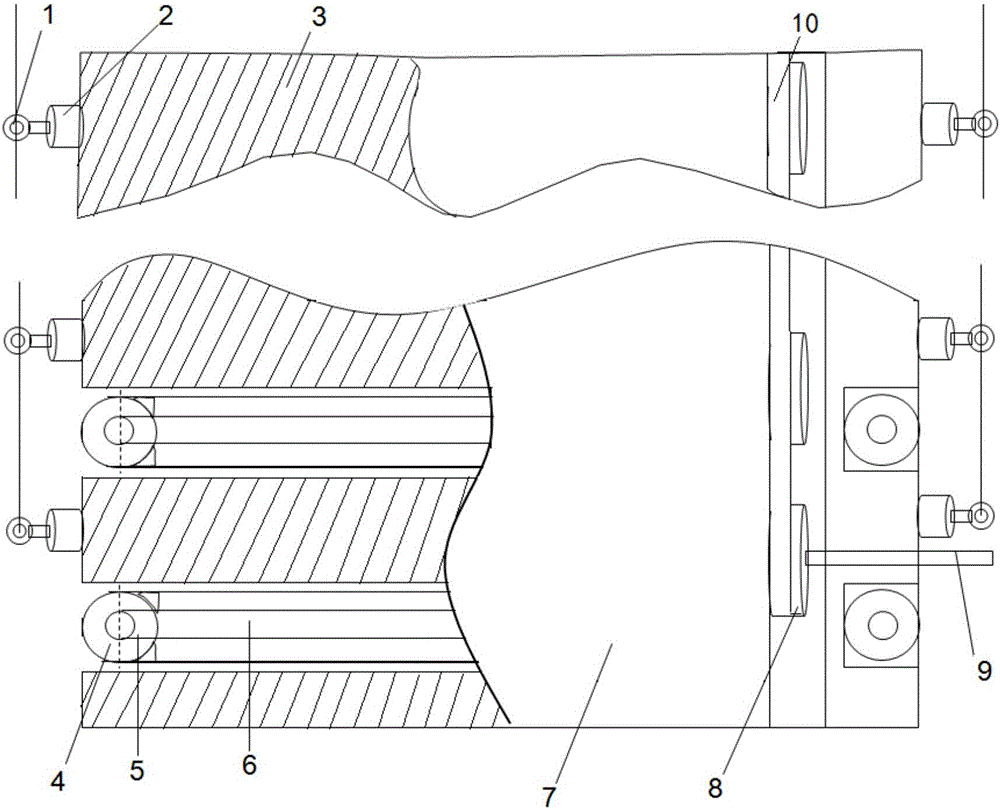
本發(fā)明涉及硅鋼熱處理工藝方法,具體涉及一種利用磁場(chǎng)回復(fù)退火提高硅鋼性能的工藝方法。
背景技術(shù):
:取向硅鋼是一種廣泛應(yīng)用于電力、電子工業(yè)的重要軟磁材料,主要用作各種電機(jī)、發(fā)電機(jī)和變壓器的鐵芯。以鐵芯損耗(鐵損)與磁感應(yīng)強(qiáng)度(磁感)為代表的磁性能是冷軋取向硅鋼的最主要性能指標(biāo),為了達(dá)到節(jié)能和保護(hù)環(huán)境的目的,全球都在致力于開(kāi)發(fā)和生產(chǎn)高磁感和低鐵損的取向硅鋼。取向硅鋼薄帶通常是由成品取向硅鋼進(jìn)一步冷軋和退火來(lái)制備,取向硅鋼的生產(chǎn)流程一般為:鐵水脫錳-冶煉-真空處理-連鑄-熱軋-?;退嵯?冷軋-脫碳退火(-回復(fù)退火)-涂氧化鎂-高溫退火-平整拉伸退火和涂絕緣層。取向硅鋼在加工工藝中獲得晶粒取向一致排列在易磁化方向的高斯織構(gòu)。晶粒在易磁化方向取向程度越高,則磁導(dǎo)率越高,鐵損越低。研究發(fā)現(xiàn)二次再結(jié)晶是形成{110}<001>高斯織構(gòu)的根本原因。而冷軋板退火時(shí)首先進(jìn)行回復(fù)退火,回復(fù)過(guò)程對(duì)于二次再結(jié)晶高斯織構(gòu)的形成有著重要影響。在回復(fù)過(guò)程冷軋組織產(chǎn)生亞晶,在高溫退火即隨后的再結(jié)晶過(guò)程中亞晶聚合形成再結(jié)晶晶核,該晶核即是有利于形成高斯織構(gòu)的組織和織構(gòu)。因此,在回復(fù)過(guò)程形成的亞晶粒即硅鋼織構(gòu)對(duì)再結(jié)晶過(guò)程高斯織構(gòu)的形成有直接而重要的影響,回復(fù)退火工藝的改善將有利于再結(jié)晶過(guò)程形成高斯織構(gòu),進(jìn)而提高硅鋼的磁性能。近年來(lái),磁場(chǎng)下冶金及材料制備這一研究領(lǐng)域受到國(guó)際學(xué)術(shù)界的廣泛關(guān)注,成為新興的科學(xué)前沿研究領(lǐng)域。磁場(chǎng)退火在控制材料的微觀結(jié)構(gòu)方面已經(jīng)引起重視,到目前為止,磁場(chǎng)已經(jīng)應(yīng)用到硅鋼的再結(jié)晶過(guò)程,并發(fā)現(xiàn)磁場(chǎng)的應(yīng)用能夠改善硅鋼的有利織構(gòu),提高硅鋼的磁性能,降低損耗。但是目前磁場(chǎng)退火主要應(yīng)用于再結(jié)晶過(guò)程,需要的磁場(chǎng)強(qiáng)度較大(大于1T),退火溫度也很高(高于750度),不易工業(yè)化。如何將磁場(chǎng)的操作簡(jiǎn)單化,更易于工業(yè)化是現(xiàn)在以及將來(lái)面臨的重要問(wèn)題。技術(shù)實(shí)現(xiàn)要素:本發(fā)明所要解決的技術(shù)問(wèn)題是提供一種利用磁場(chǎng)回復(fù)退火提高硅鋼性能的工藝方法。本發(fā)明解決上述技術(shù)問(wèn)題的技術(shù)方案如下:一種利用磁場(chǎng)回復(fù)退火提高硅鋼性能的工藝方法,在硅鋼回復(fù)退火過(guò)程中,對(duì)硅鋼施加強(qiáng)度為0-6T的磁場(chǎng)。在上述技術(shù)方案的基礎(chǔ)上,本發(fā)明還可以做如下改進(jìn)。進(jìn)一步的,所述磁場(chǎng)為靜磁場(chǎng)。進(jìn)一步的,所述回復(fù)退火的溫度范圍為450-600℃。進(jìn)一步的,在磁場(chǎng)下回復(fù)退火的時(shí)間范圍為0-30分鐘。進(jìn)一步的,在磁場(chǎng)下回復(fù)退火的時(shí)間為5分鐘。進(jìn)一步的,所述的磁場(chǎng)強(qiáng)度為0-1T。進(jìn)一步的,所述的磁場(chǎng)強(qiáng)度為0.5T。進(jìn)一步的,所述硅鋼為取向硅鋼。本發(fā)明的有益效果是:在回復(fù)退火過(guò)程中對(duì)硅鋼施加靜磁場(chǎng)以獲得有利于形成高斯織構(gòu)的組織和結(jié)構(gòu),進(jìn)而制備出高磁性能的取向硅鋼。本發(fā)明在硅鋼回復(fù)退火過(guò)程中施加靜磁場(chǎng),以改變其微觀結(jié)構(gòu),提高硅鋼的晶粒取向,從而提高硅鋼的磁性能。利用靜磁場(chǎng)可在薄帶中產(chǎn)生依賴晶粒取向的磁晶各向異性能,這為晶界遷移提供附加的驅(qū)動(dòng)力。同時(shí)外加磁場(chǎng)誘發(fā)產(chǎn)生的磁有序降低了原子的擴(kuò)散性,進(jìn)而降低了晶界的可動(dòng)性。本發(fā)明通過(guò)這一系列效應(yīng)來(lái)改善取向硅鋼退火后的織構(gòu)。本發(fā)明將靜磁場(chǎng)應(yīng)用到取向硅鋼在550度低溫區(qū)進(jìn)行回復(fù)退火,為硅鋼二次再結(jié)晶過(guò)程奠定較好的織構(gòu)基礎(chǔ),使硅鋼成品的高斯織構(gòu)增強(qiáng)。由于退火過(guò)程時(shí)間短,溫度低,磁場(chǎng)強(qiáng)度小,將更容易控制和在工業(yè)上進(jìn)行推廣應(yīng)用。附圖說(shuō)明圖1為本發(fā)明配套使用的熱處理爐主視圖;圖2為本發(fā)明配套使用的熱處理裝置俯視圖;圖3為透射電鏡觀察0.5T條件下(001)晶面取向亞晶粒電子衍射譜;圖4為圖3中的(001)晶面取向亞晶粒放大圖(暗場(chǎng)掃描);圖5為圖3中的(001)晶面取向亞晶粒放大圖(明場(chǎng)掃描)。附圖中,各標(biāo)號(hào)所代表的部件列表如下:1.導(dǎo)線,2.加熱棒,3.耐火磚,4.耐火棉,5.銅管,6.冷卻水,7.硅鋼片,8.托輥;9.電機(jī);10.傳送帶具體實(shí)施方式以下結(jié)合附圖對(duì)本發(fā)明的原理和特征進(jìn)行描述,所舉實(shí)例只用于解釋本發(fā)明,并非用于限定本發(fā)明的范圍。如圖1、圖2所示為本發(fā)明配套使用的熱處理爐結(jié)構(gòu)示意圖,將硅鋼片7放置在傳送帶10上,電機(jī)9控制托輥8,托輥8帶動(dòng)傳送帶10傳動(dòng),爐內(nèi)通有氮?dú)?。通過(guò)熱電偶控制加熱棒2進(jìn)行加熱,加熱棒2通過(guò)導(dǎo)線1并聯(lián)連接。在加熱棒2相鄰纏繞銅管5,通電流產(chǎn)生平行于軋制方向的勻強(qiáng)磁場(chǎng)。銅管5內(nèi)部為冷卻水6,外部包有耐火棉4,加熱棒2外部被耐火磚3包裹,回復(fù)退火溫度為450-600℃,退火時(shí)間選擇0-30min;磁場(chǎng)強(qiáng)度選擇0T-6T。在磁場(chǎng)中完成退火之后將樣品表面均勻涂布氧化鎂隔離涂層,送入電阻熱處理爐進(jìn)行1050~1150℃、純氫氣保護(hù)氣氛下、6~12小時(shí)的高溫退火處理,使取向硅鋼完成二次再結(jié)晶,之后隨爐冷卻。最后利用取向硅鋼專用的MATS-2010M硅鋼測(cè)量裝置對(duì)樣品進(jìn)行磁性能測(cè)試。上述利用磁場(chǎng)回復(fù)退火提高硅鋼性能的工藝方法中,施加靜磁場(chǎng)的方向?yàn)槿∠蚬桎摰能堉品较?,所采用的隔離劑為以氧化鎂為主要成分的隔離劑。所述的硅鋼試樣,采用工業(yè)生產(chǎn)中取向硅鋼的冷軋樣品,其主要成分為C:<30ppm,Si:~3%。實(shí)施例1選用工業(yè)生產(chǎn)中取向硅鋼的冷軋樣品硅鋼片7,將其放置在傳送帶10上面以一定速度前進(jìn),爐內(nèi)通氮?dú)庖员WC硅鋼在退火過(guò)程中不被氧化;退火過(guò)程中硅鋼處于加熱爐的恒溫區(qū)域內(nèi),銅管5產(chǎn)生的磁場(chǎng)方向沿硅鋼軋制方向。硅鋼片退火溫度為550℃,退火時(shí)間為5分鐘,磁場(chǎng)強(qiáng)度為1T;將回復(fù)退火后的樣品表面均勻涂布氧化鎂隔離劑;將涂好氧化鎂涂層的試樣送入電阻熱處理爐進(jìn)行1100℃、純氫氣保護(hù)氣氛下、12個(gè)小時(shí)的高溫退火處理,使取向硅鋼完成再結(jié)晶;最后對(duì)取向硅鋼成品進(jìn)行磁性能測(cè)量。為進(jìn)行對(duì)比,取普通無(wú)磁場(chǎng)退火下取向硅鋼試樣進(jìn)行上述高溫退火處理,最后對(duì)取向硅鋼成品進(jìn)行磁性能測(cè)量。表1是硅鋼片在普通無(wú)磁場(chǎng)回復(fù)退火5分鐘條件下后經(jīng)高溫結(jié)晶退火后的六片樣品磁性能的平均值,和磁場(chǎng)強(qiáng)度1T條件下回復(fù)退火5分鐘經(jīng)高溫結(jié)晶退火后的六片樣品磁性能的平均值的數(shù)據(jù)對(duì)比,其中B8是六片樣品磁感的平均值;rB是磁場(chǎng)作用下相比于無(wú)磁場(chǎng)情況下磁感的增長(zhǎng)率;DB是六片樣品磁感的誤差;P17/50是六片樣品鐵損的平均值;rP是磁場(chǎng)作用下相比于無(wú)磁場(chǎng)情況下鐵損的降低率;DP是六片樣品鐵損的誤差。(B8指取磁場(chǎng)強(qiáng)度為800A/m時(shí)的磁感值;P17/50指取磁感為1700mT,50Hz時(shí)的鐵損值)磁場(chǎng)強(qiáng)度(T)B8(mT)rBDBP17/50(W/kg)rPDP01786-±1.6%1.53-±6.4%118393.0%±0.6%1.389.8%±3.2%結(jié)合上述實(shí)施例中的測(cè)試結(jié)果可以看到,采用靜磁場(chǎng)回復(fù)退火制備的取向硅鋼的磁感值要遠(yuǎn)遠(yuǎn)高于沒(méi)有施加磁場(chǎng)的磁感值,而鐵損值也遠(yuǎn)遠(yuǎn)低于沒(méi)有施加靜磁場(chǎng)的鐵損值。實(shí)施例2將上述磁場(chǎng)強(qiáng)度調(diào)整為0.5T,回復(fù)退火過(guò)程及熱處理溫度不變;同時(shí)為進(jìn)行對(duì)比,取普通無(wú)磁場(chǎng)回復(fù)退火下取向硅鋼試樣進(jìn)行上述高溫退火處理,最后對(duì)取向硅鋼成品進(jìn)行磁性能測(cè)量。表2是硅鋼片在普通無(wú)磁場(chǎng)回復(fù)退火5分鐘條件下后經(jīng)高溫結(jié)晶退火后的六片樣品磁性能的平均值,和磁場(chǎng)強(qiáng)度0.5T條件下回復(fù)退火5分鐘經(jīng)高溫結(jié)晶退火后的六片樣品磁性能的平均值的數(shù)據(jù)對(duì)比,其中B8是六片樣品磁感的平均值;rB是磁場(chǎng)作用下相比于無(wú)磁場(chǎng)情況下磁感的增長(zhǎng)率;DB是六片樣品磁感的誤差;P17/50是六片樣品鐵損的平均值;rP是磁場(chǎng)作用下相比于無(wú)磁場(chǎng)情況下鐵損的降低率;DP是六片樣品鐵損的誤差。磁場(chǎng)強(qiáng)度(T)B8(mT)rBDBP17/50(W/kg)rPDP01786-±1.6%1.53-±6.4%0.518362.8%±0.9%1.3512%±3.5%將硅鋼薄片在雙噴射電解減薄器上進(jìn)行減薄,進(jìn)行透射電鏡觀察。在整個(gè)剪薄視場(chǎng),在至少10張隨機(jī)拍攝的照片上進(jìn)行觀察,如圖3、圖4和圖5所示,0.5T磁場(chǎng)下亞晶粒組織較多,且主要為立方織構(gòu)(4-5個(gè)),亞晶粒主要是由于位錯(cuò)滑移和攀移產(chǎn)生的,磁場(chǎng)的作用下使亞晶粒更易于(110)取向,(001)面增多。在隨后的高溫退火再結(jié)晶過(guò)程,亞晶粒聚合長(zhǎng)大,形成取向程度較高的硅鋼成品,提高硅鋼磁性能。結(jié)合上述實(shí)施例中的測(cè)試結(jié)果可以看到,在本發(fā)明中施加0.5T靜磁場(chǎng)對(duì)硅鋼磁性能有了明顯改觀,說(shuō)明采用低于1T靜磁場(chǎng)退火可以制備出性能優(yōu)于常規(guī)退火方式制備的取向硅鋼。這對(duì)靜磁場(chǎng)回復(fù)退火工業(yè)化將具有現(xiàn)實(shí)指導(dǎo)意義。以上所述僅為本發(fā)明的較佳實(shí)施例,并不用以限制本發(fā)明,凡在本發(fā)明的精神和原則之內(nèi),所作的任何修改、等同替換、改進(jìn)等,均應(yīng)包含在本發(fā)明的保護(hù)范圍之內(nèi)。當(dāng)前第1頁(yè)1 2 3