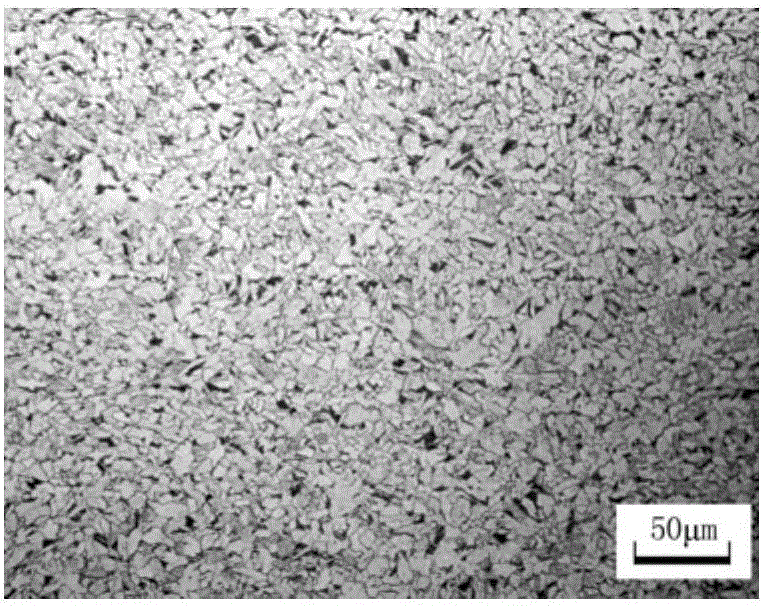
本發(fā)明涉及工程機械、橋梁、船板等行業(yè)用熱軋開平鋼板的工藝制造領域,具體地指一種厚規(guī)格高表面質量熱軋開平板及其制造方法。
背景技術:
:厚規(guī)格熱軋開平板,主要應用與船舶、工程機械及橋梁等制造行業(yè),以目前常見的2250mm產線為例,當鋼板厚度規(guī)格在14-25mm時,由于鋼板較厚,生產過程受機械設備能力、生產節(jié)奏等限制,表面質量往往很難控制,尤其是對于強度級別較低的軟鋼,表面硬度較低,不僅鋼板表面會出現(xiàn)大量氧化鐵皮,同時在開平生產過程中很容易形成凹坑、麻點、壓印等表面缺陷。目前,熱軋鋼板表面凹坑、麻點、壓印等缺陷不僅直接影響外觀,更對下游終端產品的噴漆效果產生一定影響,隨著下游各行業(yè)競爭的日趨激烈,國內外相關行業(yè)的主要生產加工廠商對鋼板表面質量的要求也越來越高,基本不允許熱軋鋼板表面出現(xiàn)黑灰、凹坑、麻點等常規(guī)缺陷。因此,采用合理的生產方法制造出性能優(yōu)異且表面質量優(yōu)良的熱軋開平板成為鋼廠亟待解決的問題。如中國專利CN102764760是一種高表面質量熱軋鋼板的制造方法,它通過將Si含量控制在0.15%以下,同時對軋制整個流程進行一定的工藝優(yōu)化、過程控制,獲得了具有較高表面質量的熱軋鋼板。但其主要以生產出熱軋卷為目的,并未考慮后期開平矯直生產過程可能對鋼板表面質量造成的影響。如中國專利CN101947557是一種減少熱軋鋼板表面生成氧化鐵皮的制備方法,它通過控制板坯抽鋼溫度、精軋開軋和終軋溫度、卷取溫度和冷卻方式實現(xiàn)減少氧化鐵皮生成的目的。此種方法主要通過控制出爐溫度,減少初生氧化鐵皮厚度,一定程度上減少了鋼板表面氧化鐵皮,改善了鋼板表面質量。但未考慮超快冷工藝和開平矯直過程對鋼板表面質量的影響。如中國專利CN101947557是一種熱軋鋼板及其表面氧化鐵皮的去除方法,它通過控制加熱溫度、精軋溫度、冷卻工藝和卷取溫度實現(xiàn)控制鋼板表面氧化鐵皮的目的。此種方法主要通過控制軋制工藝盡可能的減少鋼板表面氧化鐵皮量,也未考慮后續(xù)開平過程對鋼板表面質量的影響。技術實現(xiàn)要素:本發(fā)明的目的是提供了一種厚規(guī)格高表面質量熱軋開平板的的制造方法。該方法即生產一種厚度為14-25mm,屈服強度級別210-400MPa,表面光亮,基本無凹坑、麻點、壓印的熱軋開平板。此鋼板普遍應用于船舶、工程機械及橋梁等制造行業(yè)。為實現(xiàn)上述目的,本發(fā)明提供的一種厚規(guī)格高表面質量熱軋開平板,所述熱軋開平板的化學成分重量百分比包括C:0.05~0.25%,Si:0.005~0.20%,Mn:0.10~2.0%,P≤0.025%,S≤0.025%,Als:0.020~0.070%、Nb:0.005~0.10%、V:0.001~0.20%、Ti:0.01~0.15%、B:0.0001~0.005%,其余為Fe及雜質。雜質要求Ni≤0.30%、Cr≤0.20%、Mo≤0.08%、Cu≤0.35%、Sn≤0.03%、Pb≤0.02%。進一步地,所述熱軋開平板的化學成分重量百分比包括C:0.05~0.20%,Si:0.01~0.20%,Mn:0.10~1.0%,Nb:0.005~0.05%、V:0.001~0.10%、Ti:0.01~0.10%、B:0.0001~0.003%、P≤0.020%、S≤0.020%、Als:0.025~0.060%,余為Fe及雜質。雜質要求Ni≤0.30%、Cr≤0.20%、Mo≤0.08%、Cu≤0.35%、Sn≤0.03%、Pb≤0.02%。再進一步地,所述熱軋開平板的化學成分重量百分比為C:0.11%,Si:0.05%,Mn:0.31%,P:0.017%,S:0.015%,Als:0.043%,Nb:0.014%,V:0.003%,Ti:0.022%,B:0.0008%,其余為Fe及雜質,雜質要求Ni≤0.30%、Cr≤0.20%、Mo≤0.08%、Cu≤0.35%、Sn≤0.03%、Pb≤0.02%。再進一步地,所述熱軋開平板的厚度規(guī)格為14~25mm,強度級別210~400MPa。本發(fā)明提供了一種厚規(guī)格高表面質量熱軋開平板的制造方法,該熱軋開平板通過高爐鐵水、鐵水預脫硫、轉爐冶煉、LF+RH精煉、板坯連鑄、鑄坯緩冷、板坯加熱、熱連軋、超快冷+層流冷卻、卷取、開卷、7輥粗矯+11輥精矯、橫切制備而成,其中,1)板坯加熱過程中板坯出爐溫度為1150~1280℃,在爐時間140~200min,保證合金元素完全固溶及充分奧氏體化;2)熱連軋過程中開軋溫度950~1080℃,精軋溫度800~980℃,卷取溫度500~680℃;采用高壓水除鱗,軋制過程中精軋機架間水全開,確保粗軋和精軋全道次除鱗;3)層流冷卻采用超快冷+前段層流冷卻模式,保證鋼板表面硬度HV10為200~280kgf/mm2;4)開卷過程中開卷前對開平線進行設備清掃,確認設備沒有油污、積聚的塵灰;5)7輥粗矯+11輥精矯過程中7輥粗矯入口矯直壓力相較計算值降低15%~25%,出口矯直壓力相較計算值降低20%~30%,11輥精矯入口和出口矯直壓力按計算值設定;7輥粗矯前加裝刷輥,去除少量FeO脫落形成的黑粉,11輥精矯前加裝吹掃裝置,防止異物壓入。作為優(yōu)先方案中,所述步驟3)中,開軋溫度950~1050℃,精軋溫度800~900℃,卷取溫度540~660℃作為優(yōu)先方案中,所述步驟3)中,超快冷段冷卻強度大于50~80℃/s,前段層流冷卻強度為10~30℃/s。作為優(yōu)先方案中,所述熱軋開平板的厚度規(guī)格為14~25mm,強度級別210~400MPa。其中:重點控制超快冷段冷卻強度和7輥粗矯出入口矯直力。以下簡述本發(fā)明中成分范圍及工藝要點的理由:C:含量控制在0.05~0.20wt%范圍內。碳是提高硬度、強度和耐磨性的主要元素,含有0.01wt%以上,才能確保鋼板的強度。但過高的C會降低鋼的延性和焊接性,本發(fā)明中碳含量控制范圍在0.05~0.25wt%,優(yōu)選為0.05~0.20wt%。Si:含量控制在0.01~0.20wt%范圍內。硅是煉鋼脫氧的必要元素,且以固溶強化形式提高鋼的強度,含量一般在0.005wt%以上。當Si≥0.2wt%時,與O發(fā)生反應后以SiO2的形式存在,SiO2又與FeO易形成FeO/Fe2SiO4的共析產物或成鐵橄欖石(2FeSiO2),F(xiàn)eO/Fe2SiO4的共析產物凝固后為錨狀形貌,F(xiàn)eO很難去除;鐵橄欖石嵌入到氧化鐵皮層中后,與基體的結合非常緊密,高壓水除磷也很難將其除去。本發(fā)明中控制Si:0.005~0.20wt%,優(yōu)選為0.01~0.20wt%。Mn:含量控制在0.10~1.0wt%。錳能消除或減弱因硫所引起的熱脆性,從而改善鋼的熱加工性能。Mn和鐵形成固溶體,提高鋼中鐵素體和奧氏體的硬度和強度,強化基體;同時又是碳化物形成元素,進入滲碳體中取代一部分鐵原子,生成Mn3C,它與Fe3C能相互溶解,在鋼中形成在(FeMn)3C型化合物,從而提高鋼的強度、硬度。因此,一般含有0.10wt%以上的錳。但錳含量較高會造成較嚴重的中心偏析,并降低韌性,錳選擇為0.10~2.0wt%,優(yōu)選為0.10~1.0wt%。Nb:含量控制在0.005~0.05wt%。鈮可細化晶粒和彌散強化提高強度,硬度,0.10wt%以下即可達到細化晶粒和彌散強化的作用。本發(fā)明中控制Nb含量為0.005~0.10wt%,優(yōu)選為0.005~0.05wt%。V:含量控制在0.001~0.10wt%。釩能顯著改善普通低碳低合金鋼的焊接性能,可細化組織晶粒,提高強度和韌性。本發(fā)明中控制V含量為0.001~0.20wt%,優(yōu)選為0.001~0.10wt%。Ti:含量控制在0.01~0.10wt%。適量的鈦在連鑄冷卻條件下生成彌散的TiN顆粒,由于它的熔點很高,在焊接熱影響區(qū)能顯著抑制晶粒長大。本發(fā)明中控制Ti含量為0.01~0.15wt%,優(yōu)選為0.01~0.10wt%。B:含量控制在0.0001~0.003wt%。硼可以提高鋼的淬透性,可使厚規(guī)格鋼板調質后性能大為改善。本發(fā)明B含量控制在0.0001~0.005wt%,優(yōu)選為0.0001~0.003wt%。板坯出爐溫度為1150~1280℃,保證生產節(jié)奏;在爐時間140~200min,保證合金元素完全固溶及充分奧氏體化,減少初生氧化鐵皮的厚度。采用高壓水除鱗,軋制過程中精軋機架間水全開,確保粗軋和精軋全道次除鱗,盡可能去除鋼板表面氧化鐵皮。開軋溫度控制在950~1050℃,精軋溫度控制在800~900℃,卷取溫度為540~660℃。開軋溫度、精軋溫度和卷曲溫度的設定主要依據常規(guī)軋制節(jié)奏,并保證鋼板力學性能。進行超快冷+前段層流冷卻,超快冷段冷卻強度大于50℃/s,前段層流冷卻強度為10~30℃/s。對厚規(guī)格鋼板使用超快冷的強冷工藝,超快冷段冷卻強度大于50℃/s,保證鋼板表面形成激冷層,表面硬度HV10≥200kgf/mm2,減少鋼板表面因矯直壓入氧化鐵皮而形成的凹坑、麻點、壓印等缺陷。前段層流冷卻強度控制在10~30℃/s,可調節(jié)CT溫度,保證鋼板力學性能。優(yōu)化矯直工藝,將7輥粗矯入口矯直壓力相較計算值降低15%~25%,出口矯直壓力相較計算值降低20%~30%,11輥精矯入口和出口矯直壓力按計算值設定。適當降低粗矯入口矯直壓力,可在保證板型的基礎上使鋼板表面的氧化鐵皮充分壓碎;降低出口矯直壓力20%~30%,可在保證板型的基礎上,防止破碎的氧化鐵皮壓入鋼板表面;粗矯后的鋼板經吹掃裝置去除破碎的氧化鐵皮后進入精矯,即保證了鋼板表面質量又避免翹曲等板型問題的出現(xiàn)。本發(fā)明的有益效果在于:本發(fā)明生產的厚度規(guī)格14-25mm,強度級別≤400MPa的熱軋開平板,力學性能優(yōu)異,表面質量良好,在船舶、工程機械、橋梁等行業(yè)具有明顯的競爭優(yōu)勢。通過對超快冷設備改造后冷卻工藝的合理利用,并對強度級別較低的厚規(guī)格鋼板開平工藝進行優(yōu)化,獲得了表面光亮,基本沒有凹坑、麻點、壓印等缺陷的熱軋開平板。此方法的應用大大提高了該類高表面質量熱軋產品的市場競爭力,經濟效益顯著。附圖說明圖1為16mm強度為355MPa的工程機械用熱軋開平板,超快冷段冷卻強度為57℃/s時的表面組織圖;圖2為熱軋開平板的心部組織圖。具體實施方式為了更好地解釋本發(fā)明,以下結合具體實施例進一步闡明本發(fā)明的主要內容,但本發(fā)明的內容不僅僅局限于以下實施例。一種厚規(guī)格高表面質量熱軋開平板的的制造方法,冶煉時,將Si的重量百分比控制在0.01~0.20wt%之間,選擇性添加適量Cu、Cr、Ni、Nb、V、Ti、B等元素。板坯出爐溫度為1150-1280℃,在爐時間140-200min,保證合金元素完全固溶及充分奧氏體化;開軋溫度950-1080℃,精軋溫度800-980℃,卷取溫度500-680℃;進行超快冷+前段層流冷卻,超快冷段冷卻強度大于50℃/s,前段層流冷卻強度為10-30℃/s,鋼板表面硬度HV10≥200kgf/mm2;采用高壓水除鱗,軋制過程中精軋機架間水全開,確保粗軋和精軋全道次除鱗;優(yōu)化矯直工藝,7輥粗矯入口矯直壓力相較計算值降低15%-25%,出口矯直壓力相較計算值降低20%-30%,11輥精矯入口和出口矯直壓力按計算值設定;開卷前對開平線進行設備清掃,確認設備沒有油污、積聚的塵灰;7輥粗矯前加裝刷輥,去除少量FeO脫落形成的黑粉,11輥精矯前加裝吹掃裝置,防止異物壓入。下面結合具體實施例對本發(fā)明的技術方案進一步詳細描述。鑄坯厚度為250mm,鋼板厚度規(guī)格為20mm,寬度為1800mm。本發(fā)明中化學成分見表1,其余為Fe。生產工藝控制與鋼板質量情況見表2。如圖1~2所示,鋼板表面激冷層晶粒細小,心部組織相對較為粗大,差別明顯。對比例1和2中,當超快冷段冷卻速度降低時,盡管對矯直壓力進行了優(yōu)化,但鋼板因表面硬度不足,仍會出現(xiàn)少量凹坑、麻點和鐵皮壓入等缺陷。對比例3中,因入口矯直力較大,鋼板表面部分氧化鐵皮直接被壓入鋼板表面,后續(xù)清掃、精矯過程中容易因鐵皮脫落出現(xiàn)凹坑、麻點等缺陷。對比例4中,因粗矯出口矯直力過低,粗矯后易出現(xiàn)翹曲,無法保證后續(xù)生產。對比例5中,粗矯入口和出口矯直力與計算值相差無幾,此時因前后矯直力過大,破碎的氧化鐵皮大量被壓入,且無法清掃去除,鋼板表面凹坑、麻點等缺陷嚴重,因此不利于高表面質量熱軋開平板的生產。表1本發(fā)明鋼板的化學成分情況(wt%)序號CSiMnPSAlsNbVTiB成分10.110.050.310.0170.0150.0430.0140.0030.0220.0008成分20.120.040.340.0160.0120.0360.0200.0010.0270.0012成分30.100.030.290.0130.0130.0350.0080.0170.0170.0015成分40.110.040.270.0190.0150.0410.0180.0020.0230.0010成分50.130.050.360.0140.0120.0430.0210.0020.0160.0009其它未詳細說明的部分均為現(xiàn)有技術。盡管上述實施例對本發(fā)明做出了詳盡的描述,但它僅僅是本發(fā)明一部分實施例,而不是全部實施例,人們還可以根據本實施例在不經創(chuàng)造性前提下獲得其他實施例,這些實施例都屬于本發(fā)明保護范圍。當前第1頁1 2 3