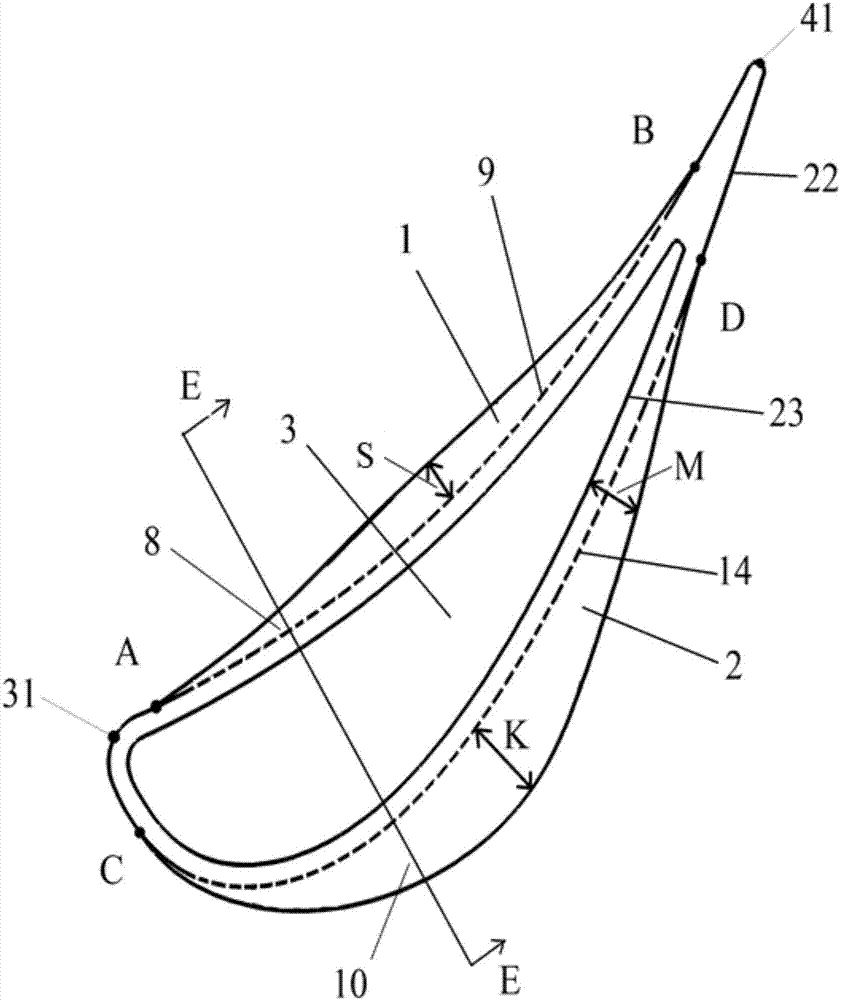
本發(fā)明屬于一種燃?xì)鉁u輪發(fā)動機的渦輪動葉葉片,具體涉及一種渦輪轉(zhuǎn)子葉片葉頂?shù)脑O(shè)計方法、結(jié)構(gòu)和裝置。
背景技術(shù):現(xiàn)代燃?xì)鉁u輪發(fā)動機核心機主要包括三個部件:壓氣機、燃燒室和渦輪。氣流流經(jīng)壓氣機時被壓縮成為高壓氣體,然后在燃燒室內(nèi)和燃油進(jìn)行混合燃燒成為高溫高壓燃?xì)?,這種燃?xì)饬鹘?jīng)渦輪時對渦輪做功,推動渦輪轉(zhuǎn)子旋轉(zhuǎn),而渦輪帶動壓氣機。渦輪轉(zhuǎn)子葉片通常包括前緣、壓力面、吸力面、尾緣和葉頂。在渦輪轉(zhuǎn)子中,為了防止渦輪動葉葉頂和外機匣壁之間發(fā)生摩擦,在它們之間會留有一定間隙。主流通道內(nèi)的流體在壓力面和吸力面壓力梯度力的驅(qū)動下由壓力面?zhèn)攘飨蛭γ鎮(zhèn)龋纬扇~頂泄漏流和相應(yīng)的葉頂泄漏渦。葉頂泄漏流會形成流動損失,同時這部分流體對渦輪轉(zhuǎn)子幾乎不做功,因此降低了渦輪的功率輸出。為了改善燃?xì)鉁u輪發(fā)動機的性能,要降低葉頂泄漏流的不利作用。如果采用傳統(tǒng)的平面,減少葉頂泄漏損失的方法是將葉頂間隙設(shè)計得盡可能小,不過葉頂間隙的最小值受到加工精度等因素的限制,總有一個最小值。另一方面,在一些已知燃?xì)鉁u輪發(fā)動機的渦輪轉(zhuǎn)子中,在發(fā)動機運行期間,該間隙的大小會隨著使用時間的增加而增大,葉尖流動會對發(fā)動機的性能造成更大的不利影響。通過采用特殊設(shè)計的葉頂結(jié)構(gòu)是另外一種用于控制渦輪葉頂流動不利影響的方法,目前已知的一些方法包括采用凹槽和小翼等幾何結(jié)構(gòu),這些方法主要是通過降低葉尖泄漏流的方法。事實上,葉尖附近的流動除了葉尖泄漏渦之外,還有刮削渦和通道渦,其中這些渦系結(jié)構(gòu)都是形成流動損失,降低渦輪效率的原因。高壓渦輪中的流體為高溫的燃?xì)?,造成葉頂?shù)臒岣g和氧化,降低發(fā)動機的壽命,葉尖泄漏渦之外,刮削渦和通道渦均會造成葉頂局部區(qū)域傳熱性能降低。
技術(shù)實現(xiàn)要素:本發(fā)明的目的是提供一種采用葉頂肋翼結(jié)構(gòu)的渦輪葉片,它通過抑制渦系結(jié)構(gòu)的發(fā)展來降低葉頂附近流動摻混的損失,達(dá)到提高渦輪效率,增大渦輪輸出功,并改善渦輪的傳熱性,延長發(fā)動機壽命的目的。抑制渦系結(jié)構(gòu)的發(fā)展也可以降低葉片表面的傳熱,從而達(dá)到改善傳熱性能的目的。本發(fā)明是這樣實現(xiàn)的,一種采用葉頂肋翼結(jié)構(gòu)的渦輪葉片,它包括葉片壓力面?zhèn)刃∫?、葉片吸力面?zhèn)刃∫?,葉片壓力面?zhèn)刃∫砼c葉片吸力面?zhèn)刃∫碇g形成葉頂中部的腔體。所述的壓力面小翼的起始點A接近葉片前緣,終止點B接近葉片尾緣;壓力面起始點A位于吸力面上,距葉片前緣的距離為0%-50%的壓力面長度,壓力面的終止點B位于壓力面上,距葉片尾緣的距離為40%-90%的壓力面長度。壓力面小翼的寬度W為壓力面小翼邊緣到葉片壓力面之間的垂直距離,其取值范圍是0到0.5倍的葉片最大厚度。吸力面小翼起始點C位于葉片吸力面上,距葉片前緣的距離為0%-15%的吸力面長度,吸力面小翼終止點D在位于葉片吸力面,距葉片尾緣的距離為10%-55%的吸力面長度。吸力面小翼厚度K為吸力面小翼邊緣到葉片吸力面之間的垂直距離,從吸力面小翼起始點C開始,到吸力面小翼終止點D為止,葉片厚度K呈先增大后減小的分布,吸力面小翼厚度K具有一個最大厚度,取值范圍是0.1到1倍的葉片最大厚度,吸力面小翼最大厚度的位置距葉片前緣的距離為20%-60%的吸力面長度。葉片頂部具有一個凹槽結(jié)構(gòu),內(nèi)圈型線為葉頂中凹槽的型線,凹槽型線和葉頂外圈型線之間的寬度為M,具體寬度在不同的位置取不同值,最大寬度小于2倍的葉片最大厚度。葉片壓力面9在F點開始,向葉頂壓力面小翼開始過渡。在F點附近采用曲線或直線或曲線直線組合的線段的方式過渡,線段與壓力面小翼葉頂面之間存在一個夾角,夾角可以為尖銳的角或者采用倒角處理。葉頂平面到F點沿展向的距離P不大于葉片弦長的10%;葉片葉頂面和凹槽結(jié)構(gòu)底部的距離T的取值范圍在1%-7%葉片弦長范圍內(nèi)。葉片吸力面從G點開始向吸力面小翼過渡。在G點附近采用曲線或直線或曲線直線組合的線段過渡,該線段和吸力面小翼頂面之間存在一個夾角,該夾角H的范圍為35度-120度;夾角為尖銳的角或者采用倒角處理。內(nèi)圈凹槽型線和外圈小翼輪廓線之間的寬度在不同的位置取不同值,在該截面處,壓力面小翼內(nèi)側(cè)和凹槽底部的夾角為W,W大于90度;壓力面小翼內(nèi)側(cè)面和凹槽底部的夾角為W,W大于70度,在該截面處,吸力面小翼內(nèi)側(cè)面和凹槽底部的夾角為X,夾角X大于70度。本發(fā)明的優(yōu)點:利用了壓力面小翼、吸力面小翼和葉頂中部的腔體組合的葉頂結(jié)構(gòu),來控制葉頂泄漏流的流動。其中壓力面小翼可以用來降低驅(qū)動葉頂間隙進(jìn)口的壓力,并且增大葉頂間隙壓力面進(jìn)口處的分離區(qū),這些作用可以使得驅(qū)動葉頂泄漏流的壓力差降低,并且減小葉頂泄漏流的有效流通通道面積,從而降低葉頂泄漏流;通常情況下,在葉頂間隙吸力側(cè)附近的壓力是較低的,對于葉頂泄漏流來說,較低的壓力會增加葉頂泄漏流的流量。另外,這樣的壓力分布會在機匣附近形成一個由壓力面指向吸力面的壓力梯度,從而驅(qū)動機匣上的邊界層流動發(fā)生分離,形成刮削渦等渦系結(jié)構(gòu)。本發(fā)明中的吸力面小翼利用泄漏流在葉頂間隙出口處和機匣刮削的相互作用來抑制泄漏流動。此時會在葉頂間隙壓力側(cè)出口處出口形成一個局部的高壓區(qū),從而降低驅(qū)動葉頂泄漏流的壓力差,減少了葉頂泄漏流流量。另一方面,這個局部高壓區(qū)會在機匣附近形成從吸力面指向葉片中心通道的壓力梯度,這抑制了端壁邊界層的分離,并減少甚至消除了機匣附近的刮削渦結(jié)構(gòu)。在兩個小翼之間采用凹槽的結(jié)構(gòu),可以利用凹槽中的渦旋結(jié)構(gòu)來進(jìn)一步加強葉頂間隙內(nèi)的流動摻混,從而降低葉頂泄漏流流量。除了在燃?xì)廨啓C中,該渦輪葉頂設(shè)計技術(shù)可以增大渦輪輸出功,提高渦輪效率,因此也能廣泛用于其它各類用于功率輸出的渦輪,比如說動力渦輪等。附圖說明圖1為本發(fā)明所提供的一種采用葉頂肋翼結(jié)構(gòu)的渦輪葉片的葉片和葉頂結(jié)構(gòu)圖;圖2為圖1的俯視示意圖;圖3為本發(fā)明所提供的一種采用葉頂肋翼結(jié)構(gòu)的渦輪葉片的葉片和葉頂?shù)牡湫徒孛鎴D;圖4為小翼間凹槽;圖5為本發(fā)明所提供的一種采用葉頂肋翼結(jié)構(gòu)的渦輪葉片的葉頂結(jié)構(gòu)對葉頂流動作用效果圖中;圖6葉頂間隙中截面(F-F)的流場速度矢量分布、葉型和翼型圖;圖7為采用圓接近的葉片壓力面和吸力面;圖8為在葉頂吸力面出口處泄漏流量沿軸向弦長德分布;圖9為葉片下游沿著展向的流動損失。圖中,1壓力面小翼,2吸力面小翼,3壓力面和吸力面之間的凹槽,14葉片的吸力面,31葉片前緣,41葉片尾緣,W壓力面小翼寬度,A壓力面小翼起始點,B壓力面小翼終止點,C吸力面小翼起始點,D吸力面小翼終止點,9葉片壓力面,K吸力面小翼厚度,22凹槽的型線,23位葉頂外圈型線,F(xiàn)點葉片壓力面到壓力面小翼的過渡點,7葉片壓力面到壓力面小翼的過渡線段,35葉片壓力面到壓力面小翼的過渡線段與壓力面小翼葉頂面之間的夾角,8葉頂平面,P葉頂平面到F點沿展向的距離,T葉頂面到凹槽底部的距離,G葉片吸力面到吸力面小翼的過渡點,11葉片吸力面到吸力面小翼的過渡線段,10吸力面小翼頂面,H葉片壓力面到壓力面小翼的過渡線段與吸力面小翼葉頂面之間的夾角,12壓力面小翼內(nèi)側(cè),13凹槽底部面,W壓力面肋內(nèi)側(cè)和凹槽底部的夾角,36吸力面小翼內(nèi)側(cè)面,X吸力面肋內(nèi)側(cè)和凹槽底部的夾角,39機匣面37吸力面小翼最厚處,38葉頂中截面泄漏流與通道流的交接面,d葉片的厚度。具體實施方式下面結(jié)合附圖和實施例對本發(fā)明進(jìn)行詳細(xì)介紹:如圖1所示,一種新型渦輪動葉葉片的葉頂結(jié)構(gòu),包括葉片壓力面?zhèn)刃∫?、葉片吸力面?zhèn)刃∫?,葉片壓力面?zhèn)刃∫?與葉片吸力面?zhèn)刃∫?之間形成葉頂中部的腔體3。如圖2所示,壓力面小翼1的起始點A接近葉片前緣31,終止點B接近葉片尾緣41;壓力面起始點A位于吸力面上,距葉片前緣31的距離為0%-50%的壓力面長度,壓力面的終止點B位于壓力面上,距葉片尾緣41的距離為40%-90%的壓力面長度。壓力面小翼的寬度W為壓力面小翼邊緣到葉片壓力面9之間的垂直距離,其取值范圍是0到0.5倍的葉片最大厚度。吸力面小翼起始點C位于葉片吸力面上,距葉片前緣31的距離為0%-15%的吸力面長度,吸力面小翼終止點D在位于葉片吸力面,距葉片尾緣41的距離為10%-55%的吸力面長度。吸力面小翼厚度K為吸力面小翼邊緣到葉片吸力面14之間的垂直距離,從吸力面小翼起始點C開始,到吸力面小翼終止點D為止,葉片厚度K呈先增大后減小的分布,吸力面小翼厚度K具有一個最大厚度,取值范圍是0.1到1倍的葉片最大厚度,吸力面小翼最大厚度的位置距葉片前緣31的距離為20%-60%的吸力面長度。葉片頂部具有一個凹槽結(jié)構(gòu)3,內(nèi)圈型線為葉頂中凹槽的型線22,凹槽型線22和葉頂外圈型線23之間的寬度為M,具體寬度在不同的位置取不同值,最大寬度小于2倍的葉片最大厚度。葉片壓力面9在F點開始,向葉頂壓力面小翼開始過渡。在F點附近采用曲線或直線或曲線直線組合的線段7的方式過渡,線段7與壓力面小翼葉頂面之間存在一個夾角35,夾角35可以為尖銳的角,也可以采用倒角處理。葉頂平面8到F點沿展向的距離P不大于葉片弦長的10%;葉片葉頂面8和凹槽結(jié)構(gòu)底部的距離T的取值范圍在1%-7%葉片弦長范圍內(nèi)。葉片吸力面14從G點開始向吸力面小翼過渡。在G點附近采用曲線或直線或曲線直線組合的線段過渡11,該線段11和吸力面小翼頂面10之間存在一個夾角H,該夾角H的范圍為35度-120度;夾角H可以為尖銳的角,也可以采用倒角處理。內(nèi)圈凹槽型線22和外圈小翼輪廓線23之間的寬度在不同的位置取不同值,在該截面處,壓力面小翼內(nèi)側(cè)12和凹槽底部13的夾角為W,W大于90度;壓力面小翼內(nèi)側(cè)面12和凹槽底部13的夾角為W,W大于70度,在該截面處,吸力面小翼內(nèi)側(cè)面36和凹槽底部13的夾角為X,夾角X大于70度。圖6是采用仿真方法所獲得的葉片葉頂中截面圖5中的F-F截面的速度,在該截面上的二維速度矢量分布。從速度矢量圖中可以看出泄漏流和主流的交接面38,葉頂吸力面小翼的設(shè)計在葉片通道的設(shè)計根據(jù)該流動交接面的具體特性來確定,從葉片前緣點開始20-60%的部分,吸力面小翼不再跟隨交接面38,向葉片吸力面靠攏。吸力面小翼最大厚度的位置距葉片前緣31的距離為20%-60%的吸力面長度,具體取決于葉片負(fù)載等情況。圖7是不采用小翼設(shè)計的葉頂,采用圓接近的葉片壓力面和吸力面的直徑為d,定義為葉片的當(dāng)?shù)睾穸?。圖8是在葉頂吸力面出口處泄漏流量沿軸向弦長德分布,可以看出采用本發(fā)明小翼葉頂?shù)男孤┝髁?6小于不采用小翼設(shè)計的葉頂?shù)男孤┝髁?5的葉頂,該效果在葉片通道前部尤其明顯。圖9是葉片下游沿著展向的流動損失,不采用葉頂小翼時的泄漏渦損失55大于本發(fā)明中葉頂設(shè)計的泄漏渦損失56,不采用葉頂小翼時的二次渦和刮削渦損失53大于本專利中葉頂設(shè)計的二次渦和刮削渦損失54,可見本設(shè)計降低了流動損失提高了效率。利用數(shù)值模擬方法,對該種帶壓力面和吸力面小翼葉頂?shù)臏u輪葉片做了流場分析,發(fā)現(xiàn)這種采用腔體和小翼結(jié)合的葉頂都能夠帶來葉片氣動和傳熱性能上的提升。首先是葉頂泄漏流的質(zhì)量流量減少了,這使得流動通道內(nèi)的流場更為均勻,從而降低了氣動損失,提高了渦輪效率,并提高了渦輪輸出功,從而提高了發(fā)動機的功率。采用了葉頂這種新型葉頂之后,葉頂區(qū)域的換熱系數(shù)也降低了,這改善了渦輪的傳熱性能,可以達(dá)到延長了渦輪的壽命的目的。