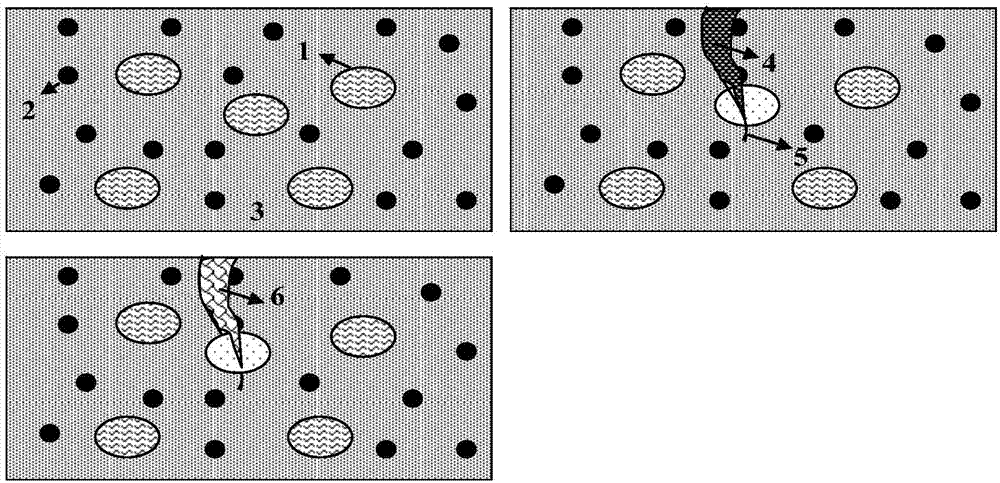
本發(fā)明屬于功能高分子復(fù)合材料制備
技術(shù)領(lǐng)域:
,尤其涉及一種微膠囊自修復(fù)碳纖維復(fù)合材料汽車件及其制備方法。
背景技術(shù):
:碳纖維復(fù)合材料具有比強(qiáng)度和比模量高、質(zhì)輕、耐腐蝕、耐疲勞、熱膨脹系數(shù)小等優(yōu)異的特點(diǎn)而使其在汽車工業(yè)中得到應(yīng)用。但是,碳纖維復(fù)合材料在使用過程中及周圍環(huán)境溫度、濕度等因素作用下,不可避免地會(huì)產(chǎn)生局部損傷和微裂紋,導(dǎo)致力學(xué)性能下降或功能喪失。肉眼能發(fā)現(xiàn)的分層或由沖擊所導(dǎo)致的宏觀裂紋可通過手工修復(fù),而樹脂基體裂紋往往在本體深處出現(xiàn),如基體微開裂等微觀范圍的損傷就很難被發(fā)現(xiàn)。如果當(dāng)材料發(fā)生破壞時(shí)會(huì)有膠粘劑隨之釋放出來,將材料微裂紋粘合在一起,阻止材料進(jìn)一步破壞和力學(xué)性能下降,這樣可解決復(fù)合材料修復(fù)問題。鑒于此,高分子自修復(fù)材料隨之誕生,其自修復(fù)功能是通過在樹脂基體中埋植含有修復(fù)劑的微膠囊來實(shí)現(xiàn),在外力作用下,裂紋附近的微膠囊破裂,在毛細(xì)管力作用下修復(fù)劑迅速滲透微裂紋,在催化劑或固化劑作用下發(fā)生聚合反應(yīng),將裂紋粘接在一起,從而實(shí)現(xiàn)復(fù)合材料修復(fù)。發(fā)明專利cn104877309a公開了一種基于表面改性微膠囊化的自修復(fù)復(fù)合材料及其制備方法,該方法分別將環(huán)氧樹脂和固化劑微膠囊化并埋植于復(fù)合材料樹脂基體中,其微膠囊囊壁材料為脲醛樹脂或密胺樹脂,氣味較大,存在游離甲醛,不適于汽車件氣味性要求;發(fā)明專利cn103694635a公開了一種基于微膠囊化的環(huán)氧樹脂及超強(qiáng)酸固化劑的室溫快速自修復(fù)復(fù)合材料,固化劑與環(huán)氧樹脂分別進(jìn)行微膠囊化,制備工藝需要采用-80℃超低溫環(huán)境,工藝復(fù)雜,難以實(shí)現(xiàn)應(yīng)用,且所采用超強(qiáng)酸五氟化砷等具有毒性,對(duì)人身健康及環(huán)境不利。技術(shù)實(shí)現(xiàn)要素:為解決上述技術(shù)問題,本發(fā)明提供了一種自修復(fù)碳纖維復(fù)合材料件及其制備方法,結(jié)合脲醛樹脂和三聚氰胺甲醛樹脂的優(yōu)點(diǎn),采用脲、三聚氰胺、甲醛混合制備改性脲醛樹脂微膠囊體系,得到耐候、耐水性好,安全環(huán)保、修復(fù)率高的微膠囊自修復(fù)體系。本發(fā)明采取的技術(shù)方案為:一種自修復(fù)碳纖維復(fù)合材料件的制備方法,所述制備方法包括以下步驟:(1)制備微膠囊;(2)將微膠囊分散于環(huán)氧樹脂中,并加入潛伏性固化劑或催化劑,50~60℃加熱反應(yīng)30~60分鐘,再加入環(huán)氧樹脂固化劑,攪拌均勻,得到混合樹脂;(3)將步驟(2)得到的混合樹脂固化即可制得自修復(fù)碳纖維復(fù)合材料件。所述微膠囊的制備方法為:(1-1)將脲、三聚氰胺、甲醛按照質(zhì)量比1.67~2.86:1:8.37~10.94攪拌混合均勻,在堿性條件下加熱反應(yīng)1~2小時(shí),加入混合溶液質(zhì)量的0.81~4.4倍的水稀釋,得到溶液一;(1-2)將囊芯和水按照質(zhì)量比1:4~6的比例混合,得到混合溶液,然后加入乳化劑攪拌混合,乳化1~2小時(shí),乳化后加入消泡劑,靜置10~50分鐘,得到溶液二;(1-3)將溶液一與溶液二混合,其中溶液一與溶液二的質(zhì)量比為0.66~0.93:1,室溫下攪拌混合均勻,然后加入稀酸調(diào)節(jié)溶液ph值為3.5~5.0,升溫至45~60℃攪拌反應(yīng)1.5~3小時(shí),得到溶液三;(1-4)將溶液三分離,洗滌,干燥,得到微膠囊。所述步驟(1-1)中:所述甲醛為質(zhì)量百分比為37%的甲醛水溶液;所述攪拌采用磁力攪拌,其轉(zhuǎn)速為300~1200轉(zhuǎn)/分鐘,攪拌時(shí)間為5~15分鐘;所述堿性條件為ph值8~9,采用三乙醇胺或1~10wt%的na2co3溶液或naoh溶液進(jìn)行ph值調(diào)節(jié);所述加熱反應(yīng)的條件為:先以1.5~3℃/分鐘的速度緩慢加熱至65℃~85℃,并在恒定溫度65℃~85℃下加熱1~2小時(shí);所述水為去離子水或蒸餾水。所述步驟(1-2)中:所述囊芯為苯乙烯、環(huán)氧樹脂或雙環(huán)戊二烯;所述乳化劑的重量是混合溶液重量的0.5~1.5%;所述乳化劑為十二烷基苯磺酸鈉、十二烷基硫酸鈉、span-80、tween-80、op-10、阿拉伯樹膠、苯乙烯馬來酸酐共聚物中的一種或兩種及以上的混合物,優(yōu)選為十二烷基苯磺酸鈉、span-80、tween-80和阿拉伯樹膠。所述消泡劑的重量是混合溶液重量的0.01~0.10%;所述消泡劑為高碳醇類消泡劑,優(yōu)選c7~c9的醇,如正辛醇、異辛醇;所述溶液二為水包油型乳化液;所述水為去離子水或蒸餾水;所述攪拌為磁力攪拌或無級(jí)電機(jī)帶動(dòng)攪拌,攪拌速度300~600轉(zhuǎn)/分鐘。所述步驟(1-3)中:所述攪拌的速度為300~600轉(zhuǎn)/分鐘;所述稀酸為濃度為5~10%的鹽酸溶液或硫酸溶液;所述升溫是指升溫速率為1.5~3℃/分鐘。所述步驟(1-4)中:所述微膠囊的粒徑為20~220μm;所述分離是指離心分離、過濾常規(guī)分離方法;所述洗滌所用溶劑為去離子水、蒸餾水、乙醇、丙酮中的一種或幾種;所述干燥為50~60℃烘箱干燥、50~60℃真空干燥箱干燥,或者冷凍干燥機(jī)干燥,干燥時(shí)間30~90分鐘。所述步驟(2)中,所述微膠囊的重量為環(huán)氧樹脂重量的1~6%;所述潛伏性固化劑的重量為環(huán)氧樹脂重量的1~4%;所述催化劑的重量為環(huán)氧樹脂重量的6~15%;所述環(huán)氧樹脂固化劑的重量為微膠囊、環(huán)氧樹脂和潛伏性固化劑三者重量之和的10~40%,或者,所述環(huán)氧樹脂固化劑的重量為微膠囊、環(huán)氧樹脂和催化劑三者重量之和的10~40%。所述環(huán)氧樹脂為5222環(huán)氧樹脂、3234環(huán)氧樹脂、5224環(huán)氧樹脂和5228環(huán)氧樹脂中的一種。所述環(huán)氧樹脂固化劑為脂肪胺類、芳香胺類、改性胺類和酸酐類固化劑中的一種。所述脂肪胺類固化劑優(yōu)選為二乙撐三胺或三乙撐四胺;所述芳香胺類固化劑優(yōu)選為苯二甲胺、間苯二甲胺或二氨基二苯基甲烷;所述改性胺類固化劑優(yōu)選為120固化劑、593固化劑或703固化劑;所述酸酐類固化劑優(yōu)選為順丁烯二酸酐、鄰苯二甲酸酐或十二烯基琥珀酸酐。所述潛伏性固化劑為咪唑類衍生物、三氯化硼-單乙胺絡(luò)合物、雙氰胺、癸二酸二酰肼中的一種;所述催化劑為苯基亞甲基雙(三環(huán)己基磷)二氯化釕。所述步驟(3)中,固化的溫度為80~120℃,固化時(shí)間為1~3小時(shí)。所述步驟(3)進(jìn)一步包括,用潔模溶劑清潔模具面,潔模后擦涂脫模劑,除去多余的脫模劑后按照一定的鋪層角度鋪疊碳布,然后合模,注入步驟(2)得到的產(chǎn)物,在80~120℃下加熱1~3小時(shí)固化,固化后得到具有自修復(fù)功能的碳纖維復(fù)合材料件。所述潔模溶劑為無水乙醇、丙酮、乙醚等有機(jī)溶劑中的一種或兩種及以上;所用脫模劑為脫模蠟。本發(fā)明還提供了一種根據(jù)上述制備方法制備得到的自修復(fù)碳纖維復(fù)合材料件。本發(fā)明采用改性脲醛樹脂為囊壁,以苯乙烯、環(huán)氧樹脂、雙環(huán)戊二烯為芯材,制備平均粒徑為20~220μm的微膠囊,將微膠囊和催化劑或潛伏性固化劑分散于熱固性樹脂基體中,采用該分散有微膠囊和催化劑或潛伏性固化劑的樹脂制備碳纖維復(fù)合材料件。采用該方法制備的碳纖維復(fù)合材料件具有可自動(dòng)修復(fù)樹脂基體微裂紋功效,無需傳統(tǒng)的復(fù)雜修復(fù)工藝,可室溫下自動(dòng)修復(fù)。相對(duì)于現(xiàn)有技術(shù),本發(fā)明具備以下優(yōu)點(diǎn):本發(fā)明采用苯乙烯、環(huán)氧樹脂或雙環(huán)戊二烯為囊芯,將囊芯和固化劑或催化劑埋植于碳纖維復(fù)合材料樹脂基體中,得到可室溫下具有自修復(fù)能力的復(fù)合材料件。當(dāng)該復(fù)合材料件受到損傷出現(xiàn)微裂紋時(shí),微膠囊破裂并釋放出囊芯修復(fù)材料,囊芯修復(fù)材料在毛細(xì)管力作用下快速滲透微裂紋,并與固化劑或催化劑接觸,進(jìn)而觸發(fā)聚合反應(yīng),囊芯修復(fù)材料在微裂紋處形成高度交聯(lián)的聚合物,實(shí)現(xiàn)微裂紋修復(fù),修復(fù)率在70%以上。附圖說明圖1自修復(fù)碳纖維復(fù)合材料件制備流程;圖2自修復(fù)碳纖維復(fù)合材料件的自修復(fù)示意圖,1-微膠囊;2-潛伏性固化劑或催化劑;3-樹脂基體;4-芯材;5-微裂紋;6-修復(fù)后的高度交聯(lián)樹脂。具體實(shí)施方式下面結(jié)合實(shí)施例1~6對(duì)本發(fā)明進(jìn)行詳細(xì)說明。本發(fā)明所用的各原料的型號(hào)及生產(chǎn)廠家如表1所示。表1原料及生產(chǎn)廠家實(shí)施例1一種自修復(fù)碳纖維復(fù)合材料件的制備方法,包括以下步驟:(1)制備微膠囊(1-1)將脲、三聚氰胺和甲醛按照質(zhì)量比1.67:1:9.65混合,得到混合溶液,然后采用磁力攪拌在1200轉(zhuǎn)/分鐘下攪拌5分鐘,攪拌后,向溶液中滴加三乙醇胺,控制溶液ph值在8.3,然后以1.5℃/分鐘的加熱速率緩慢加熱,并在恒定溫度65℃加熱2小時(shí),然后向其中加入去離子水進(jìn)行稀釋,去離子水加入量為混合溶液質(zhì)量的0.81倍,冷卻至室溫后得到溶液一;(1-2)將苯乙烯、去離子水按照1:4的比例混合成混合液,然后加入0.5%混合液重量的十二烷基苯磺酸鈉,在300轉(zhuǎn)/分鐘的攪拌速度下攪拌1.5小時(shí),然后加入占混合溶液總重量百分比為0.015%的正辛醇消泡,靜置10分鐘后得到溶液二;(1-3)將上述溶液一和溶液二按照質(zhì)量比0.66:1混合,并在室溫下以300轉(zhuǎn)/分鐘的轉(zhuǎn)速攪拌,攪拌均勻后,加入5wt%的硫酸調(diào)節(jié)溶液ph值至5.0,然后在持續(xù)攪拌的情況下,以1.5℃/分鐘的升溫速率緩慢升溫至50℃,并在此溫度下持續(xù)反應(yīng)3小時(shí),得到溶液三;(1-4)將溶液三離心分離、丙酮洗滌后再次離心分離,分離產(chǎn)物在50℃烘箱中干燥60分鐘,得到平均粒徑為120μm的微膠囊;(2)將所得微膠囊加入碳纖維復(fù)合材料制備所用的5222環(huán)氧樹脂中,分散均勻,然后加入苯基亞甲基雙(三環(huán)己基磷)二氯化釕,分散均勻,得到混合物;所述微膠囊的重量為環(huán)氧樹脂重量的1%;苯基亞甲基雙(三環(huán)己基磷)二氯化釕的重量為環(huán)氧樹脂重量的6%;然后將該混合物在50℃下加熱60分鐘,再加入二乙撐三胺,混合物與二乙撐三胺的質(zhì)量比為100:11,攪拌均勻;(3)分別用無水乙醇和丙酮對(duì)模具面進(jìn)行清潔,待溶劑完全揮發(fā)后涂脫模蠟,并用無紡布將多余脫模蠟擦去,然后將裁剪好的碳布按照設(shè)計(jì)的鋪層方式[(±45)/(±45)/(±45)/(±45)]進(jìn)行鋪疊,合模,然后將步驟(2)得到的產(chǎn)物注入模具中,在100℃下加熱1小時(shí)固化,固化后,按照gb/t1451-2005《纖維增強(qiáng)塑料簡支梁式?jīng)_擊韌性試驗(yàn)方法》中規(guī)定的方法進(jìn)行制樣和沖擊韌性測試,沖擊后得到空白樣的沖擊韌性,然后將沖擊后的試樣夾緊固定,室溫下放置24小時(shí)后再次進(jìn)行沖擊試驗(yàn),得到的沖擊韌性與空白樣沖擊韌性的比值為修復(fù)率。本實(shí)施例所得自修復(fù)復(fù)合材料的自修復(fù)率達(dá)到78%。實(shí)施例2一種自修復(fù)碳纖維復(fù)合材料件的制備方法,包括以下步驟:(1)制備微膠囊(1-1)將脲、三聚氰胺和甲醛按照質(zhì)量比1.90:1:8.37混合,得到混合溶液,然后采用磁力攪拌在1000轉(zhuǎn)/分鐘下攪拌8分鐘,攪拌后,向溶液中滴加1wt%naoh溶液,控制溶液ph值在8.0,然后以2℃/分鐘的加熱速率緩慢加熱,并在恒定溫度70℃加熱2小時(shí),然后向其中加入去離子水進(jìn)行稀釋,去離子水加入量為混合溶液質(zhì)量的1倍,冷卻至室溫后得到溶液一;(1-2)將苯乙烯、去離子水按照1:4的比例混合成混合液,然后加入1.0%混合液重量的span-80,在500轉(zhuǎn)/分鐘的攪拌速度下攪拌1.5小時(shí),然后加入占混合溶液總重量百分比為0.01%的正辛醇消泡,靜置30分鐘后得到溶液二;(1-3)將上述溶液一和溶液二按照質(zhì)量比0.8:1混合,并在室溫下以500轉(zhuǎn)/分鐘的轉(zhuǎn)速攪拌,攪拌均勻后,加入10wt%的硫酸調(diào)節(jié)溶液ph值至5.0,然后在持續(xù)攪拌的情況下,以2℃/分鐘的升溫速率緩慢升溫至60℃,并在此溫度下持續(xù)反應(yīng)2.5小時(shí),得到溶液三;(1-4)將溶液三離心分離、分別用乙醇和丙酮洗滌后再次離心分離,分離產(chǎn)物在60℃烘箱中干燥40分鐘,得到平均粒徑為145μm的微膠囊;(2)將所得微膠囊加入碳纖維復(fù)合材料制備所用的3234環(huán)氧樹脂中,分散均勻,然后加入苯基亞甲基雙(三環(huán)己基磷)二氯化釕,分散均勻,得到混合物;所述微膠囊的重量為環(huán)氧樹脂重量的2%;苯基亞甲基雙(三環(huán)己基磷)二氯化釕的重量為環(huán)氧樹脂重量的10%;然后將該混合物在60℃下加熱30分鐘,再加入間苯二甲胺,混合物與間苯二甲胺的質(zhì)量比為100:15,攪拌均勻;(3)用丙酮對(duì)模具面進(jìn)行清潔,待溶劑完全揮發(fā)后涂脫模蠟,并用無紡布將多余脫模蠟擦去,然后將裁剪好的碳布按照設(shè)計(jì)的鋪層方式[(±45)/(±45)/(±45)/(±45)]進(jìn)行鋪疊,合模,然后將步驟(2)得到的產(chǎn)物注入模具中,在120℃下加熱3小時(shí)固化,固化后,按照gb/t1451-2005《纖維增強(qiáng)塑料簡支梁式?jīng)_擊韌性試驗(yàn)方法》中規(guī)定的方法進(jìn)行制樣和沖擊韌性測試,沖擊后得到空白樣的沖擊韌性,然后將沖擊后的試樣夾緊固定,室溫下放置24小時(shí)后再次進(jìn)行沖擊試驗(yàn),得到的沖擊韌性與空白樣沖擊韌性的比值為修復(fù)率。本實(shí)施例所得自修復(fù)復(fù)合材料的自修復(fù)率達(dá)到85%。實(shí)施例3一種自修復(fù)碳纖維復(fù)合材料件的制備方法,包括以下步驟:(1)制備微膠囊(1-1)將脲、三聚氰胺和甲醛按照質(zhì)量比2.38:1:8.37混合,得到混合溶液,然后采用磁力攪拌在800轉(zhuǎn)/分鐘下攪拌10分鐘,攪拌后,向溶液中滴加10wt%na2co3溶液,控制溶液ph值在9,然后以3℃/分鐘的加熱速率緩慢加熱,并在恒定溫度70℃加熱1小時(shí),然后向其中加入去離子水進(jìn)行稀釋,去離子水加入量為混合溶液質(zhì)量的2倍,冷卻至室溫后得到溶液一;(1-2)將雙環(huán)戊二烯、去離子水按照1:5的比例混合成混合液,然后加入1.0%混合液重量的阿拉伯樹膠與tween-80的混合乳化劑,阿拉伯樹膠與tween-80質(zhì)量比為3:1,在450轉(zhuǎn)/分鐘的攪拌速度下攪拌1.5小時(shí),然后加入占混合溶液總重量百分比為0.03%的正辛醇消泡,靜置30分鐘后得到溶液二;(1-3)將上述溶液一和溶液二按照質(zhì)量比0.93:1混合,并在室溫下以500轉(zhuǎn)/分鐘的轉(zhuǎn)速攪拌,攪拌均勻后,加入8wt%的硫酸調(diào)節(jié)溶液ph值至5.0,然后在持續(xù)攪拌的情況下,以2℃/分鐘的升溫速率緩慢升溫至60℃,并在此溫度下持續(xù)反應(yīng)2.5小時(shí),得到溶液三;(1-4)將溶液三離心分離、用丙酮洗滌后再次離心分離,分離產(chǎn)物在50℃真空干燥烘箱中干燥30分鐘,得到平均粒徑為195μm的微膠囊;(2)將所得微膠囊加入碳纖維復(fù)合材料制備所用的5224環(huán)氧樹脂中,分散均勻,然后加入苯基亞甲基雙(三環(huán)己基磷)二氯化釕,分散均勻,得到混合物;所述微膠囊的重量為環(huán)氧樹脂重量的1.8%;苯基亞甲基雙(三環(huán)己基磷)二氯化釕的重量為環(huán)氧樹脂重量的15%;然后將該混合物在50℃下加熱50分鐘,再加入793固化劑,混合物與793固化劑的質(zhì)量比為100:30,攪拌均勻;(3)用丙酮對(duì)模具面進(jìn)行清潔,待溶劑完全揮發(fā)后涂脫模蠟,并用無紡布將多余脫模蠟擦去,然后將裁剪好的碳布按照設(shè)計(jì)的鋪層方式[(±45)/(±45)/(±45)/(±45)]進(jìn)行鋪疊,合模,然后將步驟(2)得到的產(chǎn)物注入模具中,在90℃下加熱3小時(shí)固化,固化后,按照gb/t1451-2005《纖維增強(qiáng)塑料簡支梁式?jīng)_擊韌性試驗(yàn)方法》中規(guī)定的方法進(jìn)行制樣和沖擊韌性測試,沖擊后得到空白樣的沖擊韌性,然后將沖擊后的試樣夾緊固定,室溫下放置24小時(shí)后再次進(jìn)行沖擊試驗(yàn),得到的沖擊韌性與空白樣沖擊韌性的比值為修復(fù)率。本實(shí)施例所得自修復(fù)復(fù)合材料的自修復(fù)率達(dá)到89%。實(shí)施例4一種自修復(fù)碳纖維復(fù)合材料件的制備方法,包括以下步驟:(1)制備微膠囊(1-1)將脲、三聚氰胺和甲醛按照質(zhì)量比2.38:1:10.94混合,得到混合溶液,然后采用磁力攪拌在300轉(zhuǎn)/分鐘下攪拌15分鐘,攪拌后,向溶液中滴加三乙醇胺,控制溶液ph值在8.3,然后以2.5℃/分鐘的加熱速率緩慢加熱,并在恒定溫度75℃加熱1.5小時(shí),然后向其中加入蒸餾水進(jìn)行稀釋,蒸餾水加入量為混合溶液質(zhì)量的3倍,冷卻至室溫后得到溶液一;(1-2)將e-51環(huán)氧樹脂、去離子水按照1:6的比例混合成混合液,然后加入0.5%混合液重量的阿拉伯樹膠與span-80的混合乳化劑,阿拉伯樹膠與span-80質(zhì)量比為2.5:1,在500轉(zhuǎn)/分鐘的攪拌速度下攪拌1.5小時(shí),然后加入占混合溶液總重量百分比為0.05%的異辛醇消泡,靜置30分鐘后得到溶液二;(1-3)將上述溶液一和溶液二按照質(zhì)量比0.93:1混合,并在室溫下以500轉(zhuǎn)/分鐘的轉(zhuǎn)速攪拌,攪拌均勻后,加入8wt%的鹽酸調(diào)節(jié)溶液ph值至4.2,然后在持續(xù)攪拌的情況下,以2.5℃/分鐘的升溫速率緩慢升溫至50℃,并在此溫度下持續(xù)反應(yīng)2.5小時(shí),得到溶液三;(1-4)將溶液三離心分離、用丙酮洗滌后再次離心分離,分離產(chǎn)物在50℃真空干燥烘箱中干燥30分鐘,得到平均粒徑為20μm的微膠囊;(2)將所得微膠囊加入碳纖維復(fù)合材料制備所用的5228環(huán)氧樹脂中,分散均勻,然后加入咪唑類衍生物2mz-azine,分散均勻,得到混合物;所述微膠囊的重量為環(huán)氧樹脂重量的1.5%;咪唑類衍生物2mz-azine的重量為環(huán)氧樹脂重量的4%;然后將該混合物在50℃下加熱40分鐘,再加入793固化劑,混合物與793固化劑的質(zhì)量比為100:30,攪拌均勻;(3)用丙酮對(duì)模具面進(jìn)行清潔,待溶劑完全揮發(fā)后涂脫模蠟,并用無紡布將多余脫模蠟擦去,然后將裁剪好的碳布按照設(shè)計(jì)的鋪層方式[(±45)/(±45)/(±45)/(±45)]進(jìn)行鋪疊,合模,然后將步驟(2)得到的產(chǎn)物注入模具中,在90℃下加熱3小時(shí)固化,固化后,按照gb/t1451-2005《纖維增強(qiáng)塑料簡支梁式?jīng)_擊韌性試驗(yàn)方法》中規(guī)定的方法進(jìn)行制樣和沖擊韌性測試,沖擊后得到空白樣的沖擊韌性,然后將沖擊后的試樣夾緊固定,室溫下放置24小時(shí)后再次進(jìn)行沖擊試驗(yàn),得到的沖擊韌性與空白樣沖擊韌性的比值為修復(fù)率。本實(shí)施例所得自修復(fù)復(fù)合材料的自修復(fù)率達(dá)到85%。實(shí)施例5一種自修復(fù)碳纖維復(fù)合材料件的制備方法,包括以下步驟:(1)制備微膠囊(1-1)將脲、三聚氰胺和甲醛按照質(zhì)量比2.86:1:8.37混合,得到混合溶液,然后采用磁力攪拌在400轉(zhuǎn)/分鐘下攪拌15分鐘,攪拌后,向溶液中滴加三乙醇胺,控制溶液ph值在8.6,然后以2.0℃/分鐘的加熱速率緩慢加熱,并在恒定溫度85℃加熱1.0小時(shí),然后向其中加入蒸餾水進(jìn)行稀釋,蒸餾水加入量為混合溶液質(zhì)量的2.5倍,冷卻至室溫后得到溶液一;(1-2)將5222環(huán)氧樹脂、去離子水按照1:4的比例混合成混合液,然后加入1.3%混合液重量的阿拉伯樹膠與十二烷基苯磺酸鈉的混合乳化劑,阿拉伯樹膠與十二烷基苯磺酸鈉的質(zhì)量比為2.5:1,在500轉(zhuǎn)/分鐘的攪拌速度下攪拌1.5小時(shí),然后加入占混合溶液總重量百分比為0.08%的異辛醇消泡,靜置30分鐘后得到溶液二;(1-3)將上述溶液一和溶液二按照質(zhì)量比0.85:1混合,并在室溫下以500轉(zhuǎn)/分鐘的轉(zhuǎn)速攪拌,攪拌均勻后,加入7wt%的鹽酸調(diào)節(jié)溶液ph值至4.2,然后在持續(xù)攪拌的情況下,以2.0℃/分鐘的升溫速率緩慢升溫至50℃,并在此溫度下持續(xù)反應(yīng)2.5小時(shí),得到溶液三;(1-4)將溶液三離心分離、用丙酮洗滌后再次離心分離,分離產(chǎn)物在50℃真空干燥烘箱中干燥30分鐘,得到平均粒徑為75μm的微膠囊;(2)將所得微膠囊加入碳纖維復(fù)合材料制備所用的5222環(huán)氧樹脂中,分散均勻,然后加入咪唑類衍生物2mz-azine,分散均勻,得到混合物;所述微膠囊的重量為環(huán)氧樹脂重量的1.0%;咪唑類衍生物2mz-azine的重量為環(huán)氧樹脂重量的4%;然后將該混合物在50℃下加熱40分鐘,再加入591固化劑,混合物與591固化劑的質(zhì)量比為100:25,攪拌均勻;(3)用丙酮對(duì)模具面進(jìn)行清潔,待溶劑完全揮發(fā)后涂脫模蠟,并用無紡布將多余脫模蠟擦去,然后將裁剪好的碳布按照設(shè)計(jì)的鋪層方式[(±45)/(±45)/(±45)/(±45)]進(jìn)行鋪疊,合模,然后將步驟(2)得到的產(chǎn)物注入模具中,在100℃下加熱2.5小時(shí)固化,固化后,按照gb/t1451-2005《纖維增強(qiáng)塑料簡支梁式?jīng)_擊韌性試驗(yàn)方法》中規(guī)定的方法進(jìn)行制樣和沖擊韌性測試,沖擊后得到空白樣的沖擊韌性,然后將沖擊后的試樣夾緊固定,室溫下放置24小時(shí)后再次進(jìn)行沖擊試驗(yàn),得到的沖擊韌性與空白樣沖擊韌性的比值為修復(fù)率。本實(shí)施例所得自修復(fù)復(fù)合材料的自修復(fù)率達(dá)到82%。實(shí)施例6一種自修復(fù)碳纖維復(fù)合材料件的制備方法,包括以下步驟:(1)制備微膠囊(1-1)將脲、三聚氰胺和甲醛按照質(zhì)量比2.86:1:10.94混合,得到混合溶液,然后采用磁力攪拌在400轉(zhuǎn)/分鐘下攪拌15分鐘,攪拌后,向溶液中滴加三乙醇胺,控制溶液ph值在8.1,然后以1.5℃/分鐘的加熱速率緩慢加熱,并在恒定溫度80℃加熱1.0小時(shí),然后向其中加入去離子水進(jìn)行稀釋,蒸餾水加入量為混合溶液質(zhì)量的1.5倍,冷卻至室溫后得到溶液一;(1-2)將5228環(huán)氧樹脂、去離子水按照1:4的比例混合成混合液,然后加入0.8%混合液重量的阿拉伯樹膠與op-10的混合乳化劑,阿拉伯樹膠與op-10的質(zhì)量比為1:1,在500轉(zhuǎn)/分鐘的攪拌速度下攪拌1.5小時(shí),然后加入占混合溶液總重量百分比為0.10%的異辛醇消泡,靜置30分鐘后得到溶液二;(1-3)將上述溶液一和溶液二按照質(zhì)量比0.85:1混合,并在室溫下以500轉(zhuǎn)/分鐘的轉(zhuǎn)速攪拌,攪拌均勻后,加入10wt%的鹽酸調(diào)節(jié)溶液ph值至4.2,然后在持續(xù)攪拌的情況下,以2.0℃/分鐘的升溫速率緩慢升溫至50℃,并在此溫度下持續(xù)反應(yīng)2.5小時(shí),得到溶液三;(1-4)將溶液三離心分離、用丙酮洗滌后再次離心分離,分離產(chǎn)物在50℃真空干燥烘箱中干燥30分鐘,得到平均粒徑為220μm的微膠囊;(2)將所得微膠囊加入碳纖維復(fù)合材料制備所用的5222環(huán)氧樹脂中,分散均勻,然后加入三氯化硼-單乙胺絡(luò)合物,分散均勻,得到混合物;所述微膠囊的重量為環(huán)氧樹脂重量的1.0%;三氯化硼-單乙胺絡(luò)合物重量為環(huán)氧樹脂重量的4%;然后將該混合物在50℃下加熱40分鐘,再加入591固化劑,混合物與591固化劑的質(zhì)量比為100:25,攪拌均勻;(3)用丙酮對(duì)模具面進(jìn)行清潔,待溶劑完全揮發(fā)后涂脫模蠟,并用無紡布將多余脫模蠟擦去,然后將裁剪好的碳布按照設(shè)計(jì)的鋪層方式[(±45)/(±45)/(±45)/(±45)]進(jìn)行鋪疊,合模,然后將步驟(2)得到的產(chǎn)物注入模具中,在100℃下加熱2.5小時(shí)固化,固化后,按照gb/t1451-2005《纖維增強(qiáng)塑料簡支梁式?jīng)_擊韌性試驗(yàn)方法》中規(guī)定的方法進(jìn)行制樣和沖擊韌性測試,沖擊后得到空白樣的沖擊韌性,然后將沖擊后的試樣夾緊固定,室溫下放置24小時(shí)后再次進(jìn)行沖擊試驗(yàn),得到的沖擊韌性與空白樣沖擊韌性的比值為修復(fù)率。本實(shí)施例所得自修復(fù)復(fù)合材料的自修復(fù)率達(dá)到88%。以上各實(shí)施例得到的自修復(fù)碳纖維復(fù)合材料件的性能測試結(jié)果如表2所示表2修復(fù)前后沖擊韌性及修復(fù)率實(shí)施例空白樣沖擊韌性kj/m2修復(fù)后沖擊韌性kj/m2修復(fù)率%實(shí)施例1212.700165.17978實(shí)施例2215.035182.12485實(shí)施例3230.696204.22289實(shí)施例4216.666184.19285實(shí)施例5213.255175.66282實(shí)施例6214.143187.39288上述參照實(shí)施例對(duì)自修復(fù)碳纖維復(fù)合材料件及其制備方法進(jìn)行的詳細(xì)描述,是說明性的而不是限定性的,可按照所限定范圍列舉出若干個(gè)實(shí)施例,因此在不脫離本發(fā)明總體構(gòu)思下的變化和修改,應(yīng)屬本發(fā)明的保護(hù)范圍之內(nèi)。當(dāng)前第1頁12