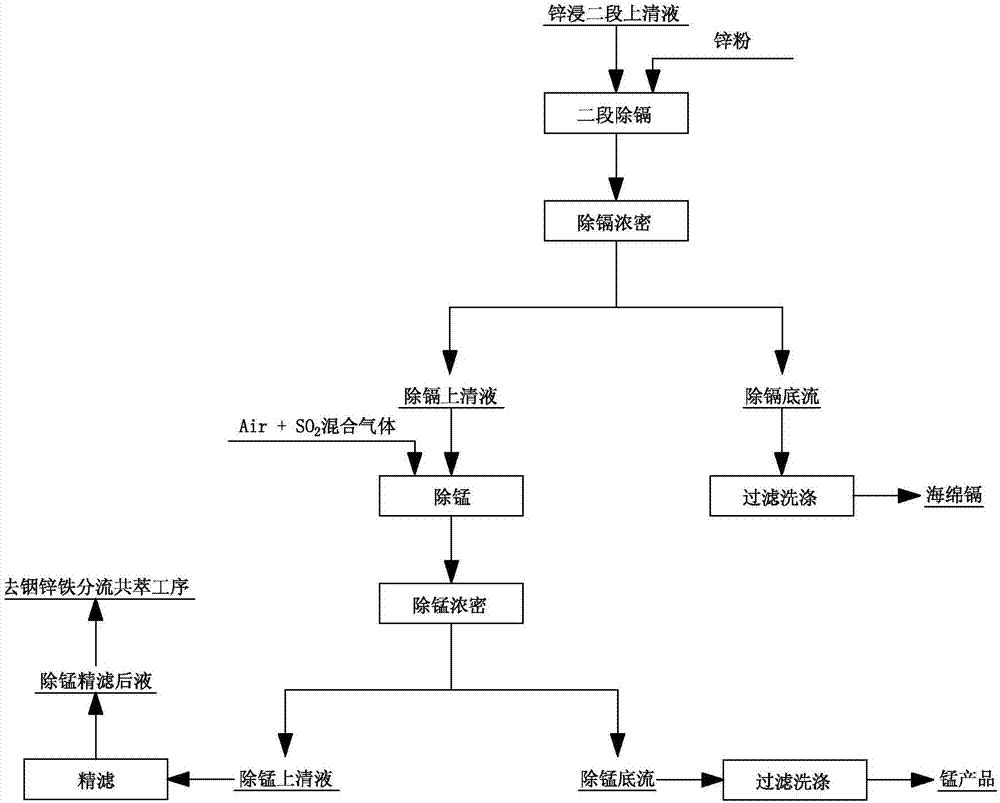
本發(fā)明涉及有色金屬固體廢渣處理領(lǐng)域,具體地說(shuō)是一種用分流共萃工藝從有色金屬固體廢渣中回收銦鋅鐵等有價(jià)金屬的方法。
背景技術(shù):有色金屬固體廢渣中的有價(jià)金屬成份較為復(fù)雜,根據(jù)其成份的不同,采用的回收方法也不盡相同,但目前國(guó)內(nèi)外對(duì)有色固體廢渣中銦鋅鐵的回收方法比較單一,主要有以下兩種:(1)酸浸除雜法:該方法采用硫酸作為浸出劑,在高酸下將銦、鋅、鐵金屬浸出,再用鐵粉作為還原劑,將溶液中的三價(jià)鐵離子全部還原成二價(jià)鐵離子,通過(guò)P204萃取后,將銦從溶液中提出,含銦液用鋅粉置換變漲成海綿銦,經(jīng)熔煉后變?yōu)榇帚熶N售;而P204萃取后液則用氧化鋅中和,將鋅的濃度提高到120~150g/L,采用黃鈉鐵礬法除鐵,再分別除去銅、鎘、鎳、鈷等雜質(zhì),如果溶液中含氟離子、氯離子濃度過(guò)高還得再將它們分別除去,得到的純凈硫酸鋅溶液可以用蒸發(fā)結(jié)晶的方法生產(chǎn)七水硫酸鋅產(chǎn)品或者直接電解生產(chǎn)鋅金屬。這種方法,一是能耗高、產(chǎn)生的工業(yè)廢渣種類較多,如:鐵渣、銅鎘渣、鎳鈷渣等;二是工業(yè)廢水排放量大,如:除氟、氯產(chǎn)生的廢水;三是收率較低,在鐵粉作為還原劑的工序,會(huì)損失大量的銦金屬到渣中;四是環(huán)保問(wèn)題嚴(yán)重,不適合中國(guó)未來(lái)環(huán)保發(fā)展的清潔冶金方向。(2)綜合法回收銦鎵鍺:以富含銦、鎵、鍺的鋅浸出渣為原料,經(jīng)過(guò)浸出、用丹寧沉淀鍺和用溶劑萃取提取銦、鎵、鍺的過(guò)程,主要包括預(yù)處理、提取銦和提取鎵等作業(yè),該法于1975年在中國(guó)研究成功。預(yù)處理濕法煉鋅廠產(chǎn)出的鋅浸出渣中,有部分鋅和鐵形成鐵酸鋅(nZnO·mFe2O3),而95%左右的銦、鍺、鎵以類質(zhì)同象存在于鐵酸鋅中。用鋅電解貧液浸出含銦、鍺、鎵的鋅浸出渣時(shí),銦、鍺、鎵轉(zhuǎn)入浸出液。過(guò)濾所得的濾液加鋅粉置換,銦、鍺、鎵被置換成金屬,獲得富含銦、鍺、鎵置換渣。置換渣用硫酸逆流浸出,控制浸出液最終酸度(含游離酸0.6mol/L左右),便可使置換渣中96~100%的銦、鍺、鎵轉(zhuǎn)入溶液。用鹽酸反萃取銦負(fù)載有機(jī)相,得含銦67~84g/L的反萃液,反萃液加鋅粉置換得海綿銦,海綿銦經(jīng)壓團(tuán)和堿熔鑄后送電解,得純度99.99%的銦,銦的回收率超過(guò)90%。而鋅粉置換的后液,則用鈉堿變?yōu)樘妓徜\或氫氧化鋅的沉淀,沉淀后溶液則排放進(jìn)入污水處理系統(tǒng)。這個(gè)方法對(duì)水的污染較為嚴(yán)重,隨著日益嚴(yán)厲的環(huán)保法的實(shí)施,已經(jīng)不再適合對(duì)銦鎵鍺等金屬的綜合回收。上述的兩種方法,在對(duì)有價(jià)金屬回收的同時(shí),會(huì)產(chǎn)生二次污染的渣和工業(yè)廢水,需要對(duì)這些污染物進(jìn)一步再處理。
技術(shù)實(shí)現(xiàn)要素:本發(fā)明所要解決的技術(shù)問(wèn)題是克服上述現(xiàn)有技術(shù)存在的缺陷,提供一種用分流共萃工藝從有色固體廢渣中回收銦鋅鐵等有價(jià)金屬的方法,其利用金屬離子在溶劑萃取中的特征,不斷地將浸出金屬離子所消耗的酸進(jìn)行再生;通過(guò)控制溶液酸度,對(duì)含有不同金屬離子的溶液進(jìn)行分流,形成一個(gè)溶液的閉路循環(huán)。為此,本發(fā)明采用如下的技術(shù)方案:用分流共萃工藝從有色固體廢渣中回收有價(jià)金屬的方法,包括依次進(jìn)行的一段加壓浸出和兩段常壓逆流浸出工序、鎘錳凈化工序、銦鋅鐵分流共萃工序、鹽酸再生工序及無(wú)錳鋅電積工序,其特征在于:1)所述的二段常壓逆流浸出工序包括鋅浸二段和鋅浸一段,在鋅浸二段中,來(lái)自于銦鋅鐵分流共萃工序的含酸共萃余液、有色固體廢渣與空氣+SO2的混合氣體進(jìn)行充分混合浸出,pH控制在3-3.5,T=45-55℃,除鋅外,鐵與其它金屬均被抑制浸出,并將鐵以FeOOH的形態(tài)存在于鋅浸二段底流中,鋅浸二段上清液進(jìn)入鎘錳凈化工序,鋅浸二段底流進(jìn)入鋅浸一段中與含酸的萃鋅余液充分混合浸出;在鋅浸一段中,pH控制在1~2.5,T=45-55℃,鋅、鐵及銦金屬被浸出,鋅浸一段底流中鋅的濃度控制在15~50g/L,鋅浸一段底流進(jìn)入一段加壓浸出工序;在一段加壓浸出工序中,加壓浸出的工藝控制條件為:有氧條件下,T=150-200℃,P=1.2~1.8Mpa,H2SO4的濃度為100~180g/L,鋅浸一段底流與銦鋅鐵分流共萃工序的含酸共萃余液充分混合浸出;利用此條件選擇性浸出In3+、Zn2+離子,除Cd2+、Mn2+離子外,其它雜質(zhì)被抑制,得到的加壓上清液及鋅浸一段上清液去銦鋅鐵分流共萃工序;2)所述的鎘錳凈化工序中,鋅浸二段上清液與鋅粉進(jìn)行兩段置換反應(yīng),除鎘底流經(jīng)過(guò)濾洗滌后得到海綿鎘,除鎘上清液與空氣+SO2的混合氣體充分混合除錳,除錳上清液去銦鋅鐵分流共萃工序,除錳底流經(jīng)過(guò)濾洗滌后得到錳產(chǎn)品;3)所述的銦鋅鐵分流共萃工序中,加壓上清液、鋅浸一段上清液及除錳底流分別進(jìn)入銦鐵共萃段、銦鋅共萃段和鋅萃取段,萃取后形成三種負(fù)載有機(jī)相和分別產(chǎn)生銦鐵共萃余液、銦鋅共萃余液和萃鋅余液,銦鐵共萃余液大部分返回一段加壓浸出進(jìn)行循環(huán),小部分進(jìn)入鋅浸二段,銦鋅共萃余液全部返回到鋅浸二段,萃鋅余液全部返回到鋅浸一段;所述的三種負(fù)載有機(jī)相依次經(jīng)過(guò)水洗段、酸洗段、反萃段、反銦段、反鐵二段、反鐵一段和洗氯段,負(fù)載有機(jī)相先經(jīng)過(guò)水洗段洗去負(fù)載有機(jī)相中機(jī)械夾帶的氯、氟離子,再經(jīng)過(guò)酸洗段洗下萃上的銅、錳離子。本發(fā)明采用一段加壓和兩段常壓逆流浸出和銦鋅鐵分流共萃新工藝,結(jié)合無(wú)鈉濕法冶金體系,實(shí)現(xiàn)了系統(tǒng)內(nèi)酸和工業(yè)廢水的循環(huán)再生。獨(dú)創(chuàng)的銦、鋅、鐵分段浸出與分段萃取技術(shù)相結(jié)合,使得萃取銦鋅鐵時(shí)產(chǎn)生的酸能夠完全被循環(huán)利用,比傳統(tǒng)工藝節(jié)約運(yùn)行成本70%以上。獨(dú)創(chuàng)的銦鋅鐵分流萃取技術(shù),做到了分段浸出與分段萃取技術(shù)有機(jī)結(jié)合,優(yōu)化與創(chuàng)新了銦鋅鐵分流共萃工藝。獨(dú)創(chuàng)的一段加壓和兩段常壓逆流技術(shù)實(shí)現(xiàn)了銦鋅鐵選擇性的浸出,加壓浸出提高了銦鋅的浸出率,達(dá)到了95%以上。獨(dú)特的萃取除鐵與Air+SO2混合氧化除鐵錳技術(shù)相結(jié)合,解決了傳統(tǒng)工藝難以解決的除鐵廢渣問(wèn)題。鹽酸再生技術(shù)解決了萃取工序產(chǎn)生的FeCl3廢酸液?jiǎn)栴},同時(shí),也將InCl3直接變成了高純In2O3;鹽酸再生技術(shù)也解決了反銦富液提取銦后殘留的ZnCl2廢酸液?jiǎn)栴}。采用了獨(dú)特的無(wú)錳電積技術(shù),鋅電解槽內(nèi)再無(wú)陽(yáng)極泥沉淀,提高了電解工序的作業(yè)率和產(chǎn)品的質(zhì)量。本發(fā)明通過(guò)各種獨(dú)創(chuàng)的和獨(dú)特的技術(shù)組合,集成了一個(gè)獨(dú)創(chuàng)的從有色固廢渣中提取銦鋅鐵等有價(jià)金屬的濕法冶金體系,比起傳統(tǒng)的技術(shù),不但實(shí)現(xiàn)了零成本提取銦,無(wú)工業(yè)除鐵廢渣的產(chǎn)生,而且實(shí)現(xiàn)了真正意義上的工業(yè)廢水零排放。在一段加壓和兩段常壓逆流浸出工序中,Air+SO2混合氧化除鐵錳技術(shù)將在常壓的條件下,抑制有色固廢渣中鐵的浸出,并將鐵以FeOOH的形態(tài)固定在常壓浸出渣中;Air+SO2進(jìn)入水溶液狀態(tài)后,會(huì)立即形成一種FeSO5的物質(zhì),這種物質(zhì)有極強(qiáng)的氧化性,可以將溶液中的Fe2+離子迅速氧化成Fe3+離子,化學(xué)反應(yīng)方程式如下:FeSO5+Fe2++2H+=2Fe3++SO42-+H2O⑴而此時(shí)的三價(jià)鐵離子又會(huì)與有色固廢渣中含有鈣、鎂等堿性氧化物發(fā)生水解反應(yīng),在控制pH保持在3-3.5的狀態(tài)下,化學(xué)反應(yīng)方程式如下:Fe3++OH-+H2O=FeOOH+2H+⑵經(jīng)過(guò)兩段常壓逆流浸出,鋅的浸出率可以達(dá)到85%以上,銦的浸出率在~30%左右,而鐵基本被抑制在常壓浸出渣中。常壓浸出渣中的各種有價(jià)金屬將會(huì)在加壓通氧的條件下被大量的浸出,在加壓浸出的過(guò)程中,溫度控制在150~200℃,壓力控制在1.2~1.8Mpa,酸度控制在100~180g/L,通入氧氣,此時(shí),鋅的總浸出率達(dá)到95%以上,銦的總浸出率達(dá)到92%以上,除已經(jīng)形成針鐵礦的以外,其它的鐵則以赤鐵礦(Fe2O3)的形式存在于渣中,但加壓浸出液中還有不超過(guò)5g/L的Fe3+離子,化學(xué)反應(yīng)方程式如下:采用Air+SO2混合氧化除鐵錳技術(shù),通過(guò)控制其中一段常壓浸出的終點(diǎn)PH值在3.0~3.5,可以有效地抑制銦和鐵的浸出,同時(shí)有色固廢渣中含有少量的金屬硫化物也可以被氧化浸出;采用高壓高酸氧浸可以選擇性的強(qiáng)化In3+、Zn2+等離子的浸出,抑制Sn2+、As2+等離子的浸出,使90%的Fe3+離子以Fe2O3形態(tài)沉淀(其它5%的Fe3+離子以FeOOH形態(tài)沉淀);而通過(guò)控制另一段常壓浸出的終點(diǎn)PH值1-2.5,則可以讓In3+、Zn2+等離子共同浸出。砷則以砷酸根的形式存在,砷酸根極易與其它金屬離子形成砷酸鹽沉淀,化學(xué)方程式如下:2As2-+5O2=2AsO53+⑷3Men++nAsO53+=Me3(AsO5)n⑸在鎘錳凈化工序中,由于Cd2+、Mn2+離子經(jīng)過(guò)一段加壓兩段常壓逆流浸出后,浸出率高達(dá)95%以上,如不及時(shí)除去,則會(huì)在溶液中循環(huán)富集,最后影響到分流共萃工序的正常運(yùn)行。采用鋅粉除鎘的方法,也是對(duì)溶液中其它離子盡一步凈化的過(guò)程,其化學(xué)反應(yīng)方程式如下:CdSO4+Zn=Cd+ZnSO4⑹MeSO4+Zn=Me+ZnSO4⑺采用Air+SO2混合氧化除鐵錳技術(shù)在此工序?qū)n2+離子以MnO2或者M(jìn)n2O3的形式除去,以消除其在整個(gè)系統(tǒng)內(nèi)的富集,其化學(xué)反應(yīng)方程式如下:當(dāng)pH<4時(shí),Mn2++SO2+O2+2H2O=MnO2+4H++SO42-⑻當(dāng)pH=5~7時(shí),2Mn2++SO2+O2+3H2O=Mn2O3+6H++SO42-⑼。在銦鋅鐵分流共萃工序中,來(lái)自于加壓浸出液(即加壓上清液)中的銦與鐵在高酸度下直接共萃,萃取的酸度在100~180g/L,在這個(gè)酸度下,In3+優(yōu)先與P204萃取劑發(fā)生反應(yīng),其次才是Fe3+與P204萃取劑發(fā)生反應(yīng),化學(xué)反應(yīng)方程式如下:In3++3HR(org)=InR3(org)+3H+⑽Fe3++3HR(org)=FeR3(org)+3H+⑾來(lái)自于常壓浸出液(即一段上清液)中的銦與鋅在pH=1~3.5時(shí)直接共萃,化學(xué)反應(yīng)方程式如下:Zn2++2HR(org)=ZnR2(org)+2H+⑿在反鋅段,則用酸度在160~220g/L的電鋅貧液(即反鋅前液)作為反萃劑將鋅反下,變成富鋅液,除油后用于鋅電積,化學(xué)反應(yīng)方程式如下:ZnR2(org)+H2SO4=ZnSO4+2HR(org)⒀在反銦段,則用酸度為2~4N的HCl和1~2NZnCl2作為反萃劑將銦反下,變成富銦液,這個(gè)過(guò)程中,也會(huì)有少許的三價(jià)鐵會(huì)被反下,因此要經(jīng)樹脂凈化提銦后,變?yōu)榧儍舻母吆熑芤海熀坎坏陀?00g/L,化學(xué)反應(yīng)方程式如下:InR3(org)+3HCl=InCl3+3HR(org)⒁在反鐵段,則用5~7N的HCl作為反萃劑采用兩段反萃鐵的工藝將鐵反下,變成富鐵液,富鐵液中的Fe3+含量不低于70g/L,化學(xué)反應(yīng)方程式如下:FeR3(org)+3HCl=FeCl3+3HR(org)⒂在鹽酸再生工序中,純凈的InCl3富銦溶液可以采用鹽酸再生技術(shù)直接與水反應(yīng)生成高純In2O3并再生鹽酸,其化學(xué)反應(yīng)方程式如下:2InCl3+3H2O=In2O3+6HCl⒃純凈的FeCl3富鐵溶液可以采用鹽酸再生技術(shù)直接與水反應(yīng)生成高純Fe2O3并再生鹽酸,其化學(xué)反應(yīng)方程式如下:2FeCl3+3H2O=Fe2O3+6HCl⒄來(lái)自于反銦段的富銦液分別用樹脂提取In3+和Fe3+等離子后,是純凈的含ZnCl2的溶液,這個(gè)溶液在反銦段循環(huán)使用后,ZnCl2含量會(huì)產(chǎn)生富集,在保持反銦需用的1~2N濃度的ZnCl2含量后,多余的ZnCl2則采用鹽酸再生技術(shù)生成ZnSO4·7H2O和回收鹽酸,化學(xué)反應(yīng)方程式如下:ZnCl2+H2SO4+7H2O=ZnSO4·7H2O+2HCl⒅在無(wú)錳鋅電積工序中,反鋅段產(chǎn)生的富鋅液,分別經(jīng)過(guò)一段樹脂除油、兩段活性碳除油,將溶液中可溶性油控制在1ppm以下,進(jìn)行電積提鋅,其化學(xué)反應(yīng)方程式如下:陰極反應(yīng):Zn2++2e=Zn,陽(yáng)極反應(yīng):2OH--2e=1/2O2+H2O⒆鋅電積后產(chǎn)生的電鋅貧液又返回到分流共萃工序的反鋅段用作反萃劑。采用Air+SO2混合氧化除鐵錳技術(shù),通過(guò)控制其中一段常壓浸出的終點(diǎn)pH值在3.0~3.5,可以有效地抑制銦和鐵的浸出,同時(shí)有色固廢渣中含有少量的金屬硫化物也可以被氧化浸出;采用高壓高酸氧浸可以選擇性的強(qiáng)化In3+、Zn2+等離子的浸出,抑制Sn2+、As2+等離子的浸出,使90%的Fe3+離子以Fe2O3形態(tài)沉淀(其它5%的Fe3+離子以FeOOH形態(tài)沉淀);而通過(guò)控制另一段常壓浸出的終點(diǎn)pH值~2,則可以讓In3+、Zn2+等離子共同浸出。鎘錳凈化工序中,首先采用鋅粉除鎘工藝可以除去溶液中的Cd2+離子,同時(shí),也進(jìn)一步將Cu2+、Ni2+、Co2+、Bi2+、Sn2+等多種金屬離子沉淀凈化;其次采用Air+SO2混合氧化除鐵錳技術(shù)能將溶液中的循環(huán)Mn2+離子除去70%;此工序的重要作用是將Cd2+、Mn2+等易于浸出卻難以消除的金屬離子從溶液中分別除去,達(dá)到溶液能夠不斷循環(huán)使用,而有害金屬離子卻不再富集的作用。銦鋅鐵分流共萃工序中,首先,In3+和Fe3+兩種離子共萃的條件是必須控制溶液的酸度[H2SO4]在0~180g/L之間;In3+和Zn2+兩種離子或者In3+、Fe3+和Zn2+三種離子共萃的條件必須是控制溶液的pH值在0.5~2.5之間;其次,上述的共萃條件也是不同溶液進(jìn)行分流的條件,不同的分流溶液按共萃的要求分別進(jìn)入到萃取系統(tǒng);第三,分流共萃是由銦鐵共萃段、銦鋅鐵共萃段、水洗段、酸洗段、反鋅段、反銦段、反鐵段、洗氯段等組成;第四,各種段的萃取、反萃或洗滌的級(jí)數(shù)根據(jù)溶液所含不同金屬離子的成份,分別選擇在3~8級(jí)之間;第五,反鐵段采用了兩段循環(huán)返鐵,可以將Fe3+離子濃度富集到70g/L以上。鹽酸再生工序中,InCl3、FeCl3在采用鹽酸再生技術(shù)后,分別生成了In2O3、Fe2O3兩種高純氧化物和再生鹽酸;ZnCl2在采用鹽酸再生技術(shù)后,生成了ZnSO4·7H2O和再生鹽酸。鹽酸再生工序解決了分流共萃反銦段中的含金屬氯化物廢水零排放的難題;萃取除鐵與鹽酸再生技術(shù)實(shí)現(xiàn)了無(wú)縫對(duì)接,浸出鐵消耗的酸經(jīng)過(guò)銦鐵共萃段得以再生循環(huán),而鐵也經(jīng)過(guò)鹽酸再生技術(shù)變成了附加值很高的Fe2O3產(chǎn)品,解決了濕法冶金中形成鐵渣污染物的工業(yè)化難題。無(wú)錳鋅電積工序中,首先是來(lái)自于分流共萃工序反鋅段的反鋅富液,除鋅以外的各類金屬雜質(zhì)含量均小于1ppm以下;其次是電鋅貧液作為反萃劑,不斷地與分流共萃工序反鋅段進(jìn)行循環(huán)反萃,產(chǎn)生高純的反鋅富液用于鋅電積工序;第三是分流共萃工序與無(wú)錳鋅電積工序之間形成了一個(gè)封閉的溶液循環(huán)體系,借助這個(gè)體系,Zn2+離子則通過(guò)分流共萃工序進(jìn)入,又通過(guò)無(wú)錳鋅電積工序以鋅金屬的形式析出;第四是有少部分電鋅貧液開路至分流共萃工序酸洗段,用以維持在分流共萃工序與無(wú)錳鋅電積工序之間形成的這個(gè)封閉溶液循環(huán)體系中的雜質(zhì)金屬含量控制在1ppm以下。本發(fā)明中的任何一個(gè)工序,均不加入鈉堿或鈉鹽。進(jìn)一步,在一段加壓浸出和兩段常壓逆流浸出工序中,采用固體原料與液體原料逆流相向的分段浸出方式。逆流分段浸出的優(yōu)勢(shì)在于可以完全利用分流共萃時(shí)產(chǎn)生的酸,以這些酸作為浸出劑,逐級(jí)最大化地實(shí)現(xiàn)有色固廢渣中的有價(jià)金屬的浸出率。進(jìn)一步,所述的負(fù)載有機(jī)相運(yùn)行到反鋅段,通過(guò)反鋅前液或電積貧液將負(fù)載有機(jī)相中的鋅全部反萃下來(lái),得到的反鋅后液去無(wú)錳鋅電積工序;在無(wú)錳鋅電積工序中,所述的反鋅后液經(jīng)過(guò)一段樹脂除油將可溶性有機(jī)物控制在10ppm以內(nèi),再經(jīng)兩段活性碳除油將可溶性有機(jī)物控制在1ppm以內(nèi)。進(jìn)一步,經(jīng)無(wú)錳鋅電積工序得到的電鋅貧液作為反鋅前液,返回到銦鋅鐵分流共萃工序的反鋅段中。進(jìn)一步,所述的負(fù)載有機(jī)相運(yùn)行到反銦段,通過(guò)反銦前液將負(fù)載有機(jī)相中的銦全部反萃下來(lái),得到的反銦后液去鹽酸再生工序。進(jìn)一步,在鹽酸再生工序中,反銦后液通過(guò)樹脂提銦吸附銦離子,用鹽酸將吸附銦離子的樹脂反洗再生,銦離子進(jìn)入富銦后液中,富銦后液進(jìn)行鹽酸再生,產(chǎn)出In2O3產(chǎn)品,并再生鹽酸,再生的鹽酸去反銦前液和用于樹脂反洗再生。進(jìn)一步,通過(guò)樹脂提銦得到的提銦余液然后進(jìn)行樹脂提鐵,用鹽酸將吸附鐵離子的樹脂反洗再生,鐵離子進(jìn)入富鐵后液中,富鐵后液進(jìn)行鹽酸再生,產(chǎn)出氧化鐵產(chǎn)品,并再生鹽酸,再生的鹽酸去反鐵一段后液和洗氯后液。進(jìn)一步,通過(guò)樹脂提鐵得到的提鐵后液加入硫酸,進(jìn)行鹽酸再生,產(chǎn)出高純ZnSO4·7H2O產(chǎn)品,并再生鹽酸,再生的鹽酸去反銦前液和用于樹脂反洗再生;濃縮的結(jié)晶母液大部分循環(huán)使用,小部分返回到反銦前液再循環(huán)。進(jìn)一步,所述的負(fù)載有機(jī)相運(yùn)行到反鐵二段和反鐵一段,通過(guò)反鐵前液將負(fù)載有機(jī)相中的鐵全部反萃下來(lái),得到的反鐵二段后液進(jìn)行鹽酸再生,產(chǎn)出氧化鐵產(chǎn)品,并再生鹽酸,再生的鹽酸去反鐵一段后液和洗氯后液。進(jìn)一步,所述的負(fù)載有機(jī)相運(yùn)行到洗氯段,洗氯前液將負(fù)載有機(jī)相中夾帶的氯離子全部反萃下來(lái),得到的洗氯后液作為反鐵一段前液使用,反鐵一段前液經(jīng)反鐵一段后得到的反鐵一段后液作用反鐵二段前液使用。本發(fā)明具有的有益效果:(1)實(shí)現(xiàn)了工業(yè)水零排放,完全的閉路循環(huán);(2)沒(méi)有造成污染的工業(yè)鐵渣(與傳統(tǒng)的濕法冶金所產(chǎn)生的大量有污染的工業(yè)鐵渣相比);(3)零成本提取銦金屬;(4)酸的循環(huán)再生與利用;(5)相對(duì)于傳統(tǒng)的濕法冶金生產(chǎn)方式具有輔料消耗低、能耗低、運(yùn)行成本低、金屬收率高等優(yōu)勢(shì)。附圖說(shuō)明下面結(jié)合說(shuō)明書附圖和具體實(shí)施方式對(duì)本發(fā)明作進(jìn)一步說(shuō)明。圖1為本發(fā)明的一段加壓和兩段常壓逆流浸出工序流程圖。圖2為本發(fā)明的鎘錳凈化工序流程圖。圖3為本發(fā)明的銦鋅鐵分流共萃工序流程圖。圖4為本發(fā)明的鹽酸再生工序流程圖。圖5為本發(fā)明的無(wú)錳鋅電積工序流程圖。具體實(shí)施方式本發(fā)明的一段加壓和兩段常壓逆流浸出工序流程如圖1所示:在鋅浸二段,來(lái)自于銦鋅鐵分流共萃工序的含酸共萃余液與有色固體廢渣、Air+SO2混合氣體在反應(yīng)器里進(jìn)行充分混合,控制pH值3~3.5,T=45~55℃,常壓浸出后,將礦漿在鋅浸二段濃密設(shè)備中進(jìn)行液固分離,分離出來(lái)的鋅浸二段上清液去鎘錳凈化工序;而鋅浸二段底流則進(jìn)入鋅浸一段與含酸的萃鋅余液在反應(yīng)器里充分混合浸出,控制pH值1~2.5,T=45~55℃,常壓浸出后,將礦漿在鋅浸一段濃密設(shè)備中進(jìn)行液固分離,分離出來(lái)的鋅浸一段上清液進(jìn)行精濾,要求ss≤1ppm;而鋅浸一段底流則進(jìn)入一段加壓浸出,控制T=150~200℃,P=1.2~1.8Mpa,[H2SO4]=100~180g/L,通入氧氣,并使鋅浸一段底流與銦鋅鐵分流共萃工序的含酸共萃余液充分混合,保持合適的浸出時(shí)間,然后將加壓浸出后的礦漿在濃密設(shè)備中進(jìn)行液固分離,分離出的固體經(jīng)過(guò)濾洗滌后變成可銷售的鉛產(chǎn)品;而分離出的加壓上清液進(jìn)行精濾,要求ss≤1ppm;精濾后的鋅浸一段上清液和加壓上清液分別進(jìn)入銦鋅鐵分流共萃工序的銦鋅共萃段段和銦鐵共萃。在一段加壓和兩段常壓逆流浸出工序中,(1)利用有色固體廢渣中的金屬氧化物成分起到了酸度的調(diào)節(jié)作用;在與Air+SO2混合氣體常壓浸出的過(guò)程中,pH控制在3~3.5,除鋅外,鐵與其它金屬均在這里被抑制浸出,來(lái)自于銦鋅鐵分流共萃工序的共萃余液中的酸得到了很好的利用,但Cd2+、Mn2+等離子開路出來(lái),需要在鎘錳凈化工序去除;而在另一個(gè)常壓浸出的過(guò)程中,pH控制在1~2.5,鋅、鐵、銦等金屬被浸出,來(lái)自于銦鋅鐵分流共萃工序的共萃余液中的酸再次得到了很好的利用;(2)循環(huán)浸出液中鋅濃度的控制起到關(guān)鍵的承上啟下的作用,P204萃取劑的濃度決定了鋅的遷移量,本發(fā)明中循環(huán)浸出液中鋅的濃度控制在15~50g/L;(3)加壓浸出的工藝控制條件為:有氧條件下,T=150~200℃,P=1.2~1.8Mpa,[H2SO4]=100~180g/L;這個(gè)條件是選擇性浸出In3+、Zn2+離子的關(guān)鍵條件,除Cd2+、Mn2+等離子外,其它雜質(zhì)幾乎被抑制住。本發(fā)明的鎘錳凈化工序流程如圖2所示:鋅浸二段上清液與鋅粉進(jìn)行二段置換反應(yīng)除鎘,將鎘等金屬離子從溶液中沉淀下來(lái);礦漿經(jīng)過(guò)除鎘濃密設(shè)備進(jìn)行液固分離,分離后的除鎘底流經(jīng)過(guò)濾洗滌后成為可銷售的粗鎘產(chǎn)品;而分離后的除鎘上清液與Air+SO2混合氣體在反應(yīng)器里充分混合氧化除錳,控制pH值為<4或5~7,T=~50℃,反應(yīng)一段時(shí)間后,將除錳后的礦漿在除錳濃密設(shè)備中進(jìn)行液固分離,分離后的除錳底流經(jīng)過(guò)濾洗滌后成為可銷售的錳產(chǎn)品;而分離后的除錳上清液進(jìn)行精濾,求ss≤1ppm,精濾后的除錳上清液進(jìn)入銦鋅鐵分流共萃工序的萃鋅段。在鎘錳凈化工序中,(1)大量的工業(yè)化試驗(yàn)已經(jīng)證明,Cd2+、Mn2+等離子無(wú)論在硫酸鹽還是氯化鹽體系均有良好的浸出率,因此,Cd2+、Mn2+等離子在溶液中循環(huán)富集是影響分流共萃技術(shù)使用的一個(gè)重要因素;(2)Cd2+離子采用鋅粉除去是工業(yè)化普遍使用的方法,但Mn2+離子在溶液中作為雜質(zhì)的去除卻是非常困難,控制溶液pH值,采用Air+SO2混合氣體氧化除錳是本發(fā)明中獨(dú)特的辦法,Mn2+離子在這個(gè)過(guò)程中會(huì)被除去~70%,主要工藝控制條件如下:T=30~50℃,pH<4或pH=5~7;(3)經(jīng)過(guò)此工序,Cd2+、Mn2+等離子在溶液中可反復(fù)循環(huán)但不會(huì)富集。本發(fā)明的銦鋅鐵分流共萃工序流程如圖3所示:分別來(lái)自于一段加壓和兩段常壓逆流浸出工序的三種溶液:精濾后加壓上清液、精濾后一段上清液和除錳精濾后液,根據(jù)這三種溶液不同的酸度,則依次分別進(jìn)入銦鋅鐵分流共萃工序的銦鐵共萃段、銦鋅共萃段和萃鋅段,In3+、Zn2+、Fe3+等離子進(jìn)入有機(jī)相中,分別產(chǎn)生了銦鐵共萃余液、銦鋅共萃余液和萃鋅余液。銦鐵共萃余液大部分返回加壓浸出進(jìn)行循環(huán),很少部分進(jìn)入鋅浸二段開路富集的鎘、錳等金屬離子;銦鋅共萃余液則全部返回到鋅浸二段;萃鋅余液則全部返回到鋅浸一段。三種負(fù)載有機(jī)相匯流到一起,負(fù)載有機(jī)相先經(jīng)過(guò)水洗段洗去有機(jī)相中機(jī)械夾帶的氯、氟等離子,再經(jīng)過(guò)酸洗段洗下萃上的銅、錳等金屬離子;負(fù)載有機(jī)相運(yùn)行到反鋅段,電解貧液將有機(jī)相中的鋅全部反萃下來(lái),使鋅濃度滿足可以進(jìn)行電積的要求;負(fù)載有機(jī)相運(yùn)行到反銦段,反銦前液將有機(jī)相中的銦全部反萃下來(lái),富集銦離子的濃度達(dá)到100g/L以上;負(fù)載有機(jī)相運(yùn)行到反鐵段,反鐵前液將有機(jī)相中的鐵全部反萃下來(lái),經(jīng)過(guò)兩段循環(huán)反鐵,使鐵離子的濃度達(dá)到70g/L以上;負(fù)載有機(jī)相運(yùn)行到洗氯段,洗氯前液將有機(jī)相中夾帶的氯離子全部洗下來(lái),不會(huì)在萃取段與分流料液混合時(shí),把氯根帶入溶液循環(huán)體系。在銦鋅鐵分流共萃工序中,(1)銦鐵共萃的工藝條件如下:Fe3+<40g/L,In3+~5g/L,[H2SO4]=100~180g/L;在這個(gè)條件下,F(xiàn)e3+、In3+離子被同時(shí)萃取進(jìn)入有機(jī)相;(2)銦鋅共萃的工藝條件如下:Zn2+=15~50g/L,In3+~5g/L,pH=1~3.5;在這個(gè)條件下,Zn2+、In3+離子被同時(shí)萃取進(jìn)入有機(jī)相;(3)反鋅的工藝條件如下:Zn2+30~90g/L,[H2SO4]=160~220g/L;(4)反銦的工藝條件如下:ZnCl2=1~2N,[HCl]=2~4N;(5)反鐵的工藝條件如下:[HCl]=5~7N;(6)根據(jù)不同的萃取料液情況設(shè)計(jì)了不同的萃取段,這是分流共萃新工藝的一個(gè)核心思想;(7)有機(jī)相共用了水洗段、酸洗段、反鋅段、反銦段、反鐵段、洗氯段;(8)萃取段(銦鐵共萃段、銦鋅共萃段、鋅萃取段等)、水洗段、酸洗段、反鋅段、反銦段、反鐵段、洗氯段是一個(gè)依次不可顛倒的順序,要實(shí)現(xiàn)分流共萃新工藝,缺一不可;(9)反鐵段采用的兩段反鐵結(jié)合鹽酸再生技術(shù),其目的是利用循環(huán)反萃的方法將Fe3+的濃度富集超過(guò)70g/L以上。本發(fā)明的鹽酸再生工序流程如圖4所示:反銦后液中含有In3+、Fe3+、Zn2+等金屬離子,溶液經(jīng)過(guò)樹脂后將In3+吸附后,提銦余液中剩下Fe3+、Zn2+等金屬離子;用HCl將吸附In3+離子的樹脂反洗再生后,樹脂可繼續(xù)用于反銦后液的處理,而In3+離子全部進(jìn)入到富銦后液中,富銦后液經(jīng)鹽酸再生技術(shù)處理后,產(chǎn)出高純In2O3產(chǎn)品,并再生鹽酸。提銦余液過(guò)樹脂后將Fe3+吸附后,提鐵后液中只剩下Zn2+離子;用HCl將吸附Fe3+離子的樹脂反洗再生后,樹脂可繼續(xù)用于提銦余液的處理,而Fe3+離子全部進(jìn)入到富鐵后液中,富鐵后液與反鐵二段后液混合后經(jīng)鹽酸再生技術(shù)處理后,產(chǎn)出高純Fe2O3產(chǎn)品,并再生鹽酸。在提鐵后液中加入硫酸,并控制溫度,經(jīng)過(guò)鹽酸再生技術(shù)處理后,產(chǎn)出高純ZnSO4·7H2O產(chǎn)品,并再生鹽酸,濃縮的結(jié)晶母液(ZnCl2)大部分返回到SSC鹽酸再生技術(shù)系統(tǒng)循環(huán)使用,小部分返回到反銦前液再循環(huán)。再生的鹽酸則分別返回到樹脂再生、反銦段的反銦前液、反鐵一段后液及反鐵段的洗氯后液中循環(huán)使用。在鹽酸再生工序中,(1)形成的FeCl3廢酸液通過(guò)鹽酸再生技術(shù)可以生成用于制作軟磁材料的高純Fe2O3產(chǎn)品,并且再生鹽酸可以返回到分流共萃工序的反鐵段循環(huán)使用,這是目前任何一個(gè)萃取工藝都無(wú)法做到的;(2)傳統(tǒng)的高純In2O3產(chǎn)品都是采用4N的精銦經(jīng)過(guò)電解、真空蒸餾、再電解達(dá)到6N的金屬銦后,再用酸溶解,并且用堿沉淀后變成氫氧化銦烘干煅燒而成,本發(fā)明中使用樹脂提銦后的富銦溶液(InCl3溶液)通過(guò)鹽酸再生技術(shù)可以直接生成高純In2O3,大幅度降低生產(chǎn)成本;(3)提銦后的含氯化鋅的廢酸液采用鹽酸再生技術(shù),生成了高純的七水硫酸鋅產(chǎn)品,再生的鹽酸又可返回到反銦前液中使用。本發(fā)明的無(wú)錳鋅電積工序流程如圖5所示:反鋅后液經(jīng)過(guò)一段樹脂除油將可溶性有機(jī)物控制在10ppm以內(nèi),再經(jīng)兩段活性碳除油將可溶性有機(jī)物控制在1ppm以內(nèi),此時(shí)的溶液可以進(jìn)入電解槽中進(jìn)行電解,控制合適的槽電壓、電流密度及電流,可以產(chǎn)出0#鋅產(chǎn)品,電鋅貧液則返回到銦鋅鐵分流共萃工序的反鋅段循環(huán)使用。在無(wú)錳鋅電積工序中,(1)鋅電解液中Mn2+離子含量低于1ppm,徹底顛覆了傳統(tǒng)鋅電解中依靠Mn2+離子保護(hù)鉛陽(yáng)極的技術(shù)思想;(2)經(jīng)過(guò)鋅電積產(chǎn)生的電鋅貧液返回到分流共萃工序的反鋅段循環(huán)使用;(3)鋅電解液中的雜質(zhì)含量均小于1ppm以下;(4)電鋅貧液有少許部分會(huì)返回到分流共萃工序的酸洗段,以確保鋅電解循環(huán)液中的雜質(zhì)含量均小于1ppm以下;(5)采用一段樹脂、兩段活性碳除油的方式,使鋅電解液中的可溶性有機(jī)物必須低于1ppm,以防止電解時(shí)燒板。