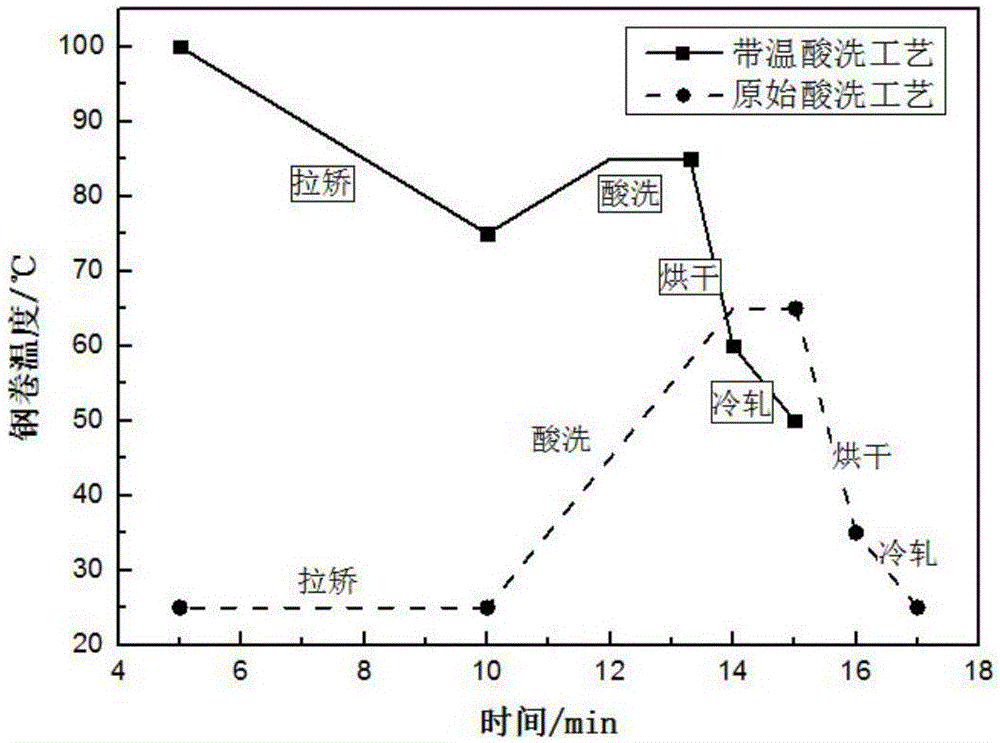
本發(fā)明屬于冷軋帶鋼酸洗
技術領域:
,具體涉及一種高強鋼帶余溫利用酸洗方法。
背景技術:
:冷軋鋼卷的原料是經(jīng)過熱軋卷取后的熱軋鋼卷,熱軋廠生產(chǎn)的熱軋帶鋼卷,由于處于高溫、高應力、水蒸氣等工況,并且伴隨著水冷空冷等冷卻方式,帶鋼表面在相應的條件下生成的氧化鐵皮,能夠很牢固地覆蓋在帶鋼的表面上,如果不將氧化皮去除,會對軋制設備及帶鋼質(zhì)量產(chǎn)生負面影響。硬而脆的氧化皮會破壞昂貴的冷軋輥,壓入鋼卷基體,影響冷軋板的表面質(zhì)量和加工性能;破碎的氧化皮進入乳化液循環(huán)系統(tǒng)當中,會破壞循環(huán)設備。因此,帶鋼在進行冷軋之前,必須去除其表面的氧化鐵皮,以保證冷軋帶鋼的表面精度。除去帶鋼表面氧化皮,也稱除鱗,常用的除鱗方式一般分為三種,分別為機械除鱗、化學除鱗以及機械和化學相結(jié)合的混合除鱗,機械除鱗方法主要有反復彎曲法、拋丸法和噴砂法等。化學除鱗主要有鹽酸酸洗和硫酸酸洗。對于高強鋼來說,一般采用拉矯彎曲和鹽酸酸洗的相結(jié)合的方法。在酸洗方法段前,能夠使帶鋼表面氧化鐵皮層出現(xiàn)裂紋的常用設備是拉矯機。目前拉矯機表現(xiàn)出的顯著特點為對新品種、尤其是高強度帶鋼的拉矯破鱗能力不足,當前無法對拉矯機進行改造的前提下,為增加帶鋼破鱗效果,因此提出鋼卷帶余溫酸洗方法。帶溫拉矯由于溫度的存在,鋼卷組織中原子的內(nèi)能增加,原子活躍,鋼卷很容易變形,根據(jù)拉矯機原理,氧化鐵皮由于不能適應鐵基體的形狀變化而發(fā)生破裂,此時的氧化鐵皮更容易剝落。除此之外,在帶鋼運行張力的作用下,鋼卷的大邊浪被弱化,抻直,減小。當經(jīng)過拉矯機時,鋼卷已經(jīng)平直,在拉矯機之后,由于板型的平直,鋼卷運行平穩(wěn),不會產(chǎn)生跑偏。鋼卷不跑偏就不會產(chǎn)生刮邊和及由于刮邊而產(chǎn)生斷帶事故,從而降低了事故率,提高了設備的有效運行時間。作為市售濃鹽酸是含有32%氯化氫的水溶液,它所含的雜質(zhì)如鐵、氯化砷,其總量小于0.002%。因此,酸洗時不用考慮其有害后果。鹽酸酸洗主要是通過化學作用溶解氧化皮,其酸洗侵蝕能力隨溫度和濃度的提高而提高。酸洗時,酸的溫度為75~85℃,如果帶鋼帶余溫酸洗,由于鋼卷溫度接近酸的溫度,而鹽酸酸洗其酸洗能力就是隨著溫度的增大而增強,因此此時酸洗效果也達到了最佳。另外由于溫度不足以產(chǎn)生新的氧化鐵皮,鋼卷表面氧化并不加重,內(nèi)層沒有形成很厚的FeO層,因此酸洗起來很容易。技術實現(xiàn)要素:為了解決上述問題,本發(fā)明提供一種高強鋼帶余溫利用酸洗方法,所述方法將熱軋生產(chǎn)線出來的500~700℃的高強鋼卷經(jīng)過堆垛冷卻至100℃,然后運輸至冷軋生產(chǎn)線,使得高強鋼卷在酸洗前的溫度達到60~85℃,接著進入酸洗槽進行酸洗,酸洗后烘干,保持烘干后的鋼卷溫度在40~60℃,最后進行冷軋軋制;進一步地,所述方法包括以下步驟:1)獲取生產(chǎn)數(shù)據(jù),所述生產(chǎn)數(shù)據(jù)包括熱軋卷取溫度、酸洗機組各設備最低極限溫度、酸洗方法設備溫度參數(shù)和烘干機蒸汽溫度參數(shù);2)將高強鋼的熱軋卷經(jīng)過堆垛冷卻至100℃;3)對冷卻后的鋼帶進行開卷、拉矯除鱗,使得拉矯后酸洗前的溫度達到60~85℃;4)經(jīng)過拉矯的帶鋼送入酸洗槽進行酸洗,酸洗過后進行漂洗烘干,烘干后使鋼卷溫度保證在40~60℃,最后進行冷軋成型;進一步地,所述高強鋼卷的材質(zhì)為QSTE420TM-P、QSTE460TM-P或QSTE500TM-P;進一步地,所述步驟3)中,拉矯后的鋼帶先經(jīng)過測溫計測溫,再進行酸洗;進一步地,所述步驟4)中烘干機蒸汽溫度設定為60~80℃;進一步地,所述步驟4)中,烘干后的鋼帶先經(jīng)過測溫計測溫,再進行冷軋;本發(fā)明的有益效果如下:1)通過利用卷取后鋼卷的余溫既節(jié)省了資源,又提高了酸洗效果;2)為了不影響冷軋機組的運行,將冷軋前溫度設置為40℃以上,此時進行冷軋軋制,鋼卷有一定的溫度,機組軋制力降低,帶鋼板形波動小,利于后續(xù)軋制生產(chǎn),為了不使烘干機的溫度設定過高,節(jié)省能源,烘干后鋼卷的溫度不超過60℃;3)通過利用帶鋼卷取后的余溫進行拉矯和酸洗,高溫下高強鋼屈服強度的降低使得拉矯過程中基體塑性變形更加容易,除鱗效果顯著;4)高溫氧化鐵皮與酸的反應加速效果更好,從而可以降低酸洗時間,節(jié)約能源,經(jīng)濟可行。附圖說明圖1為不同溫度下的屈服強度、抗拉強度對比;圖2為本發(fā)明一種高強鋼帶余溫利用酸洗方法圖;圖3為不同鋼卷溫度下酸洗時間的對比。具體實施方式為了使本發(fā)明的目的、技術方案及優(yōu)點更加清楚明白,以下結(jié)合附圖及實施例,對本發(fā)明進行進一步詳細描述。應當理解,此處所描述的具體實施例僅僅用于解釋本發(fā)明,并不用于限定本發(fā)明。相反,本發(fā)明涵蓋任何由權(quán)利要求定義的在本發(fā)明的精髓和范圍上做的替代、修改、等效方法以及方案。進一步,為了使公眾對本發(fā)明有更好的了解,在下文對本發(fā)明的細節(jié)描述中,詳盡描述了一些特定的細節(jié)部分。對本領域技術人員來說沒有這些細節(jié)部分的描述也可以完全理解本發(fā)明。下面結(jié)合附圖和具體實施例對本發(fā)明作進一步說明,但不作為對本發(fā)明的限定。下面為本發(fā)明的舉出最佳實施例:如圖1-圖3所示,本發(fā)明提供一種高強鋼帶余溫利用酸洗方法,包括以下步驟:1)獲取生產(chǎn)數(shù)據(jù),所述生產(chǎn)數(shù)據(jù)包括熱軋卷取溫度、酸洗機組各設備最低極限溫度、酸洗方法設備溫度參數(shù)、烘干機蒸汽溫度參數(shù);2)將高強鋼的熱軋卷經(jīng)過堆垛冷卻至100℃;3)對冷卻后的鋼帶進行開卷、拉矯除鱗,使得拉矯后酸洗前的溫度達到60~85℃;4)經(jīng)過拉矯的帶鋼送入酸洗槽進行酸洗,酸洗過后進行漂洗烘干,烘干后使鋼卷溫度保證在40~60℃,最后進行冷軋成型;所述步驟3)中,拉矯后先經(jīng)過測溫計測溫,然后進行酸洗。在拉矯之后的帶鋼溫度達到60~85℃,優(yōu)選地溫度保證了更好的除鱗效果;所述步驟4)中,進行酸洗之后,將烘干機蒸汽溫度設定為60~80℃,然后進行軋制;所述步驟4)中,烘干后先經(jīng)過測溫計測溫,然后進行冷軋。此時進行冷軋軋制,機組軋制力降低,帶鋼卷形波動小,利于后續(xù)軋制生產(chǎn);本發(fā)明提供的方法是通過控制帶鋼進入酸軋機組之前的溫度來達到拉矯和酸洗時一定的鋼卷溫度。在冷軋帶鋼酸洗機組中,一方面,對于一定溫度的鋼卷,隨著變形溫度的升高,高強鋼的屈服強度和抗拉強度總體均呈下降趨勢,如圖1,由于拉矯破鱗時,氧化鐵皮不具有塑性并破壞強度較低,氧化鐵皮會由于不能適應金屬形狀改變而發(fā)生破裂產(chǎn)生剝落。而帶鋼溫度的提高引起屈服強度的降低,金屬變形更加容易,氧化鐵皮更加容易剝離。另一方面。在進行酸洗前,如果鋼卷溫度是常溫的話,鋼卷經(jīng)過酸洗時就會發(fā)生指數(shù)曲線的明顯的溫度上升,根據(jù)湍流擴散理論和對流傳熱理論,酸液溫度就會產(chǎn)生不均勻變化,影響酸洗效果,如果來料溫度與酸的溫度接近,而是趨于平直的直線,如圖2。鋼卷只會吸收少量酸的熱量,酸池內(nèi)酸液的溫度穩(wěn)定,因而紊流酸洗效果良好。由于鋼卷溫度接近酸的溫度,此時酸洗效果也到了最佳。因為理想情況時,帶鋼的溫度與酸液溫度相同時,能夠發(fā)揮最佳的化學反應速率。這樣兩種條件就會導致最后的酸洗終點時間不同,酸洗的質(zhì)量效果也不同。因此通過利用卷取后鋼卷的余溫既節(jié)省了資源,又提高了酸洗效果。本發(fā)明中堆垛溫度處理為100℃,選擇這個溫度原因在于酸洗連軋機組設備能夠承受的高溫;從圖3可以看出,高強鋼60℃時酸洗時間下降較多,因此酸洗前保證在60℃以上較為合理,又為了防止由于溫度過高以產(chǎn)生新的氧化鐵皮形成,且酸液溫度是75~85℃,因此將酸洗前的溫度定為60~85℃;為了不影響冷軋機組的運行,將冷軋前溫度設置為40℃以上,此時進行冷軋軋制,因為鋼卷有一定的溫度,機組軋制力降低,帶鋼板形波動小,利于后續(xù)軋制生產(chǎn)。又為了不使烘干機的溫度設定過高,節(jié)省能源,故烘干后鋼卷的溫度不超過60℃。實施案例:1)從現(xiàn)場獲取QSTE420TM-P高強鋼的生產(chǎn)數(shù)據(jù),所述生產(chǎn)數(shù)據(jù)包括熱軋卷取溫度590℃、酸洗機組各設備極限溫度最低100℃、酸洗方法設備溫度參數(shù),如表1、烘干機蒸汽溫度參數(shù),如表2;2)將高強鋼的熱軋卷經(jīng)過堆垛冷卻至100℃;3)對冷卻后的鋼帶進行開卷、拉矯除鱗,拉矯后這時采用溫度計進行測量,此時鋼卷溫度75℃,符合60~85℃;4)經(jīng)過拉矯的帶鋼送入酸洗槽進行鹽酸酸洗,酸洗過后進行漂洗,將烘干機技術參數(shù)蒸汽溫度設定為80℃,對鋼帶進行烘干后,采用溫度計進行測量此時鋼卷溫度60℃,符合40~60℃,最后進行冷軋成型。由圖2可以看出,由于鋼卷溫度接近酸的溫度,只會吸收少量酸的熱量,酸池內(nèi)酸液的溫度穩(wěn)定,保證了紊流酸洗效果。表1酸洗方法設備溫度參數(shù)項目名稱1#酸槽2#酸槽3#酸槽再生酸溫度/℃75~8575~8575~85---表2烘干機蒸汽溫度參數(shù)型式水平循環(huán)蒸汽加熱式蒸汽溫度最大100℃以上所述的實施例,只是本發(fā)明較優(yōu)選的具體實施方式的一種,本領域的技術人員在本發(fā)明技術方案范圍內(nèi)進行的通常變化和替換都應包含在本發(fā)明的保護范圍內(nèi)。當前第1頁1 2 3