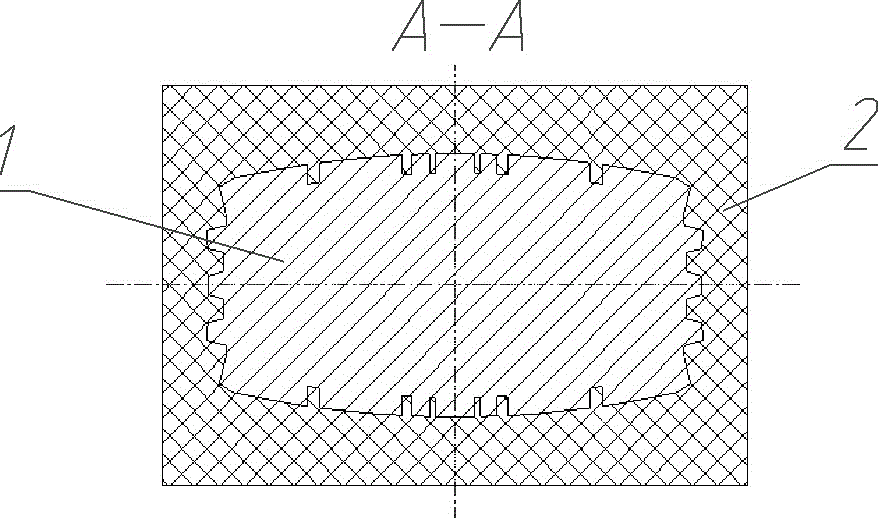
本發(fā)明涉及超硬材料復合片及其基體。
背景技術:超硬材料具有很高的強度和良好的耐磨性能,例如聚晶金剛石、立方氮化硼或者陶瓷等,常被應用于鉆具、刀片等場合。整體聚晶金剛石刀片、整體立方氮化硼刀片和陶瓷刀片工作區(qū)域只有刃口部位,刀片除刃口外其他部位在切削過程中僅起到支撐的作用,但是聚晶金剛石、立方氮化硼材料和陶瓷材料做支撐材料存在一定的缺陷,其成本高,質脆,不易開槽或開孔,所以整體聚晶金剛石、立方氮化硼刀片和陶瓷刀片一般不設置刀片定位孔。并且,由于這些整體刀片的刃口磨損后刀具就會失去價值,因此會浪費很多金剛石或者立方氮化硼等原料,不符合綠色環(huán)保節(jié)能的發(fā)展趨勢。超硬材料復合片一般由聚晶金剛石、立方氮化硼或者陶瓷材料與硬質合金在高溫高壓條件下燒結而成,聚晶金剛石、立方氮化硼或者陶瓷材料作為工作層,硬質合金作為支撐體,二者復合而成的復合片能夠兼具聚晶金剛石、立方氮化硼或者陶瓷材料高硬度、高耐磨特性和硬質合金的高強度、抗沖擊韌性等特點,能夠作為復合刀片廣泛用于硬度材料及難加工材料的切削加工,如淬硬鋼、高合金耐磨鑄鐵、高溫合金、高速鋼、表面噴焊材料、燒結金屬材料等難加工材料的切削加工。但是,聚晶金剛石、立方氮化硼或者陶瓷材料與硬質合金復合刀片在燒結過程中,由于兩種材料之間膨脹系數不同,潤濕度不高,且早期的兩種材料間的結合面是平面結構,因此結合效果不理想,結合面處容易產生開裂。申請?zhí)枮?01120224121.6、授權公告號為CN202181849U的中國專利公開了一種金剛石硬質合金復合片,包括硬質合金制成的基體和通過高壓高溫燒結在硬質合金基體上表面的聚晶金剛石層,所述的硬質合金基體上表面設有均勻分布且前后錯開的凸起單元,使各凸起單元周圍的凹槽間隔分布且相互連通,該凸起單元可以為四棱錐臺、圓錐臺、長方體、圓柱體或正六棱錐臺,從而在一定程度上提升了硬質合金基體和聚晶金剛石層的結合強度,減小了應力,提高抗沖擊性。但是,由于兩種材料之間膨脹系數不同,潤濕度不高的問題仍然存在,上述復合片的結合強度和抗沖擊性能仍十分有限,仍然會出現結合面開裂的問題。
技術實現要素:本發(fā)明的目的是提供一種能夠有效地預防基體與超硬材料之間的結合面開裂的超硬材料復合片,同時,本發(fā)明還提供了一種超硬材料復合片的基體。本發(fā)明中超硬材料復合片采用的技術方案是:超硬材料復合片,包括基體和超硬材料層,所述基體的各個側面均具有用于與所述超硬材料層結合固定的結合面,所述結合面為設有凸起結構和/或凹陷結構的結合面,所述超硬材料層通過所述基體的各個側面上的結合面結合固定在基體上,所述超硬材料層結合在各所述結合面上的部分相互連接。所述結合面為朝外凸起的外凸結合面,所述基體的各個側面上的外凸結合面之間平滑過渡連接。所述外凸結合面的凸起高度小于相應基體對應側面的半徑或小于相應基體對應側面的邊長的一半。所述基體的整個外表面均為結合面,所述基體完全被包覆在所述超硬材料層中。所述基體上設有貫通相應側面的刀片定位孔,所述基體上除刀片定位孔的孔口外的表面均為結合面。本發(fā)明中超硬材料復合片的基體采用的技術方案是:超硬材料復合片的基體,包括用于與超硬材料層結合固定的結合面,所述基體的各個側面均具有所述結合面,所述結合面為設有凸起結構和/或凹陷結構的結合面,所述凸起結構或凹陷結構的棱邊設有倒角。所述結合面為朝外凸起的外凸結合面,所述基體的各個側面上的外凸結合面之間平滑過渡連接。所述外凸結合面的凸起高度小于相應基體對應側面的半徑或小于相應基體對應側面的邊長的一半。所述基體的整個外表面均為結合面,所述基體完全被包覆在所述超硬材料層中。所述凸起結構或凹陷結構的徑向尺寸均不大于10mm,相鄰凸起結構和/或凹陷結構之間的間距也不大于10mm。本發(fā)明采用上述技術方案,超硬材料復合片的基體的各個側面均具有用于與所述超硬材料層結合固定的結合面,所述結合面為設有凸起結構和/或凹陷結構的結合面,所述超硬材料層通過所述基體的各個側面上的結合面結合固定在基體上,所述超硬材料層結合在各所述結合面上的部分相互連接,因此,與現有技術相比,基體與超硬材料層之間能夠依靠基體的各個側面和各個側面上的凸起結構和/或凹陷結構具有更大的結合面積,并且超硬材料層結合在各所述結合面上的部分相互連接可以使位于某一側面處的超硬材料層能夠依靠與其相鄰的超硬材料層更牢固地與基體結合,承受更大的受力,從而有效地預防基體與超硬材料之間的結合面開裂,形成牢固的結合。另外,在基體的凸起結構或凹陷結構的棱邊設有倒角能夠避免出現死角,從而有效地減小因結構突變造成的應力集中,起到更好的防開裂效果。附圖說明圖1是本發(fā)明中超硬材料復合片的實施例一的剖視圖;圖2是圖1的A—A剖視圖;圖3是圖1中基體的上表面和下表面上凹陷結構的輪廓和形狀示意圖;同時也是本發(fā)明中超硬材料復合片的基體的實施例一的結構示意圖;圖4是圖3的A’—A’剖視圖;圖5是本發(fā)明中超硬材料復合片的基體的實施例二的剖視圖,同時也是本發(fā)明中超硬材料復合片的實施例二中的基體的剖視圖;圖6是圖5的B—B剖視圖;圖7是圖5中基體的結合面上凸起結構的輪廓放大示意圖;圖8是本發(fā)明中超硬材料復合片的基體的實施例三的剖視圖,同時也是本發(fā)明中超硬材料復合片的實施例三中的基體的剖視圖;圖9是圖8的C—C剖視圖;圖10是圖8中基體的結合面上凸起結構和凹陷結構的輪廓放大示意圖;圖11是本發(fā)明中超硬材料復合片的基體的實施例四的剖視圖,同時也是本發(fā)明中超硬材料復合片的實施例四中的基體的剖視圖;圖12是圖11的D—D剖視圖;圖13是圖11中基體的結合面上凸起結構的輪廓放大示意圖;圖14是本發(fā)明中超硬材料復合片的實施例五的剖視圖(基體表面的凸起結構和凹陷結構未示出);圖15是圖14的E—E剖視圖。圖中各附圖標記對應的名稱為:1基體,11凸起結構,12凹陷結構,13刀片定位孔,2超硬材料層。具體實施方式本發(fā)明中超硬材料復合片的實施例一如圖1~圖4所示,是用于機械加工領域的超硬材料復合刀片,該超硬材料復合刀片是橫截面為圓形的圓形刀片,由超硬材料層2和硬質合金制成的基體1兩部分組成,基體1設置在超硬材料層2的中心位置,形成芯部結構?;w1的形狀接近圓柱狀,具有上面、下表面和圓周面三個側面,上表面、下表面和圓周面均為向外成圓弧形凸起的外凸結合面,三者之間平滑過渡連接;圓周面上的外凸結合面在基體1的軸向方向上的中間尺寸大于兩側尺寸?;w1的上表面和下表面上均設有不規(guī)則排列的凹陷結構12,包括兩圈同軸設置的環(huán)形凹陷和八條沿徑向設置的輻射狀凹陷,輻射狀凹陷的寬度由圓心向外逐漸增大,在基體1的上表面和下表面隔離出表面積大小不一的區(qū)域,靠近圓心的區(qū)域表面積小,遠離圓心的表面積大,能夠保證基體1與超硬材料層2的良好結合;基體1的圓周面上設有形狀為圓錐臺形的凹陷結構12。制造時,通過控制用于形成超硬材料層2的超硬材料粉料的用量,使燒結形成的超硬材料層2能夠完全把基體1包覆起來,并通過設有凹陷結構12的外凸結合面與基體1結合固定。本發(fā)明中超硬材料復合片的實施例二如圖5~圖7所示,與實施例一的不同之處在于:本實施例中,超硬材料復合刀片是橫截面為菱形的菱形刀片,基體1具有上表面、下表面和四個外側面等六個側面,六個側面均為向外成圓弧形凸起且彼此之間平滑過渡連接的外凸結合面。基體1的六個側面上均設有棱錐臺形狀的凸起結構11,棱錐母線與基線夾角小于90°,且小端朝外。制造時,通過控制用于形成超硬材料層2的超硬材料粉料的用量,使燒結形成的超硬材料層2能夠完全把基體1包覆起來,并通過設有凸起結構11的外凸結合面與基體1結合固定。本發(fā)明中超硬材料復合片的實施例三如圖8~圖10示,與實施例一的不同之處在于:本實施例中,超硬材料復合刀片是橫截面為方形的方形刀片,基體1具有上表面、下表面和四個外側面等六個側面,六個側面均為向外成圓弧形凸起且彼此之間平滑過渡連接的外凸結合面?;w1的六個側面上均設有方柱形狀的凹陷結構12和凸起結構11。制造時,通過控制用于形成超硬材料層2的超硬材料粉料的用量,使燒結形成的超硬材料層2能夠完全把基體1包覆起來,并通過設有凹陷結構12和凸起結構11的外凸結合面與基體1結合固定。本發(fā)明中超硬材料復合片的實施例四如圖11~圖13所示,與實施例一的不同之處在于:本實施例中,超硬材料復合刀片是橫截面為三角形的三角形刀片,基體1具有上表面、下表面和三個外側面等五個側面,五個側面均為向外成圓弧形凸起且彼此之間平滑過渡連接的外凸結合面?;w1的五個側面上均設有圓錐臺形狀的凸起結構11,圓錐母線與基線夾角小于90°,且小端朝外。制造時,通過控制用于形成超硬材料層2的超硬材料粉料的用量,使燒結形成的超硬材料層2能夠完全把基體1包覆起來,并通過設有凸起結構11的外凸結合面與基體1結合固定。本發(fā)明中超硬材料復合片的實施例五如圖14~圖15所示(基體1表面的凸起結構和凹陷結構未示出),與實施例三的不同之處在于:本實施例中,成品刀片上設有貫通上表面和下表面的刀片定位孔13,制造時,通過控制用于形成超硬材料層2的超硬材料粉料的用量,使基體1上除了與刀片定位孔13的孔口相對應的部分以外的表面均被包覆在所述超硬材料層2中。這樣,超硬材料層2結合到基體1上以后,能夠在裸露出來的硬質合金芯部很容易地開設刀片定位孔13,很好地解決環(huán)繞材料和現有技術中整體超硬材料刀片存在的難加工孔的弊端,便于使用時裝夾定位。上述各實施例中的超硬材料層2可以為立方氮化硼聚晶體、金剛石聚晶體以及陶瓷材料中的任意一種。而上述各實施例中用于形成芯部的基體1的結合面均為向外凸起的圓弧面,能夠在高壓高溫合成過程中減少與超硬材料之間的應力,提高復合片的韌性,同時還能夠增大結合面積。另外,上述各實施例中結合面為設有等間距均勻分布的凸起結構11或凹陷結構12的結合面,同樣能夠起到增大結合面積、提高結合力的作用,并且在凸起結構11或凹陷結構12的棱邊設有倒角,避免出現死角,能夠有效地減小因結構突變造成的應力集中。為了更好地避免由于殘余應力集中而導致的裂紋,上述各實施例中的凸起結構11或凹陷結構12的徑向尺寸均不大于10mm,相鄰凸起結構11和/或凹陷結構12之間的間距也不大于10mm,設計過程中,可以盡可能多的增加凸起結構11和/或凹陷結構12的數量,減少凸起結構11和/或凹陷結構12的尺寸,實現增加比表面積,提高實際結合強度的效果;而凸起結構11或凹陷結構12的排列形式可以為規(guī)則排列形式,也可以采用非規(guī)則排列形式。并且,外凸結合面的凸起高度小于基體1對應側面的半徑或基體1對應側面的邊長的一半,能夠避免在高溫高壓合成時產生應力集中。制造上述超硬材料復合片時,首先在用于制造超硬材料復合片的基體1的各個側面上分別加工出上述用于與超硬材料層2結合固定的結合面,然后將用于形成超硬材料層2的超硬材料粉料環(huán)繞在基體1外,放置到相應的模具中,并且使超硬材料粉料與各所述結合面對應的部分相互連接;最后,將環(huán)繞好的超硬材料粉料與基體1共同燒結,在基體1外部形成與基體1通過結合面結合固定的超硬材料層2,得到超硬材料復合片。通過控制超硬材料粉料的用量,可以使基體1完全被包覆在所述超硬材料層2中,形成如實施例一—實施例四中的復合刀片;或者使基體1上除刀片定位孔13的孔口外的表面均被包覆在所述超硬材料層2中,形成如實施例五中的復合刀片。本發(fā)明中超硬材料復合片的基體的實施例即上述各實施例中的基體,具體結構此處不再贅述。在上述實施例中,基體1各個側面上的結合面均為向外成圓弧形凸起的外凸結合面,并且結合面上設有凸起結構11或凹陷結構12。在本發(fā)明的其他實施例中,基體1各個側面上的結合面也可以是平面或者其他形式的結合面,例如波浪形結合面,而結合面向外凸起的形狀也可以是其他形狀,例如成角形凸起、非圓弧弧形凸起等。另外,結合面上的凸起結構11和/或凹陷結構12也可以省去或根據需要設置成其他形狀,例如半球形、正五邊形棱柱形狀、正六邊形棱柱形狀等,而在其他實施例中,超硬材料復合片的形狀也可以是ISO標準中的其他形狀,也可以是非標刀型。再者,在其他實施例中,與基體1各側面對應的超硬材料層2也可以部分連接在一起,而不用把基體1各側面的過渡處完全包覆。