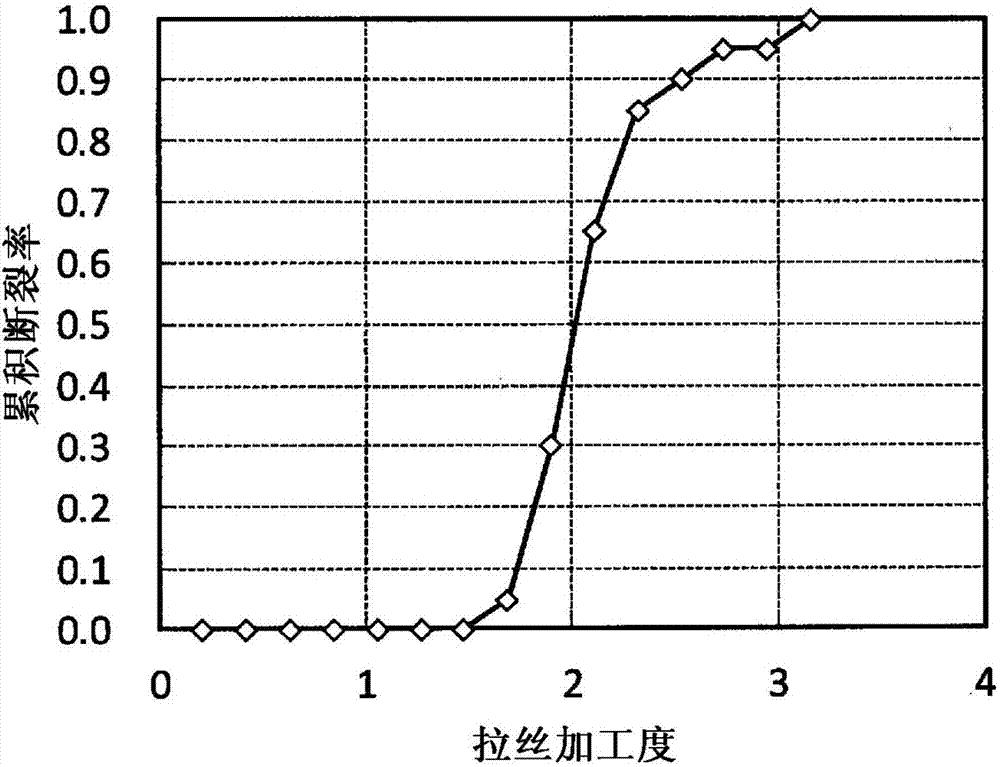
本發(fā)明涉及在拉絲后在輸電線用線纜、吊橋用線纜等各種鋼纜等中所使用的高碳鋼線材。
背景技術(shù):
:對于在輸電線用線纜、吊橋用線纜、各種鋼纜等中所使用的高碳鋼線材,在拉絲后有高強(qiáng)度、高延性的基礎(chǔ)上,從生產(chǎn)率的觀點(diǎn)出發(fā)謀求良好的拉絲加工性。從這樣的要求出發(fā),至今開發(fā)了各種高品質(zhì)的高碳線材。例如,專利文獻(xiàn)1中,提出了由于基于ti的添加的固溶n量的降低和基于固溶ti的應(yīng)變時(shí)效的降低而得到良好的拉絲加工性的技術(shù)。此外,專利文獻(xiàn)2中,提出了通過將滲碳體形態(tài)控制為球狀化,從而得到低強(qiáng)度和良好的拉絲加工性的技術(shù)。專利文獻(xiàn)3中,提出了通過確定鋼材中的c、si、mn、p、s、n、al以及o的各含量并且控制第二相鐵素體面積率和珠光體片層間距,從而得到斷線不易發(fā)生并且可以抑制模具磨耗使模具壽命延長的拉絲加工性優(yōu)異的線材的技術(shù)。專利文獻(xiàn)4中,提出了c:0.6~1.1%的高碳鋼線材,其是如下的高延性的高碳鋼線材:95%以上由珠光體組織形成,熱軋線材的中心部的通過ebsp裝置測定得到的珠光體的珠光體塊粒徑的最大值為45μm以下且平均值為10~25μm。現(xiàn)有技術(shù)文獻(xiàn)專利文獻(xiàn)專利文獻(xiàn)1:特開2012-097300號公報(bào)專利文獻(xiàn)2:特開2004-300497號公報(bào)專利文獻(xiàn)3:特開2007-327084號公報(bào)專利文獻(xiàn)4:特開2008-007856號公報(bào)技術(shù)實(shí)現(xiàn)要素:發(fā)明要解決的問題然而,若根據(jù)本發(fā)明人等的實(shí)驗(yàn),則即便采用上述各技術(shù),在超過1300mpa的高強(qiáng)度材料的情況下,也未必能夠得到通過ti的添加、固溶n的降低而使拉絲加工性改善的明確的效果。此外,對于球狀化熱處理而言,拉絲后的強(qiáng)度低,不適于作為高碳鋼線的用途。本發(fā)明是鑒于這樣的實(shí)際情況而成的,以提供成為用于得到強(qiáng)度高、拉絲加工性良好的鋼線的原材料的鋼線材為課題。用于解決問題的方案本發(fā)明為成為高強(qiáng)度的鋼線的原材料的高碳鋼線材,其主旨如以下所述。(1)一種高碳鋼線材,其為熱軋后的高碳鋼線材,鋼成分以質(zhì)量%計(jì)含有c:0.60~1.10%、si:0.02~2.0%、mn:0.1~2.0%、cr:0.3~1.6%、al:0.001~0.05%,將n限制為0.008%以下、將p限制為0.020%以下、將s限制為0.020%以下,余量為fe以及不可避免的雜質(zhì),該高碳鋼線材的組織以在與線材長度方向垂直的截面中的面積率計(jì)95%以上為珠光體,前述珠光體的平均片層間距為50~100nm,與線材長度方向垂直的截面的自中心開始的直徑相對于線材的直徑d為d/2的圓以內(nèi)的區(qū)域即中心部的珠光體塊徑的平均值為5μm<珠光體塊徑<15μm。(2)根據(jù)(1)的高碳鋼線材,其中,在與線材長度方向垂直的截面的自表層開始500μm以內(nèi)的區(qū)域即外周部,珠光體組織中的鐵素體的晶體取向<110>的集聚度為1.3以上。(3)根據(jù)(1)的高碳鋼線材,其中,以質(zhì)量%計(jì)進(jìn)一步含有mo:0.01~0.2%。(4)根據(jù)(1)的高碳鋼線材,其中,以質(zhì)量%計(jì)進(jìn)一步含有nb:0.01~0.2%、v:0.01~0.2%之中的1種或2種。(5)根據(jù)(1)的高碳鋼線材,其中,以質(zhì)量%計(jì)進(jìn)一步含有b:0.0003~0.003%。(6)根據(jù)(1)的高碳鋼線材,其中,si:0.02~1.0%。(7)根據(jù)(1)的高碳鋼線材,其中,珠光體塊徑的平均值規(guī)定為5μm<珠光體塊徑<12μm。發(fā)明的效果根據(jù)本發(fā)明,可以提供具有1300mpa以上的拉伸強(qiáng)度、并且延性高的高碳鋼線材等,在產(chǎn)業(yè)上的貢獻(xiàn)極其顯著。附圖說明圖1為示出在與線材長度方向垂直的截面中的中心部a和外周部b的圖。圖2為示出拉絲對數(shù)應(yīng)變(真歪)和累積斷裂率的關(guān)系的圖。具體實(shí)施方式本發(fā)明人等為了解決上述那樣的問題,對于鋼線材的組織以及熱處理方法反復(fù)進(jìn)行各種調(diào)查·研究。其結(jié)果,得到下述(a)~(b)的見解。(a)cr的添加促進(jìn)原γ粒徑的微細(xì)化,使相變后的珠光體塊徑微細(xì)化。(b)在線材的中心部a(規(guī)定)中所觀察到的珠光體塊徑的平均值越細(xì),拉絲加工性越良好。(c)在與線材長度方向垂直的截面的外周部b(規(guī)定)中所觀察到的鐵素體晶體取向的<110>方位集合的情況下,拉絲中的晶體旋轉(zhuǎn)變得更少,因此可以抑制由剪切應(yīng)力導(dǎo)致的空隙的發(fā)生。鋼線材的線材長度方向的鐵素體晶體取向以及珠光體的塊徑從中心到表層有不同的分布。圖1表示與線材長度方向垂直的截面中的中心部a和外周部b。在本說明書中,如該圖1所示,將相對于直徑dmm的線材從中心開始的直徑為1/2d的圓以內(nèi)的區(qū)域定義為中心部a,將從表層開始的500μm以內(nèi)的區(qū)域定義為外周部b。對于珠光體塊徑,可以將圖1的中心部a設(shè)為測定位置,通過電子背散射(electronbackscatterdiffraction,稱為ebsd)法來測定。例如,利用膠態(tài)二氧化硅顆粒對與線材長度方向垂直的截面進(jìn)行鏡面研磨,在徑向的中心部附近進(jìn)行利用ebsd法的測定,制成鐵素體晶體取向的圖。例如,在映射區(qū)域?yàn)槊?邊為500μm以上的矩形區(qū)域進(jìn)行,以像素形狀配置為正六邊形元素、測定間隔為0.5μm間隔來進(jìn)行。線材長度方向的鐵素體晶體取向<110>的集聚度可以通過將圖1的外周部b設(shè)為測定位置,將各個(gè)像素的晶體取向標(biāo)記在{110}極圖上來測定。更詳細(xì)而言,鐵素體晶體取向<110>的集聚度可以利用ebsd法的測定結(jié)果而生成{110}極圖,對所得到的極圖進(jìn)行織構(gòu)(texture)解析等來測定。對于集聚度,將晶體取向無規(guī)的情況設(shè)為1,以強(qiáng)度比來表示。此外,若通過ebsd法鑒定鐵素體晶體取向,則各個(gè)六邊形狀像素給予鐵素體的晶體取向的情報(bào),其結(jié)果,鄰接的像素的邊界定義晶體取向的角度差的情報(bào)。像在二個(gè)像素間的邊界具有9°以上的鐵素體晶體取向傾角差且與其鄰接的像素邊界也為9°以上那樣,具有9°以上的傾角差的像素邊界連續(xù)的情況下,將它們連接而定義為珠光體塊晶界。在從像素的三重點(diǎn)延伸的像素邊界均為9°以上的情況下,珠光體塊晶界分支。像素邊界的晶體取向差為9°以上的條件在途中間斷的情況下,該像素邊界不被視為珠光體塊晶界而無視。根據(jù)以上的思考方式,在整個(gè)矩形區(qū)域定義具備9°以上的鐵素體方位差的像素邊界,像素邊界包圍一個(gè)封閉的區(qū)域的情況下,將該區(qū)域定義為一個(gè)珠光體塊,將像素邊界定義為珠光體塊晶界。如此操作,在鐵素體晶體取向的圖上示出珠光體塊晶界,測定珠光體的塊徑。其中,所定義的珠光體塊的一粒由25個(gè)像素以下構(gòu)成的情況下,作為噪音來處理而無視。其中,珠光體塊和珠光體瘤意義相同。此外,珠光體為層狀珠光體。對于片層間距可以通過如下從而求出:用硝酸化乙醇腐蝕液腐蝕與線材長度方向垂直的截面,使用sem,對于在以倍率10000倍進(jìn)行拍攝的視野內(nèi)片層間距最小的位置,垂直地劃線為5個(gè)片層間距,將5個(gè)片層間距的長度除以5。需要說明的是,用sem的拍攝在10個(gè)視野以上進(jìn)行,各視野中所求出的片層間距除以視野數(shù),從而得到平均值。對于拉絲加工性,將長度10m的試驗(yàn)材料浸漬于鹽酸而去除氧化皮,水洗后實(shí)施磷酸鹽覆膜處理,進(jìn)行干式拉絲加工來評價(jià)。拉絲加工可以使用具有拉拔模入口(整體)角度20°、定徑(ベアリング)長度為孔徑的0.3倍左右的形狀的wc-co超硬合金制模具來進(jìn)行。拉絲速度設(shè)為50m/分鐘,可以使用以硬脂酸鈉以及硬脂酸鈣為主體的干式拉絲潤滑劑。不發(fā)生斷線的情況下,為了使截面減少率為20%而減小模具孔徑,至發(fā)生斷線為止進(jìn)行拉絲加工。總計(jì)的斷線次數(shù)為20次時(shí)終止評價(jià),由試驗(yàn)材料的線徑(拉絲開始前的線徑)d0和發(fā)生斷線的模具孔徑d根據(jù)下式而求出拉絲加工度。拉絲加工度(ε)=2×ln(d0/d)各個(gè)拉絲加工度下,發(fā)生斷裂的次數(shù)除以20(總試驗(yàn)數(shù))而求出斷裂率,其加上至此為止的累積斷裂率,求出各拉絲加工度下的累積斷裂率。圖2為判斷拉絲加工性為良好的作為基準(zhǔn)的線材卷的試驗(yàn)結(jié)果。拉絲加工度為1.7時(shí),斷裂次數(shù)為1次,縱軸的累積斷裂率為0.05(1/20)。拉絲加工度為1.9時(shí),斷裂次數(shù)為5次而斷裂率為0.25,加上此前(拉絲加工度1.7)的累積斷裂率0.05時(shí),累積斷裂率為0.3。并且,20次試驗(yàn)中拉絲加工度成為最大時(shí),累積斷裂率成為1.0。本發(fā)明中,從圖表中求出累積斷裂率成為0.5的拉絲加工度,定義為拉絲加工性。如圖2所示,判斷拉絲加工性為良好的作為基準(zhǔn)的線材卷的拉絲加工性為2.23。進(jìn)而,累積斷裂率為0.9的拉絲加工率為3.0,累積斷裂率為1.0的拉絲加工率為3.12。因此,本發(fā)明中,將拉絲加工性為2.23以上評價(jià)為良好,更優(yōu)選拉絲加工性為2.53以上,進(jìn)一步優(yōu)選將拉絲加工性為2.95以上評價(jià)為良好。(對于鋼線材)接著,對于本發(fā)明的鋼線材的成分進(jìn)行說明。需要說明的是,涉及成分的%為質(zhì)量%。<對于成分>cc為使組織成為珠光體,提高強(qiáng)度的元素。c量不足0.60%時(shí),晶界鐵素體等非珠光體組織生成而損害拉絲加工性,極細(xì)鋼線的拉伸強(qiáng)度也降低。另一方面,c量超過1.10%時(shí),先共析滲碳體等非珠光體組織生成,拉絲加工性劣化。因此,c量限定為0.60~1.10%的范圍。優(yōu)選將c量設(shè)為0.65%以上。sisi為用于鋼的脫氧的元素,也有助于固溶強(qiáng)化。為了得到效果,添加0.02%以上的si。優(yōu)選將si量設(shè)為0.05%以上。另一方面,si量超過2.0%時(shí),在熱軋工序中容易產(chǎn)生表面脫碳,因此將上限設(shè)為2.0%。優(yōu)選將si量設(shè)為1.0%以下,更優(yōu)選設(shè)為0.5%以下。mnmn為用于脫氧、脫硫的元素,添加0.1%以上。另一方面,mn量超過2.0%時(shí),珠光體相變顯著延遲,鉛浴淬火處理的時(shí)間變長,因此將mn量設(shè)為2.0%以下。mn量優(yōu)選為1.0%以下。crcr為使原γ粒徑微細(xì)化、使珠光體組織微細(xì)的元素,也有助于高強(qiáng)度化。為了得到效果,添加0.3%以上的cr。另一方面,cr量超過1.6%時(shí),先共析滲碳體析出,使拉絲加工性降低,因此將上限設(shè)為1.6%。優(yōu)選設(shè)為1.3%以下。更優(yōu)選設(shè)為1.0%以下。alal為具有脫氧作用的元素,對于使鋼中的氧量降低是必要的。然而,al含量不足0.001%時(shí),難以得到該效果。另一方面,al容易形成硬質(zhì)的氧化物系夾雜物,特別是,al含量超過0.05%時(shí),粗大的氧化物系夾雜物的形成變得顯著,因此拉絲加工性的降低顯著。因此,將al的含量設(shè)為0.001~0.05%。更優(yōu)選下限為0.01%以上,更優(yōu)選上限為0.04%以下。nn為在冷拉絲加工中固著于位錯(cuò)而提高鋼線的強(qiáng)度,反而使拉絲加工性降低的元素。特別是,n含量超過0.008%時(shí),拉絲加工性的降低變得顯著。因此,將n含量限制為0.008%以下。更優(yōu)選為0.005%以下。pp在鋼中容易偏析,偏析時(shí),顯著延遲共析相變,因此,共析相變未完成,容易形成硬質(zhì)的馬氏體。為了防止該問題,將p含量限制為0.02%以下。ss大量地存在時(shí),大量地形成mns,使鋼的延性降低,因此限制為0.020%以下。更優(yōu)選為0.01%以下。momo的添加是任意的。若添加,則具有提高鋼線材的拉伸強(qiáng)度的效果。為了得到該效果,期望添加0.02%以上的mo。然而,mo的含量超過0.20%時(shí),馬氏體組織容易生成,拉絲加工性降低。因此,mo的含量優(yōu)選為0.02~0.20%。更優(yōu)選為0.08%以下。vv的添加是任意的。若添加,則在鋼線材中形成碳氮化物,減小珠光體塊徑,提高拉絲加工性。為了得到該效果,期望添加0.02%以上的v。然而,v的含量超過0.20%時(shí),存在粗大的碳氮化物容易生成,拉絲加工性降低的情況。因此,v的含量優(yōu)選為0.02~0.20%。更優(yōu)選為0.08%以下。nbnb的添加是任意的。若添加,則在鋼線材中形成碳氮化物,減小珠光體塊徑,提高拉絲加工性。為了得到該效果,期望添加0.002%以上的nb。然而,nb的含量超過0.05%時(shí),存在粗大的碳氮化物容易生成,拉絲加工性降低的情況。因此,nb的含量優(yōu)選為0.002~0.05%。更優(yōu)選為0.02%以下。titi的添加是任意的。若添加,則在鋼線材中形成碳化物或氮化物,減小珠光體塊徑,提高拉絲加工性。為了得到該效果,期望添加0.002%以上的ti。然而,ti的含量超過0.05%時(shí),容易形成粗大的碳化物或氮化物,存在拉絲加工性開始降低的情況。因此,優(yōu)選將ti的含量設(shè)為0.02~0.05%。更優(yōu)選為0.03%以下。bb的添加是任意的。若添加,則鋼線材中的固溶n形成為bn,降低鋼中的固溶n,提高拉絲加工性。為了得到該效果,期望添加0.0003%以上的b。然而,b的含量超過0.003%時(shí),存在容易生成粗大的氮化物,拉絲加工性降低的情況。因此,b的含量優(yōu)選為0.0003~0.003%。更優(yōu)選為0.002%以下。<對于金相組織>接著,對于本發(fā)明的鋼線材的金相組織進(jìn)行說明。面積率先共析鐵素體、先共析滲碳體等非珠光體組織在最終拉絲中成為發(fā)生龜裂的原因。在本發(fā)明的實(shí)施方式中,為了提高拉絲加工性,將珠光體的面積率設(shè)為95%以上。余量為先共析鐵素體、先共析滲碳體等非珠光體組織。需要說明的是,上述的金相組織可如下來確定:將相對于線材長度方向垂直地切斷線材的截面切取為樣品,鏡面研磨之后,用掃描電子顯微鏡進(jìn)行觀察。此外,各金相組織的面積率可以根據(jù)由掃描電子顯微鏡觀察的結(jié)果使用測面積法或計(jì)點(diǎn)法而求出。優(yōu)選的是,觀察倍率,例如設(shè)為1000倍以上,觀察的面積,例如設(shè)為1000μm2以上。例如用計(jì)點(diǎn)法確定面積率時(shí),優(yōu)選將測定點(diǎn)設(shè)為200點(diǎn)以上。珠光體的塊徑如上述見解那樣,珠光體的塊徑(以下,也稱為珠光體塊徑)大于15μm時(shí),拉絲加工性降低,因此設(shè)為15μm以下。更優(yōu)選為12μm以下。此外,珠光體塊徑設(shè)為5μm以下時(shí),非珠光體組織增加,因此將5μm設(shè)為下限。鐵素體晶體取向<110>的集聚度鐵素體晶體取向<110>集聚于與線材長度方向垂直的截面的外周部時(shí),可以抑制拉絲加工中的方位旋轉(zhuǎn),抑制基于剪切變形的空隙形成。本發(fā)明中,該效果突顯的、鐵素體晶體取向<110>的集聚度設(shè)為1.3以上。優(yōu)選為1.5以上、更優(yōu)選為1.7以上。需要說明的是,珠光體塊徑以及鐵素體晶體取向<110>的集聚度可以利用如上述那樣的ebsd法來確定。片層間距本發(fā)明中的金相組織以珠光體為主體,目標(biāo)是使該鋼線材的拉伸強(qiáng)度為1300mpa以上、優(yōu)選為1350mpa以上、更優(yōu)選為1400mpa以上。為了得到該強(qiáng)度,后述的實(shí)施例中示出的珠光體的平均片層間距需要為100nm以下。此外,珠光體的平均片層間距不足50nm時(shí),除珠光體以外的貝氏體組織混合存在,不能得到目標(biāo)強(qiáng)度,并且拉絲加工硬化率降低,因此將下限設(shè)為50nm。<對于鋼線材的制造方法>接著,對于本發(fā)明的鋼線材的制造方法以具體的例子進(jìn)行說明。需要說明的是,以下的說明只不過是用于說明本發(fā)明的例子,并不限定本發(fā)明的范圍。本發(fā)明的鋼線材通過常規(guī)方法來熔煉具有上述的成分的鋼,進(jìn)行鑄造,對于所得到的鋼坯實(shí)施熱軋來制造。熱軋為將鋼坯加熱到1150℃左右來進(jìn)行。熱軋的精軋溫度為740~880℃。在精軋后為了發(fā)生珠光體相變,用強(qiáng)制風(fēng)冷、噴霧冷卻、水冷等手段以25℃/秒~40℃/秒冷卻至達(dá)到550℃~650℃為止(一次冷卻),在該溫度范圍下保持30秒~180秒之后,用氣冷、水冷的手段以2℃/秒以上冷卻至300℃(二次冷卻),用放冷等手段冷卻至室溫。需要說明的是,線材的直徑只要可以確保在制成鋼線時(shí)必要的加工硬化,則沒有特別限定。熱軋的精軋溫度高于880℃時(shí),原γ粒徑的微細(xì)化效果變少,因此設(shè)為880℃以下。此外,不足740℃下進(jìn)行軋制時(shí),軋制中會析出先共析鐵素體,因此將下限設(shè)為740℃。一次冷卻下的冷卻速度不足25℃/秒時(shí),原γ粒徑粗大化,因此將下限設(shè)為25℃/秒。超過40℃/秒的冷卻在實(shí)際制造中是困難的,因此設(shè)為40℃/秒以下。保持溫度超過650℃時(shí),原γ粒徑粗大化并且強(qiáng)度降低,因此將上限設(shè)為650℃。此外,不足550℃時(shí),非珠光體組織增加,因此將下限設(shè)為550℃。保持時(shí)間不足30秒時(shí),珠光體相變未完成,非珠光體組織增加,因此將下限設(shè)為30秒。此外,超過180秒的保持引起生產(chǎn)率的惡化、片層珠光體的形狀崩塌而引起線材強(qiáng)度的降低,因此將上限設(shè)為180秒。2次冷卻中,在300℃以上的溫度范圍進(jìn)行爐冷等不足2℃/秒的緩慢冷卻時(shí),引起強(qiáng)度的降低,因此將至300℃為止的二次冷卻速度的下限設(shè)為2℃/秒。需要說明的是,不需理會從300℃到室溫為止的冷卻速度。實(shí)施例以下,一邊示出實(shí)施例一邊對于本發(fā)明的實(shí)施方式所述的鋼線材以及鋼線材的制造方法具體地說明。需要說明的是,以下示出的實(shí)施例僅是本發(fā)明的實(shí)施方式中所述的鋼線材以及鋼線材的制造方法的一個(gè)例子,本發(fā)明所述的鋼線材以及鋼線材的制造方法并不限于下述的例子。對于表1中示出的成分組成的高碳鋼熱軋線材,通過改變表2中示出的熱軋條件,從而制作相同的是為珠光體組織,但中心部的珠光體塊徑、表層部的鐵素體晶體取向<110>集聚度、拉伸強(qiáng)度各不相同的線材。用拉絲加工臨界應(yīng)變評價(jià)這些線材。在表3中示出該結(jié)果。[表1]鋼種csimncralmobnbvtia0.820.20.50.50.029-----發(fā)明鋼b1.070.050.11.20.028-----發(fā)明鋼c0.621.51.50.30.0040.1----發(fā)明鋼d0.920.20.50.50.045-0.002---發(fā)明鋼e1.080.050.50.80.030--0.010.1-發(fā)明鋼f0.830.150.20.70.035----0.03發(fā)明鋼g0.920.050.50.10.004-----比較鋼h0.820.22.50.50.018-----比較鋼i1.350.050.510.022-----比較鋼[表2][表3]在以下說明這些高碳鋼線材的具體的制造方法。如成為表1中示出的線材的化學(xué)成分那樣,用轉(zhuǎn)爐熔煉,將該鋼塊初軋,制作155mm見方的中小型鋼坯,加熱到1150℃左右后,在軋制的終止溫度為740℃~880℃的范圍進(jìn)行熱軋,得到直徑10mm的線材。對于上述熱軋終止后的線材,通過設(shè)置在軋制生產(chǎn)線上的冷卻帶,立刻用噴嘴噴射冷卻水冷卻到550℃~650℃的范圍。此時(shí),改變水量和水冷時(shí)間,控制達(dá)到溫度。此外,接著通過強(qiáng)制風(fēng)冷將線材以5℃/秒~25℃/秒的冷卻速度冷卻至650℃~550℃的范圍。之后在該溫度范圍保持60秒左右,從而完成珠光體相變,通過氣冷而冷卻至室溫。分別測定這些鋼線材的珠光體面積率(%)、珠光體塊徑、片層間距、鐵素體晶體取向、拉伸強(qiáng)度。珠光體面積率如下求出,對于切斷線材而得到的橫截面進(jìn)行鏡面研磨的試樣,用硝酸和乙醇的混合液蝕刻,用2000倍觀察線材的表面和中心之間的中央部從而求出。對于珠光體塊徑以及片層間距,在鋼線材的中心5mm的范圍中62500μm2的區(qū)域測定。鐵素體取向<110>集聚度使用tsl公司制的ebsd測定裝置,在距表層500μm以內(nèi)的范圍中62500μm2的區(qū)域測定。拉伸試驗(yàn)基于jisz2241來進(jìn)行。對于拉絲加工性,如上所述,進(jìn)行干式拉絲加工,將總計(jì)的斷線次數(shù)設(shè)為20次,制作拉絲對數(shù)應(yīng)變和累積斷裂率的關(guān)系的圖,以累積斷裂率為50%的拉絲對數(shù)應(yīng)變來評價(jià)。在表3中示出結(jié)果。pbs為珠光體塊徑的平均。no.10的保持溫度高,因此片層間距大、拉伸強(qiáng)度不足。no.11的cr量低,珠光體塊徑的微細(xì)化不充分,因此拉絲加工臨界應(yīng)變變小。no.12的mn量多,珠光體相變未完成,珠光體面積率非常小,因此拉絲加工臨界應(yīng)變變小。no.13的c量高,先共析滲碳體生成,因此珠光體面積率小,拉絲加工臨界應(yīng)變變小。no.14的保持時(shí)間短,在珠光體相變完成前進(jìn)行二次冷卻,因此珠光體面積率小,拉絲加工臨界應(yīng)變變小。no.15的一次冷卻速度小、原γ粒徑粗大化,因此珠光體塊徑大,拉絲加工臨界應(yīng)變變小。no.16的保持時(shí)間長,片層珠光體的形狀崩塌,拉伸強(qiáng)度不足。no.17的精軋溫度低、先共析鐵素體大量生成,拉伸強(qiáng)度不足,并且拉絲加工臨界應(yīng)變變小。no.18的精軋溫度高、原γ粒徑粗大化,因此珠光體塊徑大,拉絲加工臨界應(yīng)變變小。no.19的二次冷卻速度小,片層珠光體的形狀崩塌,拉伸強(qiáng)度降低。當(dāng)前第1頁12