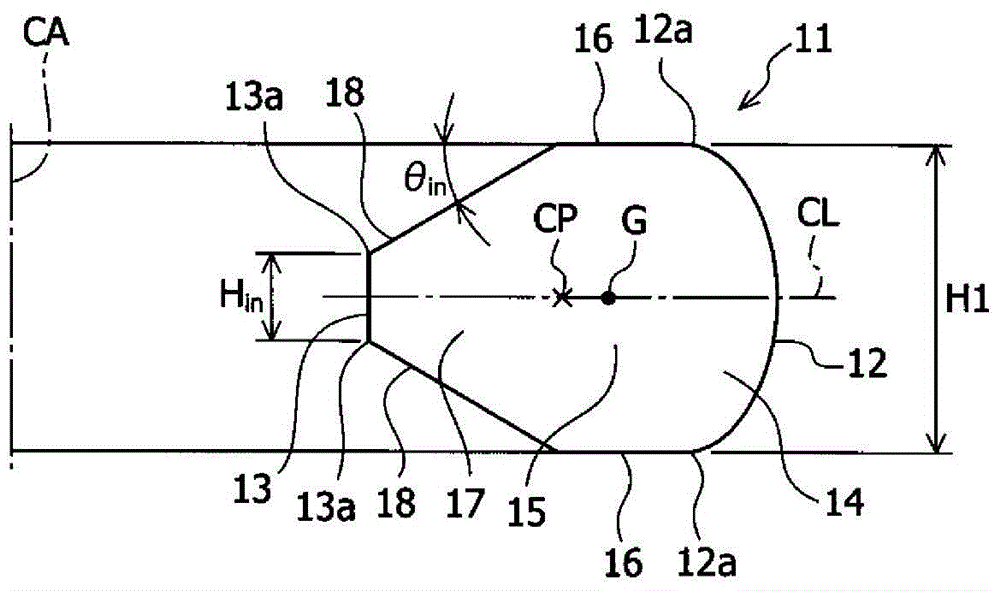
本發(fā)明涉及一種將通過軋制成形的在高溫環(huán)境下使用的環(huán)軋用材料(materialforringrolling)的制造方法。
背景技術(shù):燃?xì)廨啓C(jī)是使用諸如耐熱鋼制部件、超耐熱合金制部件等的大量部件的裝置的例子。在燃?xì)廨啓C(jī)中,多個環(huán)狀的渦輪盤的外周部均配置有翼狀的葉片,從而使流體的軸向流動(即,沿轉(zhuǎn)動軸的軸線方向的流動)轉(zhuǎn)換為轉(zhuǎn)動運(yùn)動,以產(chǎn)生動力。從燃?xì)廨啓C(jī)的前方吸入空氣,然后通過位于燃?xì)廨啓C(jī)下游的多段軸流壓縮部壓縮空氣。此外,在位于燃?xì)廨啓C(jī)的更下游的燃燒器內(nèi)燃燒包括壓縮空氣和燃料的混合物的氣體,以產(chǎn)生高溫高壓的燃燒氣體。該燃燒氣體在沿各渦輪盤的外周部的流路軸向流動時與安裝于各渦輪盤的葉片碰撞,從而將該軸向運(yùn)動轉(zhuǎn)換為轉(zhuǎn)動運(yùn)動,使得各渦輪盤以高速轉(zhuǎn)動。由該轉(zhuǎn)動產(chǎn)生的驅(qū)動力經(jīng)由轉(zhuǎn)動軸使前段的渦輪盤轉(zhuǎn)動,從而進(jìn)一步壓縮空氣,以便提供渦輪盤的連續(xù)轉(zhuǎn)動。近年來,出于節(jié)能的觀點(diǎn),提高燃?xì)廨啓C(jī)的效率是重要的技術(shù)需求。但是,將被處理的燃燒氣體的最高溫度會隨著效率的提高而升高,因此,燃?xì)廨啓C(jī)必須能夠在更高的溫度下運(yùn)行。另一方面,燃?xì)廨啓C(jī)中的渦輪盤和葉片在高速轉(zhuǎn)動的情況下使用,因此,存在如下問題:渦輪盤和葉片在燃?xì)廨啓C(jī)運(yùn)行期間受到歸因于離心力而施加的高的載荷。另外,渦輪盤和葉片暴露于600℃或更高的高溫氣體,并且它們在高溫氣體的流路附近的位置處使用。因此,對于渦輪盤和葉片來說在高溫環(huán)境下具有高的強(qiáng)度是不可或缺的。此外,如果在燃?xì)廨啓C(jī)的運(yùn)行的啟動和停止間歇地發(fā)生的運(yùn)行模式下使用渦輪盤和葉片,則渦輪盤和葉片的部件會受到反復(fù)施加的載荷,結(jié)果,在升高部件的溫度階段和冷卻部件的階段產(chǎn)生的熱應(yīng)力也反復(fù)地作用于渦輪盤和葉片的部件。因此,對燃?xì)廨啓C(jī)來說重要的是,使燃?xì)廨啓C(jī)由具有足夠?qū)股鲜龇磸?fù)施加的載荷和熱應(yīng)力的高強(qiáng)度的部件構(gòu)成。另外,存在為了提高燃?xì)廨啓C(jī)的效率而增大諸如渦輪盤和葉片等的轉(zhuǎn)動體尺寸的傾向,因此,需要由能夠抵抗高離心力的諸如耐熱鋼、超耐熱合金等的高品質(zhì)材料形成的環(huán)件。為了適應(yīng)上述要求,在燃?xì)廨啓C(jī)的內(nèi)部,以奧氏體類耐熱鋼、鐵素體類耐熱鋼和718合金為典型代表的Ni基超耐熱合金主要用作具有抵抗高溫環(huán)境的高強(qiáng)度的耐熱鋼。在上述合金中,已知在高溫下具有特別優(yōu)異的強(qiáng)度的Ni基超耐熱合金(例如,718合金)中,能夠通過使其材料的金屬結(jié)晶結(jié)構(gòu)微細(xì)化來提高合金的疲勞強(qiáng)度。另外,已經(jīng)提出了用于使材料內(nèi)部的粒子尺寸減小的方法的各種技術(shù)。例如,如專利文獻(xiàn)1記載的,已知為了使結(jié)晶結(jié)構(gòu)微細(xì)化,抑制晶粒的粗大化的使粒子析出的方法等是有利的。另外,如專利文獻(xiàn)2記載的,提出如下方法:在該方法中,材料在熱加工期間扭曲以便促進(jìn)粒子微細(xì)化現(xiàn)象,從而能夠獲得微細(xì)粒。關(guān)于將在高溫環(huán)境下使用的環(huán)件的制造方法,因?yàn)镹i基超耐熱合金主要包括稀有金屬,所以Ni基超耐熱合金比普通的鋼材貴。因此,通常使用近凈成形鍛造(near-net-shapeforging),其中將具有與最終形狀接近的近凈成形材料用作待切削的材料,并且進(jìn)一步切削使得切削期間產(chǎn)生的切屑量減小,結(jié)果,能夠降低制造成本。對于近凈成形鍛造,一般使用熱鍛造。作為上述生產(chǎn)工序的例子,使用熱鍛造加工,其中對圓柱狀的坯料施加頂鍛(upsetforging)以將其成形為圓盤狀,對已成形為圓盤狀的圓柱狀的坯料的中心部穿孔,對已穿孔的圓柱狀的坯料施加環(huán)軋以將其成形為具有預(yù)定直徑的環(huán)件,最后,通過使用模具將環(huán)件成形為具有期望的截面形狀?,F(xiàn)有技術(shù)文獻(xiàn)專利文獻(xiàn)專利文獻(xiàn)1:日本特開昭61-238936號公報專利文獻(xiàn)2:日本特開平7-138719號公報專利文獻(xiàn)3:日本特開2011-56548號公報
技術(shù)實(shí)現(xiàn)要素:發(fā)明要解決的問題但是,在使用上述熱鍛造工序的環(huán)軋中,歸因于生產(chǎn)條件的熱而可能會產(chǎn)生異常高的溫度,結(jié)果,這可能會導(dǎo)致產(chǎn)品品質(zhì)的下降。具體地,在使用諸如718合金等的Ni基超耐熱合金的情況下,如果溫度超過1050℃,則抑制結(jié)晶粒子生長的粒子會溶解在固體的基材中。結(jié)果,使結(jié)晶粒子的生長活躍化,可能會產(chǎn)生包括粗粒的結(jié)構(gòu)。因此,對生產(chǎn)環(huán)件極其重要的技術(shù)要求是,在環(huán)軋期間Ni基超耐熱合金的任何位置都不會歸因于發(fā)熱而產(chǎn)生異常高的溫度。此外,在用于將材料成形為最終形狀的鍛造工序中,在將材料形成為具有諸如渦輪盤等的部件的復(fù)雜截面形狀時,難以通過模具鍛造使材料的整個表面均勻且最佳地扭曲。因此,會歸因于鍛造的目標(biāo)形狀而在鍛造期間產(chǎn)生幾乎不扭曲的死區(qū)。在該情況下,會不充分地產(chǎn)生由扭曲的導(dǎo)入所引起的金屬結(jié)晶結(jié)構(gòu)的微細(xì)化現(xiàn)象。結(jié)果,可能會頻繁地殘留導(dǎo)致低循環(huán)下的疲勞特性的劣化的粗粒,而這會導(dǎo)致生產(chǎn)問題。因此,在生產(chǎn)通過模鍛造成形的、環(huán)軋用材料的情況下,在作為預(yù)處理的環(huán)軋階段提前獲得由微細(xì)結(jié)晶構(gòu)成的結(jié)構(gòu)也是重要的技術(shù)要求。此外,如專利文獻(xiàn)3記載的,還提出如下方法:在該方法中,在使用一個環(huán)狀材料時,能夠在使用具有特殊形狀的主輥和芯輥的情況下通過熱軋制在一個工序中獲得均形成為具有近凈成形形狀的環(huán)狀的多個元件。在該提案中,與具有矩形截面的上述環(huán)軋用材料不同的是,使用具有大致圓形截面或大致橢圓形截面的環(huán)軋用材料。但是,專利文獻(xiàn)3的目的在于省略熱鍛造工序,這與傳統(tǒng)技術(shù)非常不同。另外,在專利文獻(xiàn)3中未充分考慮環(huán)軋用材料的形狀,并且如果將具有專利文獻(xiàn)3中記載的形狀的環(huán)軋用材料生產(chǎn)為一個成形品,則可能會在局部發(fā)生異常發(fā)熱。為了解決上述技術(shù)問題,本發(fā)明的目的是提供一種能夠在環(huán)軋用材料的整個表面上導(dǎo)入均勻且最佳的扭曲的環(huán)軋用材料的制造方法,特別地,所述環(huán)軋用材料用作在燃?xì)廨啓C(jī)等的高溫部所使用的轉(zhuǎn)動部件的材料。用于解決問題的方案為了解決上述問題而作出本發(fā)明。具體地,根據(jù)本發(fā)明的一方面,提供一種環(huán)軋用材料的制造方法,其包括如下步驟:(1)將圓板狀的熱鍛造用材料加熱至熱加工溫度;(2)將所述熱鍛造用材料配置在具有截頭圓錐狀的凸部的下模上;(3)通過使用具有截頭圓錐形狀的凸部的上模對所述熱鍛造用材料的中央部加壓來形成薄壁部;以及(4)通過去除所述薄壁部來制得所述環(huán)軋用材料,其中所述環(huán)軋用材料的半截面的形狀被形成為包括高度減小部,所述高度減小部的距中心線的高度朝向所述環(huán)軋用材料的內(nèi)周面逐漸減小,所述中心線在所述半截面的高度方向上將該半截面分成兩半。優(yōu)選地,在所述環(huán)軋用材料中,所述環(huán)軋用材料的半截面的重心被定位成比所述半截面的該半截面的厚度方向上的中心靠近所述環(huán)軋用材料的外周面,所述環(huán)軋用材料被形成為所述半截面的形狀包括所述高度減小部,所述高度減小部的距在所述高度方向上將該半截面分成兩半的中心線的高度朝向所述內(nèi)周面逐漸減小,并且所述半截面的形狀被形成為關(guān)于作為該半截面的對稱軸線的所述中心線大致線對稱,并且所述內(nèi)周面的高度為所述環(huán)軋用材料的最大高度的20%~50%。發(fā)明的效果根據(jù)本發(fā)明,能夠容易地制造能夠獲得如下效果的環(huán)軋用材料。在通過本發(fā)明獲得的環(huán)軋用材料中,作為通過使用具有上述特征的環(huán)軋用材料來執(zhí)行環(huán)軋的結(jié)果,能夠通過高度減小部確保用于環(huán)軋用材料變形的自由空間。因此,減少了執(zhí)行環(huán)軋時的發(fā)熱,能夠抑制歸因于異常發(fā)熱而可能發(fā)生的晶粒的生長,因此,能夠獲得高品質(zhì)的環(huán)件。另外,能夠減少環(huán)軋結(jié)束時可能發(fā)生的內(nèi)徑側(cè)缺少部分,因此,能夠獲得具有極精確形狀的高品質(zhì)的環(huán)件。因此,在生產(chǎn)必須控制環(huán)軋期間的結(jié)晶粒度的、在高溫環(huán)境下使用的環(huán)件時,能夠在適當(dāng)?shù)臏囟确秶鷥?nèi)完成軋制。因此,能夠抑制由粒子的生長所導(dǎo)致的非微細(xì)金相結(jié)構(gòu)的產(chǎn)生,因此,能夠獲得在環(huán)件的整個部分中包括微細(xì)粒子的高品質(zhì)的成形元件。此外,在用于生產(chǎn)環(huán)件的傳統(tǒng)方法中,為了防止執(zhí)行環(huán)軋時的異常發(fā)熱,以如下方式實(shí)施具有多個加熱工序的軋制:執(zhí)行環(huán)軋直到可能產(chǎn)生發(fā)熱的階段前的階段為止,然后中斷環(huán)軋,再進(jìn)一步加熱環(huán)軋用材料,并且執(zhí)行環(huán)軋的后續(xù)工序。但是,在該傳統(tǒng)的方法中,諸如軋制中斷的條件等的工序的設(shè)計因素的數(shù)量增多,用于確定工序的勞動量增大,此外,在多個加熱工序的情況下用于控制環(huán)軋用材料的結(jié)構(gòu)的勞動管理增大。相比之下,通過使用根據(jù)本發(fā)明的方面的環(huán)軋用材料,能夠適當(dāng)?shù)鼐S持環(huán)軋期間產(chǎn)生的加熱溫度,與使用傳統(tǒng)形狀的環(huán)軋相比,減少了加熱工序的數(shù)量,因此,能夠縮短生產(chǎn)時間。附圖說明圖1是示意性地圖示根據(jù)本發(fā)明的制造方法的環(huán)軋用材料的成形過程的截面圖。圖2是示意性地示出通過本發(fā)明的制造方法獲得的環(huán)軋用材料的例子的半截面圖。圖3是示意性地示出通過本發(fā)明的制造方法獲得的環(huán)軋用材料的例子的半截面圖。圖4是示意性地示出通過本發(fā)明的制造方法獲得的環(huán)軋用材料的例子的半截面圖。圖5是示意性地示出通過本發(fā)明的制造方法獲得的環(huán)軋用材料的例子的半截面圖。圖6是示意性地圖示制造環(huán)軋用材料時使用的上模和下模的例子的截面圖。圖7是示意性地示出制造環(huán)軋用材料時使用的上模和下模的例子的截面圖。圖8是示意性地示出制造環(huán)軋用材料時使用的上模和下模的例子的截面圖。圖9是示意性地示出制造環(huán)軋用材料時使用的上模和下模的例子的截面圖。圖10是示意性地圖示環(huán)軋用材料的環(huán)軋工序的立體圖。圖11是示出通過對環(huán)軋的情況實(shí)施的數(shù)值分析獲得的溫度分布的圖,分別使用由根據(jù)本發(fā)明的制造方法獲得的環(huán)軋用材料和比較例的環(huán)軋用材料進(jìn)行上述環(huán)軋。圖12是示出通過對環(huán)軋的情況實(shí)施的數(shù)值分析獲得的扭曲(distortion)分布的圖,分別使用由根據(jù)本發(fā)明的制造方法獲得的環(huán)軋用材料和比較例的環(huán)軋用材料進(jìn)行上述環(huán)軋。圖13是通過放大照相(macrophotograph)示出由根據(jù)本發(fā)明的制造方法獲得的環(huán)軋用材料的上部、內(nèi)徑部、中心部、外徑部和下部的金相結(jié)構(gòu)的圖。具體實(shí)施方式以下,將參照附圖說明本發(fā)明的實(shí)施方式。以下,將參照附圖說明本發(fā)明。(環(huán)軋用材料的成形)將說明用于作為本發(fā)明的實(shí)施方式的例子的、燃?xì)廨啓C(jī)用的均具有Φ1000mm或更大的直徑的盤的環(huán)軋用材料。將具有優(yōu)異的高溫強(qiáng)度的Ni基超耐熱合金用作環(huán)軋用材料。以下,將說明與718合金等同的Ni基超耐熱合金用作該材料的例子,并且注意,作為Ni基超耐熱合金的成分的例子,Ni基超耐熱合金具有如下成分組成:按質(zhì)量百分比計,Ni:50%~55%,Cr:15%~22%,Nb:4.5%~6.5%,Mo:2.5%~3.5%,Ti:0.6%~1.2%,Al:0.2%~0.8%,余量由Fe和不可避免的雜質(zhì)構(gòu)成。如圖1的(a)所示,將盤狀且具有預(yù)定高度的Ni基超耐熱合金1加熱至熱加工溫度。注意,對于熱加工溫度,溫度可以根據(jù)環(huán)軋用材料的材料特性來確定。例如,如果材料為Ni基超耐熱合金,則900℃~950℃的范圍的溫度是適合的。如果使用高強(qiáng)度不銹鋼材料,則850℃~900℃的范圍的溫度是優(yōu)選的。接下來,將由Ni基超耐熱合金制成的材料配置在具有截頭圓錐形狀的凸部的下模。在材料的配置中,將材料放置在下模上是最容易的。另外,如圖1的(b)所示,然后通過使用上模2和下模3(上側(cè)成型模和下側(cè)成型模)如圖1的(b)所示地在Ni基超耐熱合金1的中央對Ni基超耐熱合金1加壓,并且注意,上模2和下模3設(shè)置在熱鍛造裝置、熱壓裝置等內(nèi),上模2和下模3在中央均具有截頭圓錐形狀的凸部,從而形成具有如下空間的薄壁部4(圖1的(b)所示的作為陰影部的部分):該空間用于具有截頭圓錐形狀的凹部。之后,切除設(shè)置在中央的薄壁部4,從而成形環(huán)軋用材料。注意,材料能夠在切除薄壁部4后通過機(jī)加工形成為具有期望的形狀。對于薄壁部的切除方法,能夠使用諸如機(jī)加工和使用噴水切割機(jī)切除等的公知的方法。此外,在本發(fā)明中,能夠?qū)峒庸ず螳@得的熱加工材料用作環(huán)軋用材料,因此,重要的是以高的精度在Ni基超耐熱合金的中央形成凹部。對于出于該目的的方法,可以使用如下方法:在該方法中,Ni基超耐熱合金材料和將放置Ni基超耐熱合金材料的下模分別形成有能夠彼此嵌合的凸形狀和凹形狀,材料和模具之間的對準(zhǔn)(對中)能夠通過凸形狀和凹形狀的彼此嵌合來執(zhí)行。作為另一可選的方法,可以使用如下方法:在該方法中,使用設(shè)置于操縱器的對準(zhǔn)機(jī)構(gòu),以將Ni基超耐熱合金材料放置在下模的中央。另外,將熱鍛造裝置用作適用于本發(fā)明的熱加工機(jī)。注意,熱鍛造包括熱壓,也包括恒溫鍛造。(環(huán)軋用材料的形狀)圖2示出通過上述環(huán)軋用材料的成形工序獲得的環(huán)軋用材料11的半截面的例子。在圖2中,將沿著環(huán)軋用材料11的中心軸線CA的方向定義為“高度方向”,將垂直于中心軸線CA的方向定義為“厚度方向”。注意,在以下將說明的圖3至圖5中,表述“高度方向”和“厚度方向”分別表示與圖2中所指示的相同的方向。圖2是示意性地示出被成形為相對于中心軸線CA軸對稱的形狀(形狀1)的環(huán)軋用材料11的半截面圖。在本發(fā)明的實(shí)施方式中,表述“半截面圖”是指示出環(huán)軋用材料11的在厚度方向上位于中心軸線CA的一側(cè)的部分的圖。也就是說,圖中省略了環(huán)軋用材料11的左側(cè)部分。該環(huán)軋用材料11具有徑向上的外周面12和徑向上的內(nèi)周面13。環(huán)軋用材料11包括具有外周面12的外周部14。外周面12是外周部14的周緣的一部分,該部分形成半截面的輪廓。外周部14被定位成比直線狀地連接外周面12的高度方向上的兩端部12a的邊界線(未圖示出)靠近環(huán)軋用材料11的外周。圖中示出的環(huán)軋用材料11的半截面的形狀包括設(shè)置在厚度方向上的中央部附近的位置處的直線部15。該直線部15包括指向高度方向且直線狀延伸的端面16。直線部15的長度(優(yōu)選為直線部15的端面16的長度)是環(huán)軋用材料11的最大高度H1的約2/3倍。高度減小部17被設(shè)置成與直線部15連接。該高度減小部17被形成為具有錐形形狀,并且高度減小部17的距在高度方向上將半截面分成兩半的中心線CL的高度朝向與芯輥(mandrelroll)接觸的內(nèi)周面13逐漸減小。內(nèi)徑端(內(nèi)周面13)側(cè)的高度Hin等于或大于環(huán)軋用材料11的最大高度H1的1/3倍(33%)并且等于或小于環(huán)軋用材料11的最大高度H1的1/2倍(50%)。另外,高度減小部17的厚度方向上的長度(優(yōu)選為高度減小部17的從環(huán)軋用材料11的高度的最高點(diǎn)朝向內(nèi)周延伸的傾斜面18的沿高度方向投影在中心線CL上的直線的長度)設(shè)定在環(huán)軋用材料11的最大高度H1的0.2倍至1.5倍的范圍內(nèi)。此外,高度減小部17被形成為具有如下形狀:該形狀為從形成在主輥側(cè)的外周面12的高度方向上的兩端部12a朝向內(nèi)周面13的高度方向上的兩端部13a逐漸變窄的形狀,并且該形狀包括具有預(yù)定長度的直線狀部分。半截面的形狀還關(guān)于作為對稱軸線的中心線CL大致線對稱。注意,環(huán)軋用材料11的半截面的重心(或圖的中心)G被定位成比環(huán)軋用材料11的厚度方向上的中心CP靠近主輥、即靠近外周面12側(cè)。在圖中,厚度方向上的中心CP用x標(biāo)記表示,重心G的位置由實(shí)心圓表示。注意,在制造圖2所示的環(huán)軋用材料時,例如,優(yōu)選地使用圖6所示的上模2和下模3。在這方面,優(yōu)選地將中央形成有截頭圓錐形狀的凸部的角度(角度θ)設(shè)定在20°~70°的范圍內(nèi)。這是因?yàn)?,如果角度小?0°,則制造后的環(huán)軋用材料的厚度可能會過度增大,從而可能會增長環(huán)軋的時間,另一方面,如果角度大于70°,則不足以使材料在熱鍛造期間流入Ni基超耐熱合金材料和具有截頭圓錐形狀的凸部之間的部分,從而在一些情況下可能無法獲得期望的形狀。角度θ的下限優(yōu)選為25°。角度θ的上限優(yōu)選為45°,更優(yōu)選為30°。圖3至圖5分別示出環(huán)軋用材料11的第一變形例至第三變形例。首先,在圖3所示的第一變形例的環(huán)軋用材料11(形狀2)的半截面圖中,徑向上的外周面12的上述圖2中的高度方向上的上側(cè)部分12b和下側(cè)部分12c包括逐漸變窄的部分。連接逐漸變窄的上側(cè)部分和逐漸變窄的下側(cè)部分的中間部分12d具有直線形狀。根據(jù)圖3所示的形狀,外周面12的上側(cè)部分12b和下側(cè)部分12c均包括逐漸變窄的部分,連接逐漸變窄上側(cè)部分和逐漸變窄的下側(cè)部分的中間部分12d被形成為具有直線形狀,因此,在環(huán)軋開始時能夠增大主輥和環(huán)軋用材料11之間的接觸面積,從而能夠穩(wěn)定地進(jìn)行環(huán)軋。均用于獲得該形狀的方法的例子包括在獲得上述圖1所示的形狀之后通過機(jī)加工來配置形狀的方法。例如,在該方法中,在形成上述環(huán)軋用材料時使用包括上模2和下模3且被形成為用于獲得圖3所示的形狀的一組模具。如果所使用的方法中采用了機(jī)加工,則能夠提高形狀的精度,另一方面,產(chǎn)品產(chǎn)率可能會變得較差。因此,有利的是,通過使用在熱鍛造(包括熱壓)階段所使用的模具形狀來形成(成形)圖3所示的形狀。如果圖3所示的環(huán)軋用材料11的形狀適用于在熱鍛造階段所使用的模具形狀,則能夠通過調(diào)整模具形狀來將從環(huán)軋用材料11的中心軸線CA至主輥的外周面的距離和從環(huán)軋用材料11的中心軸線CA至外周面12的距離設(shè)定為彼此相同。結(jié)果,能夠更穩(wěn)定地執(zhí)行環(huán)軋。注意,如果通過熱鍛造來成形圖3所示的形狀,則壓載荷比施加于圖2所示的形狀的壓載荷高。因此,在考慮將使用的鍛造裝置的最大載荷、鍛造期間所施加的最大載荷的情況下,能夠確定是應(yīng)用圖3所示的形狀,還是應(yīng)用圖2所示的形狀。在生產(chǎn)圖3所示的環(huán)軋用材料時,優(yōu)選地使用圖7所示的上模2和下模3。在這種情況下,優(yōu)選以與上述情況相同的方式將中央形成有截頭圓錐形狀的凸部的角度(θ)設(shè)定為25°~35°的范圍內(nèi)的角度。接下來,圖4所示的第二變形例的環(huán)軋用材料11(形狀3)具有如下形狀:即從形成在主輥側(cè)的外周面12的高度方向上的兩端部12a朝向內(nèi)周面13的高度方向上的兩端部13a的直線地逐漸變窄的形狀。均用于獲得該形狀的方法的例子包括在獲得上述圖1所示的形狀之后通過機(jī)加工來配置形狀的方法。例如,在該方法中,在形成上述環(huán)軋用材料11時使用包括上模2和下模3且被形成為用于獲得圖4所示的形狀的一組模具。如果所使用的方法采用了機(jī)加工,則能夠提高形狀的精度,另一方面,產(chǎn)品產(chǎn)率可能會變得較差。因此,有利的是,通過使用模具形狀來形成(成形)圖4所示的形狀。注意,在圖4中,外周面12被形成為曲面形狀。但是,如果將曲面形狀的與主輥?zhàn)钕冉佑|的部分加工成平坦的,則在環(huán)軋開始時能夠增大主輥和環(huán)軋用材料11之間的接觸面積,因此,能夠穩(wěn)定地進(jìn)行環(huán)軋??蛇x擇地,理所當(dāng)然地,可以將外周面12側(cè)的整個曲面形狀加工成平坦的。注意,在生產(chǎn)圖4所示的環(huán)軋用材料時,優(yōu)選地使用圖8所示的上模2和下模3。在這種情況下,優(yōu)選以與上述情況相同的方式將中央形成有截頭圓錐形狀的凸部的角度(θ)設(shè)定為15°~25°的范圍內(nèi)的角度。在圖5中的示出第三變形例(形狀4)的半截面圖中示出的環(huán)軋用材料11中,與芯輥接觸的內(nèi)周面13被形成為直線形狀,其它部分均被形成為曲面形狀。為了獲得該形狀,能夠通過例如如下的方法來成形材料:在形成上述環(huán)軋用材料時將上模2和下模3形成為圖4所示的形狀,或者在形成上述環(huán)軋用材料時將形成于上模2和下模3的具有截頭圓錐形狀的凸部的高度增大。另外,在制造圖5所示的環(huán)軋用材料時,例如,優(yōu)選地使用圖9所示的上模2和下模3。在這種情況下,優(yōu)選地以與上述情況相同的方式將中央形成有截頭圓錐形狀的凸部的角度(θ)設(shè)定為35°~45°的范圍內(nèi)的角度。注意,在制造圖5所示的環(huán)軋用材料的情況下,優(yōu)選地根據(jù)具有曲面形狀的高度減小部的形狀來逐漸地改變具有截頭圓錐形狀的凸部的角度。注意,使用圖2至圖5所示的形狀中的圖2和圖3所示的形狀均能夠更穩(wěn)定地執(zhí)行環(huán)軋。接下來,將說明根據(jù)本發(fā)明的實(shí)施方式的環(huán)軋用材料11的形狀的優(yōu)選特征。如上所述,環(huán)軋用材料11具有由高度減小部17形成的朝向內(nèi)周面13側(cè)逐漸變窄的形狀,因此,環(huán)軋用材料11的重心G被定位成比環(huán)軋用材料11的厚度方向上的中心CP靠近主輥側(cè)、即靠近外周面12側(cè)。根據(jù)上述形狀,芯輥和環(huán)軋用材料11之間的接觸面積能夠被控制成較小。通過該特征,能夠在減小環(huán)軋期間所施加的載荷的同時執(zhí)行環(huán)軋。因此,特別地,能夠減少與芯輥接觸的環(huán)軋用材料11的局部發(fā)熱。另外,環(huán)軋用材料11的內(nèi)周面13的高度Hin被控制成環(huán)軋用材料11的最大高度H1的20%以上、50%以下,使得環(huán)軋用材料11的高度減小部17在環(huán)軋期間依次發(fā)生變形,并且能夠利用相對低的壓力執(zhí)行環(huán)軋。如果內(nèi)周面13的高度Hin小于環(huán)軋用材料11的最大高度H1的20%,則芯輥和內(nèi)周面13之間的接觸面積減小,因此,環(huán)軋用材料11在環(huán)軋期間容易向上側(cè)或下側(cè)傾倒,從而環(huán)軋可能會變得不穩(wěn)定。另一方面,如果內(nèi)周面13的高度Hin超過環(huán)軋用材料11的最大高度H1的50%,則可能會產(chǎn)生異常高的熱。具體地,如果適當(dāng)?shù)乜刂票景l(fā)明的實(shí)施方式中規(guī)定的諸如截面的形狀、重心G的位置以及內(nèi)周面13的高度Hin和環(huán)軋用材料11的最大高度H1之間的關(guān)系等的條件,則能夠在增強(qiáng)熱加工性的同時,能夠抑制環(huán)軋用材料11的局部發(fā)熱。此外,為了更確實(shí)地獲得上述有益效果,內(nèi)周面13的高度Hin的下限優(yōu)選地為環(huán)軋用材料11的最大高度H1的25%,更優(yōu)選為環(huán)軋用材料11的最大高度H1的33%。另一方面,內(nèi)周面13的高度Hin的上限優(yōu)選為環(huán)軋用材料11的最大高度H1的45%,更優(yōu)選為環(huán)軋用材料11的最大高度H1的40%。表述“內(nèi)周面13的高度”是指內(nèi)周面13的高度方向上的兩端部13a之間的間隔,其相對于高度減小部17的傾斜面18的曲率具有大的曲率差。例如,在圖2至圖5所示的半截面中,“內(nèi)周面13的高度”是指與芯輥接觸的直線狀部分的長度。注意,即使內(nèi)周面13上存在輕微的曲面或輕微的凹凸形狀而使得內(nèi)周面13的高度Hin的測量變得不精確,也能夠在位于從最先與芯輥接觸的位置向外周側(cè)去等于或小于20mm的范圍內(nèi)的、相對于高度減小部17的曲率具有大的曲率差的位置處執(zhí)行測量。如圖2至圖5所示,環(huán)軋用材料11關(guān)于作為對稱軸線的中心線CL大致線對稱地形成。通過使用被形成為關(guān)于作為對稱軸線的中心線CL大致線對稱的形狀,能夠穩(wěn)定地執(zhí)行環(huán)軋。關(guān)于“大致線對稱”,例如,如果使用未約束外周面12的模具來通過熱鍛造以上述方式執(zhí)行環(huán)軋用材料的成形,則在一些情況下可能無法獲得完全的線對稱。因此,在本發(fā)明中的表述“大致線對稱”表示如下形狀:該形狀可以容許在形成上述環(huán)軋用材料時發(fā)生形狀的誤差、偏差等。此外,在本發(fā)明的實(shí)施方式中,如圖2至圖5所示地設(shè)置有高度減小部17。高度減小部17為在通過使用環(huán)軋機(jī)成形期間環(huán)軋用材料11變形用的自由空間,特別地,通過該特征,能夠防止位于芯輥側(cè)的環(huán)軋用材料11的過度發(fā)熱。關(guān)于高度減小部17,如上所述,在本發(fā)明的實(shí)施方式中,能夠使用中央均具有截頭圓錐形狀的凸部的上模2和下模3對中央加壓來成形高度減小部17。在這種情況下,高度減小部17的厚度方向上的長度隨著截頭圓錐狀的凸部的角度的減小而增大。但是,如果過長地設(shè)定高度減小部17的厚度方向上的長度,則在環(huán)軋期間高度減小部17的加工時間可能會變得較長。另一方面,高度減小部17的厚度方向上的長度隨著截頭圓錐狀的凸部的角度的增大而減小。但是,如果長度過小,則將在加壓后切除的缽狀部分(mortar-shapedportion)會增大,而這會降低產(chǎn)品產(chǎn)率。另外,如果增大凸部的加壓表面的面積,則必須用較高的壓力對模具加壓,結(jié)果,必須使用能夠施加高的載荷的特別的鍛造裝置。在這種情況下,在環(huán)軋期間環(huán)軋用材料11的溫度會局部變高。因此,在本發(fā)明的實(shí)施方式中,高度減小部17的厚度方向上的長度(優(yōu)選為通過將高度減小部17的傾斜面18沿高度方向投影在中心線CL上獲得的直線的長度)是環(huán)軋用材料11的最大高度H1的0.2倍至1.5倍。在這樣的關(guān)系下,高度減小部17的厚度方向上的長度的下限優(yōu)選為最大高度H1的0.5倍,更優(yōu)選為最大高度H1的0.6倍。另一方面,高度減小部17的厚度方向上的長度的上限優(yōu)選為最大高度H1的1.1倍,更優(yōu)選為最大高度H1的1.0倍。在根據(jù)本發(fā)明的實(shí)施方式的環(huán)軋用材料11中,與主輥接觸的外周部14優(yōu)選被形成為具有朝向外周逐漸變窄的形狀。圖2至圖5所示的環(huán)軋用材料11均被形成為逐漸變窄的形狀。如果應(yīng)用上述形狀,則使用例如在成形環(huán)軋用材料時通過熱鍛造來約束外周面12的模具,該模具能夠用于環(huán)軋,而這在經(jīng)濟(jì)上是有利的。此外,如果在環(huán)軋期間與主輥接觸的外周面12具有上述平坦部,則能夠穩(wěn)定地執(zhí)行環(huán)軋。因此,優(yōu)選地將環(huán)軋用材料11中的與主輥接觸的外周面14的一部分設(shè)置成平坦部。在該特征中,優(yōu)選地設(shè)置具有最大高度H1的大約1/6倍以上、1/3倍以下的長度的平坦部(即,圖中外周面12的直線狀部分)。另外,在本發(fā)明的實(shí)施方式中,可以將包括高度方向上的大致直線狀延伸的兩端面16的直線部15設(shè)置在外周部14和高度減小部17之間。關(guān)于直線部15,如果將軸向輥用于環(huán)軋,并且設(shè)置有用于供軸向輥加壓的平坦部,則能夠穩(wěn)定地執(zhí)行環(huán)軋,能夠更容易獲得期望的形狀。為此,優(yōu)選直線部15的厚度方向上的長度(更優(yōu)選直線部15的端面16的長度)為大于環(huán)軋用材料11的最大高度H1的0倍且等于或小于環(huán)軋用材料11的最大高度H1的2/3倍。盡管不特別限制本發(fā)明,但是環(huán)軋用材料11的厚度(材料厚度)可以是環(huán)軋用材料11的最大高度H1的0.5倍或更大。在考慮如下風(fēng)險的情況下來確定該限制:因?yàn)楦鶕?jù)本發(fā)明的實(shí)施方式的環(huán)軋用材料11是通過環(huán)軋后所進(jìn)一步執(zhí)行的熱鍛造(包括在高溫和恒溫下的鍛造和加壓的熱鍛造)加工成最終產(chǎn)品的形狀的,所以如果材料過薄,則在后續(xù)的熱鍛造時可能會發(fā)生屈曲。環(huán)軋用材料11的被表示為“θin”的角度優(yōu)選為等于或大于20°。如果角度θin小于20°,則高度減小部17會變得較長,而這可能會導(dǎo)致環(huán)軋時間的增長。在這種情況下,增加了在諸如熱鍛造和熱壓等的熱加工后將切除的薄壁部4的重量,結(jié)果,這也會降低產(chǎn)品產(chǎn)率。另一方面,如果角度θin超過70°,則徑向上的內(nèi)周面13在環(huán)軋期間容易產(chǎn)生局部發(fā)熱。在這種情況下,由于Ni基超耐熱合金1在熱加工時將不會在上模2和下模3內(nèi)完全延伸,所以難以獲得期望的形狀。能夠更確實(shí)地防止這些問題的角度θin的下限優(yōu)選為25°。角度θin的上限優(yōu)選為45°,更優(yōu)選為30°。(形成耐熱合金環(huán)件的環(huán)軋工序)通過使用環(huán)軋機(jī)對上述環(huán)軋用材料11進(jìn)行環(huán)軋。能夠?qū)⒕哂袌D10所示的特征的環(huán)軋機(jī)用作環(huán)軋時使用的環(huán)軋機(jī)。注意,環(huán)軋機(jī)還可以包括導(dǎo)輥(對中輥)和定尺寸輥(sizingroll)。在圖10所示的環(huán)軋機(jī)中,能夠以預(yù)定的轉(zhuǎn)速轉(zhuǎn)動的主輥21和能夠繞其軸線從動轉(zhuǎn)動的芯輥22被配置成彼此相對、分別位于環(huán)軋用材料11的徑向上的外周面12和徑向上的內(nèi)周面13。此外,環(huán)軋機(jī)還包括兩個軸向輥23A、23B,該兩個軸向輥23A、23B被配置成彼此相對、分別位于環(huán)軋用材料11的高度方向上的上表面和下表面。如果將能夠從動轉(zhuǎn)動的導(dǎo)輥配置在主輥21的兩側(cè),則在環(huán)軋用材料11的外周部14被支撐的同時進(jìn)行軋制,以減小和抑制在軋制期間可能發(fā)生的環(huán)軋用材料11的從中心的偏離,從而能夠更穩(wěn)定地執(zhí)行軋制。主輥21被形成為圓柱形狀。該主輥21在與環(huán)軋用材料11的外周面12接觸的狀態(tài)下從動轉(zhuǎn)動,使得環(huán)軋用材料11在環(huán)軋期間轉(zhuǎn)動。對于芯輥22,使用圓柱狀的輥。該芯輥22被構(gòu)造成繞其軸線自由轉(zhuǎn)動,并且與主輥21的轉(zhuǎn)動軸線大致平行地配置。在芯輥22的外周面與環(huán)軋用材料11的內(nèi)周面13接觸的狀態(tài)下執(zhí)行軋制。在該軋制期間,主輥21和芯輥22之間的輥距逐漸減小,結(jié)果,沿厚度方向?qū)Νh(huán)軋用材料11的徑向上的內(nèi)周面13和徑向上的外周面12之間的部分加壓。上軸向輥23A和下軸向輥23B被形成為具有20°~45°的頂角的圓錐形狀或截頭圓錐形狀。此外,為了調(diào)整環(huán)軋用材料11的高度方向上的尺寸,將上軸向輥23A和下軸向輥23B配置成兩者的頂端均可以指向環(huán)軋用材料11的大致中心。注意,根據(jù)環(huán)軋用材料11的轉(zhuǎn)速來轉(zhuǎn)動地驅(qū)動上軸向輥23A和下軸向輥23B,并且可選擇地,上軸向輥23A和下軸向輥23B可以從動轉(zhuǎn)動。關(guān)于軋制工序,芯輥22插通被加熱至預(yù)定溫度的環(huán)軋用材料11的內(nèi)徑孔。然后,芯輥22朝向徑向外側(cè)逐漸移動,使得主輥21和芯輥22之間的間隔可以逐漸減小。之后,當(dāng)它們之間的距離與環(huán)軋用材料11的初始狀態(tài)下的厚度相同時,環(huán)軋用材料11歸因于主輥21的表面和環(huán)軋用材料11的外周面12之間的摩擦而轉(zhuǎn)動。在該工序中,芯輥22以跟隨環(huán)軋用材料11的轉(zhuǎn)動而轉(zhuǎn)動的方式從動轉(zhuǎn)動。隨后,通過朝向徑向外側(cè)(朝向外周)逐漸移動芯輥22來使主輥21和芯輥22之間的間隔逐漸減小。因此,沿厚度方向?qū)Νh(huán)軋用材料11加壓,從而使環(huán)軋用材料11沿著環(huán)軋用材料的周向以連續(xù)的方式塑性變形。用于該工序的環(huán)軋用材料11具有本發(fā)明規(guī)定的上述形狀。(有益效果)以下將說明通過使用上述環(huán)軋機(jī)對具有上述截面形狀的環(huán)軋用材料11進(jìn)行軋制所能夠獲得的有益效果。以下,為了確認(rèn)位于內(nèi)周側(cè)的被形成為具有逐漸變窄形狀的部分變形時所起到的作用,將參照使用計算機(jī)執(zhí)行的數(shù)值模擬的分析例子來說明有益效果。但是,在分析例子中,為了簡化數(shù)值計算,建模對象中不包括不直接影響成形的導(dǎo)輥。對于使具有圖2所示的半截面的形狀的環(huán)軋用材料11的外徑增大1.2倍的軋制條件,通過使用三維剛塑性有限元分析方法(three-dimensionalrigid-plasticfiniteelementanalysismethod)來實(shí)施環(huán)軋的數(shù)值分析。注意,環(huán)軋用材料11的外徑是φ600mm,環(huán)軋用材料11的最大厚度是100mm,環(huán)軋用材料11的內(nèi)徑側(cè)的厚度是40mm。在考慮將環(huán)軋用材料11的周向上具有截面形狀的對稱面CL(從半截面觀察時等同于中心線CL的對稱面CL)作為對稱基準(zhǔn)的對稱性的情況下,約束位于對稱面CL的節(jié)點(diǎn)的面外側(cè)的方向上的移位,并且將位于對稱面CL上側(cè)的部分用作分析對象。對于芯輥22和軸向輥23A,將條件設(shè)定為它們分別能夠繞各自的軸線轉(zhuǎn)動。主輥21的直徑為φ800mm,主輥21能夠以20轉(zhuǎn)每分鐘(20RPM)的恒定速度轉(zhuǎn)動。注意,將初始加熱溫度設(shè)定為980℃。對于將等同于718合金的合金用作材料時所獲得的熱流動應(yīng)力的數(shù)據(jù),使用通過在700℃~1100℃的范圍的試驗(yàn)溫度下執(zhí)行壓縮試驗(yàn)所獲得的數(shù)據(jù)。圖11的(a)至圖11的(c)均示出通過數(shù)值分析獲得的軋制過程中的截面形狀的變化圖案和其溫度分布。為了比較,圖11的(d)至圖11的(f)均示出使用具有傳統(tǒng)的矩形截面的環(huán)軋用材料、在與上述相同的條件下執(zhí)行軋制過程中的截面形狀的變化圖案和其溫度分布。在圖11中,由“CL”指示的點(diǎn)劃線表示中心線。所有圖11的(a)至圖11的(f)示出被中心線CL分開的半截面的上半部分的模擬結(jié)果。注意,圖11的(a)至圖11的(c)以及圖11的(d)至圖11的(f)包括:主輥21和芯輥22處于它們的初始位置并且分別與環(huán)軋用材料11的外周面12和內(nèi)周面13接觸的時間點(diǎn)的狀態(tài)的圖(圖7的(a)和圖7的(d))、環(huán)軋用材料11的外徑增加3%的時間點(diǎn)的狀態(tài)的圖(圖11的(b)和圖11的(e))以及環(huán)軋用材料11的外徑進(jìn)一步增加20%的時間點(diǎn)的狀態(tài)的圖(圖11的(c)和圖11的(f))。當(dāng)關(guān)注在沿著主輥21和芯輥22的轉(zhuǎn)動軸線配置且包括轉(zhuǎn)動軸線的假想平面中通過主輥21和芯輥22的環(huán)軋用材料11時,在沿厚度方向?qū)Νh(huán)軋用材料11加壓的條件下,環(huán)軋用材料11的厚度方向上的尺寸隨著時間的推移而減小。但是,環(huán)軋用材料11自身的體積在塑性變形期間是恒定的,結(jié)果,在周向上發(fā)生了的材料流動。此外,在芯輥22和主輥21之間的區(qū)域中,芯輥22和主輥21在軸向上不受約束,因此,還提供了高度方向上的流動成分。在軋制根據(jù)本發(fā)明的實(shí)施方式的環(huán)軋用材料11時,環(huán)軋用材料11包括高度減小部17(具有逐漸變窄的形狀),因此,對于內(nèi)側(cè)的流動,在初期,形成自由空間的逐漸變窄的形狀的頂端區(qū)域選擇性地變形。在該工序中,上軸向輥23A和下軸向輥23B位于最大厚度部分,因此,位于內(nèi)周面13側(cè)的區(qū)域中的高度方向上的變形自由地進(jìn)行。當(dāng)關(guān)注圖11的(a)至圖11的(c)所示的溫度分布時,在將溫度維持為等于或小于1000℃的狀態(tài)下執(zhí)行軋制。另一方面,圖11的(d)至圖11的(f)示出在軋制具有傳統(tǒng)方式中通常使用的矩形截面的材料時獲得的溫度分布的結(jié)果。在傳統(tǒng)形狀的情況下,在外徑增大20%的時間點(diǎn),在內(nèi)徑角部中,溫度歸因于加工發(fā)熱而上升,并且溫度上升至大約1130℃。相比之下,在軋制根據(jù)本發(fā)明的實(shí)施方式的環(huán)軋用材料11的情況下,從軋制開始到軋制結(jié)束變化的溫度最大為1000℃,從而能夠觀察到軋制是在適當(dāng)?shù)臏囟确秶鷥?nèi)執(zhí)行的。此外,圖12的(a)和圖12的(b)分別示出通過數(shù)值分析獲得的環(huán)軋工序結(jié)束時的扭曲分布圖,其中對根據(jù)本發(fā)明的實(shí)施方式的環(huán)軋用材料11和具有傳統(tǒng)的矩形截面的環(huán)軋用材料進(jìn)行上述數(shù)值分析。注意,圖12的(a)和圖12的(b)還均示出被中心線CL分開的半截面的上半部分的模擬結(jié)果。如將從這些結(jié)果理解的,在傳統(tǒng)技術(shù)的情況下,由于在內(nèi)徑角部已集中地產(chǎn)生了變形,所以會歸因于該變形而發(fā)熱。此外,由于材料歸因于發(fā)熱而已發(fā)生了軟化,所以局部的扭曲值會等于或大于4。另一方面,在本發(fā)明的實(shí)施方式的情況下,當(dāng)關(guān)注內(nèi)徑角部的扭曲時,扭曲值大約為2.5,因此,局部變形減小為小于傳統(tǒng)技術(shù)中的局部變形?;谶@些結(jié)果,能夠理解,截面內(nèi)的變形更均勻。當(dāng)Ni基超耐熱合金在高溫狀態(tài)下加工扭曲時,粗粒在工序初期會再結(jié)晶為微細(xì)粒,結(jié)果,獲得了微細(xì)結(jié)構(gòu)。注意,一般將扭曲定義為“((變形后的長度)-(變形前的長度))/(變形前的長度)”。因此,能夠解決如下傳統(tǒng)問題:在傳統(tǒng)問題中,諸如具有過高溫度的內(nèi)徑角部等的部分會發(fā)生粒子粗大化,使得扭曲的分布?xì)w因于局部變形而變得不均勻,結(jié)果,會使結(jié)構(gòu)變得不均勻。因此,即使將環(huán)件形成為與傳統(tǒng)技術(shù)相同的目標(biāo)形狀,根據(jù)本發(fā)明的實(shí)施方式的形狀也適用于環(huán)軋用材料,從而能夠抑制軋制期間的發(fā)熱,在Ni基超耐熱合金的晶粒的生長被抑制的狀態(tài)下促進(jìn)了微細(xì)化的粒子的再結(jié)晶,因此,能夠通過軋制成形具有優(yōu)異品質(zhì)的環(huán)件。如上所述,根據(jù)本發(fā)明的實(shí)施方式的環(huán)軋用材料11的形狀包括形成在高度減小部17(具有逐漸變窄的形狀)和環(huán)軋用材料11的最大高度部分之間的空間,并且促進(jìn)塑性變形,使得材料在加壓過程中逐漸流入?yún)^(qū)域內(nèi)。因此,防止了局部集中變形,從而能夠使整個環(huán)件的變形均勻。結(jié)果,抑制了異常高的發(fā)熱,能夠?qū)⑹┘佑谳S向輥的熱載荷減小至低的水平,因此,能夠增強(qiáng)軸向輥的壽命。相比之下,在使用軋制用材料的傳統(tǒng)形狀的情況下,如果在完成軋制之前角部填充有材料,則材料的靠近角部的部分被沿厚度方向壓縮在芯輥22和主輥21之間,因此,不能在適當(dāng)?shù)姆较蛏媳卉堉频牟牧涎馗叨确较蛄鲃印A硪环矫?,角部附近的部分在高度方向上在上軸向輥23A和下軸向輥23B之間被壓縮,該壓縮方向與材料的上述流動方向相反,因此,不能在適當(dāng)?shù)姆较蛏媳卉堉频牟牧涎睾穸确较蛄鲃?。因此,每次轉(zhuǎn)動均會反復(fù)地發(fā)生變形,結(jié)果,歸因于變形而發(fā)熱。特別地,由于Ni基超耐熱合金的熱傳導(dǎo)率低,所以一旦發(fā)熱,需要花時間來使溫度降低,結(jié)果,溫度會歸因于環(huán)軋期間發(fā)生的反復(fù)的局部變形而上升。因此,材料溫度達(dá)到使晶粒粗大化的溫度區(qū)域內(nèi)的1050℃,因此,材料可能會包括在結(jié)束軋制后具有低強(qiáng)度特征的部分。用于防止該問題的手段的例子包括諸如水冷卻、設(shè)置額外的成形部、減小軋制速度等的手段。但是,在水冷卻的情況下,根據(jù)軋制工序的進(jìn)程來管理溫度是非常困難的。如果設(shè)置額外的成形部,則需要切除該額外的成形部的邊緣,從而可能會降低材料的產(chǎn)品產(chǎn)率,并且可能會增大所要求的軋制能力。如果降低軋制速度以抑制角部的發(fā)熱,則完成軋制花費(fèi)的時間可能會變得較長,因此,這導(dǎo)致了其它部分的溫度降低。對于根據(jù)本發(fā)明的實(shí)施方式的環(huán)軋用材料11,通過使用與傳統(tǒng)技術(shù)等同的準(zhǔn)備工序來形成材料。此外,對于環(huán)軋用材料11,通過熱頂鍛(upsethotforging)來鍛造圓柱狀坯料,并且通過使用沖模來使圓柱狀坯料的中心穿孔,然后,必要時,通過機(jī)加工來對材料進(jìn)行切削,以便具有根據(jù)本發(fā)明的實(shí)施方式的形狀。因此,能夠容易地獲得上述環(huán)軋用材料的形狀。注意,因?yàn)槟軌蚍乐古c軸向輥的局部接觸,并且能夠抑制軸向輥的磨損,所以如果在連接部的各側(cè)邊設(shè)置倒角部(filletportion)(彎曲部)則是更適當(dāng)?shù)?。?shí)施例對于用于直徑Φ1000mm或更大的燃?xì)廨啓C(jī)用盤的等同于718合金的合金,圖1所示的環(huán)軋用材料的形成方法用于形成圖2所示的環(huán)軋用材料11。將等同于718合金的合金的熱鍛造溫度設(shè)定為920℃。對于實(shí)施例中使用的模具的形狀,使用圖6所示的上模和下模。具有截頭圓錐形狀的凸部的角度(θ)為32°。將環(huán)軋用材料11的尺寸設(shè)定為表1所示的值。具體地,將環(huán)軋用材料11的與主輥接觸的外周部14成形為具有朝向外周逐漸變窄的曲面形狀。環(huán)軋用材料11的半截面的形狀包括高度減小部17,高度減小部17被形成為距在高度方向上將半截面分成兩半的中心線CL的高度朝向與芯輥接觸的內(nèi)周面13減小。此外,將環(huán)軋用材料11的形狀成形為關(guān)于作為對稱軸線的中心線CL大致線對稱。環(huán)軋用材料11的半截面的重心G位于比環(huán)軋用材料11的厚度方向上的中心CP靠近主輥側(cè)的位置處、即位于靠近外周面12側(cè)的位置處。[表1]對于環(huán)軋用材料11,通過使用圖10所示的環(huán)軋機(jī)來執(zhí)行環(huán)軋。該試驗(yàn)中使用的環(huán)軋機(jī)設(shè)置有導(dǎo)輥和測量輥。在開始環(huán)軋之前,將環(huán)軋用材料11加熱至990℃。在環(huán)軋期間,與上述模擬結(jié)果相同,位于內(nèi)周面13側(cè)的區(qū)域中的高度方向上的變形自由地進(jìn)行,并且未觀察到過度異常的高發(fā)熱。因此,發(fā)熱次數(shù)少至兩次,從而可以縮短生產(chǎn)時間。另外,由于包括大致直線狀延伸的端面16的位于高度方向上的直線部(平坦部)15設(shè)置在外周部14和高度減小部17之間,所以可以在用軸向輥對材料加壓時穩(wěn)定地執(zhí)行環(huán)軋。通過以這種方式執(zhí)行環(huán)軋,可以獲得具有1141mm的外徑、933mm的內(nèi)徑、104mm的厚度和189mm的高度、包括矩形形狀的環(huán)軋用材料11。目視觀察環(huán)軋用材料11的外觀,然后,檢查諸如裂紋、碎片等的缺陷,并且環(huán)軋用材料11中未發(fā)現(xiàn)這些缺陷,從而形成了大致正圓形形狀的環(huán)軋用材料11。從環(huán)軋用材料11中取樣用于觀察金相結(jié)構(gòu)的試驗(yàn)片。取樣部分是環(huán)軋用材料(環(huán)軋機(jī)軋制材料(ringmillrollingmaterial))11的上部、內(nèi)徑部、中心部、外徑部和下部。通過使用光學(xué)顯微鏡來觀察環(huán)軋用材料11的金相結(jié)構(gòu),此外,測量結(jié)晶粒度編號。根據(jù)ASTM-E112規(guī)定的測量方法來實(shí)施結(jié)晶粒度的測量。表2示出結(jié)晶粒度的測量結(jié)果,圖13示出金相結(jié)構(gòu)的照片。[表2]觀察位置平均結(jié)晶粒度編號上部11內(nèi)徑部11中心部10.5外徑部11下部10根據(jù)截面的金相結(jié)構(gòu)的觀察結(jié)果和平均結(jié)晶粒度的測量結(jié)果,能夠理解,通過使用根據(jù)本發(fā)明的實(shí)施方式的環(huán)軋用材料11所生產(chǎn)的環(huán)軋用材料中的晶粒是均勻且微細(xì)的。因此,確認(rèn),對環(huán)軋用材料11的整個表面施加均勻且最佳的扭曲,并且該環(huán)軋用材料11適用于用作燃?xì)廨啓C(jī)的高溫部所使用的轉(zhuǎn)動部件的材料。附圖標(biāo)記說明1環(huán)軋用Ni基超耐熱合金2上模(上側(cè)成型模)3下模(下側(cè)成型模)4薄壁部11環(huán)軋用材料12外周面12a端部12b上側(cè)部分12c下側(cè)部分12d中間部分13內(nèi)周面13a端部14外周部15直線部16端面17高度減小部18傾斜面21主輥22芯輥23A上軸向輥23B下軸向輥CA中心軸線CP中心CL中心線Hin內(nèi)周面的高度H1環(huán)軋用材料的最大高度θin角度