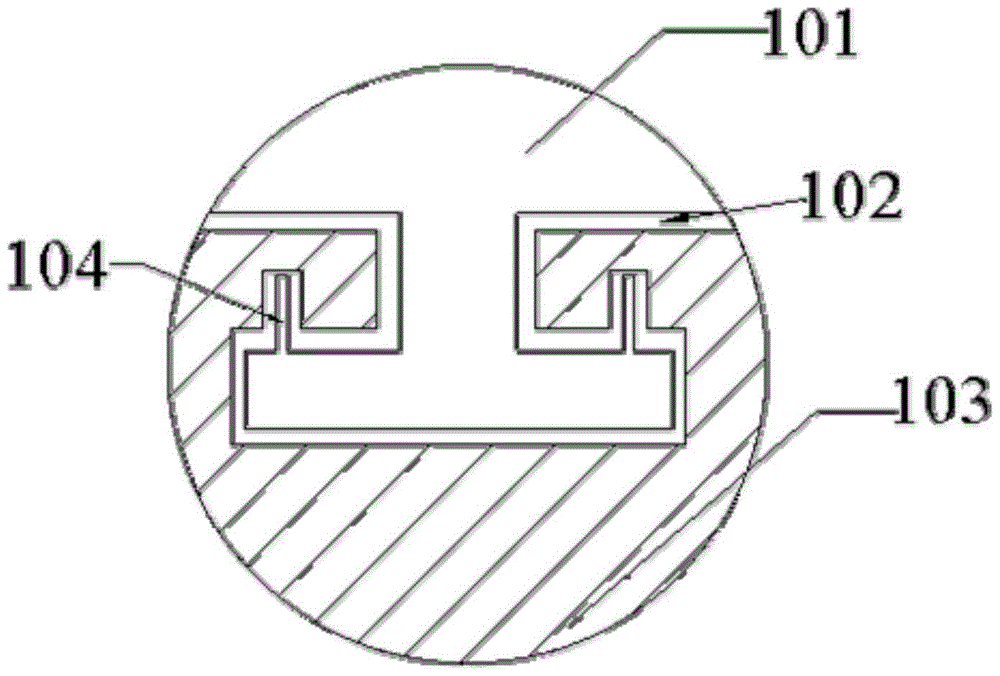
本發(fā)明屬于超硬材料制備領(lǐng)域,特別地涉及一種具有內(nèi)嵌結(jié)構(gòu)的聚晶金剛石復(fù)合片及其制造方法。
背景技術(shù):聚晶金剛石復(fù)合片是一種金剛石聚晶與硬質(zhì)合金基體組成的復(fù)合材料,具有硬度高、耐磨性好的特點?,F(xiàn)有聚晶金剛石-硬質(zhì)合金復(fù)合片通常采用鎢鈷類硬質(zhì)合金作為基體材料,然后在高溫(通常1200~1600℃)、高壓(通常5Gpa以上)的一次合成;也有采用CVD聚晶切割片增強的制造方法,如公開號為102700191A,公開日為2012年10月3日的中國發(fā)明專利ZL201210200657.3。其他,如在硬質(zhì)合金上進(jìn)行CVD或者PVD金剛石或者立方氮化硼、氮化鈦涂層。該技術(shù)已經(jīng)應(yīng)用多年,但該技術(shù)僅僅是為提高硬質(zhì)合金的切削性能,是硬質(zhì)合金性能提升的拓展延續(xù)。采用CVD、PVD處理的金剛石涂層硬質(zhì)合金,主要應(yīng)用在金屬切削方面。地質(zhì)鉆探用材料通常要求材料具有高硬度、高強度,高耐磨性、抗沖擊等好的綜合性能而不是單一性能。采用硬質(zhì)合金進(jìn)行CVD或者PVD處理的材料難以適應(yīng)高性能地質(zhì)鉆探的使用要求,尤其是石油鉆探高鉆探深度的要求,這類鉆探最忌諱井底損壞。鉆探用材料的要求是具有抗沖擊性,一般選用高含鈷量的鎢鈷類硬質(zhì)合金。高含鈷量的硬質(zhì)合金對金剛石聚晶的直接影響就是對金剛石使用過程的反催化,促使金剛石石墨化,從而,降低金剛石聚晶的性能。鎢鈷類硬質(zhì)合金具有強度高、硬度高的特點,但其韌性差、抗沖擊性能差,在地質(zhì)鉆探等場合難以適應(yīng)要求。目前,為改善此類基底硬質(zhì)合金的性能,還集中在添加晶粒細(xì)化劑等研究方向上。隨著市場需求發(fā)展,現(xiàn)聚硬質(zhì)合金-晶金剛石復(fù)合片向大尺寸,高厚度聚晶層發(fā)展,聚晶層厚度目前已經(jīng)達(dá)到4mm。但由于硬質(zhì)合金與金剛石聚晶具有不同的特性,這些材料由于膨脹系數(shù)及溫度等影響,目前在大尺寸,高厚度硬質(zhì)合金-金剛石聚晶復(fù)合片生產(chǎn)上容易產(chǎn)生結(jié)合界面應(yīng)力破壞,從而導(dǎo)致復(fù)合片的界面失效,即復(fù)合片從界面處斷裂分離。采用CVD聚晶母材切割片增強的聚晶復(fù)合片,是制造金剛石聚晶復(fù)合片的另外工藝。采用CVD法可生產(chǎn)大尺寸、高厚度聚晶金剛石母材。但在聚晶金剛石塊體與基底材料的復(fù)合上,目前還鮮有研究。如公開號為102700191A,公開日為2012年10月3日的中國發(fā)明專利ZL201210200657.3公開了一種制造方法,但該方法只是采用簡單的熱壓燒結(jié)工藝,聚晶CVD金剛石增強條與金剛石聚晶微粉之間無法形成有效的C-C共價鍵的化學(xué)鍵結(jié)合,聚晶微粉與微粉之間也未形成有效的C-C共價鍵的化學(xué)鍵結(jié)合,只是簡單的聚晶混合燒結(jié)體,產(chǎn)品性能差是工藝缺陷的必然。另外,將CVD聚晶切割片與金剛石聚晶微粉埋入硬質(zhì)合金粉末中進(jìn)行壓制、燒結(jié),尤其是在氫氣氣氛下進(jìn)行燒結(jié),由于鈷的“反催化”及氫氣的“脫碳”效應(yīng),會顯著降低金剛石聚晶及聚晶復(fù)合片的性能,這種制造方法有待進(jìn)一步提升。采用大尺寸聚晶母材可以利用激光切割成各種現(xiàn)狀的聚晶形狀,但這種形狀難以與基底硬質(zhì)合金進(jìn)行有效復(fù)合。尤其是,當(dāng)需要基底硬質(zhì)合金為不規(guī)則形,特別是帶內(nèi)橫向或縱向、斜向盲孔結(jié)構(gòu)時,更難以形成有效結(jié)合。
技術(shù)實現(xiàn)要素:為解決上述問題,本發(fā)明的目的在于提供一種具有內(nèi)嵌結(jié)構(gòu)的聚晶金剛石復(fù)合片制造方法,硬質(zhì)合金具有內(nèi)盲孔等異形結(jié)構(gòu)同時具有復(fù)合過渡層,減緩或消除金剛石與硬質(zhì)合金材料使用過程鈷反催化效應(yīng),是提高硬質(zhì)合金聚晶復(fù)合片性能的一種有效方法。本發(fā)明又一目的在于提供一種具有內(nèi)嵌結(jié)構(gòu)的聚晶金剛石復(fù)合片,使得金剛石復(fù)合片具有內(nèi)盲孔等異形結(jié)構(gòu)同時具有復(fù)合過渡層。為實現(xiàn)上述目的,本發(fā)明的技術(shù)方案為:一種具有內(nèi)嵌結(jié)構(gòu)的聚晶金剛石復(fù)合片制造方法,包括以下步驟:S10,選用硬質(zhì)合金喂料與過渡層喂料,于頂部設(shè)置有若干倒T型凹槽的模具中進(jìn)行共注射,倒T型凹槽的一字邊兩側(cè)設(shè)置有橫向盲孔,注射壓力為8~82MPa,注射溫度140~200℃,后將注射件脫脂、燒結(jié),燒結(jié)溫度1200~1500℃,時間2~24小時,得含過渡層注射燒結(jié)復(fù)合件;S20,聚晶準(zhǔn)備S201,選用球形微米級金剛石,金剛石微粉粒度為1~40微米,與接合劑進(jìn)行混合球磨;S202,將球形微米級金剛石與接合劑混合球磨產(chǎn)物進(jìn)行真空干燥,干燥溫度500~600℃;S203,將干燥物壓制成聚晶片;S30,聚晶復(fù)合片合成S301,將硬質(zhì)合金基底與聚晶壓制片裝入葉蠟石塊體中;S302,將組裝好的葉蠟石塊體放入六面頂或兩面頂中,逐步加壓致3.1~8.4GPa,通電流加熱,維持5~16min;S303,卸掉載荷,進(jìn)行后續(xù)脫除處理并在聚晶層滲入硅合金即獲得聚晶復(fù)臺片。優(yōu)選地,設(shè)置有盲孔的模具為具有縱向盲孔的模具,注射壓力為8~60MPa。優(yōu)選地,設(shè)置有盲孔的模具為具有橫向盲孔的模具,注射壓力為8~80MPa。優(yōu)選地,設(shè)置有盲孔的模具為具有斜向盲孔的模具,注射壓力為8~82MPa。優(yōu)選地,設(shè)置有盲孔的模具為具有橫向,縱向和斜向三向盲孔的模具,注射壓力為10~82MPa。優(yōu)選地,所述過渡層喂料為無碳氮化物氮化鈦,粘結(jié)劑為水基材料。優(yōu)選地,所述過渡層喂料為無碳氮化物氮化硼,粘結(jié)劑為水基材料。優(yōu)選地,所述過渡層喂料為無碳氮化物氮化鋁,粘結(jié)劑為水基材料。本發(fā)明又一技術(shù)方案為:一種具有內(nèi)嵌結(jié)構(gòu)的聚晶金剛石復(fù)合片,通過上述任一所述的方法獲得,底層為頂部具有倒T型凹槽的硬質(zhì)合金基底層,硬質(zhì)合金基底層頂部的邊緣上為過渡層,過渡層上方為與過渡層形狀互補的金剛石聚晶層,三層結(jié)構(gòu)嵌合形成整體結(jié)構(gòu)。與現(xiàn)有技術(shù)相比,本發(fā)明的有益效果如下:(1)具有更加復(fù)雜的異形孔結(jié)構(gòu),可以進(jìn)一步提高金剛石聚晶與硬質(zhì)合金之間的結(jié)合把持力;(2)消除了產(chǎn)品在使用過程中鈷反催化對產(chǎn)品性能的影響;(3)提高了產(chǎn)品的抗沖擊性能;可以實現(xiàn)大尺寸,高厚度聚晶層因界面結(jié)合應(yīng)力作用而產(chǎn)生的界面斷裂,提高了產(chǎn)品的抗沖擊性能。附圖說明圖1為本發(fā)明實施例1的具有內(nèi)嵌結(jié)構(gòu)的聚晶金剛石復(fù)合片的剖面結(jié)構(gòu)示意圖;圖2為圖1中A部分的放大結(jié)構(gòu)示意圖;圖3為本發(fā)明實施例2的具有內(nèi)嵌結(jié)構(gòu)的聚晶金剛石復(fù)合片的剖面結(jié)構(gòu)示意圖;圖4為圖3中B部分的放大結(jié)構(gòu)示意圖;圖5為本發(fā)明實施例3的具有內(nèi)嵌結(jié)構(gòu)的聚晶金剛石復(fù)合片的剖面結(jié)構(gòu)示意圖;圖6為圖5中C部分的放大結(jié)構(gòu)示意圖;圖7為本發(fā)明實施例4的具有內(nèi)嵌結(jié)構(gòu)的聚晶金剛石復(fù)合片的剖面結(jié)構(gòu)示意圖;圖8為圖7中D部分的放大結(jié)構(gòu)示意圖。具體實施方式為了使本發(fā)明的目的、技術(shù)方案及優(yōu)點更加清楚明白,以下結(jié)合附圖及實施例,對本發(fā)明進(jìn)行進(jìn)一步詳細(xì)說明。應(yīng)當(dāng)理解,此處所描述的具體實施例僅僅用以解釋本發(fā)明,并不用于限定本發(fā)明。相反,本發(fā)明涵蓋任何由權(quán)利要求定義的在本發(fā)明的精髓和范圍上做的替代、修改、等效方法以及方案。進(jìn)一步,為了使公眾對本發(fā)明有更好的了解,在下文對本發(fā)明的細(xì)節(jié)描述中,詳盡描述了一些特定的細(xì)節(jié)部分。對本領(lǐng)域技術(shù)人員來說沒有這些細(xì)節(jié)部分的描述也可以完全理解本發(fā)明。實施例1S10,選用硬質(zhì)合金喂料與氮化硼喂料,于具有倒T型凹槽的模具中進(jìn)行共注射,倒T型凹槽的一字邊兩側(cè)設(shè)置有縱向盲孔,注射壓力為8~60MPa,注射溫度140~200℃,然后將注射件脫脂、燒結(jié),燒結(jié)溫度1200~1500℃,時間2~24小時,得含過渡層的注射燒結(jié)復(fù)合件。S20聚晶金剛石準(zhǔn)備S201,選用球形微米級金剛石,金剛石微粉粒度1~40微米,與接合劑進(jìn)行混合球磨;S202,將混合球磨產(chǎn)物進(jìn)行真空干燥,干燥溫度500~600℃;S203,將干燥物壓制成聚晶片;S30,聚晶金剛石復(fù)合片合成S301,將硬質(zhì)合金基底與聚晶壓制片裝入葉蠟石塊體中;S302,將組裝好的葉蠟石塊體放入六面頂或兩面頂中,逐步加壓致3.2~8GPa,通電流加熱,維持5~12min;S303,卸掉載荷,進(jìn)行后續(xù)脫除處理并在聚晶層滲入硅合金即獲得聚晶復(fù)臺片。參見圖1所示為采用上述方法獲的具有內(nèi)嵌結(jié)構(gòu)的聚晶金剛石復(fù)合片的剖面結(jié)構(gòu)示意圖,圖2為圖1中A部分的局部放大圖,該聚晶金剛石復(fù)合片底層為頂部具有倒T型凹槽的硬質(zhì)合金基底層103,倒T型凹槽的一字邊的兩側(cè)設(shè)置有縱向盲孔104,硬質(zhì)合金基底層頂部的邊緣上為過渡層102,過渡層102上方為與過渡層形狀互補的金剛石聚晶層101,三層結(jié)構(gòu)嵌合形成整體結(jié)構(gòu)。縱向盲孔中的硬質(zhì)合金注射材料起到加強復(fù)合片強度的作用。經(jīng)檢測,與目前市售復(fù)合片比較,磨耗比達(dá)到49.2~52.6萬。產(chǎn)品耐熱性能檢測,產(chǎn)品在750℃焙燒2分鐘后,磨耗比達(dá)49.1~52.5萬。說明產(chǎn)品焙燒前后磨耗比相差不大,在硬質(zhì)合金表面處理后,使用過程金剛石與基底之間未產(chǎn)生石墨化效應(yīng),與通過ZL201210200657.3的方法所得的金剛石聚晶復(fù)合片在同等條件下進(jìn)行比較,性能提高21%。實施例2S10,選用硬質(zhì)合金喂料與氮化鋁喂料,于具有倒T型凹槽的模具中進(jìn)行共注射,倒T型凹槽的一字邊兩側(cè)設(shè)置有橫向盲孔,注射壓力8~80MPa,注射溫度140~200℃,后將注射件脫脂、燒結(jié)。燒結(jié)溫度1200~1480℃,時間2~24小時,得含過渡層注射燒結(jié)復(fù)合件;S20,聚晶準(zhǔn)備S201,選用球形微米級金剛石,金剛石微粉粒度1~40微米,與接合劑進(jìn)行混合球磨;S202,將混合球磨產(chǎn)物進(jìn)行真空干燥,干燥溫度500~600℃;S203,將干燥物壓制成聚晶片;S30,聚晶金剛石復(fù)合片合成S301,將硬質(zhì)合金基底與聚晶壓制片裝入葉蠟石塊體中;S302,將組裝好的葉蠟石塊體放入六面頂或兩面頂中,逐步加壓至3.1~7.8GPa,通電流加熱,維持5~16min;S303,卸掉載荷,進(jìn)行后續(xù)脫除處理并在聚晶層滲入硅合金即獲得聚晶復(fù)臺片。參見圖3所示為采用上述方法獲得具有內(nèi)嵌結(jié)構(gòu)的聚晶金剛石復(fù)合片的剖面結(jié)構(gòu)示意圖,圖4為圖3的B部分的局部放大圖,該聚晶金剛石復(fù)合片底層為頂部具有倒T型凹槽的硬質(zhì)合金基底層103,倒T型凹槽的一字邊的兩側(cè)設(shè)置有橫向盲孔104,硬質(zhì)合金基底層頂部的邊緣上為過渡層102,過渡層102上方為與過渡層形狀互補的金剛石聚晶層101,三層結(jié)構(gòu)嵌合形成整體結(jié)構(gòu)。橫向盲孔中的硬質(zhì)合金注射材料起到加強復(fù)合片強度的作用。經(jīng)檢測,與目前市售復(fù)合片比較,磨耗比達(dá)到48.6~50.2萬。產(chǎn)品耐熱性能檢測,產(chǎn)品在750℃焙燒2分鐘后,磨耗比達(dá)48.4~50.3萬。說明產(chǎn)品焙燒前后磨耗比相差不大,說明,在硬質(zhì)合金表面處理后,使用過程金剛石與基底之間未產(chǎn)生石墨化效應(yīng)。與通過ZL201210200657.3的方法所得的金剛石聚晶復(fù)合片在同等條件下進(jìn)行比較,性能提高18%。實施例3S10,選用硬質(zhì)合金喂料與氮化鋁喂料,于具有倒T型凹槽的模具中進(jìn)行共注射,倒T型凹槽的一字邊兩側(cè)設(shè)置有斜向盲孔,注射壓力8~82MPa,注射溫度150~210℃,后將注射件脫脂、燒結(jié),燒結(jié)溫度為1200~1500℃,時間為2~24小時,得含過渡層注射燒結(jié)復(fù)合件;S20,聚晶金剛石片準(zhǔn)備S201,選用球形微米級金剛石,金剛石微粉粒度1~40微米,與接合劑進(jìn)行混合球磨;S202,將混合球磨產(chǎn)物進(jìn)行真空干燥,干燥溫度500~600℃;S203,將干燥物壓制成聚晶金剛石片;S30,聚晶復(fù)合片合成S301,將硬質(zhì)合金基底與聚晶壓制片裝入葉蠟石塊體中;S302,將組裝好的葉蠟石塊體放入六面頂或兩面頂中,逐步加壓致3.6~8.4GPa,通電流加熱,維持5~12min;S303,卸掉載荷,進(jìn)行后續(xù)脫除處理并在聚晶層滲入硅合金即獲得聚晶復(fù)臺片。參見圖5所示為采用上述方法獲得的具有內(nèi)嵌結(jié)構(gòu)的聚晶金剛石復(fù)合片的剖面結(jié)構(gòu)示意圖,圖6為圖5的C部分的局部放大圖,該聚晶金剛石復(fù)合片底層為頂部具有倒T型凹槽的硬質(zhì)合金基底層103,倒T型凹槽的一字邊的兩側(cè)設(shè)置有斜向盲孔106,硬質(zhì)合金基底層頂部的邊緣上為過渡層102,過渡層102上方為與過渡層形狀互補的金剛石聚晶層101,三層結(jié)構(gòu)嵌合形成整體結(jié)構(gòu)。斜向盲孔中的硬質(zhì)合金注射材料起到加強復(fù)合片強度的作用。經(jīng)檢測,與目前市售復(fù)合片比較,磨耗比達(dá)到52.6~54.3萬。產(chǎn)品耐熱性能檢測,產(chǎn)品在750℃焙燒2分鐘后,磨耗比達(dá)52.4~54.2萬。說明產(chǎn)品焙燒前后磨耗比相差不大,在硬質(zhì)合金表面處理后,使用過程金剛石與基底之間未產(chǎn)生石墨化效應(yīng)。與通過ZL201210200657.3的方法所得的金剛石聚晶復(fù)合片在同等條件下進(jìn)行比較,性能提高24%。實施例4S10,選用硬質(zhì)合金喂料與氮化鋁喂料,于具有倒T型凹槽的模具中進(jìn)行共注射,倒T型凹槽的一字邊兩側(cè)設(shè)置有縱向,橫向和斜向三向盲孔,注射壓力10~82MPa,注射溫度150~210℃,后將注射件脫脂、燒結(jié),燒結(jié)溫度為1200~1500℃,時間為2~24小時,得含過渡層注射燒結(jié)復(fù)合件;S20,聚晶金剛石片準(zhǔn)備S201,選用球形微米級金剛石,金剛石微粉粒度1~40微米,與接合劑進(jìn)行混合球磨;S202,將混合球磨產(chǎn)物進(jìn)行真空干燥,干燥溫度500~600℃;S203,將干燥物壓制成聚晶金剛石片;S30,聚晶復(fù)合片合成S301,將硬質(zhì)合金基底與聚晶壓制片裝入葉蠟石塊體中;S302,將組裝好的葉蠟石塊體放入六面頂或兩面頂中,逐步加壓致3.6~8.4GPa,通電流加熱,維持5~12min;S303,卸掉載荷,進(jìn)行后續(xù)脫除處理并在聚晶層滲入硅合金即獲得聚晶復(fù)臺片。參見圖7所示為采用上述方法獲得的具有內(nèi)嵌結(jié)構(gòu)的聚晶金剛石復(fù)合片的剖面結(jié)構(gòu)示意圖,圖8為圖7的D部分的局部放大圖,該聚晶金剛石復(fù)合片底層為頂部具有倒T型凹槽的硬質(zhì)合金基底層103,倒T型凹槽的一字邊的兩側(cè)設(shè)置有縱向盲孔104,橫向盲孔105和斜向盲孔106,硬質(zhì)合金基底層頂部的邊緣上為過渡層102,過渡層102上方為與過渡層形狀互補的金剛石聚晶層101,三層結(jié)構(gòu)嵌合形成整體結(jié)構(gòu)。縱向盲孔,橫向盲孔和斜向盲孔中的硬質(zhì)合金注射材料起到加強復(fù)合片強度的作用。經(jīng)檢測,與目前市售復(fù)合片比較,磨耗比達(dá)到52.6~54.3萬。產(chǎn)品耐熱性能檢測,產(chǎn)品在750℃焙燒2分鐘后,磨耗比達(dá)52.4~54.2萬。說明產(chǎn)品焙燒前后磨耗比相差不大,在硬質(zhì)合金表面處理后,使用過程金剛石與基底之間未產(chǎn)生石墨化效應(yīng)。與通過ZL201210200657.3的方法所得的金剛石聚晶復(fù)合片在同等條件下進(jìn)行比較,性能提高24%。以上所述僅為本發(fā)明的較佳實施例而已,并不用以限制本發(fā)明,凡在本發(fā)明的精神和原則之內(nèi)所作的任何修改、等同替換和改進(jìn)等,均應(yīng)包含在本發(fā)明的保護范圍之內(nèi)。