓還原氣氛以確保部件中的氧化物的有效還原。任選進一步致密化在燒結步驟后,可以對該燒結部件施以任選的進一步致密化,如hip或通過例如表面輥軋的表面致密化。硬化在燒結后,在含有含碳物質,如ch4、c2h2和c3h8或其混合物的低壓氣氛(即最多40毫巴,優(yōu)選最多20毫巴)中對該部件施以表面硬化工藝(即低壓滲碳,lpc)。在溫度已從燒結溫度降至比奧氏體化溫度高最多大約100℃的溫度(即850-1000℃的溫度)時,在爐中引入該含碳物質?;蛘撸绻摬考跓Y后冷卻至比850-1000℃低的溫度,在lpc爐中引入含碳物質前將該部件加熱到比奧氏體化溫度高最多大約100℃的溫度。在滲碳溫度下的總停留時間為大約15-120分鐘。通過在奧氏體化溫度以上的低和受控溫度下進行滲碳,可以將該部件的晶粒生長和變形減至最低。在短時期內將含碳物質引入爐中,有時被稱作增進周期(boostcycle)。該增進周期可重復多次。在各增進周期后接著可被稱作擴散周期的時期。當作為低壓滲碳進行l(wèi)pc工藝時,也將含氮物質(優(yōu)選為氨形式)引入爐中。淬火在滲碳步驟后,該部件在惰性氣氛中在高壓下淬火,即高壓氣淬hpgq。淬火氣體的實例是氮氣、n2和氦氣he。在10至30巴的壓力下進行淬火,以使從大約850-1000℃的溫度到至少低于大約300℃的冷卻速率為至少5℃/s?;鼗馂榱讼龖?,可以在空氣中在150-300℃的溫度下對該最部件施以回火15-120分鐘。最終部件的性質根據本發(fā)明的預合金化鐵基粉末和指定制造法的組合能夠制造例如齒輪,其中輪齒具有硬馬氏體表面層和主要由貝氏體和/或珠光體構成的較軟芯。該馬氏體表面層應具有最低700hv0.1的微硬度并且芯微硬度應優(yōu)選為300-550hv0.1。這樣的齒輪具有有利的應力分布,即在表面層中有利的壓縮應力。此外,最終pm齒輪部件具有大約0.3-1.5mm的嚴格控制的表面硬化層深度,即其中硬度為550hv0.1。圖例圖1顯示實施例1中研究的材料的極限抗拉強度(uts)vs碳含量。圖2顯示實施例1中研究的材料的微硬度(hv0.1)vs碳含量。圖3顯示實施例2中所用的pm齒輪樣品(以毫米測量)。圖4顯示實施例2中的熱處理試樣的齒輪齒橫截面的金相圖。圖5顯示在實施例2中的熱處理試樣的齒輪齒上測得的微硬度(hv0.1)分布圖。圖6顯示試樣(在用700mpa壓實壓力單軸壓實后)的生坯密度(gd)(可壓縮性)vs實施例3中的試驗混合物中所用的預合金化鋼粉的cr含量。實施例實施例1根據本發(fā)明的預合金化鋼粉a1通過水霧化、接著還原退火工藝制造。在小型(15千克熔體量)水霧化裝置中在保護性n2氣氛中進行霧化。在實驗室規(guī)模的帶式爐中在h2氣氛中在1000-1100℃的溫度下進行退火。在退火后進行粉末的研磨和篩分(-212m)。該粉末的化學組成與其它兩種商業(yè)級預合金化鋼粉(b=85mo,c=可獲自ab,sweden,并用作參考材料)的組成一起列在表1中。所有三種粉末具有用于pm的標準粒度分布并用-212μm篩網尺寸篩分。表1.化學組成(重量%)粉末fe(%)cr(%)mo(%)mn(%)o(%)c(%)a1基礎0.900.340.030.03<0.01b基礎0.030.850.090.07<0.01c基礎1.800.040.090.14<0.01通過圓柱形試樣(直徑25毫米,高度20毫米)在潤滑模頭中在600mpa壓實壓力下的單軸壓實評估鋼粉的可壓縮性。通過根據阿基米德原理在空氣和水中稱重試樣,測量各試樣的生坯密度(gd)。結果列在表2中并且表明粉末a1具有明顯優(yōu)于粉末c的可壓縮性和與粉末b相當的可壓縮性。表2.可壓縮性(600mpa壓實壓力,潤滑模頭)粉末gd(g/cm3)a17.13b7.15c7.05將鋼粉與0.25-0.35重量%石墨(kropfmühluf4)和0.60重量%潤滑劑(lubee,可獲自ab,sweden)混合。由該粉末混合物通過在700mpa的壓實壓力下單軸壓實制造根據iso2740的標準拉伸試驗棒。該試驗棒的生坯密度為大約7.25克/立方厘米。該試驗棒在n2/h2(95/5)氣氛中在1120℃下燒結30分鐘。燒結試樣的熱處理在真空(10毫巴)中在920℃下進行60分鐘,接著用20巴n2高壓氣淬。在這種熱處理操作中不進行滲碳,因為該實驗的目的是評估該合金在通過將石墨添加到該粉末混合物中得出的碳含量下的可硬化性。隨后在空氣中在200℃下進行回火60分鐘。對熱處理的試樣進行拉伸試驗。試驗結果表明a1和c在研究的碳含量范圍內具有大約750-1130mpa的類似極限抗拉強度(uts)值;見圖1。材料b在所有碳含量下具有低于600mpa的明顯更低uts值。也在熱處理的試樣的拋光橫截面上進行微硬度測量(根據vickers方法的hv0.1);見圖2中的結果。材料a1在0.25-0.31%c范圍內的碳含量下具有310-510hv0.1的微硬度值。材料b甚至在最高評估碳含量(0.30%c)下也具有低于300hv0.1的相對較低微硬度。材料c的微硬度值與材料a1比較相當。這一實施例證實粉末a1具有pm齒輪材料的性質的有吸引力的組合。高可壓縮性允許壓實到高密度,且可硬化性足以提供300-550hv0.1的微硬度值。這是在用于高負荷傳動用途的齒輪制造中在表面硬化后齒輪齒芯硬度的所需硬度范圍。評估的碳含量相當于在齒輪齒的芯區(qū)域中的典型碳含量。實施例2根據本發(fā)明的預合金化鋼粉a2通過水霧化、接著還原退火工藝制造。在小型(15千克熔體量)水霧化裝置中在保護性n2氣氛中進行霧化。在實驗室規(guī)模的帶式爐中在h2氣氛中在1000-1100℃的溫度下進行退火。在退火后進行粉末的研磨和篩分(-212m)。該粉末的化學組成列在表2中。該粉末具有用于pm的標準粒度分布并用-212μm篩網尺寸篩分。表2.化學組成(重量%)粉末fe(%)cr(%)mo(%)mn(%)o(%)c(%)a2基質0.850.300.040.06<0.01將粉末a2與0.40重量%石墨(c-uf)和0.60重量%潤滑劑(lubee)混合。由該粉末混合物通過在700mpa的壓實壓力下單軸壓實,壓實大齒輪試樣(參見圖3中的尺寸)。該齒輪試樣的生坯密度為7.20克/立方厘米。該齒輪試樣在n2/h2(95/5)氣氛中在1250℃下燒結30分鐘。通過在965℃下低壓滲碳(lpc)接著用20巴n2高壓氣淬進行燒結齒輪的表面硬化。lpc工藝中的基礎氣氛是n2(8毫巴壓力)且滲碳氣體是c2h2/n2(50/50)。施加四個滲碳增進周期,各增進周期的長度為37-65秒。各增進周期后的擴散時間在312-3550秒之間不等。在965℃下的總時間為96分鐘。在氣淬后隨后在空氣中在200℃下進行回火60分鐘。對熱處理的齒輪試樣的拋光和蝕刻橫截面進行的金相檢查表明,該齒輪齒具有馬氏體表面層和貝氏體芯結構;見圖4。也在拋光橫截面上進行微硬度測量(根據vickers方法的hv0.1)以研究齒輪齒的硬度分布圖,見圖5中的結果。這些測量表明表面硬度高于800hv0.1且芯硬度為320-340hv0.1,齒根處的硬度水平略低于側面。表面硬化層深度(其中硬度為550hv0.1)在側面為0.8毫米且在根部為0.6毫米。這一實施例證實粉末a2適用于在通過lpc-hpgq法進行表面硬化的方法中制造高強度pm齒輪。在該粉末混合物中使用該鐵基粉末混合物的0.40重量%的石墨含量以在施加hpgq時在大齒輪部件內獲得的冷卻速率下為該合金提供足夠的可硬化性。該粉末的高可壓縮性允許壓實到齒輪的高密度,并在熱處理后在齒輪齒的表面處和在芯區(qū)域中都獲得所需水平的硬度值。也實現界限分明的表面硬化層深度。實施例3通過水霧化、接著還原退火工藝制造具有不同cr含量(0.5-1.0%)和相同mo含量(0.3%)的預合金化鋼粉。在小型(15千克熔體量)水霧化裝置中在保護性n2氣氛中進行霧化。在實驗室規(guī)模的帶式爐中在h2氣氛中在1000-1100℃的溫度下進行退火。對所有粉末使用相同退火參數。在退火后進行粉末的研磨和篩分(-212m)。粉末的化學組成列在表3中。表3.化學組成(重量%)粉末fecr(%)mo(%)mn(%)o(%)c(%)x1基礎0.570.300.040.11<0.01x2基礎0.760.320.030.13<0.01x3基礎0.830.320.040.13<0.01x4基礎0.920.330.030.12<0.01x5基礎1.000.320.030.11<0.01將鋼粉與0.25/0.35重量%石墨(kropfmühluf4)和0.60重量%潤滑劑(lubee,可獲自ab,sweden)混合。通過圓柱形試樣(直徑25毫米,高度20毫米)在700mpa壓實壓力下的單軸壓實評估粉末混合物的可壓縮性。通過根據阿基米德原理在空氣和水中稱重試樣,測量各試樣的生坯密度(gd)。結果列在圖6中并且證實具有0.7-0.9重量%cr和0.3重量%mo的合金化含量(符合本發(fā)明)的預合金化鐵基粉末產生高可壓縮性且cr含量應該為最多0.9重量%。低于0.7重量%的cr含量不會顯著提高可壓縮性,即產生更高生坯密度(gd)。當前第1頁12