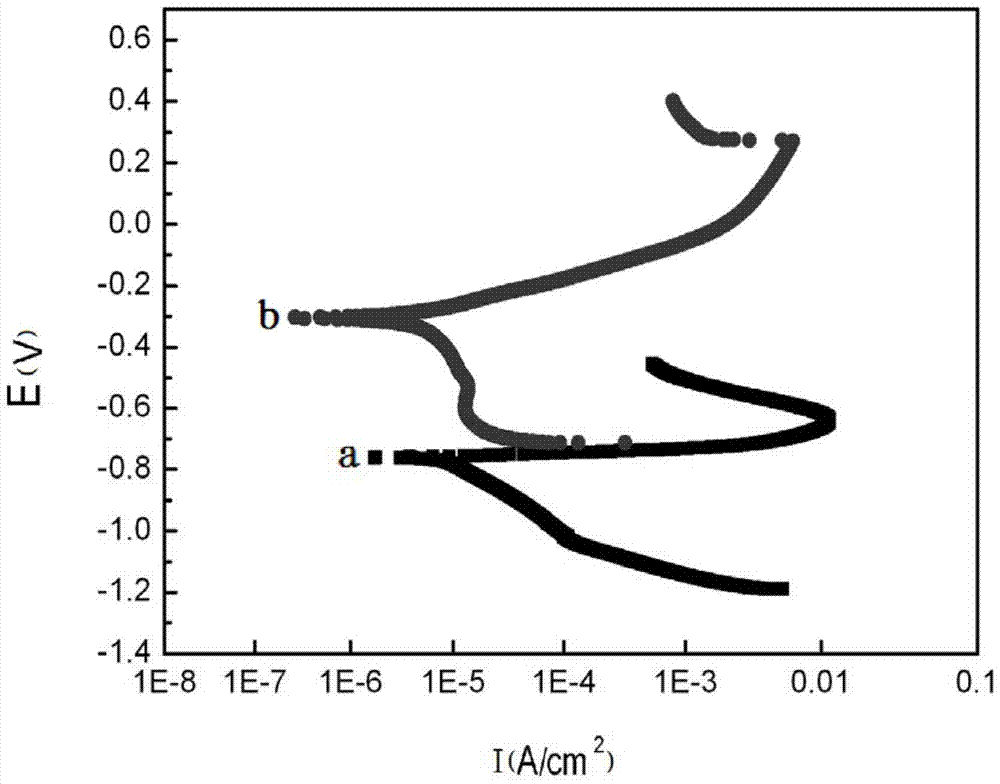
本發(fā)明屬于涂層材料制備技術領域,具體涉及一種在鋼板表面制備耐蝕復合涂層的方法。
背景技術:隨著我國國防工業(yè)和國民經(jīng)濟的發(fā)展,鋼材的應用廣泛,特別是海洋事業(yè)的發(fā)展,對海上水下工程提出了越來越高的要求。材料的高強度和高耐海水腐蝕性能是水下工程的關鍵指標之一。鋼材是最常用的結構材料,具有一系列優(yōu)良的性能,如力學性能、焊接性能、熱穩(wěn)定性能等,且成本相對較低。然而鋼材的耐海洋腐蝕性能遠不如鈦合金,且比重較大。鋼材在海水中的主要腐蝕破壞形態(tài)為點蝕和縫隙腐蝕。國內(nèi)外一些文獻都明確指出,304L和316L試樣全浸在海水中僅經(jīng)歷3~6個月,便因嚴重點蝕和縫隙腐蝕而穿孔,降低了使用壽命。因此、在某些情況下需要將鋼材與鈦連接起來使用,發(fā)揮各自的優(yōu)勢。因此從使用性能角度出發(fā),在鋼材表面制備鈦合金耐蝕涂層是非常有必要的。鋼材中的鐵元素與鈦元素在元素周期表中不同族,鋼材與鈦金屬之間物理、化學和力學性能均差異巨大,采用常規(guī)表面方法在鋼材表面制備鈦合金涂層,容易出現(xiàn)冶金不相容性,在界面易于形成脆性化合物相,以及由于熱物理性能不匹配產(chǎn)生殘余應力等嚴重影響表面質(zhì)量。鋼材表面制備鈦合金耐蝕涂層的主要難點是:互溶性差,由相圖可知,低溫下,F(xiàn)e在α-Ti中的固溶度很小,激光直接熔覆時,二者不發(fā)生反應,成分不均勻,此外,二者的熱導率、比熱容和線膨脹系數(shù)差異均比較大,容易導致連接區(qū)域變形大,不平整。
技術實現(xiàn)要素:本發(fā)明所要解決的技術問題在于針對上述現(xiàn)有技術中的不足,提供一種在鋼板表面制備耐蝕復合涂層的方法,該方法在鋼板表面制備得到的耐蝕復合涂層由鎳過渡層和鈦表面層構成,該耐蝕復合涂層結構致密、表面平整光滑、與基體結合良好且耐蝕性能良好,能夠顯著提高海洋工程用鋼材材料表面的耐蝕性能。為解決上述技術問題,本發(fā)明采用的技術方案是:一種在鋼板表面制備耐蝕復合涂層的方法,其特征在于,包括以下步驟:步驟一、對鋼板表面進行脫脂清洗,然后將脫脂清洗后的鋼板置于電解液中,以鋼板為陰極,以鈦板為陽極,在電流密度為0.1A/dm2~2A/dm2的條件下對所述鋼板進行陰極活化處理;所述電解液為質(zhì)量濃度為2.16%~20%的鹽酸溶液,所述陰極活化處理的時間為1min~5min;步驟二、將步驟一中經(jīng)陰極活化處理后的鋼板置于鎳電鍍液中,以鋼板為陰極,以鈦板為陽極,在電流密度為2A/cm2~5A/cm2的條件下對所述鋼板表面進行電鍍處理,清洗后干燥,得到表面具有鎳過渡層的鋼板;所述鎳電鍍液的溫度為40℃~60℃,鎳電鍍液的pH值為4~6,電鍍處理的時間為1h~5h;步驟三、以金屬鈦粉為粉料,采用同步送粉的方式,在氣壓為0.01MPa~1MPa的氬氣保護氣氛下對步驟二中具有鎳過渡層的鋼板表面進行激光熔覆處理,在鎳過渡層表面得到厚度為0.5mm~1.51mm的鈦表面層,然后將經(jīng)激光熔覆處理后的鋼板按2℃/min~3℃/min冷卻速度冷卻至室溫,在鋼板表面制備得到耐蝕復合涂層;所述激光熔覆處理的激光功率為1000W~8000W,正離焦為10mm~15mm,送粉率為30g/min~50g/min,掃描速度為20mm/s~30mm/s,搭接率為70%~80%。上述的一種在鋼板表面制備耐蝕復合涂層的方法,其特征在于,步驟二中每升所述鎳電鍍液中含氨基磺酸鎳300g~400g,氯化鎳30g~50g,硼酸30g~45g,十二烷基硫酸鈉0.5g~1g。上述的一種在鋼板表面制備耐蝕復合涂層的方法,其特征在于,步驟二中所述鎳過渡層的厚度不小于0.1mm。上述的一種在鋼板表面制備耐蝕復合涂層的方法,其特征在于,步驟二中所述電鍍處理的電流密度為2A/cm2~3A/cm2,鎳電鍍液的溫度為45℃~55℃,鎳電鍍液的pH值為4.5~5,電鍍處理的時間為3h~5h。上述的一種在鋼板表面制備耐蝕復合涂層的方法,其特征在于,所述電鍍處理的電流密度為2.5A/cm2,鎳電鍍液的溫度為50℃,鎳電鍍液的pH值為4.5,電鍍處理的時間為4h。上述的一種在鋼板表面制備耐蝕復合涂層的方法,其特征在于,步驟三中所述激光熔覆處理的激光功率為2500W~7500W,正離焦為12mm~15mm,送粉率為35g/min~45g/min,掃描速度為20mm/s~25mm/s,搭接率為70%~75%。上述的一種在鋼板表面制備耐蝕復合涂層的方法,其特征在于,所述激光熔覆處理的激光功率為6000W,正離焦為15mm,送粉率為40g/min,掃描速度為20mm/s,搭接率為70%。本發(fā)明與現(xiàn)有技術相比具有以下優(yōu)點:1、本發(fā)明在鋼板表面制備得到的耐蝕復合涂層由鎳過渡層和鈦表面層構成,該耐蝕復合涂層結構致密平整,與基體結合良好且耐蝕性能良好,能夠顯著提高海洋工程用鋼材材料表面的耐蝕性能。2、本發(fā)明在具有鎳過渡層的鋼板表面采用激光熔覆的工藝制備鈦表面層,能夠充分發(fā)揮鋼材與鈦金屬在性能和經(jīng)濟上的互補優(yōu)勢,為了在鋼板表面獲得耐蝕性能優(yōu)良的鈦涂層,設計鎳為過渡層,一方面,F(xiàn)e與Ni為同族元素,兩者的相容性好,所以形成的固溶體的性能較好,另一方面,鎳過渡層和鈦表面層之間可以實現(xiàn)Ti-Ni無限固溶,Ti-Ni無限固溶形成的過飽和固溶體相的塑性比Ti-Fe金屬間化合物的塑性優(yōu)良。3、本發(fā)明采用金屬鎳為中間過渡層,能夠顯著改善鋼板和鈦連接處材料界面的狀況,如力學性能、結構和成分均勻性等,有效減少脆性金屬間化合物的生成,顯著改善涂層的表面質(zhì)量,如平整度、缺陷等,大大減少涂層開裂的傾向。4、本發(fā)明制備的鈦表面層能夠與鎳過渡層實現(xiàn)冶金結合,使鋼板能夠適用于極端重載荷的工況,本發(fā)明工藝過程穩(wěn)定性好、適用范圍廣、成本低,適用于大規(guī)模工業(yè)化生產(chǎn)。下面通過附圖和實施例,對本發(fā)明的技術方案做進一步的詳細描述。附圖說明圖1為本發(fā)明實施例1制備的耐蝕復合涂層的SEM照片。圖2為本發(fā)明實施例1制備耐蝕復合涂層前和制備耐蝕復合涂層后鋼板表面的電位極化曲線對比圖。具體實施方式實施例1本實施例包括以下步驟:步驟一、利用超聲波清洗機對鋼板表面進行脫脂清洗,然后將脫脂清洗后的鋼板置于電解液中,以鋼板為陰極,以鈦板為陽極,在電流密度為0.5A/dm2的條件下對所述鋼板進行陰極活化處理;所述電解液為質(zhì)量濃度為4.3%的鹽酸溶液,所述陰極活化處理的時間為5min,所述脫脂清洗的時間為15min,所述鋼板為45#鋼板;步驟二、將步驟一中經(jīng)陰極活化處理后的鋼板置于鎳電鍍液中,以鋼板為陰極,以鈦板為陽極,在電流密度為2.5A/cm2的條件下對所述鋼板表面進行電鍍處理,清洗后干燥,得到表面具有鎳過渡層的鋼板;所述鎳電鍍液的溫度為40℃,鎳電鍍液的pH值為5,電鍍處理的時間為5h,所述鎳電鍍液的溶劑為水,鎳電鍍液中各組分的濃度為氨基磺酸鎳350g/L,氯化鎳40g/L,硼酸40g/L,十二烷基硫酸鈉0.5g/L;步驟三、以金屬鈦粉為粉料,采用同步送粉的方式,在氣壓為0.01MPa的氬氣保護氣氛下對步驟二中具有鎳過渡層的鋼板表面進行激光熔覆處理,在鎳過渡層表面得到厚度約為0.50mm的鈦表面層,然后將經(jīng)激光熔覆處理后的鋼板按2℃/min冷卻速度冷卻至室溫25℃,在鋼板表面制備得到耐蝕復合涂層;所述激光熔覆處理的激光功率為2580W,正離焦為12mm,送粉率為30g/min,掃描速度為30mm/s,搭接率為70%,激光熔覆處理中激光束輸出前預通氬氣5min~10min。從圖1中可以看出,本實施例在鋼板表面制備得到了由厚度約為0.16mm的鎳過渡層和厚度約為0.50mm的鈦表面層構成的耐蝕復合涂層,該復合涂層結構致密平整,與基體結合良好,其中鎳過渡層與鈦表面層之間明顯形成了冶金結合,結合強度較高;圖2中曲線a為制備耐蝕復合涂層前鋼板表面的電位極化曲線(電解液為3.5wt.%的氯化鈉水溶液),曲線b為制備耐蝕復合涂層后鋼板表面的電位極化曲線(電解液為3.5wt.%的氯化鈉水溶液),對比曲線a和曲線b可以看出,制備耐蝕復合涂層后鋼板表面的Icorr<制備耐蝕復合涂層前鋼板表面的Icorr,制備耐蝕復合涂層后鋼板表面的Ecorr>制備耐蝕復合涂層前鋼板表面的Ecorr,Icorr越小,Ecorr越高,表面鋼材的耐蝕性能越好,本實施例制備耐蝕復合涂層后鋼板表面的Icorr=1×10-6A/cm2,Ecorr=-0.3V,制備耐蝕復合涂層前鋼板表面的Icorr=1×10-5A/cm2,Ecorr=-0.75V,說明本實施例在鋼材表面制備的耐蝕復合涂層使鋼材的耐蝕性能得到顯著的提高。實施例2本實施例包括以下步驟:步驟一、利用超聲波清洗機對鋼板表面進行脫脂清洗,然后將脫脂清洗后的鋼板置于電解液中,以鋼板為陰極,以鈦板為陽極,在電流密度為1A/dm2的條件下對所述鋼板進行陰極活化處理;所述電解液為質(zhì)量濃度為2.16%的鹽酸溶液,所述陰極活化處理的時間為2min,所述脫脂清洗的時間為15min,所述鋼板為1Cr17Ni2不銹鋼板;步驟二、將步驟一中經(jīng)陰極活化處理后的鋼板置于鎳電鍍液中,以鋼板為陰極,以鈦板為陽極,在電流密度為2A/cm2的條件下對所述鋼板表面進行電鍍處理,清洗后干燥,得到表面具有鎳過渡層的鋼板;所述鎳電鍍液的溫度為60℃,鎳電鍍液的pH值為4,電鍍處理的時間為3h,所述鎳電鍍液的溶劑為水,鎳電鍍液中各組分的濃度為氨基磺酸鎳300g/L,氯化鎳50g/L,硼酸45g/L,十二烷基硫酸鈉1g/L;步驟三、以金屬鈦粉為粉料,采用同步送粉的方式,在氣壓為0.01MPa的氬氣保護氣氛下對步驟二中具有鎳過渡層的鋼板表面進行激光熔覆處理,在鎳過渡層表面得到厚度約為0.73mm的鈦表面層,然后將經(jīng)激光熔覆處理后的鋼板按3℃/min冷卻速度冷卻至室溫22℃,在鋼板表面制備得到耐蝕復合涂層;所述激光熔覆處理的激光功率為6015W,正離焦為15mm,送粉率為34g/min,掃描速度為30mm/s,搭接率為70%,激光熔覆處理中激光束輸出前預通氬氣5min~10min。本實施例在鋼板表面制備得到了由厚度約為0.11mm的鎳過渡層和厚度約為0.73mm的鈦表面層構成的耐蝕復合涂層,該復合涂層結構致密平整,與基體結合良好,其中鎳過渡層與鈦表面層之間形成了冶金結合,結合強度較高;本實施例制備耐蝕復合涂層后鋼板表面的Icorr=1×10-8A/cm2,Ecorr=-0.08V,制備耐蝕復合涂層前鋼板表面的Icorr=1×10-7A/cm2,Ecorr=-0.3V,說明本實施例在鋼材表面制備的耐蝕復合涂層使鋼材的耐蝕性能得到顯著的提高。實施例3本實施例包括以下步驟:步驟一、利用超聲波清洗機對鋼板表面進行脫脂清洗,然后將脫脂清洗后的鋼板置于電解液中,以鋼板為陰極,以鈦板為陽極,在電流密度為1A/dm2的條件下對所述鋼板進行陰極活化處理;所述電解液為質(zhì)量濃度為10.4%的鹽酸溶液,所述陰極活化處理的時間為1min,所述脫脂清洗的時間為15min,所述鋼板為Q235鋼板;步驟二、將步驟一中經(jīng)陰極活化處理后的鋼板置于鎳電鍍液中,以鋼板為陰極,以鈦板為陽極,在電流密度為3A/cm2的條件下對所述鋼板表面進行電鍍處理,清洗后干燥,得到表面具有鎳過渡層的鋼板;所述鎳電鍍液的溫度為40℃,鎳電鍍液的pH值為5,電鍍處理的時間為5h,所述鎳電鍍液的溶劑為水,鎳電鍍液中各組分的濃度為氨基磺酸鎳400g/L,氯化鎳30g/L,硼酸30g/L,十二烷基硫酸鈉0.8g/L;步驟三、以金屬鈦粉為粉料,采用同步送粉的方式,在氣壓為0.01MPa的氬氣保護氣氛下對步驟二中具有鎳過渡層的鋼板表面進行激光熔覆處理,在鎳過渡層表面得到厚度約為1.42mm的鈦表面層,然后將經(jīng)激光熔覆處理后的鋼板按2℃/min冷卻速度冷卻至室溫23℃,在鋼板表面制備得到耐蝕復合涂層;所述激光熔覆處理的激光功率為7426W,正離焦為12mm,送粉率為45g/min,掃描速度為30mm/s,搭接率為70%,激光熔覆處理中激光束輸出前預通氬氣5min~10min。本實施例在鋼板表面制備得到了由厚度約為0.21mm的鎳過渡層和厚度約為1.42mm的鈦表面層構成的耐蝕復合涂層,該復合涂層結構致密平整,與基體結合良好,其中鎳過渡層與鈦表面層之間形成了冶金結合,結合強度較高;本實施例制備耐蝕復合涂層后鋼板表面的Icorr=1×10-7A/cm2,Ecorr=-0.05V,制備耐蝕復合涂層前鋼板表面的Icorr=1×10-6A...