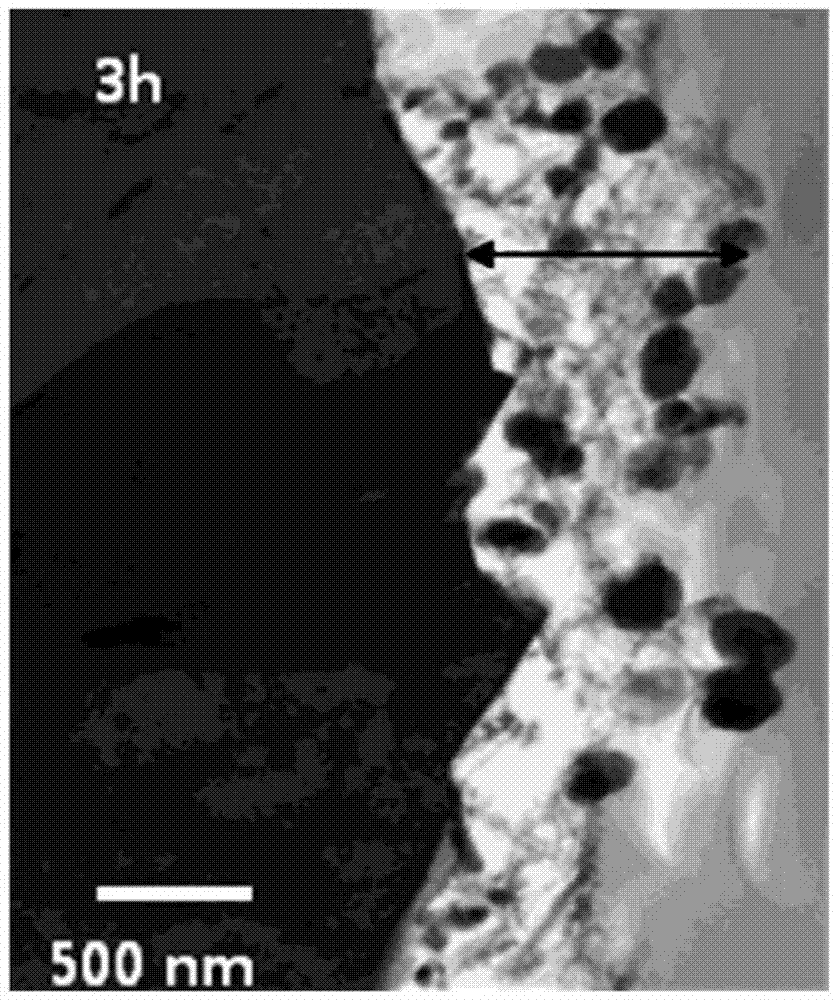
本發(fā)明涉及一種用作火力發(fā)電廠、鍋爐、管道、熱交換器等的材料的鋼板,具體涉及一種耐硫酸腐蝕性及琺瑯粘著力優(yōu)異的鋼板及其制造方法。
背景技術(shù):通過燃燒化石燃料獲得能量的鍋爐等設(shè)備在化石燃料燃燒之后產(chǎn)生的排放氣體中存在大量NOX(氮氧化物)、SOX(二氧化硫、三氧化硫(SO2、SO3))等,鍋爐等的在高溫下排放的氣體在向大氣排放之前會經(jīng)過高爐脫氮設(shè)備、脫硫設(shè)備等多個凈化設(shè)備,由此在排放到大氣之前排放氣體的溫度就會下降。此時,當(dāng)包含所述SOX(二氧化硫、三氧化硫(SO2、SO3))等的排放氣體的溫度低于硫酸的露點(DEWPOINT)時,發(fā)生硫酸以露水形態(tài)冷凝到鋼材表面的硫酸冷凝腐蝕現(xiàn)象,以造成嚴(yán)重的腐蝕環(huán)境,由此在采用鋼材的部件上引發(fā)嚴(yán)重的缺陷。作為對上述問題的應(yīng)對方案有采用將易腐蝕的普通熱軋鋼板使用在上述部件上,在腐蝕之后短期內(nèi)持續(xù)更換部件的方法,或者使用高價的鎳(Ni)基高合金鋼或不銹鋼(STS)鋼種來抑制腐蝕的方法,或者使用價位稍微低廉的銅(Cu)基耐腐蝕鋼的方法等。但是,使用普通熱軋鋼板的前一個方法,因熱軋鋼板的部件制造成本及更換成本的壓力而幾乎不使用,而使用Ni基或不銹鋼基高耐腐蝕鋼的方法不僅存在對腐蝕的危險性,而且是高價的元素,在經(jīng)濟(jì)上存在不利的一面,因此目前限制使用。因此,最近針對頻繁經(jīng)受這種硫酸冷凝腐蝕的材料采用添加了Cu的碳鋼,該碳鋼比普通的熱軋鋼板具有20倍以上的腐蝕延遲時間,具有與Ni基高合金鋼或不銹鋼相比價格低廉的優(yōu)點。這種鋼板稱之為耐硫酸冷凝腐蝕鋼板。除上述的方法以外,還有通過利用琺瑯鋼板在鋼板表層鍍覆美麗的琺瑯層,將琺瑯層的耐蝕/磨損特性和普通鋼的優(yōu)異的成型、硬度特性應(yīng)用在要求具備耐蝕性的部件上的方法。另外,上述的耐硫酸冷凝腐蝕鋼板由于直接在硫酸冷凝氛圍下使用,因此在水分多或溫度低的環(huán)境,即硫酸的冷凝現(xiàn)象頻繁產(chǎn)生的環(huán)境下具有腐蝕速度快的缺點,與高耐腐蝕鋼相比,在很多情況下都無法使用。另外,在相對惡劣的腐蝕環(huán)境下使用的琺瑯鋼板,具有當(dāng)琺瑯層因磨損、碰撞、魚鱗(fishscale)的生成、粘著力不良等原因從鋼板的表面脫落時,由普通鋼組成的母材迅速發(fā)生腐蝕的問題等。因此,需要開發(fā)一種在惡劣的硫酸冷凝氛圍下使用琺瑯鋼板時,即使琺瑯層脫落也能夠防止母材迅速腐蝕的材料。專利文獻(xiàn)1:日本公開專利第2005-054246號
技術(shù)實現(xiàn)要素:(一)要解決的技術(shù)問題本發(fā)明的一方面提供一種在確保琺瑯粘著力的同時,針對硫酸冷凝腐蝕具有優(yōu)異的耐蝕性的鋼板及其制造方法。(二)技術(shù)方案本發(fā)明的一個方面,提供一種耐硫酸腐蝕性及琺瑯粘著力優(yōu)異的鋼板,以重量%計,包括:碳(C):0.04~0.10%、錳(Mn):0.05~0.50%、硅(Si):0.05%以下、鋁(Al):0.1%以下、磷(P):0.02%以下、硫(S):0.03~0.07%、銅(Cu):0.05~0.20%、鎳(Ni):0.02~0.20%、鈦(Ti):0.06~0.15%、銻(Sb):0.05~0.20%、鈷(Co):0.02~0.07%、氮(N):0.006%以下、余量為Fe及其他不可避免的雜質(zhì)。本發(fā)明的另一方面,提供一種耐硫酸腐蝕性及琺瑯粘著力優(yōu)異的鋼板的制造方法,包括以下步驟:準(zhǔn)備滿足上述組成成分的鋼坯;將準(zhǔn)備好的所述鋼坯在1150℃以上的溫度下進(jìn)行再加熱;將已再加熱的所述鋼板進(jìn)行粗軋后,通過在Ar3以上的溫度下進(jìn)行熱終軋,由此制造熱軋鋼板;將所述制造的熱軋鋼板在500℃以上的溫度下進(jìn)行卷??;將卷取的所述鋼板以75~90%的壓下率進(jìn)行冷軋,由此制造冷軋鋼板;以及將所述冷冷軋鋼板在650~850℃的溫度下進(jìn)行連續(xù)退火。(三)有益效果根據(jù)本發(fā)明,耐硫酸腐蝕性及琺瑯特性均優(yōu)異,從而能夠適用于要求同時具備耐蝕性及琺瑯性的材料。特別是,本發(fā)明的鋼板即使受惡劣的腐蝕環(huán)境的影響而使琺瑯層脫落時,因母材的優(yōu)異的耐蝕特性,與現(xiàn)有的琺瑯鋼板相比具有優(yōu)異的耐蝕性。附圖說明圖1是示出用透射電子顯微鏡(TEM)觀察本發(fā)明的一個方面的發(fā)明鋼的剖面的圖。圖2是示出將本發(fā)明的一個方面的發(fā)明鋼暴露在硫酸腐蝕環(huán)境中,并用透射電子顯微鏡觀察其剖面的圖(用箭頭表示的部分為Cu凝聚層,3h表示浸漬三個小時)。具體實施方式本發(fā)明人針對提供適于惡劣的硫酸冷凝腐蝕環(huán)境的琺瑯鋼板,為了開發(fā)所述琺瑯鋼板的琺瑯層即使受到腐蝕環(huán)境的影響而發(fā)生脫落時也能夠防止母材腐蝕的材料而進(jìn)行了深入的研究,結(jié)果發(fā)現(xiàn)通過適當(dāng)調(diào)配有利于耐蝕性的一些成分的同時,優(yōu)化鋼的制造條件,能夠提供在惡劣的腐蝕環(huán)境下耐硫酸腐蝕性優(yōu)異的鋼板,從而完成了本發(fā)明。而且,當(dāng)利用能夠有效地吸留根據(jù)腐蝕環(huán)境有可能從外部等流入的氫的析出物時,不僅琺瑯的粘著力優(yōu)異,而且具有防止發(fā)生破壞琺瑯層的魚鱗的缺陷的效果。下面,對本發(fā)明進(jìn)行詳細(xì)說明。根據(jù)本發(fā)明的一個方面的耐硫酸腐蝕性及琺瑯粘著力優(yōu)異的鋼板,以重量%計,優(yōu)選包含:碳(C):0.04~0.10%、錳(Mn):0.05~0.50%、硅(Si):0.05%以下、鋁(Al):0.1%以下、磷(P):0.02%以下、硫(S):0.03~0.07%、銅(Cu):0.05~0.20%、鎳(Ni):0.02~0.20%、鈦(Ti):0.06~0.15%、銻(Sb):0.05~0.20%、鈷(Co):0.02~0.07%、氮(N):0.006%以下。下面,詳細(xì)說明如上所述限定本發(fā)明的鋼板成分的理由。此時,如無另作記載,成分元素的含量均表示重量%。C:0.04~0.10%碳(C)是為確保鋼的硬度而添加的元素。在本發(fā)明中為了通過形成硫化鈦(TiS)析出物以外,還形成碳化鈦(TiC)或Ti(C、S)復(fù)合析出物來作為吸留氫的位置(site)使用,優(yōu)選地,包含適當(dāng)含量的C。當(dāng)C的含量小于0.04%時,由于鋼內(nèi)析出的Ti基碳化物及復(fù)合碳化物的量極少,因此具有不僅吸留氫的效果不夠充分,而且鋼的硬度也會降低的問題。相反,當(dāng)C的含量超過0.10%時,由于鋼內(nèi)的固溶碳含量增加,在冷卻的過程中形成硬質(zhì)相,而且鋼的硬度變得過高,從而在冷軋等過程中可能引起問題。因此,在本發(fā)明中優(yōu)選地,將C的含量限定在0.04~0.10%,更為優(yōu)選地,將其含量限定在0.06~0.08%。Mn:0.05~0.50%錳(Mn)雖起到通過鋼中的固溶強(qiáng)化提高硬度的作用,但是Mn的含量過高時,有可能會形成粗大的硫化錳(MnS),在這種情況下,反而會存在降低硬度的問題。當(dāng)所述Mn的含量小于0.05%時,無法期待充分的硬度增加的效果,相反,當(dāng)Mn的含量超過0.05%時,由于形成中心偏析區(qū),有可能在熱軋時發(fā)生缺陷。因此,在本發(fā)明中優(yōu)選地,將Mn的含量限定在0.05~0.50%,更為優(yōu)選地,將其含量限定在0.1~0.3%。Si:0.05%以下硅(Si)雖是起脫氧作用的元素,但在本發(fā)明中使用鋁(Al)代替Si,以獲得脫氧效果,因此,優(yōu)選地,將Si的含量控制在低含量。當(dāng)這種Si的含量超過0.05%時,由于固溶強(qiáng)化效果,存在鋼的硬度過度增加的問題,在本發(fā)明中優(yōu)選地,將Si的含量限定在0.05%以下,更為優(yōu)選地,將其含量可限定在0.02%以下。Al:0.1%以下(0除外)鋁(Al)是制造鋁鎮(zhèn)靜(Al-killed)鋼時必須添加的元素,為達(dá)到脫氧效果,優(yōu)選地添加適當(dāng)?shù)腁l。只是,當(dāng)所述Al的含量超過0.1%時,不僅提高引發(fā)鋼板的表面缺陷的可能性,而且也會降低焊接性。因此,在本發(fā)明中優(yōu)選地,將Al的含量限定在0.1%以下,更為優(yōu)選地,將其含量限定在0.02~0.06%。P:0.02%以下磷(P)是制造鋼的過程中不可避免地被摻雜的雜質(zhì),當(dāng)所述P的含量過高時,具有偏析到晶界而引發(fā)常溫下的脆性的問題,因此,優(yōu)選地,將P的含量控制在低含量。即使在制造鋼的過程中進(jìn)行脫磷處理,一般鋼中也會存在0.005%以上的P,當(dāng)這種P的含量超過0.02%時,會存在上述的問題。因此,在本發(fā)明中優(yōu)選地,將P的含量限定在0.02%以下,考慮到制鋼工序中的負(fù)荷,可包含0.005%以上的P,更為優(yōu)選地,將其含量限定在0.005%~0.015%。S:0.03~0.07%在本發(fā)明中硫(S)是與鈦(Ti)一起充當(dāng)為防止魚鱗缺陷而形成TiS析出物的元素。當(dāng)這種S的含量小于0.03%時,由于TiS析出物無法充分地形成,琺瑯處理后具有發(fā)生魚鱗缺陷的危險,相反,S的含量超過0.07%時,由于形成硫化亞鐵(FeS),具有引發(fā)高溫脆性的問題。因此,在本發(fā)明中優(yōu)選地,將S的含量限定在0.03~0.07%,更為優(yōu)選地,將其含量限定在0.04~0.06%。Cu:0.05~0.20%在本發(fā)明中銅(Cu)是在遇到惡劣的硫酸冷凝腐蝕環(huán)境時,起到凝聚在表面層上并形成Cu納米晶體(nano-crystal)的作用,因此是在惡劣的硫酸環(huán)境下也具有耐蝕性的非常重要的元素。當(dāng)這種Cu的含量小于0.05%時,無法形成充分的凝聚層,因此具有在硫酸環(huán)境下無法具備耐蝕性的問題,相反,當(dāng)Cu的含量超過0.20%時,存在硬度大幅增加,琺瑯粘著力降低的問題。因此,在本發(fā)明中優(yōu)選地,將Cu的含量限定在0.05~0.20%,更為優(yōu)選地,將其含量限定在0.07~0.13%。Ni:0.02~0.20%在本發(fā)明中鎳(Ni)是為防止因所述銅(Cu)的低的液化溫度而有可能形成的液體金屬脆化(liquidmetalembrittlement,LME)現(xiàn)象而添加的元素。當(dāng)這種Ni的含量小于0.02%時,無法充分地確保上述效果,相反,當(dāng)Ni的含量超過0.20%時,不僅上述的效果飽和,而且還具有耐蝕性降低、由高價元素導(dǎo)致的產(chǎn)品價格上升的問題。因此,在本發(fā)明中優(yōu)選地,將Ni的含量限定在0.02~0.20%。Ti:0.06~0.15%在本發(fā)明中鈦(Ti)是起到形成TiS、TiC、Ti(C、S)等多種析出物的作用的元素。當(dāng)這種Ti的含量小于0.06%時,由于無法充分形成所述析出物,因此在琺瑯處理后有可能發(fā)生魚鱗缺陷,相反,當(dāng)Ti的含量超過0.15%時,由于形成過量的TiC,因此具有由析出強(qiáng)化而硬度過于增加的問題。這種情況下,會阻礙鋼的成形性,因此不優(yōu)選。因此,在本發(fā)明中優(yōu)選地,將Ti的含量限定在0.06~0.15%,更為優(yōu)選地,將其含量限定在0.07~0.12%。Sb:0.05~0.20%在本發(fā)明中銻(Sb)是起到在硫酸冷凝腐蝕環(huán)境下形成堅固的Cu凝聚層的催化劑作用的元素。當(dāng)這種Sb的含量小于0.05%時,具有無法充分地起到形成堅固的Cu凝聚層的催化劑的作用的問題,相反,當(dāng)Sb的含量超過0.20%時,具有充當(dāng)降低琺瑯粘著力的因素的問題。因此,在本發(fā)明中優(yōu)選地,將Sb的含量限定在0.05~0.20%,更為優(yōu)選地,將其含量限定在0.07~0.13%。Co:0.02~0.07%鈷(Co)是與Sb一起起到形成堅固的Cu凝聚層的催化劑作用的元素,當(dāng)這種Co的含量小于0.02%時,無法充分地確保上述效果,相反,當(dāng)Co的含量超過0.07%時,反而具有琺瑯粘著力降低的問題。因此,在本發(fā)明中優(yōu)選地,將Co的含量限定在0.02~0.07%,更為優(yōu)選地,將其含量限定在0.03~0.06%。N:0.006%以下氮(N)是在鋼中起固溶元素的作用,在高溫下與鈦(Ti)一起形成氮化鈦(TiN)析出物的具有代表性的元素。在本發(fā)明中將所述Ti用于形成如TiS、TiC、Ti(C、S)等析出物,在形成所述析出物之前,重要的是所述Ti盡量以固溶狀態(tài)存在。因此,優(yōu)選地,將用于形成TiN的N的含量盡量控制在低含量。如果,N的含量超過0.006%,由于存在與S或C相結(jié)合的Ti的含量變少的問題,因此不優(yōu)選。因此,在本發(fā)明中優(yōu)選地,將N的含量限定在0.006%以下,更為優(yōu)選地,將其含量限定在0.004%以下。優(yōu)選地,在本發(fā)明中為了更加有利地確保耐硫酸腐蝕性及琺瑯粘著力,被限定為上述的范圍的各種成分的關(guān)系滿足以下的關(guān)系式1至關(guān)系式4。[關(guān)系式1]1≤(Cu/Sb)≤3[關(guān)系式2](Cu/2)≤Ni[關(guān)系式3]Ti/(C+S)≤1[關(guān)系式4]1≤(Ti/S)≤3更為具體地,所述Cu和Sb是在惡劣的硫酸冷凝腐蝕環(huán)境下形成堅固的Cu凝聚層,從而提高鋼的耐蝕性的有利元素,若所述Cu與Sb的比滿足1~3,則能夠充分地獲得本發(fā)明所要達(dá)到的耐蝕效果。如果,Cu與Sb的比小于1,具有無法形成充分的凝聚層的問題,相反,當(dāng)其比值超過3時,由于Cu的含量相對過高,具有硬度大幅增加以及琺瑯粘著力低下的問題,因此不優(yōu)選。而且,在本發(fā)明中為了提高鋼的耐蝕性而添加Cu,并且為防止由所述Cu引起的液體金屬催化現(xiàn)象而添加Ni,此時,若所述Cu和Ni的關(guān)系不滿足所述關(guān)系式2,則會存在引發(fā)液體金屬催化現(xiàn)象或無法充分地確保由Cu帶來的耐蝕效果的問題。而且,在本發(fā)明中Ti、C及S是形成用于吸留氫的析出物的主要元素,若所述Ti、C及S的關(guān)系不滿足上述關(guān)系式3,則由固溶強(qiáng)化導(dǎo)致鋼的硬度大幅增加,或由于無法充分地形成析出物而導(dǎo)致無法充分地吸留鋼中以原子形態(tài)存在的氫,從而在琺瑯處理后有可能會發(fā)生魚鱗缺陷。不僅如此,當(dāng)所述Ti與S的比小于1時,由于形成FeS,有可能發(fā)生高溫脆性,相反,當(dāng)其比值超過3時,由于Ti的含量過高,因此具有鋼的硬度大幅增加的問題。優(yōu)選地,除上述的組成成分以外,其余包含F(xiàn)e及不可避免的雜質(zhì),本發(fā)明的鋼板并不排除添加其他組成成分。所述不可避免的雜質(zhì)是在一般的鋼鐵制造過程中可從原料或周圍環(huán)境無意地被摻入的物質(zhì),因此無法排除。對于一般的鋼鐵制造過程中的技術(shù)人員來說是能夠理解所述不可避免的雜質(zhì)。均滿足上述的成分組成及成分關(guān)系的鋼板包括TiS、TiC及Ti(C、S)析出物中的一種以上,此時,當(dāng)所述析出物在觀察視野范圍內(nèi)在每平方厘米(cm2)分布7×108個以上時,能夠確保不發(fā)生魚鱗缺陷等表面缺陷的同時琺瑯粘著力優(yōu)異的鋼板。按如上所述的分布形成的TiS、TiC及Ti(C、S)析出物中的一種以上的析出物,在熱軋及冷軋時,所述析出物被破碎的同時發(fā)生內(nèi)部龜裂(crack),從而能夠大幅提高所述析出物本身或其周圍的微孔(micro-void)的形成。所述形成的微孔可用作能夠吸收-儲存氫的吸留位置(site)。而且,優(yōu)選地,本發(fā)明的鋼板進(jìn)一步包括琺瑯層,在包括所述琺瑯層的情況下,具備氫的滲透率為800秒/mm2以上,并且琺瑯粘著力指數(shù)為90%以上的優(yōu)異的琺瑯特性。而且,本發(fā)明的鋼板在50重量%的硫酸溶液中的腐蝕損失率為30mg/cm2/hr以下,從而具備優(yōu)異的耐硫酸腐蝕性。況且,當(dāng)遇到惡劣的硫酸冷凝腐蝕環(huán)境時,因鋼板腐蝕而生成的腐蝕生成物銹層中包含的Cu的含量優(yōu)選為10重量%以上,并且包含所述含量的Cu的銹層堅固且不發(fā)生龜裂。下面,詳細(xì)說明本發(fā)明的鋼板的制造方法。下面的制造方法只是表示能夠制造本發(fā)明的鋼板的一個優(yōu)選實施例,本發(fā)明并不限定于此。首先,制造滿足上述成分組成及成分關(guān)系的鋼坯之后,對所述鋼坯進(jìn)行再加熱處理。在進(jìn)行所述再加熱時,當(dāng)溫度低于1150℃時,由于Ti的再固溶不充分,因此無法實現(xiàn)本發(fā)明所要達(dá)到的充分地形成Ti基析出物的目的。因此,優(yōu)選地,在1150℃以上的溫度下進(jìn)行所述再加熱。優(yōu)選地,將所述已再加熱的鋼坯進(jìn)行粗軋后,通過在Ar3以上的溫度下進(jìn)行熱終軋,由此制造熱軋鋼板。當(dāng)所述熱終軋溫度小于Ar3時,由于生成延伸的晶粒,因此具有延伸率大幅下降的問題。因此,當(dāng)進(jìn)行所述熱終軋時,優(yōu)選在Ar3以上的溫度下進(jìn)行,更為優(yōu)選地,可在850~1000℃下進(jìn)行。優(yōu)選地,將所述制造的熱軋鋼板在500℃以上的溫度下進(jìn)行卷取。當(dāng)進(jìn)行所述卷取時的溫度小于500℃時,會形成粗大的碳化物,而且由于形成珠光體相,具有鋼的硬度大幅增加的問題。因此,優(yōu)選地,將所述卷取溫度控制在500℃以上,更為優(yōu)選地,可在500~800℃的溫度下實施。之后,優(yōu)選地,將上述已卷取的熱軋鋼板進(jìn)行冷軋,由此制造冷軋鋼板。在進(jìn)行所述冷軋時,當(dāng)冷軋壓下率小于75%時,由于無法在Ti基析出物周圍形成充分的微孔,因此在進(jìn)行琺瑯處理后有可能會發(fā)生魚鱗缺陷,相反,當(dāng)冷軋壓下率超過90%時,由于加工硬化,具有軋制性及板形狀不良的問題。因此,優(yōu)選地,在進(jìn)行所述冷軋時,將冷軋壓下率控制在75~90%。之后,優(yōu)選地,將所述已制造的冷軋鋼板在650~850℃下進(jìn)行連續(xù)退火處理。當(dāng)進(jìn)行所述連續(xù)退火處理時,若退火溫度小于650℃,則由于無法完成再結(jié)晶,因此很難確保韌性及成型性,相反,若退火溫度超過850℃,則由于轉(zhuǎn)變成兩相區(qū),有可能形成硬質(zhì)相,因此不優(yōu)選。以下,通過實施例對本發(fā)明進(jìn)行更為具體的說明。只是,以下的實施例只是為了更好地說明本發(fā)明而示例的,并不是限定本發(fā)明的權(quán)利要求范圍,本發(fā)明的權(quán)利要求范圍是由權(quán)利要求書中記載的事項和從所述記載的事項合理地推導(dǎo)的事項決定。(實施例1)準(zhǔn)備具有以下表1中示出的組成成分的鋼坯,然后在1200℃的溫度下將所述鋼坯進(jìn)行再加熱,然后在850℃的溫度下進(jìn)行熱終軋,由此制造各熱軋鋼板。在750℃的溫度下,將所述已制造的各熱軋鋼板進(jìn)行卷取,然后以80%冷軋壓下率進(jìn)行冷軋,由此制造冷軋鋼板。之后,在750℃的溫度下,對所述冷軋鋼板進(jìn)行連續(xù)退火處理。之后,為了調(diào)查所述冷軋鋼板的琺瑯特性而準(zhǔn)備琺瑯處理試片,然后實施琺瑯處理。此時,準(zhǔn)備的所述琺瑯處理試片為以50mm×120mm的大小切斷的試片。對所述已準(zhǔn)備的琺瑯處理試片進(jìn)行完全脫脂后,涂布下釉的釉液,在200℃的溫度下干燥10分鐘,以完全去除水分,之后在830℃的溫度下維持7分鐘并實施煅燒處理,然后冷卻至常溫。之后,對已完成下釉琺瑯處理的試片重新涂布上釉的釉液,然后在200℃的溫度下干燥10分鐘,以完全去除水分。將已干燥的試片在800℃的溫度下維持7分鐘,并實施煅燒處理,然后實施空冷式琺瑯處理。此時,將鍛燒爐的氛圍條件為將露點溫度設(shè)置成30℃,以采用最容易發(fā)生魚鱗缺陷的惡劣的條件。之后,將已完成琺瑯處理的試片在200℃的恒溫爐中維持20小時,對魚鱗進(jìn)行加速處理。之后,通過肉眼調(diào)查發(fā)生的魚鱗缺陷數(shù)量。而且,對琺瑯粘著力的評價是通過粘著力試驗儀器(ASTMC313-78規(guī)格的測試設(shè)備)來測量粘度指數(shù)。而且,用于測量已經(jīng)過琺瑯處理的試片的氫滲透率的試驗是按ASTMG31規(guī)格實施,在脫脂的鋼板的相反的一側(cè),將經(jīng)過硫酸電解的氫投入后,在相反的一側(cè)使用電荷耦合器件攝象機(jī)(CCD)得出產(chǎn)生氫所需的時間除以鋼材的厚度的值。將通過上述方法測量的結(jié)果表示在表2中。而且,了解所述冷軋鋼板的硫酸腐蝕特性。此時,銹層中的Cu含量是在70℃的溫度下將試片在50重量%的硫酸(H2SO4)溶液中浸漬一個小時后拿出來,再使用聚焦離子束(FIB,F(xiàn)ocusedIonBeam)切斷包括腐蝕生成物的斷面,然后在所述切斷的試片的母材的正上方(10μm以內(nèi))通過掃描電子顯微鏡(SEM)進(jìn)行元素分析,由此測量相對的元素含量。銹層的龜裂(crack)發(fā)生與否是通過500倍的光學(xué)顯微鏡觀察浸漬在所述硫酸溶液中的試片上表面時,以通過肉眼能夠觀察到的母材的程度來判斷龜裂的形成與否。硫酸腐蝕損失率是浸漬在所述硫酸溶液中的試片除以表面積的值,表示每小時(1h)每單位面積(cm2)的腐蝕損失率。而且,軋制時的龜裂發(fā)生與否是通過判斷最終冷軋時邊緣(edge)部的破裂現(xiàn)象及鋼板斷裂與否來表示的。將通過上述方法測量的結(jié)果表示在表2中。[表1](在上述表1中,‘N*’是將成分范圍的單位以ppm表示的。在上述表1中,成分關(guān)系式1、3及4分別表示從[關(guān)系式1]、[關(guān)系式3]及[關(guān)系式4]得到的值,成分關(guān)系式2中的‘○’表示滿足[關(guān)系式2],‘×’表示不滿足[關(guān)系式2]。)[表2](在上述表2中,銹層的Cu含量是以重量%表示,腐蝕損失率用單位mg/cm2/hr表示。而且,所述銹層龜裂及軋制時的龜裂是表示龜裂的發(fā)生與否。)如上述表1及表2所示,均滿足本發(fā)明的成分組成、成分關(guān)系及制造條件的發(fā)明鋼1至4,在鋼中充分地形成Ti基析出物,并且充分吸留鋼中的氫,從而不會發(fā)生魚鱗缺陷,氫滲透率也表示800秒/mm2的高的氫滲透率,而且琺瑯粘度指數(shù)為100%,從而可確認(rèn)琺瑯特性優(yōu)異。而且,可確認(rèn)在硫酸腐蝕試驗中發(fā)生的銹層中的Cu含量為10%以上,即使琺瑯層腐蝕,所述Cu在腐蝕環(huán)境下起到保護(hù)母材的耐蝕層的作用。相反,對比鋼1,可確認(rèn)由于C的含量不足,無法充分地形成析出物,因此琺瑯處理后發(fā)生魚鱗缺陷,而且氫滲透率為650秒/mm2,比較低,因此可確認(rèn)對于硫酸的耐腐蝕性差。對比鋼2,可確認(rèn)由于Cu的含量不充分,銹層中的Cu含量不足,從而在銹層內(nèi)發(fā)生龜裂,而且腐蝕損失率為350mg/cm2/hr,呈現(xiàn)很高的值。對比鋼3,由于對Cu銹層起到穩(wěn)定化作用的Sb的含量不充分,銹層內(nèi)Cu的含量為5%,比較低,由此得到腐蝕損失率變高的結(jié)果。對比鋼4,可確認(rèn)氫的滲透率為800秒/mm2,但由于鋼中的Cu的含量高,因此表面上生成的厚的Cu凝聚層妨礙琺瑯粘著力,從而發(fā)生魚鱗缺陷。對比鋼5,可確認(rèn)由于幾乎沒有形成Ti基析出物,因此鋼材幾乎無法進(jìn)行氫的吸留,氫滲透率也呈現(xiàn)出比較低的值,而且琺瑯粘著力非常差。對比鋼6,由于C的含量相對低,氫的滲透率呈現(xiàn)為720秒/mm2,并且發(fā)生魚鱗缺陷,琺瑯粘著力也差。對比鋼7,由于鋼中C的含量過高,軋制時軋制負(fù)荷增加,從而在軋制過程中發(fā)生鋼板斷裂。對比鋼8及對比鋼9,可確認(rèn)由于S的含量均比較低,無法充分形成Ti基析出物,因此氫滲透率低,并且發(fā)生魚鱗缺陷。特別是,對比鋼9中Ti的含量也不充分,與對比鋼8相比,所形成的Ti基析出物更少。對比鋼10,為了防止因添加Cu而導(dǎo)致的液體金屬脆化現(xiàn)象而添加的Ni的含量不足,出現(xiàn)Cu的液體脆化,在軋制過程中發(fā)生邊緣結(jié)痂(edgescab)的缺陷。對比鋼11,可得到由于無法充分形成Ti基析出物,不僅氫滲透率無法滿足800秒/mm2以上,而且由于未添加Co,銹層中的Cu的含量為10%,比較低,腐蝕損失率變高的結(jié)果。(實施例2)利用上述表1的發(fā)明鋼1,通過如下表3中所示的制造條件制造各冷軋鋼板。之后,通過與上述實施例1相同的方法實施琺瑯處理,然后確認(rèn)氫滲透率和硫酸腐蝕損失率及軋制時的龜裂與否,并將其結(jié)果表示在表3中。[表3]如上述表3中所述,在加熱溫度低的情況下(1),由于加熱時Ti無法被充分再固溶,Ti基析出物無法充分形成,從而氫滲透率低??纱_認(rèn)在卷取溫度低的情況下(2),軋制后發(fā)生龜裂。而且,可確認(rèn)在退火溫度過高的情況下(3),由于制造之后形成硬質(zhì)相貝氏體和馬氏體,軋制后發(fā)生龜裂。而且,可確認(rèn)在冷軋壓下率低的情況(4),示出氫滲透率低。如上所述,為了同時確保本發(fā)明所要達(dá)到的硫酸耐蝕性及琺瑯特性,不僅要滿足本發(fā)明中所提出的成分組成及成分之間的關(guān)系,而且還要滿足制造條件。另外,圖1是示出用透射電子顯微鏡觀察均滿足本發(fā)明的發(fā)明鋼的剖面的圖。可確認(rèn)形成TiS析出物以及冷軋時從所述析出物形成微孔。所述微孔起到當(dāng)從內(nèi)部流入氫時防止氫的擴(kuò)散,同時吸留所述氫的吸留位置(site)的作用,琺瑯時內(nèi)部氫原子相結(jié)合而形成氫分子(H2),由此產(chǎn)生內(nèi)壓,因此對破壞琺瑯層的魚鱗缺陷具有抵抗性。而且,圖2是示出當(dāng)本發(fā)明的發(fā)明鋼被暴露在硫酸腐蝕環(huán)境中(在70℃下,在50重量%的硫酸(H2SO4)溶液中浸漬3個小時)時,通過透射電子顯微鏡觀察鋼中Cu凝聚在表面而形成凝聚層的情況的圖。如圖2所示,所形成的Cu凝聚層起到在惡劣的硫酸腐蝕環(huán)境下具有耐蝕性的作用。