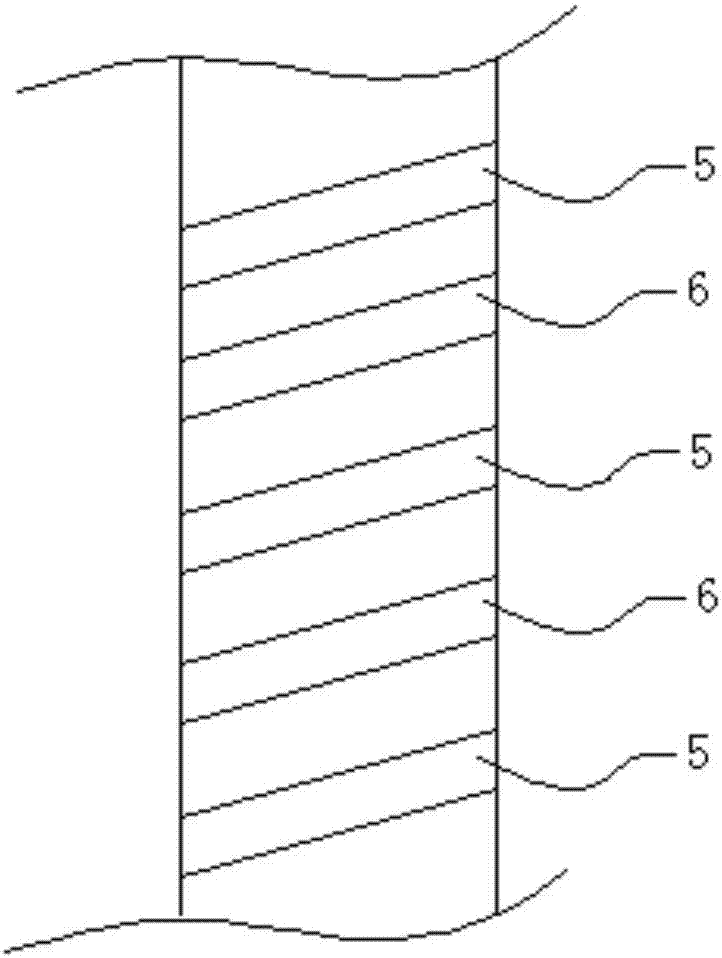
本發(fā)明涉及建筑用預應力管樁技術及其制作領域,尤其涉及一種抗震耐腐的預應力混凝土管樁及其制作方法。
背景技術:
:phc(預應力高強混凝土)管樁是預應力高強混凝土管樁的簡稱,是建筑基礎中最常采用的混凝土構件,被廣泛地應用于各類建筑、交通、水利等工程。我國是世界上最大的管樁生產國和使用國,近年來全國年產均量超過3.5億米?;炷潦枪軜妒褂玫闹饕现唬彩亲钪匾脑?,混凝土,簡稱為“砼”:是指由膠凝材料將集料膠結成整體的工程復合材料的統(tǒng)稱。通常講的混凝土一詞是指用水泥作膠凝材料,砂、石作集料;與水(可含外加劑和摻合料)按一定比例配合,經(jīng)攪拌而得的水泥混凝土,也稱普通混凝土,它廣泛應用于土木工程。但是對于phc管樁來說,混凝土的性能對其有重要的影響,特別是是沿海軟土地區(qū),由于存在腐蝕性地質條件,工程上對混凝土管樁的耐腐蝕性提出要求。而目前對于管樁的耐腐蝕問題,采用的主要方法是:摻入磨細礦渣、磨細粉煤灰等,降低混凝土中氧化鈣的含量,以減少氯離子等對管樁混凝土的腐蝕。這種生產方法,工藝復雜,需要增加磨細礦渣和磨細粉煤灰的儲罐及計量設備,另外,此類管樁強度不夠,抗震性能差;管樁耐腐能力有限,容易腐蝕,管樁的壽命短,存在塌陷的風險;而且需要通過高壓蒸汽養(yǎng)護增強管樁的強度,高壓蒸汽養(yǎng)護需要大量的蒸汽,生產過程能耗高;高壓釜投資大,維修成本高,存在安全隱患;經(jīng)過高溫蒸壓養(yǎng)護后,混凝土的耐久性下降,對管樁長期服役能力產生不利影響。因此十分有必要研究一種與鋼筋粘結性能優(yōu)越、抗侵蝕能力好、耐酸耐堿能力強、致密度高的混凝土以及利用該混凝土制作的高強度管樁。技術實現(xiàn)要素:本發(fā)明主要解決的技術問題是提供一種抗震耐腐預應力管樁,不僅具有抗侵蝕能力好、耐酸耐堿能力強的優(yōu)點,而且抗剪切能力強,抗彎承載力佳,抗震性能優(yōu),使用壽命長,特別適用于沿海軟土地質,更佳的是,制作周期短,安全性高,成本低。為解決上述技術問題,本發(fā)明采用的一個技術方案是:提供一種抗震耐腐預應力管樁,包括樁身本體和鋼筋,所述鋼筋包括縱向主筋、雙螺旋箍筋和環(huán)形箍筋,所述縱向主筋、所述雙螺旋箍筋和所述環(huán)形箍筋皆埋植于所述樁身本體內,所述雙螺旋箍筋纏繞于所述縱向主筋的外側,所述環(huán)形箍筋焊接于所述縱向主筋的內側,所述雙螺旋箍筋的螺旋方向與所述環(huán)形箍筋的傾斜方向相交;所述雙螺旋箍筋包括相互平行的第一螺旋箍筋和第二螺旋箍筋,所述第一螺旋箍筋和第二螺旋箍筋之間的距離為管樁外徑的1/10-1/8,所述雙螺旋箍筋的螺距為管樁外徑的1/4-1/2,所述管樁的兩端且為管樁外徑的2-4倍距離內皆為箍筋加密段,所述箍筋加密段的環(huán)形箍筋和螺旋箍筋的分布密度分別是管樁其余部分的環(huán)形箍筋和螺旋箍筋密度的2-3倍;所述鋼筋的表面皆設有一條從所述鋼筋的一端螺旋到另一端的螺旋凸棱,且所述螺旋凸棱之間設有從所述鋼筋的一端螺旋到另一端的螺旋凹槽,所述螺旋凸棱與所述螺旋凹槽在所述鋼筋表面構成凸棱與凹槽間隔排布的雙螺旋結構,且所述螺旋凸棱和所述螺旋凹槽的螺距皆為2-4cm,凸棱和凹槽的截面皆為等腰三角形,所述凸棱的高度和所述凹槽的深度皆為4-8mm,所述凸棱的根部寬度為5-10mm,所述凹槽的槽口寬度為5-10mm;所述鋼筋表面皆涂有第一防腐層,所述第一防腐層為環(huán)氧樹脂防銹層,所述環(huán)氧樹脂防銹層的厚度為4-6mm,所述環(huán)氧樹脂防銹層包括以下重量百分含量的原料:環(huán)氧樹脂為35-45%、增韌劑為13-15%、防銹劑為20-30%、硅烷偶聯(lián)劑為15-20%、聚酰胺固化劑為3-5%和腰果酚類固化劑為4-6%;所述樁身本體為混凝土樁身本體,所述混凝土包括以下重量份的原料組成:52.5級的普通硅酸鹽水泥為100-150份、42.5r級粉煤灰硅酸鹽水泥為130-160份、52.5r級復合硅酸鹽水泥為180-200份、粒徑為5-20mm的碎石100-200份、粒徑為0.5-10mm的粗砂100-200份、粒徑為0.35-0.5mm的中砂100-200份、粒徑為0.25-0.35mm的細砂20-40份、脫硫石膏為10-20份、聚羧酸減水劑為5-10份、抗凝劑為3-5份、鋼筋阻銹劑為1-2份和水為80-90份;所述樁身本體表面有第二防腐層,所述第二防腐層為有機硅防腐層,所述有機硅防腐層包括厚度為3-5mm的薄膜層和能夠滲入樁身本體內3-7mm的滲入層。進一步地說,所述第一螺旋箍筋和第二螺旋箍筋之間的距離為管樁外徑的1/9-1/8,所述雙螺旋箍筋的螺距為管樁外徑的1/4-1/3,所述管樁的兩端且為管樁外徑的2-3倍距離內皆為箍筋加密段。進一步地說,所述螺旋凸棱和所述螺旋凹槽的螺距皆為3-4cm,所述凸棱的高度和所述凹槽的深度皆為6-8mm,所述凸棱的根部寬度為5-8mm,所述凹槽的槽口寬度為5-8mm。進一步地說,所述聚羧酸減水劑由以下重量百分比的原料組成:聚羧酸超塑化劑為22-25%,氫氧化鈉為0.3-0.6%,過硫酸銨為0.2-0.4%,葡萄糖酸鈉為1-2%,硅酸鈉為3-5%,消泡劑為0.04-0.6%,余量為水。進一步地說,所述增塑劑為上海美東生物材料有限公司的md5020型號產品,所述防銹劑為深圳市鈍化技術有限公司的dh-906型號產品。進一步地說,所述環(huán)氧樹脂防銹層的厚度為5-6mm;所述有機硅防腐層包括厚度為3-4mm薄膜層和能夠滲入樁身本體內5-7mm的滲入層。進一步地說,所述鋼筋阻銹劑為亞硝酸鹽類的阻銹劑、氨基醇類的阻銹劑或氨基羧酸類阻銹劑。進一步地說,所述抗凝劑為多聚磷酸鈉混合體、多聚磷酸鉀混合體和多聚磷酸鈣混合體中的至少一種。進一步地說,所述的一種抗震耐腐預應力管樁的制作方法,按照下述步驟進行:步驟一:將普通硅酸鹽水泥、粉煤灰硅酸鹽水泥、復合硅酸鹽水泥、碎石、粗砂、中砂、細砂、脫硫石膏、聚羧酸減水劑、抗凝劑、鋼筋阻銹劑和水按配比加入攪拌機,一起攪拌10-15分鐘,溫度控制在80-90℃,得到混凝土混合料備用;步驟二:同時將主筋和箍筋軋制成鋼筋籠,并吊入離心成型機的模具內;步驟三:將步驟一所述的混凝土混合料加入模具內,鎖緊模具螺絲,然后依次經(jīng)過低速離心、低中速離心、中速離心和高速離心;步驟四:離心成型后的混凝土管樁,進行常壓養(yǎng)護,先于25-30℃下靜停1-2h,然后置于蒸汽養(yǎng)護池中,在2-3h內勻速升溫至80-84℃,隨后在80-84℃下在保溫3-5h,冷卻后脫模;步驟五:在脫模后的管樁樁身本體表面刷涂一層有機硅防腐層,在20-35℃下干燥0.5-1h即可得到成品。進一步地說,步驟三所述低速離心是在轉速為40-50r/min下離心3-4min;所述低中速離心是在轉速為112-125r/min下離心1-1.5min;所述中速離心是在轉速為236-243r/min下離心2-2.5min;所述高速離心是在轉速500-550r/min下離心5-7min。本發(fā)明的有益效果是:本發(fā)明至少具有以下幾點優(yōu)點:一、本發(fā)明相比普通的單螺旋箍筋phc管樁增加一圈螺旋箍筋,采用雙螺旋箍筋結構,再者縱向主筋內側焊接有與螺旋箍筋螺旋方向相交的環(huán)形箍筋,且箍筋在兩端距管樁端面2-4倍樁徑距離區(qū)間內加密布置,能大大提升管樁的水平抗剪和豎向抗拔性能,進而抗剪切能力強,抗彎承載力佳,抗震性能優(yōu),使用壽命長;二、本發(fā)明的箍筋和主筋的表面均設有由螺旋凸棱和螺旋凹槽組成的雙螺旋結構,而且凸起的截面為帶尖端的等腰三角形,大大提高與樁身混凝土的結合力,提高密實度,進而增強鋼筋的承重能力和抗震性;三、本發(fā)明的樁身本體采用的混凝土,配方合理,大大優(yōu)化了混凝土的凝膠部分的性能,普通硅酸鹽水泥可以提高水泥的韌性和強度,可以提高混凝土與其他組分之間的結合性能,同時復合硅酸鹽水泥會改善固化時間和收縮率,同時本發(fā)明還通過添加碎石、粗砂和中砂等輔助材料,雖然以上的輔助材料是常見的輔料,但是通過整體的優(yōu)化,一方面降低混凝土的成本,同時還會提高混凝土的力學性能以及粘結性能;更佳的是,本發(fā)明的減水劑其減水率高、分散性好、坍落度損失小且非常的環(huán)保;四、本發(fā)明中將鋼筋阻銹劑摻入樁身混凝土中,有明顯促凝作用,減少坍落度損失,而且在鋼筋表面形成致密的保護層,當有害離子(如氯離子)侵入混凝土結構中,它能有效的抑制、阻止和延緩鋼筋銹蝕的電化學反應過程,從而延長鋼筋混凝土結構的使用壽命;五、本發(fā)明的縱向主筋和螺旋箍筋表面涂有環(huán)氧樹脂防銹層,其中采用的環(huán)氧樹脂、增韌劑、防銹劑、硅烷偶聯(lián)劑、聚酰胺固化劑和腰果酚類固化劑,配方合理,性能優(yōu)越,能在鋼筋表面形成的一層惰性、低表面能的氧化物薄膜,大大提高鋼筋的抗侵蝕能力和耐酸耐堿能力;六、本發(fā)明的管樁的樁身本體表面涂有有機硅防腐層,采用有機硅防腐處理,不僅在表面形成簿膜,還可以滲入表層3-7mm,進一步提高管樁的防腐蝕能力,即使表面涂層被損壞了,滲入混凝土里面的部分仍然起了強有力的防護作用;七、本發(fā)明的管樁離心成型后僅通過常壓蒸養(yǎng)和較短時間的自然養(yǎng)護就能達到85mpa以上,經(jīng)過20天自然養(yǎng)護可以達到85mpa以上,省去了高壓蒸養(yǎng)工藝,縮短了生產周期,每生產1m管樁可以減少消耗標準燃煤近75%。上述說明僅是本發(fā)明技術方案的概述,為了能夠更清楚了解本發(fā)明的技術手段,并可依照說明書的內容予以實施,以下以本發(fā)明的較佳實施例并配合附圖詳細說明如后。附圖說明圖1是本發(fā)明的樁體內鋼筋分布示意圖;圖2是本發(fā)明的鋼筋的結構示意圖;圖3是本發(fā)明的鋼筋的縱向剖面示意圖;附圖中各部分標記如下:樁身本體1、雙螺旋箍筋2、第一螺旋箍筋21、第二螺旋箍筋22、縱向主筋3、環(huán)形箍筋4、螺旋凸棱5和螺旋凹槽6。具體實施方式以下通過特定的具體實施例說明本發(fā)明的具體實施方式,本領域技術人員可由本說明書所揭示的內容輕易地了解本發(fā)明的優(yōu)點及功效。本發(fā)明也可以其它不同的方式予以實施,即,在不背離本發(fā)明所揭示的范疇下,能予不同的修飾與改變。實施例:一種抗震耐腐預應力管樁,如圖1、圖2和圖3所示(虛線表示環(huán)形箍筋),包括樁身本體1和鋼筋,所述鋼筋包括縱向主筋3、雙螺旋箍筋2和環(huán)形箍筋4,所述縱向主筋3、所述雙螺旋箍筋2和所述環(huán)形箍筋4皆埋植于所述樁身本體1內,所述雙螺旋箍筋2纏繞于所述縱向主筋3的外側,所述環(huán)形箍筋4焊接于所述縱向主筋3的內側,所述雙螺旋箍筋2的螺旋方向與所述環(huán)形箍筋4的傾斜方向相交;所述雙螺旋箍筋2包括相互平行的第一螺旋箍筋21和第二螺旋箍筋22,所述第一螺旋箍筋和第二螺旋箍筋之間的距離為管樁外徑的1/10-1/8,所述雙螺旋箍筋的螺距為管樁外徑的1/4-1/2,所述管樁的兩端且為管樁外徑的2-4倍距離內皆為箍筋加密段,所述箍筋加密段的環(huán)形箍筋和螺旋箍筋的分布密度分別是管樁其余部分的環(huán)形箍筋和螺旋箍筋密度的2-3倍;所述鋼筋的表面皆設有一條從所述鋼筋的一端螺旋到另一端的螺旋凸棱5,且所述螺旋凸棱5之間設有從所述鋼筋的一端螺旋到另一端的螺旋凹槽6,所述螺旋凸棱5與所述螺旋凹槽6在所述鋼筋表面構成凸棱與凹槽間隔排布的雙螺旋結構,且所述螺旋凸棱5和所述螺旋凹槽6的螺距皆為2-4cm,凸棱和凹槽的截面皆為等腰三角形,所述凸棱的高度和所述凹槽的深度皆為4-8mm,所述凸棱的根部寬度為5-10mm,所述凹槽的槽口寬度為5-10mm;所述鋼筋表面皆涂有第一防腐層,所述第一防腐層為環(huán)氧樹脂防銹層,所述環(huán)氧樹脂防銹層的厚度為4-6mm,所述環(huán)氧樹脂防銹層包括以下重量百分含量的原料:環(huán)氧樹脂為35-45%、增韌劑為13-15%、防銹劑為20-30%、硅烷偶聯(lián)劑為15-20%、聚酰胺固化劑為3-5%和腰果酚類固化劑為4-6%;所述樁身本體1為混凝土樁身本體,所述混凝土包括以下重量份的原料組成:52.5級的普通硅酸鹽水泥為100-150份、42.5r級粉煤灰硅酸鹽水泥為130-160份、52.5r級復合硅酸鹽水泥為180-200份、粒徑為5-20mm的碎石100-200份、粒徑為0.5-10mm的粗砂100-200份、粒徑為0.35-0.5mm的中砂100-200份、粒徑為0.25-0.35mm的細砂20-40份、脫硫石膏為10-20份、聚羧酸減水劑為5-10份、抗凝劑為3-5份、鋼筋阻銹劑為1-2份和水為80-90份;所述樁身本體1表面有第二防腐層,所述第二防腐層為有機硅防腐層,所述有機硅防腐層包括厚度為3-5mm的薄膜層和能夠滲入樁身本體內3-7mm的滲入層。優(yōu)選的,所述第一螺旋箍筋21和第二螺旋箍筋22之間的距離為管樁外徑的1/9-1/8,所述雙螺旋箍筋的螺距為管樁外徑的1/4-1/3,所述管樁的兩端且為管樁外徑的2-3倍距離內皆為箍筋加密段。優(yōu)選的,所述螺旋凸棱5和所述螺旋凹槽6的螺距皆為3-4cm,所述凸棱的高度和所述凹槽的深度皆為6-8mm,所述凸棱的根部寬度為5-8mm,所述凹槽的槽口寬度為5-8mm。所述聚羧酸減水劑由以下重量百分比的原料組成:聚羧酸超塑化劑為22-25%,氫氧化鈉為0.3-0.6%,過硫酸銨為0.2-0.4%,葡萄糖酸鈉為1-2%,硅酸鈉為3-5%,消泡劑為0.04-0.6%,余量為水。所述增塑劑為上海美東生物材料有限公司的md5020型號產品,所述防銹劑為深圳市鈍化技術有限公司的dh-906型號產品。所述環(huán)氧樹脂防銹層的厚度為5-6mm;所述有機硅防腐層包括厚度為3-4mm薄膜層和能夠滲入樁身本體內5-7mm的滲入層。所述鋼筋阻銹劑為亞硝酸鹽類的阻銹劑、氨基醇類的阻銹劑或氨基羧酸類阻銹劑。所述抗凝劑為多聚磷酸鈉混合體、多聚磷酸鉀混合體和多聚磷酸鈣混合體中的至少一種。實施例1到實施例5的環(huán)氧樹脂防銹層的配方和混凝土的配方分別如表1和表2所示。表2:實施例1實施例2實施例3實施例4實施例552.5級的普通硅酸鹽水泥(份)10012015011013042.5r級粉煤灰硅酸鹽水泥(份)13014016015013552.5r級復合硅酸鹽水泥(份)200190180185195粒徑為5-20mm的碎石(份)100200120150180粒徑為0.5-10mm的粗砂(份)200150160170100粒徑為0.35-0.5mm的中砂(份)120100140200180粒徑為0.25-0.35mm的細砂(份)2035403025脫硫石膏(份)1517102018聚羧酸減水劑(份)567109抗凝劑(份)34543鋼筋阻銹劑(份)121.521水(份)8085908783實施例1到實施例5,所述的一種抗震耐腐預應力管樁的制作方法,按照下述步驟進行:步驟一:將普通硅酸鹽水泥、粉煤灰硅酸鹽水泥、復合硅酸鹽水泥、碎石、粗砂、中砂、細砂、脫硫石膏、聚羧酸減水劑、抗凝劑、鋼筋阻銹劑和水按配比加入攪拌機,一起攪拌10-15分鐘,溫度控制在80-90℃,得到混凝土混合料備用;步驟二:同時將主筋和箍筋軋制成鋼筋籠,并吊入離心成型機的模具內;步驟三:將步驟一所述的混凝土混合料加入模具內,鎖緊模具螺絲,然后依次經(jīng)過低速離心、低中速離心、中速離心和高速離心;步驟四:離心成型后的混凝土管樁,進行常壓養(yǎng)護,先于25-30℃下靜停1-2h,然后置于蒸汽養(yǎng)護池中,在2-3h內勻速升溫至80-84℃,隨后在80-84℃下在保溫3-5h,冷卻后脫模;步驟五:在脫模后的管樁樁身本體表面刷涂一層有機硅防腐層,在20-35℃下干燥0.5-1h即可得到成品。步驟三所述低速離心是在轉速為40-50r/min下離心3-4min;所述低中速離心是在轉速為112-125r/min下離心1-1.5min;所述中速離心是在轉速為236-243r/min下離心2-2.5min;所述高速離心是在轉速500-550r/min下離心5-7min。本發(fā)明提供的一種抗震耐腐預應力管樁,不僅具有抗侵蝕能力好、耐酸耐堿能力強的優(yōu)點,而且抗剪切能力強,抗彎承載力佳,抗震性能優(yōu),使用壽命長,特別適用于沿海軟土地質,更佳的是,制作周期短,安全性高,成本低。以上所述僅為本發(fā)明的實施例,并非因此限制本發(fā)明的專利范圍,凡是利用本發(fā)明說明書及附圖內容所作的等效結構,或直接或間接運用在其他相關的
技術領域:
,均同理包括在本發(fā)明的專利保護范圍內。當前第1頁12