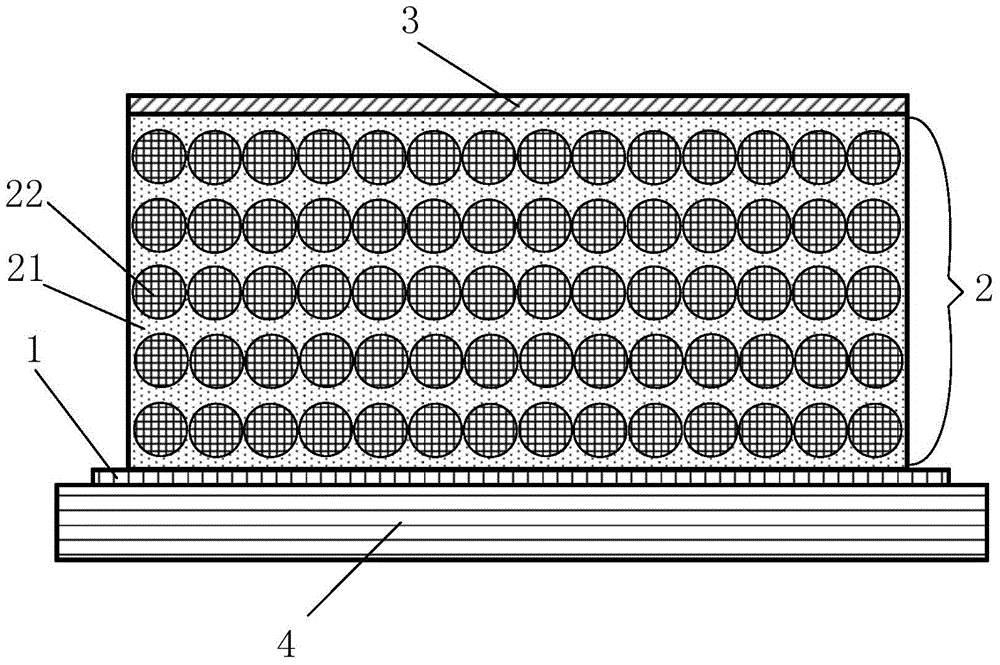
本發(fā)明屬于光電子材料與器件技術(shù)領(lǐng)域,具體涉及一種可用于電子束器件、發(fā)光器件、平板顯示器件、微波器件和傳感器件的納米硅/氮化硅薄膜型電子源及其制作方法。
背景技術(shù):場發(fā)射電子源的種類很多,有Spindt型、硅微尖型、碳納米管型、金剛石薄膜型、類金剛石薄膜型、多孔硅型和表面?zhèn)鲗?dǎo)電子發(fā)射型、金屬——絕緣體(氧化物)——金屬型和金屬——絕緣體(氧化物)——半導(dǎo)體——金屬型等。為了獲得良好的場致電子發(fā)射,電子源材料應(yīng)滿足的基本要求有:較低的功函數(shù),場發(fā)射開啟電壓低;場發(fā)射電流密度大并且均勻穩(wěn)定;較高的電導(dǎo)率和熔點;穩(wěn)定的表面物理化學(xué)性質(zhì);材料經(jīng)濟(jì)實用,成本低,易加工等。在眾多電子源材料中,硅材料的加工處理與半導(dǎo)體工藝技術(shù)相兼容,因而工藝成熟,加工精度高,易于制備具有不同結(jié)構(gòu)要求的場發(fā)射電子源。例如,采用鍍膜和光刻工藝可以制備出硅微尖陣列電子源,該電子源可以在很低的開關(guān)電壓下產(chǎn)生較高的發(fā)射電流。但硅陣列電子源的熱穩(wěn)定性較差、發(fā)射可靠性低以及難以大面積制備。多孔硅電子源是另一種硅基場發(fā)射電子源,它主要利用電化學(xué)陽極刻蝕技術(shù)制備而成,與其他場發(fā)射電子源相比,利用多孔硅制作的平面型電子源工藝相對簡單,且具有驅(qū)動電壓低和電子發(fā)散角小等特點,更重要的是其對環(huán)境氣壓不敏感,甚至可在氣體中發(fā)射電子。但多孔硅電子源也存在以下不足之處:(1)多孔硅電子源的電子發(fā)射穩(wěn)定性較差,機(jī)械性能和化學(xué)性能不穩(wěn)定,不利于制備長時間使用的器件。(2)電化學(xué)陽極刻蝕技術(shù)采用氫氟酸作為腐蝕液,會產(chǎn)生有毒廢水,嚴(yán)重污染環(huán)境,因而有很大的局限性。
技術(shù)實現(xiàn)要素:本發(fā)明的目的在于提供一種納米硅/氮化硅薄膜型電子源及其制作方法,該方法安全環(huán)保,制得的納米硅/氮化硅薄膜電子源既有好的電子發(fā)射穩(wěn)定性,還具有高的電子發(fā)射密度。為了達(dá)到上述目的,本發(fā)明納米硅/氮化硅薄膜電子源,包括依次沉積在基底上的底電極、納米硅/氮化硅層以及頂電極;其中,納米硅/氮化硅層采用鑲嵌有納米晶硅的氮化硅薄膜;或者納米硅/氮化硅層采用納米晶硅層與氮化硅層交替組成的多層薄膜。所述的納米硅/氮化硅層中的納米晶硅的粒徑為3-6nm,納米硅/氮化硅層的厚度為100-2000nm;其中,鑲嵌有納米晶硅的氮化硅薄膜中相鄰納米晶硅間的氮化硅的厚度為0.5-1.5nm;或者納米晶硅層與氮化硅層交替組成的多層薄膜中每層氮化硅的厚度為0.5-1.5nm。一種納米硅/氮化硅薄膜電子源的制作方法,采用濺射法在基底上沉積底電極;然后采用濺射法結(jié)合高溫退火工藝在底電極上制備納米硅/氮化硅層;接著采用濺射法在納米硅/氮化硅層上沉積頂電極,即得到納米硅/氮化硅薄膜電子源;其中,納米硅/氮化硅層采用如下兩種方法之一制得:第一種方法:在底電極上沉積富硅氮化硅薄膜,其中的硅以非晶的形式存在,然后對富硅氮化硅薄膜進(jìn)行高溫退火處理,使其中的非晶硅轉(zhuǎn)變?yōu)榧{米晶硅,以形成納米硅/氮化硅層;且納米硅/氮化硅層為鑲嵌有納米晶硅的氮化硅薄膜;第二種方法:在底電極上交替沉積非晶硅薄膜和氮化硅薄膜以構(gòu)成非晶硅/氮化硅交替多層復(fù)合薄膜,然后對非晶硅/氮化硅交替多層復(fù)合薄膜進(jìn)行高溫退火處理,使非晶硅轉(zhuǎn)變?yōu)榧{米晶硅以得到納米硅/氮化硅層;且納米硅/氮化硅層為由納米晶硅層與氮化硅層交替組成的多層薄膜。第一種方法中沉積富硅氮化硅薄膜采用以下三種方式中的一種來實現(xiàn):第一種方式:向鍍膜腔中通入氬氣和氮氣,控制氬氣與氮氣的分壓比為(10:1)-(1:1),以硅靶為濺射源在底電極上沉積富硅氮化硅薄膜;第二種方式:向鍍膜腔中通入氬氣,以硅靶和氮化硅靶為共濺射源在底電極上沉積富硅氮化硅薄膜;第三種方式:向鍍膜腔中通入氬氣,以硅和氮化硅復(fù)合靶為濺射源在底電極上沉積富硅氮化硅薄膜;第二種方法中沉積非晶硅/氮化硅交替多層復(fù)合薄膜采用以下兩種方式中的一種來實現(xiàn):第一種方式:以硅靶為濺射源在底電極上沉積非晶硅/氮化硅交替多層復(fù)合薄膜,在濺射硅靶過程中,向鍍膜腔中交替性地通入氬氣以及同時通入氬氣和氮氣,在同時通入氬氣和氮氣時,保持鍍膜腔中氬氣與氮氣的分壓比為(1:2)-(1:4),每次通入氬氣或同時通入氬氣和氮氣的時間為1-10分鐘;第二種方式:向鍍膜腔中通入氬氣,以硅靶和氮化硅靶為濺射源,交替濺射硅靶和氮化硅靶沉積非晶硅/氮化硅交替多層復(fù)合薄膜,每次濺射硅靶或氮化硅靶的時間為1-10分鐘。在沉積富硅氮化硅薄膜或非晶硅/氮化硅交替多層復(fù)合薄膜的過程中,控制鍍膜腔中總氣壓為0.07-4.0Pa;基底的溫度控制在300-600℃。所述的第一種方法和第二種方法中高溫退火處理是在氮氣環(huán)境中或者由體積比為(50:1)-(10:1)的氮氣和氫氣組成的混合氣體環(huán)境中進(jìn)行的,且高溫退火處理的溫度為500-1100℃,高溫退火處理的時間為30-120分鐘。所述的底電極采用濺射鎢、鎳、鉻、鋁、銅、鈦中一種材料的靶材或由其中幾種材料組成的復(fù)合靶材在基底上沉積得到的。所述的頂電極采用濺射Au、Ag、Pt中一種材料的靶材或由其中幾種材料組成的復(fù)合靶材在納米硅/氮化硅層上沉積得到的。與現(xiàn)有技術(shù)相比,本發(fā)明的有益效果在于:1、本發(fā)明在電子源的頂電極和底電極之間加入了納米硅/氮化硅層,其中的氮化硅由于隧穿勢壘較低(1.5-2.0ev),有利于電子的注入,并且其還具有良好的物理化學(xué)穩(wěn)定性及高熔點和高密度的特性,而電子在納米晶硅中傳輸時有較大的漂移長度,因此由超薄的氮化硅層分隔的納米晶硅組成的薄膜作為電子源材料,一方面電子在其中傳輸時受到的散射較少,另一方面可在納米硅/氮化硅層中施加較強(qiáng)的電場以利于電子加速,因而,本發(fā)明的納米硅/氮化硅薄膜電子源具有良好的電子發(fā)射能力。2、本發(fā)明納米硅/氮化硅薄膜電子源具有多層結(jié)構(gòu),由依次制作于基底上的底電極——納米硅/氮化硅層(由納米晶硅和氮化硅組成)——頂電極構(gòu)成,其中的納米硅/氮化硅層采用濺射法結(jié)合高溫退火工藝制作。與其它鍍膜技術(shù)相比,本發(fā)明采用的濺射法可以制備致密、均勻、重復(fù)性好的富硅氮化硅薄膜(其中的硅為非晶硅,即α-Si)或α-Si/氮化硅多層復(fù)合薄膜。此外,本發(fā)明采用干法制備工藝,克服了電化學(xué)陽極濕法刻蝕帶來的污染問題,工藝與硅基微電子加工工藝兼容。進(jìn)一步,本發(fā)明納米硅/氮化硅薄膜型電子源的納米硅/氮化硅層中,納米晶硅的粒徑為3-6nm;鑲嵌有納米晶硅的氮化硅層中相鄰納米晶硅間的氮化硅的厚度為0.5-1.5nm;或者納米晶硅層與氮化硅層交替組成的多層薄膜中每層氮化硅的厚度為0.5-1.5nm。這樣可減小電子在薄膜內(nèi)部運動過程中受到的散射。進(jìn)一步,本發(fā)明對富硅氮化硅薄膜或α-Si/氮化硅多層復(fù)合薄膜采用氮氣/氫氣混合氣體環(huán)境中的高溫退火處理以形成納米硅/氮化硅層,使膜層中存在的大量硅的懸掛鍵可以被退火過程中擴(kuò)散到膜層內(nèi)部的氫原子所飽和,因而可以消除硅的懸掛鍵缺陷,從而進(jìn)一步減小電子在膜層中傳輸時受到的散射和被捕獲幾率。因此,這樣制備出的納米硅/氮化硅薄膜電子源既有好的電子發(fā)射的穩(wěn)定性,同時還有高的電子發(fā)射密度,而且機(jī)械和化學(xué)性能穩(wěn)定。進(jìn)一步,本發(fā)明通過調(diào)節(jié)硅靶和氮化硅靶的濺射功率和濺射時間、通入鍍膜腔中的氬氣和氮氣的分壓比以及后續(xù)高溫退火工藝中的退火溫度和退火時間,從而能夠更精確地控制最終形成的納米硅/氮化硅層中的硅晶粒大小、硅晶粒密度及膜層總厚度,并且可以減少硅原子懸掛鍵等硅晶粒與氮化硅的界面缺陷,以達(dá)到減小電子在膜層傳輸過程中受到的散射和被捕獲幾率的目的。本發(fā)明的納米硅/氮化硅薄膜電子源具有底電極——納米硅/氮化硅層——頂電極結(jié)構(gòu),其中的納米硅/氮化硅層采用濺射法結(jié)合高溫退火工藝制備;且納米硅/氮化硅層采用鑲嵌有納米晶硅的氮化硅薄膜;或者納米硅/氮化硅層采用納米晶硅層與氮化硅層交替組成的多層薄膜。在納米硅/氮化硅層的制備過程中,通過調(diào)節(jié)通入鍍膜腔中的氬氣和氮氣的分壓比或調(diào)節(jié)硅靶(純硅靶、摻磷的n型硅靶或摻硼的p型硅靶)和氮化硅靶的濺射功率,使薄膜中硅的含量發(fā)生改變,來控制最后制得的納米硅/氮化硅層中的硅晶粒的大小及密度。附圖說明圖1是第一種納米硅/氮化硅薄膜電子源的結(jié)構(gòu)示意圖;圖2是第二種納米硅/氮化硅薄膜電子源的結(jié)構(gòu)示意圖;圖3是納米硅/氮化硅薄膜電子源的電子發(fā)射特性曲線。其中,1、底電極,2、納米硅/氮化硅層,21、氮化硅,22、納米晶硅,3、頂電極,4、基底。具體實施方式下面結(jié)合附圖對本發(fā)明做進(jìn)一步詳細(xì)說明。參見圖1和2,本發(fā)明納米硅/氮化硅薄膜電子源包括依次沉積在基底4上的厚度為40-200nm的底電極1、厚度為100-2000nm的納米硅/氮化硅層2以及厚度為5-15nm的頂電極3;其中,納米硅/氮化硅層2中的納米晶硅22的粒徑為3-6nm;納米硅/氮化硅層2采用鑲嵌有納米晶硅22的氮化硅21薄膜,鑲嵌有納米晶硅22的氮化硅21薄膜中相鄰納米晶硅22之間氮化硅21的厚度為0.5-1.5nm(見圖1);或者納米硅/氮化硅層2采用納米晶硅22與氮化硅21交替組成的多層薄膜,多層薄膜中每層氮化硅21的厚度為0.5-1.5nm(見圖2)。如圖1所示的第一種納米硅/氮化硅薄膜電子源的制備方法包括以下步驟:1)采用濺射鎢、鎳、鉻、鋁、銅、鈦中一種材料的靶材或由其中幾種材料組成的復(fù)合靶材在基底4上沉積底電極1,其厚度為40-200nm;2)在底電極1上沉積厚度為100-2000nm的納米硅/氮化硅層2,其方法為:在底電極1上沉積富硅氮化硅薄膜,其中的硅以非晶的形式存在,然后在氮氣或由體積比為(50:1)-(10:1)的氮氣和氫氣組成的混合氣體中于500-1100℃對富硅氮化硅薄膜進(jìn)行高溫退火,高溫退火時間為30-120分鐘,使富硅氮化硅薄膜(SiNx,x<4/3)中的非晶硅轉(zhuǎn)變?yōu)榧{米晶硅22,以形成納米硅/氮化硅層2;且納米硅/氮化硅層2為鑲嵌有納米晶硅22的氮化硅21薄膜;其中,沉積富硅氮化硅薄膜采用以下三種方式中的一種來實現(xiàn):第一種方式:向鍍膜腔中通入氬氣和氮氣,控制氬氣與氮氣的分壓比為(10:1)-(1:1),以硅靶為濺射源在底電極1上沉積富硅氮化硅薄膜;第二種方式:向鍍膜腔中通入氬氣,以硅靶和氮化硅靶為共濺射源在底電極1上沉積富硅氮化硅薄膜;第三種方式:向鍍膜腔中通入氬氣,以硅和氮化硅復(fù)合靶為濺射源在底電極1上沉積富硅氮化硅薄膜;上述三種方式中控制鍍膜腔中總氣壓為0.07-4.0Pa;基底4的溫度控制在300-600℃;3)通過濺射Au、Ag、Pt中一種材料的靶材或由其中幾種材料組成的復(fù)合靶材在納米硅/氮化硅層2上沉積頂電極層3,其厚度為5-15nm。如圖2所示的第二種納米硅/氮化硅薄膜電子源的制備方法包括以下步驟:1)采用濺射鎢、鎳、鉻、鋁、銅、鈦中一種材料的靶材或由其中幾種材料組成的復(fù)合靶材在基底4上沉積底電極1,其厚度為40-200nm;2)在底電極1上交替沉積非晶硅薄膜和氮化硅薄膜以構(gòu)成非晶硅/氮化硅交替多層復(fù)合薄膜,然后在氮氣或由體積比為(50:1)-(10:1)的氮氣和氫氣組成的混合氣體中于500-1100℃對富硅氮化硅薄膜進(jìn)行高溫退火,高溫退火時間為30-120分鐘,使非晶硅轉(zhuǎn)變?yōu)榧{米晶硅22以得到納米硅/氮化硅層2;且納米硅/氮化硅層2為納米晶硅22層與氮化硅21層交替組成的多層薄膜;非晶硅/氮化硅交替多層復(fù)合薄膜是采用以下兩種方式中的一種進(jìn)行沉積的:第一種方式:以硅靶為濺射源在底電極1上沉積非晶硅/氮化硅交替多層復(fù)合薄膜,在薄膜沉積過程中,向鍍膜腔中交替性地通入氬氣以及同時通入氬氣和氮氣,同時通入氬氣和氮氣時,保持鍍膜腔中氬氣和氮氣的分壓比為(1:2)-(1:4),每次通入氬氣或同時通入氬氣和氮氣的時間為1-10分鐘;第二種方式:向鍍膜腔中通入氬氣,以硅靶和氮化硅靶為濺射源,交替濺射硅靶和氮化硅靶以沉積非晶硅/氮化硅交替多層復(fù)合薄膜,每次濺射硅靶或氮化硅靶的時間為1-10分鐘;3)通過濺射Au、Ag、Pt中一種材料的靶材或由其中幾種材料組成的復(fù)合靶材在納米硅/氮化硅層2上沉積頂電極層3,其厚度為5-15nm。上述兩種方式中控制鍍膜腔中總氣壓為0.07-4.0Pa,基底4的溫度控制在300-600℃。本發(fā)明的納米硅/氮化硅薄膜電子源的電子發(fā)射過程為:在頂電極3和底電極1間施加一個電壓(10~30V),電子由底電極進(jìn)入到納米硅/氮化硅層2中,電子在電場的作用下相繼多次隧穿通過相鄰納米晶硅22之間的氮化硅21,并在納米硅/氮化硅層2中(特別是在氮化硅21中)得到加速,最終有部分具有較高能量的電子穿過頂電極而發(fā)射出去。電子在傳輸過程中可能會受到膜層中電子和聲子的散射及電子陷阱的捕獲使電子能量降低和傳輸電子數(shù)目減少,這將影響到電子源的電子發(fā)射穩(wěn)定性和發(fā)射密度。本發(fā)明的基本構(gòu)思是:氮化硅的隧穿勢壘較低(1.5-2.0ev),有利于電子的注入,而且它還具有良好的物理化學(xué)穩(wěn)定性及高熔點和高密度的特性,而電子在納米晶硅中傳輸時有較大的漂移長度。用由很薄的氮化硅層分隔的納米晶硅組成的薄膜作為電子源材料,一方面電子在其中傳輸時受到的散射較少,另一方面可在納米硅/氮化硅薄膜中施加較強(qiáng)的電場以利于電子加速,因而納米硅/氮化硅薄膜是一種適合的電子發(fā)射材料。納米硅/氮化硅薄膜電子源具有多層結(jié)構(gòu),由依次制作于基底上的底電極——納米硅/氮化硅層(由納米晶硅和氮化硅組成)——頂電極構(gòu)成,其中的納米硅/氮化硅層采用濺射法結(jié)合高溫退火工藝制作。和其它鍍膜技術(shù)相比,濺射法可以制備致密、均勻、重復(fù)性好的富硅氮化硅薄膜或α-Si/氮化硅多層復(fù)合薄膜,并可以通過調(diào)節(jié)硅靶和氮化硅靶的濺射功率和濺射時間、氬氣和氮氣分壓比以及后續(xù)高溫退火工藝中的退火溫度和退火時間,從而更精確地控制最終形成的納米硅/氮化硅層中的硅晶粒大小、硅晶粒密度及膜層總厚度。制備的納米硅/氮化硅層中的納米晶硅的粒徑為3-6nm,而鑲嵌有納米晶硅的氮化硅層中相鄰納米晶硅間的氮化硅的厚度為0.5-1.5nm;或者納米晶硅層與氮化硅層交替組成的多層薄膜中每層氮化硅的厚度為0.5-1.5nm。這樣可減小電子在薄膜內(nèi)部運動過程中受到的散射。此外,在富硅氮化硅薄膜或非晶硅/氮化硅交替多層復(fù)合薄膜經(jīng)過在含氫氣的氣氛中的高溫退火處理以形成納米硅/氮化硅層時,氫原子擴(kuò)散到膜層內(nèi)部可以消除硅的懸掛鍵缺陷,從而進(jìn)一步減小電子在膜層傳輸過程中受到的散射和被捕獲幾率。因此,這樣制備出的納米硅/氮化硅薄膜電子源既有好的電子發(fā)射的穩(wěn)定性,同時還有高的電子發(fā)射密度。本發(fā)明的納米硅/氮化硅薄膜電子源有以下顯著優(yōu)點:(1)制備工藝重復(fù)性好,制備出的電子源的電子發(fā)射的穩(wěn)定性好。(2)采用干法制備工藝,克服了電化學(xué)陽極濕法刻蝕造成的污染,工藝與硅基微電子加工工藝兼容。(3)具有很好的機(jī)械和化學(xué)穩(wěn)定性能。下面進(jìn)一步給出本發(fā)明納米硅/氮化硅薄膜電子源的制作方法的實施例,但僅限于解釋而不是限定。實施例1:參見圖1,該納米硅/氮化硅薄膜電子源的制作過程包括以下步驟:1)采用濺射鎢靶材在基底4上沉積底電極1,其厚度為200nm;2)向鍍膜腔中通入氬氣和氮氣,控制氬氣與氮氣的分壓比為3:1,并使鍍膜腔中總氣壓為0.1Pa,基底4的溫度控制在550℃,以硅靶為濺射源在底電極1上沉積厚度為500nm的富硅氮化硅薄膜;然后,在900℃體積比為25:1的氮氣和氫氣的混合氣中退火120分鐘,使非晶硅轉(zhuǎn)變?yōu)榧{米晶硅22,以形成鑲嵌有納米晶硅22的氮化硅21薄膜,此薄膜即為納米硅/氮化硅層2,硅晶粒22的粒徑為3-6nm,鑲嵌有納米晶硅22的氮化硅21薄膜中相鄰納米晶硅22之間的氮化硅21的厚度為0.5-1.5nm;3)通過濺射金靶在納米硅/氮化硅層2上沉積頂電極層3,其厚度為10nm。實施例2:參見圖1,該納米硅/氮化硅薄膜電子源的制作過程包括以下步驟:1)采用濺射鎳靶材在基底4上沉積底電極1,其厚度為100nm;2)向鍍膜腔中通入氬氣,控制鍍膜腔中氣壓為0.3Pa,基底4的溫度控制在500℃,以硅靶和氮化硅靶為共濺射源在底電極1上沉積厚度為200nm的富硅氮化硅薄膜;然后,在1000℃體積比為30:1的氮氣和氫氣的混合氣中退火90分鐘,使非晶硅轉(zhuǎn)變?yōu)榧{米晶硅22,以形成鑲嵌有納米晶硅22的氮化硅21薄膜,此薄膜即為納米硅/氮化硅層2,硅晶粒22的粒徑為3-6nm,鑲嵌有納米晶硅22的氮化硅21薄膜中相鄰納米晶硅22之間的氮化硅21的厚度為0.5-1.5nm;3)通過濺射鉑靶在納米硅/氮化硅層2上沉積頂電極層3,其厚度為5nm。實施例3:參見圖1,該納米硅/氮化硅薄膜電子源的制作過程包括以下步驟:1)采用濺射鋁靶材在基底4上沉積底電極1,其厚度為50nm;2)向鍍膜腔中通入氬氣,同時控制鍍膜腔中氣壓為2.0Pa,基底4的溫度控制在450℃,以硅和氮化硅復(fù)合靶為濺射源在底電極1上沉積厚度為1000nm的富硅氮化硅薄膜;然后,在1100℃體積比為40:1的氮氣和氫氣的混合氣中退火30分鐘,使非晶硅轉(zhuǎn)變?yōu)榧{米晶硅22,以形成鑲嵌有納米晶硅22的氮化硅21薄膜,此薄膜即為納米硅/氮化硅層2,硅晶粒22的粒徑為3-6nm,鑲嵌有納米晶硅22的氮化硅21薄膜中相鄰納米晶硅22之間的氮化硅21的厚度為0.5-1.5nm;3)通過濺射鉑和銀組成的復(fù)合靶材在納米硅/氮化硅層2上沉積頂電極層3,其厚度為15nm。實施例4:參照圖2所示,該納米硅/氮化硅薄膜電子源的制作過程包括以下步驟:1)采用濺射鎢和鈦組成的復(fù)合靶材在基底4上沉積底電極1,其厚度為120nm;2)以硅靶為濺射源在底電極1上沉積非晶硅/氮化硅交替多層復(fù)合薄膜,在濺射硅靶過程中,向鍍膜腔中交替性地通入氬氣以及同時通入氬氣和氮氣,同時通入氬氣和氮氣時,保持鍍膜腔中氬氣與氮氣的分壓比為1:3,控制鍍膜腔中總氣壓為0.4Pa,每次通入氬氣的時間為2分鐘,每次同時通入氬氣和氮氣的時間為5分鐘,基底4的溫度控制在350℃,在底電極1上沉積厚度為500nm的非晶硅/氮化硅交替多層復(fù)合薄膜;然后,在體積比為20:1的氮氣和氫氣的混合氣體中于950℃對非晶硅/氮化硅交替多層復(fù)合薄膜高溫退火100分鐘,使非晶硅轉(zhuǎn)變?yōu)榧{米晶硅22,以形成由納米晶硅22層與氮化硅21層組成的交替多層薄膜,此薄膜即為納米硅/氮化硅層2,硅晶粒22的粒徑為3-6nm,相鄰納米晶硅22層間的氮化硅21層的厚度為0.5-1.5nm;3)通過濺射銀靶在納米硅/氮化硅層2上沉積頂電極層3,其厚度為10nm。實施例5:參照圖2所示,該納米硅/氮化硅薄膜電子源的制作過程包括以下步驟:1)采用濺射鈦靶在基底4上沉積底電極1,其厚度為180nm;2)向鍍膜腔中通入氬氣,控制鍍膜腔中氣壓為1Pa,基底4的溫度控制在300℃,以硅靶和氮化硅靶為濺射源,交替濺射硅靶和氮化硅靶沉積非晶硅/氮化硅交替多層復(fù)合薄膜,每次濺射硅靶時間為1分鐘,每次濺射氮化硅靶的時間為3分鐘,沉積的非晶硅/氮化硅交替多層復(fù)合薄膜的總厚度為800nm;然后,在體積比為30:1的氮氣和氫氣的混合氣體中于1100℃對非晶硅/氮化硅交替多層復(fù)合薄膜高溫退火30分鐘,使非晶硅轉(zhuǎn)變?yōu)榧{米晶硅22,以形成由納米晶硅22與氮化硅21組成的交替多層薄膜,此薄膜即為納米硅/氮化硅層2,硅晶粒22的粒徑為3-6nm,相鄰納米晶硅22層間的氮化硅21層的厚度為0.5-1.5nm;3)通過濺射鉑靶在納米硅/氮化硅層2上沉積頂電極層3,其厚度為8nm。實施例6:參照圖2所示,該納米硅/氮化硅薄膜電子源的制作過程包括以下步驟:1)采用濺射鎳靶在基底4上沉積底電極1,其厚度為80nm;2)向鍍膜腔中通入氬氣,控制鍍膜腔中氣壓為0.8Pa,基底4的溫度控制在500℃,以硅靶和氮化硅靶為濺射源,交替濺射硅靶和氮化硅靶沉積非晶硅/氮化硅交替多層復(fù)合薄膜,每次濺射硅靶時間為2分鐘,每次濺射氮化硅靶的時間為5分鐘,沉積的非晶硅/氮化硅交替多層復(fù)合薄膜的總厚度為1500nm;然后,在體積比為25:1的氮氣和氫氣的混合氣體中于1100℃對非晶硅/氮化硅交替多層復(fù)合薄膜高溫退火30分鐘,使非晶硅轉(zhuǎn)變?yōu)榧{米晶硅22,以形成由納米晶硅22與氮化硅21組成的交替多層薄膜,此薄膜即為納米硅/氮化硅層2,硅晶粒22的粒徑為3-6nm,相鄰納米晶硅22層間的氮化硅21層的厚度為0.5-1.5nm;3)通過濺射鉑靶在納米硅/氮化硅層2上沉積頂電極層3,其厚度為15nm。圖3所示為納米硅/氮化硅薄膜電子源的電子發(fā)射特性曲線。納米硅/氮化硅薄膜電子源的閾值電壓約為8.5V,并且隨著施加在頂電極3與底電極1間正偏壓Vb的升高,電子源的二級管電流Id(流過頂電極3的電流)和發(fā)射電流Ie均相應(yīng)增加。雖然本發(fā)明以上述較佳的實施例對本發(fā)明進(jìn)行了詳細(xì)的描述,但并非用上述實施例來限定本發(fā)明。本發(fā)明的納米硅/氮化硅薄膜電子源的結(jié)構(gòu)和制作方法不局限于上述幾種方案,只要是按照本發(fā)明的基本構(gòu)思,采用底電極——納米硅/氮化硅層(由納米晶硅和氮化硅組成)——頂電極結(jié)構(gòu)制備薄膜型電子源,均屬于本發(fā)明的保護(hù)范圍。