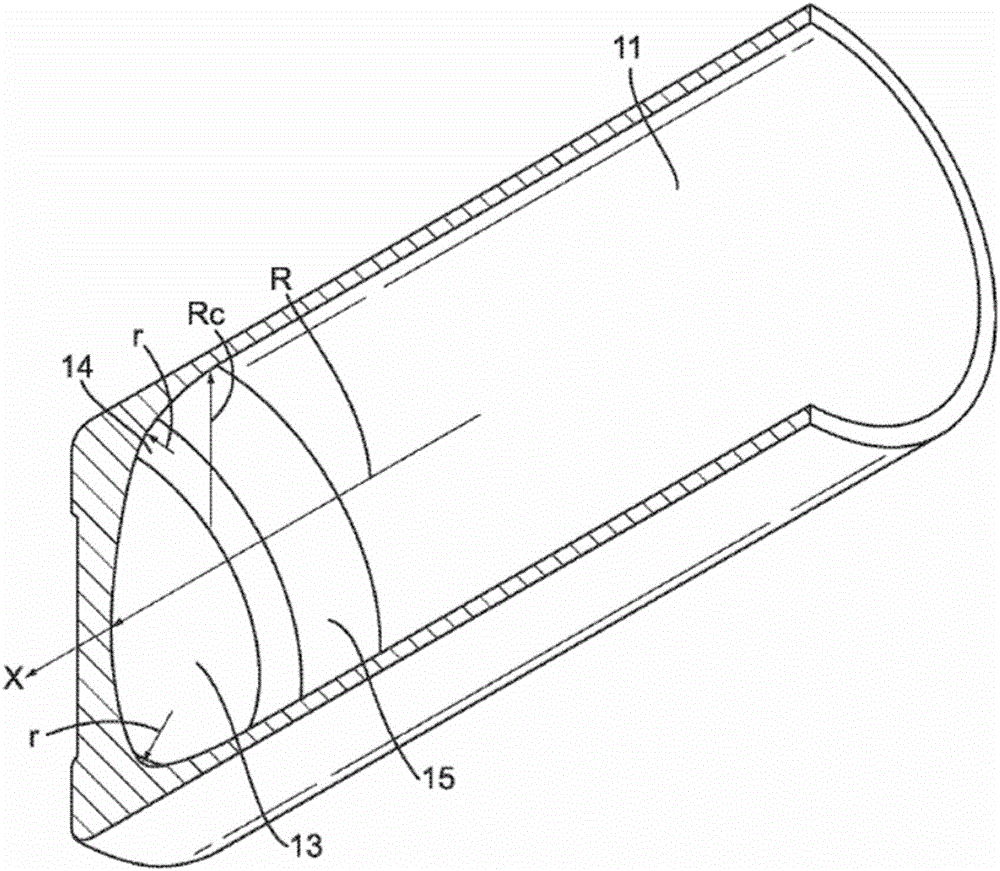
本發(fā)明涉及適于容納加壓流體的容器的制造方法、其制造設(shè)備以及使用此方法制造的壓力容器。更特定來說,本發(fā)明涉及用于能夠容納處于壓力下的流體的金屬容器的制造的反向擠壓方法、其擠壓設(shè)備以及根據(jù)所述方法制造的壓力容器。特定來說但并非排他性地,本發(fā)明涉及用于適于容納處于高于大氣壓力的壓力的氣體的封閉末端式箍包氣筒的制造方法以及通過所述方法制作的封閉末端式箍包氣筒。
背景技術(shù):
:當(dāng)前,壓力容器是用鋁、鋼和復(fù)合材料來制造。I型壓力容器僅由例如鋼或鋁合金等金屬材料形成。相比之下,II型壓力容器包括具有絲狀復(fù)合套筒的金屬容器(通常由鋁制成),所述絲狀復(fù)合套筒例如由環(huán)氧樹脂、芳綸和/或碳纖維形成,且環(huán)繞容器的僅圓柱形側(cè)壁(本文稱為箍包)。II型壓力容器的重量一般比I型壓力容器輕,因?yàn)镮I型壓力容器的金屬容器壁可以比I型壓力容器薄且無性能損失。對(duì)于I型和II型壓力容器兩者,在壓力下的氣體的重復(fù)分配和容器再填充造成容器撓曲,且此撓曲會(huì)促進(jìn)容器壁中的裂縫傳播。對(duì)于金屬和復(fù)合壓力容器,常規(guī)制造方法包含對(duì)包括金屬材料的坯料的熱與冷擠壓,所述金屬材料通常是用于高壓容器的鋁合金。US3648351提供了封閉末端式中空金屬容器的反向擠壓的早期實(shí)施例,其中金屬材料的坯塊或坯料受迫沿著柱塞的側(cè)面向上擠壓,所述柱塞的末端向下壓在模腔內(nèi)的坯塊上。WO96/11757描述了使用反向擠壓的改進(jìn)制造方法,其中對(duì)安裝于模腔中的兩種材料一起進(jìn)行擠壓。另外,已經(jīng)使用自緊法來改善壓力容器抗疲勞性。自緊法涉及在容器的鏜孔內(nèi)施加足以使內(nèi)表面處的金屬塑性變形的壓力。所述技術(shù)在內(nèi)部表面處或附近產(chǎn)生壓縮殘余應(yīng)力,且這增強(qiáng)了經(jīng)受循環(huán)內(nèi)部壓力加載的容器的抗疲勞性。WO96/11759描述了在壓力容器的制造中使用自緊法來使壓力容器壁中的峰值應(yīng)力區(qū)移動(dòng)遠(yuǎn)離內(nèi)部或外部壁表面。本發(fā)明尋求提供一種改進(jìn)壓力容器的抗疲勞性的壓力容器制造方法、制造設(shè)備以及使用所述方法制造的壓力容器。本發(fā)明還尋求提供一種減少過早失效的可能性的壓力容器制造方法、制造設(shè)備以及使用所述方法制造的壓力容器。本發(fā)明進(jìn)一步尋求提供一種尤其適于制造AA6XXX和AA7XXX系列鋁高壓圓筒和圓筒襯里的冷擠壓制造方法和制造設(shè)備。再者,本發(fā)明尋求提供與常規(guī)封閉末端式箍包壓力容器相比具有改進(jìn)性能的封閉末端式箍包壓力容器。本發(fā)明單獨(dú)地尋求提供滿足例如EN12257和/或ISO11119-1等壓力容器標(biāo)準(zhǔn)的法規(guī)要求且具有復(fù)合曲線內(nèi)表面的壓力容器。技術(shù)實(shí)現(xiàn)要素:本發(fā)明因此提供一種形成封閉末端式壓力容器的方法,所述方法包括:將可擠壓金屬的坯料放置到模具中,所述坯料具有軸線和前向表面;使用具有縱向?qū)ΨQ軸線、端面區(qū)和基本上圓柱形的側(cè)壁的柱塞,通過沿著所述坯料的所述軸線迫使所述柱塞的所述端面區(qū)進(jìn)入到所述坯料的所述前向表面中來致使所述金屬受到擠壓,以便致使所述金屬擠壓到所述柱塞與所述模具之間的空間中且沿著所述柱塞的所述圓柱形側(cè)壁擠壓以形成擠出物;以及從所述模具移出所述擠出物且使所述擠出物的開放末端成形以形成肩部和頸部,借此所述柱塞的所述端面區(qū)具有包括中心區(qū)段、至少一個(gè)中間環(huán)和最外面的環(huán)的表面型面,所述中心區(qū)段、所述至少一個(gè)中間環(huán)和所述最外面的環(huán)分別具有相交但不同的半徑R、r和Rc的曲率,所述中心區(qū)段、所述至少一個(gè)中間環(huán)和所述最外面的環(huán)使所述端面與所述柱塞的所述縱向軸線相交處的中心點(diǎn)與所述柱塞的所述圓柱形側(cè)壁在距所述中心點(diǎn)軸向距離H處相連接,所述軸向距離H的范圍為0.28ID至0.5ID,其中ID是所述柱塞的所述圓柱形側(cè)壁的橫截面直徑。優(yōu)選地,所述軸向距離H在0.3ID至0.4ID的范圍內(nèi)。在尤其優(yōu)選的實(shí)施方案中,所述軸向距離H基本上等于ID/3。所述中心區(qū)段優(yōu)選地具有在0.5ID至1.2ID的范圍內(nèi)的曲率半徑R。較優(yōu)選地,所述中心區(qū)段具有基本上等于1.1ID的曲率半徑R。更優(yōu)選地,所述中間環(huán)具有在0.1ID與0.5ID之間的范圍內(nèi)的曲率半徑r。所述中間環(huán)優(yōu)選地具有在0.12ID至0.13ID的范圍內(nèi)的曲率半徑r。在又一優(yōu)選實(shí)施方案中,所述柱塞的所述端面區(qū)可以具有包含至少兩個(gè)中間環(huán)的表面型面,所述至少兩個(gè)中間環(huán)各自具有不同的表面曲率半徑。優(yōu)選地,所述最外面的環(huán)具有在ID/(3±2)的范圍內(nèi)的曲率半徑Rc。更優(yōu)選地,所述最外面的環(huán)具有在ID/(3±1)的范圍內(nèi)的曲率半徑Rc。所述最外面的環(huán)優(yōu)選地具有基本上等于ID/2的曲率半徑Rc。所述方法可以進(jìn)一步包括對(duì)所述壓力容器進(jìn)行自緊法處理的步驟。所述坯料可以包括AA6XXX系列鋁合金。在尤其優(yōu)選的實(shí)施方案中,所述坯料包括AA7XXX系列鋁合金。在第二方面中,本發(fā)明提供一種用于在封閉末端式壓力容器的制造中使用的擠壓設(shè)備,所述擠壓設(shè)備包括用于容納可擠壓金屬的坯料的模具以及具有縱向?qū)ΨQ軸線、端面區(qū)和基本上圓柱形的側(cè)壁的柱塞,所述柱塞的所述端面區(qū)具有包括中心區(qū)段、至少一個(gè)中間環(huán)和最外面的環(huán)的表面型面,所述中心區(qū)段、所述至少一個(gè)中間環(huán)和所述最外面的環(huán)分別具有相交但不同的半徑R、r和Rc的曲率,所述中心區(qū)段、所述至少一個(gè)中間環(huán)和所述最外面的環(huán)使所述端面與所述柱塞的所述縱向軸線相交處的中心點(diǎn)與所述柱塞的所述圓柱形側(cè)壁在距所述中心點(diǎn)軸向距離H處相連接,所述軸向距離H的范圍為0.28ID至0.5ID,其中ID是所述柱塞的所述圓柱形側(cè)壁的橫截面直徑。優(yōu)選地,所述軸向距離H在0.3ID至0.4ID的范圍內(nèi)。在尤其優(yōu)選的實(shí)施方案中,所述軸向距離H基本上等于ID/3。所述中心區(qū)段優(yōu)選地具有在0.5ID至1.2ID的范圍內(nèi)的曲率半徑R。較優(yōu)選地,所述中心區(qū)段具有基本上等于1.1ID的曲率半徑R。所述中間環(huán)優(yōu)選地具有在0.1ID與0.5ID之間的范圍內(nèi)的曲率半徑r。較優(yōu)選地,所述中間環(huán)具有在0.12ID與0.13ID之間的范圍內(nèi)的曲率半徑r。在又一優(yōu)選實(shí)施方案中,所述柱塞的所述端面區(qū)可以具有包含至少兩個(gè)中間環(huán)的表面型面,所述至少兩個(gè)中間環(huán)各自具有不同的表面曲率半徑。所述最外面的環(huán)優(yōu)選地具有在ID/(3±2)的范圍內(nèi)的曲率半徑Rc。較優(yōu)選地,所述最外面的環(huán)具有在ID/(3±1)的范圍內(nèi)的曲率半徑Rc。更優(yōu)選地,所述最外面的環(huán)具有基本上等于ID/2的曲率半徑Rc。在第三方面中,本發(fā)明提供一種由可擠壓金屬形成的封閉末端式壓力容器,所述壓力容器包括封閉末端區(qū)段、具有橫截面內(nèi)徑ID的基本上圓柱形的側(cè)壁、肩部以及頸部且具有縱向?qū)ΨQ軸線,所述封閉末端區(qū)段的內(nèi)表面型面包括中心區(qū)段、至少一個(gè)中間環(huán)和最外面的環(huán),所述中心區(qū)段、所述至少一個(gè)中間環(huán)和所述最外面的環(huán)分別具有相交但不同的半徑R、r和Rc的曲率,所述中心區(qū)段、所述至少中間環(huán)和所述最外面的環(huán)使所述封閉末端區(qū)段與所述縱向軸線相交處的中心點(diǎn)與所述圓柱形側(cè)壁在距所述中心點(diǎn)軸向距離H處相連接,所述軸向距離H的范圍為0.28ID至0.5ID。優(yōu)選地,所述軸向距離H在0.3ID至0.4ID的范圍內(nèi)。在尤其優(yōu)選的實(shí)施方案中,所述軸向距離H基本上等于ID/3。所述中心區(qū)段優(yōu)選地具有在0.5ID至1.2ID的范圍內(nèi)的曲率半徑R。較優(yōu)選地,所述中心區(qū)段具有基本上等于1.1ID的曲率半徑R。所述中間環(huán)優(yōu)選地具有在0.1ID與0.5ID之間的范圍內(nèi)的曲率半徑r。較優(yōu)選地,所述中間環(huán)具有在0.12ID與0.13ID之間的范圍內(nèi)的曲率半徑r。在又一優(yōu)選實(shí)施方案中,所述封閉末端區(qū)段的所述內(nèi)表面型面可以包含至少兩個(gè)中間環(huán),所述至少兩個(gè)中間環(huán)各自具有不同的表面曲率半徑。所述最外面的環(huán)優(yōu)選地具有在ID/(3±2)的范圍內(nèi)的曲率半徑Rc。較優(yōu)選地,所述最外面的環(huán)具有在ID/(3±1)的范圍內(nèi)的曲率半徑Rc。在尤其優(yōu)選的實(shí)施方案中,所述最外面的環(huán)具有基本上等于ID/2的曲率半徑Rc。所述封閉末端式壓力容器可以包括AA6XXX系列鋁合金。在尤其優(yōu)選的實(shí)施方案中,所述封閉末端式壓力容器包括AA7XXX系列鋁合金。在又一方面中,本發(fā)明提供一種復(fù)合壓力容器,其包括如上所述的封閉末端式壓力容器以及復(fù)合材料制套筒。所述復(fù)合材料可以選自碳纖維復(fù)合物、玄武巖纖維、芳綸和/或玻璃纖維。本發(fā)明的制造方法和制造設(shè)備使得能夠使用冷或溫?cái)D壓制造封閉末端式高壓力容器,其與使用熱擠壓制造的等效高壓力容器相比具有等效或改進(jìn)的壽命且即使在較低壓力自緊法的情況下也實(shí)現(xiàn)等效性能。附圖說明現(xiàn)在將舉例來說僅參考附圖描述本發(fā)明的實(shí)施方案,附圖中:圖1示意性圖示了在金屬坯料的反向擠壓以形成封閉末端式壓力容器中的一系列階段;圖2是穿過根據(jù)本發(fā)明的壓力容器的封閉末端的橫截面的透視圖;圖3是圖2的壓力容器的封閉末端的詳細(xì)橫截面;圖4圖示了圖2的壓力容器的封閉末端的表面曲率半徑的關(guān)系;圖5a和5b圖示了使用常規(guī)箍包壓力容器襯里的基底的有限元分析的第一主應(yīng)力和VonMises應(yīng)力;以及圖6a和6b圖示了使用根據(jù)本發(fā)明的箍包壓力容器襯里的基底的有限元分析的第一主應(yīng)力和VonMises應(yīng)力。具體實(shí)施方式雖然根據(jù)本發(fā)明的熱擠壓(其中擠壓通常在高于再結(jié)晶溫度的溫度下執(zhí)行)是可能的,但冷和/或溫?cái)D壓(其中擠壓是在低于再結(jié)晶溫度的溫度下執(zhí)行)作為較低成本程序而是優(yōu)選的。溫?cái)D壓通常是以100-250℃的起始坯料溫度來執(zhí)行,而冷擠壓通常是以低于100℃、優(yōu)選為環(huán)境溫度的起始坯料溫度來執(zhí)行。然而,精確的擠壓條件對(duì)本發(fā)明并不重要,且可以采用擠壓的常規(guī)條件。制造如圖1中所示的封閉末端式壓力容器的方法涉及在金屬坯料2的反向擠壓中使用擠壓設(shè)備1??傮w來說,將例如鋁合金的金屬材料坯料2放置于模具4(也稱為擠壓套筒)中的腔3的底部處。橫截面優(yōu)選為圓柱形且具有基本上平行的側(cè)壁的柱塞5被布置成用于沿著柱塞5、模具4和坯料2的共同軸線X進(jìn)行往復(fù)移動(dòng)。柱塞5插入到模腔3中,使得柱塞5的端面6接合坯料2的面朝模腔3的開口的表面。柱塞5朝向模腔3的封閉末端的持續(xù)往復(fù)移動(dòng)迫使柱塞的端面區(qū)6進(jìn)入金屬坯料2。這造成坯料2的金屬材料沿著柱塞5的側(cè)壁表面擠壓。擠出物從模腔3退出的速度通常在50-500厘米/分鐘的范圍內(nèi),且還可以至少在柱塞5的端面6接觸坯料2之處提供潤(rùn)滑(未圖示)以減少所需的擠壓壓力。柱塞5的往復(fù)移動(dòng)繼續(xù)直到柱塞的端面6到達(dá)距模腔3的內(nèi)底面的預(yù)定距離,所述距離大體上對(duì)應(yīng)于所得壓力容器的封閉末端的所需厚度。類似地,柱塞5的側(cè)壁與模具4的圓柱形內(nèi)表面的徑向分離大體上對(duì)應(yīng)于壓力容器的圓柱形側(cè)壁的厚度。因此,壓力容器的封閉末端的內(nèi)部型面對(duì)應(yīng)于柱塞5的外部型面。壓力容器的封閉末端的形成導(dǎo)致初始大體上杯形的擠出物,其具有基底、平行側(cè)壁以及開放的頂部。隨后使擠出物的開放頂部成方形且加熱,通常感應(yīng)加熱到300-450℃,然后使用常規(guī)型鍛或自旋技術(shù)形成頸部。所得的中空主體經(jīng)過溶液熱處理,一般在冷水中淬火,并最終老化。還可以執(zhí)行例如自緊法和噴丸等常規(guī)精整工藝,以完成壓力容器的制造。上文描述的擠壓方法不同于借助新穎且具發(fā)明性的擠壓設(shè)備1的使用對(duì)金屬坯料的常規(guī)反向擠壓。擠壓設(shè)備1的特征一般在設(shè)計(jì)上是常規(guī)的,但柱塞5的端面的外表面10除外,這在下文更詳細(xì)描述。如早先提到,壓力容器的封閉末端的內(nèi)表面型面對(duì)應(yīng)于柱塞5的外表面10的型面,且因此本文通過參考圖2至4來描述柱塞5的外表面10,圖2至4以橫截面示出了使用擠壓設(shè)備1的模具4和柱塞5制造的壓力容器的封閉末端??傮w來說且參考圖2和3,所述壓力容器具有外部直徑或外徑OD,其基本上等于擠壓套筒或模具4的圓柱形側(cè)壁的內(nèi)徑,且具有內(nèi)徑ID,其基本上等于柱塞5的外部側(cè)壁的外部圓柱形直徑。所述內(nèi)徑與外徑之間的差對(duì)應(yīng)于壓力容器的基本上圓柱形的側(cè)壁11的厚度,即a=(OD-ID)/2,其也基本上對(duì)應(yīng)于柱塞5和模具4的側(cè)壁的空隙或徑向差。柱塞5的外表面10的型面的關(guān)鍵特征包含:中心點(diǎn)12,在此處柱塞5的末端與其縱向?qū)ΨQ軸線X相交;中心區(qū)段13;以及至少兩個(gè)環(huán)14、15,所述環(huán)將中心點(diǎn)12連接到柱塞5的基本上圓柱形的側(cè)壁11。當(dāng)沿著軸線X觀看時(shí),中心區(qū)段13以及兩個(gè)環(huán)14和15全部相對(duì)于軸線X旋轉(zhuǎn)對(duì)稱,且相對(duì)于彼此同心。相比之下,圖3和4的垂直橫截面中的中心區(qū)段13以及兩個(gè)環(huán)14和15的表面型面清楚可見具有不同的但相交的表面曲率。在每一情況下,中心區(qū)段13、中間環(huán)14和最外面的環(huán)15的表面曲率在它們的邊界之間延伸,且分別具有R、r和Rc的半徑。中心點(diǎn)12位于中心區(qū)段13的中心處。中心區(qū)段13的表面型面具有的半徑R的曲率在0.5ID至1.2ID之間,較優(yōu)選地在0.8ID至1.2ID之間,且再優(yōu)選地為1ID<R<1.2ID。中心區(qū)段13的外部邊緣與本文稱為中間環(huán)14的第一關(guān)節(jié)區(qū)段的內(nèi)部邊緣接合或相交,所述中間環(huán)14具有的半徑r的曲率在0.1ID至0.5ID之間,較優(yōu)選地在0.1ID至0.25ID之間,且再優(yōu)選地為0.1ID<r<0.15ID。又,中間環(huán)14的外部邊緣與本文稱為第二或最外面的環(huán)15的第二關(guān)節(jié)區(qū)段的內(nèi)部邊緣接合或相交,所述最外面的環(huán)15具有的半徑Rc=ID/(3±2)的曲率,較優(yōu)選地為Rc=ID/(3±1),且再優(yōu)選地為0.4ID<Rc<0.6ID。雖然中心區(qū)段13以及兩個(gè)環(huán)14、15的潛在曲率的范圍彼此重疊,但對(duì)于任何特定的柱塞5,界定外表面10的中心區(qū)段和兩個(gè)環(huán)將各自具有與其它者的表面曲率不同的表面曲率,且中間環(huán)14的表面曲率的半徑總是小于中心區(qū)段13和最外面的環(huán)15的曲率。參考圖4,由于中心區(qū)段13相對(duì)于軸線X旋轉(zhuǎn)對(duì)稱,因此中心區(qū)段的表面曲率的半徑R是從沿著軸線X的距離R的點(diǎn)(原點(diǎn))測(cè)得。此外,中心區(qū)段13與中間環(huán)14的相交、中間環(huán)14與最外面的環(huán)15的相交以及最外面的環(huán)15與圓柱形側(cè)壁11的相交各自混合而確保柱塞5的末端的表面型面中沒有不連續(xù),所述不連續(xù)可能有損圓筒的強(qiáng)度。這要求在每一相交處,接合部的任一側(cè)的表面的曲率的切線(所述切線正交于接合部的線)是基本上對(duì)準(zhǔn)的且優(yōu)選共同的。在最外面的環(huán)15與圓柱形側(cè)壁11的相交的情況下,最外面的環(huán)15的表面曲率的切線(正交于線,如果相交)基本上與圓柱形側(cè)壁11的表面對(duì)準(zhǔn)。在最外面的環(huán)15與圓柱形側(cè)壁11的接合部處穿過柱塞5取得的橫截面在中心點(diǎn)12上方距離H處與軸線X相交。距離H在0.28ID至0.5ID之間,較優(yōu)選地為0.3ID至0.4ID之間,再優(yōu)選地為H=ID/3。由于在最外面的環(huán)15與側(cè)壁11的接合點(diǎn)處,最外面的環(huán)15的表面曲率的切線與圓柱形壁11基本上對(duì)準(zhǔn),因此最外面的環(huán)的表面曲率的半徑Rc是從位于穿過柱塞5的橫截平面中在中心點(diǎn)12上方的高度H處的點(diǎn)(原點(diǎn))測(cè)得。因此為了確保中間環(huán)14的曲率與中心區(qū)段13和最外面的環(huán)15混合,中間環(huán)14的半徑r是從對(duì)應(yīng)于Rc-r和R-r的相交的點(diǎn)(原點(diǎn))測(cè)得。此外,中間環(huán)14的中心的橫截面直徑IDC小于或等于OD-(3xa),其中OD是壓力容器的外部圓柱形直徑(等于模具4的內(nèi)部圓柱形直徑),且a是壓力容器壁的厚度(等于模具4和柱塞5的圓柱形側(cè)壁的分離)。雖然附圖圖示了單個(gè)中間環(huán)14,但壓力圓筒的內(nèi)表面型面(且因此還有柱塞5的外表面型面)可以包括多于一個(gè)中間環(huán),其中每一中間環(huán)具有其自身的表面曲率半徑,且每一中間環(huán)在其邊緣處與相鄰環(huán)的邊緣混合,即,每一中間環(huán)在所述中間環(huán)的邊緣處的表面曲率的切線與相鄰環(huán)的表面曲率的切線基本上對(duì)準(zhǔn)。此外,雖然附圖圖示了中心區(qū)段13的表面曲率由單個(gè)半徑界定,但也設(shè)想中心13可以由基本上平坦的內(nèi)部中心區(qū)段以及與內(nèi)部中心區(qū)段同心的外部中心區(qū)段組成,其具有半徑R的表面曲率。實(shí)施例1以下陳述根據(jù)本發(fā)明的擠壓設(shè)備的模具4和柱塞5以及使用所述模具和柱塞制作的5升AA7060圓筒襯里的對(duì)應(yīng)尺寸的第一組示例性尺寸。圓筒的總高度=465mm圓筒的總重量=4.8Kg柱塞和模具5升AA7060圓筒襯里(mm)模具的內(nèi)徑OD140柱塞的外徑ID129模具與柱塞的圓柱形表面的徑向分離a5.5柱塞的有輪廓端到圓柱形側(cè)壁的軸向高度H43有輪廓柱塞表面的最內(nèi)部環(huán)半徑R146有輪廓柱塞表面的第二環(huán)半徑r16有輪廓柱塞表面的最外面的環(huán)半徑Rc64實(shí)施例2以下陳述常規(guī)2升碳纖維箍包AA7060合金襯里(和常規(guī)擠壓設(shè)備的模具4和柱塞5的對(duì)應(yīng)尺寸)(形狀A(yù))以及類似地根據(jù)本發(fā)明的2升碳纖維箍包AA7060合金襯里(及其對(duì)應(yīng)模具和柱塞)(形狀B)的第二組示例性尺寸:以下在表1中陳述使用實(shí)施例2中描述的擠壓設(shè)備在冷擠壓下制造的壓力容器以及使用冷擠壓和常規(guī)反向擠壓模具制造的2升箍包7060鋁合金襯里(形狀A(yù))的比較性失效性能測(cè)試結(jié)果。表1失效位點(diǎn)0=泄漏,位置未知;失效位點(diǎn)1=圓筒底部處的破裂;失效位點(diǎn)2=圓筒主體中的泄漏;以及失效位點(diǎn)3=肩部中的泄漏。將使用以上實(shí)施例1中描述的設(shè)備在冷擠壓下制造的5升箍包7060鋁合金襯里(形狀B)的壽命和失效特性與也使用冷擠壓但用常規(guī)反向擠壓模具制造的5升箍包7060鋁合金襯里(形狀A(yù))的性能進(jìn)行比較。以下在表2中陳述在壽命(達(dá)到失效的再填充循環(huán)的次數(shù))和失效位點(diǎn)方面的結(jié)果。表2表1和2的結(jié)果清楚示出了與等效常規(guī)壓力容器相比的失效性能的顯著改進(jìn)。測(cè)試具有實(shí)施例1中陳述的尺寸的二十七個(gè)測(cè)試壓力容器達(dá)到失效。使各自具有五個(gè)壓力容器的五個(gè)組經(jīng)受循環(huán)測(cè)試,其中每一組壓力容器已經(jīng)進(jìn)行不同量的自緊法。使剩余兩個(gè)壓力容器(未進(jìn)行自緊法)經(jīng)受爆破測(cè)試。測(cè)試壓力容器中的每一者是使用具有實(shí)施例1中陳述的尺寸的模具4和柱塞5在冷反向擠壓過程中制造的5升碳纖維箍包7060鋁合金壓力容器。以下在表3中陳述每一組壓力容器的自緊法量的細(xì)節(jié)以及測(cè)試的結(jié)果。表3(a)表示圓筒主體壁中的失效(b)表示在圓筒的不同部分處的失效。在以上測(cè)試中,經(jīng)受110%自緊法壓力的壓力容器中的兩個(gè)以及經(jīng)受120%自緊法壓力的壓力容器中的三個(gè)展現(xiàn)了碳纖維從外部套筒的脫離。如WO96/11759中論述,已知自緊法在改善疲勞性能方面的有效性是取決于壓力容器的封閉末端的設(shè)計(jì)。舉例來說,具有半球形封閉末端的壓力容器當(dāng)經(jīng)受自緊法時(shí)并不展現(xiàn)疲勞性能方面的顯著改進(jìn)。相比之下,已知具有半橢圓形或準(zhǔn)球形碟形封閉末端的壓力容器以自緊法帶來改進(jìn)的性能。因此,自緊法為封閉末端通過關(guān)節(jié)區(qū)接合到圓柱形側(cè)壁的壓力容器提供改進(jìn)的失效性能。自緊法壓力根據(jù)相關(guān)標(biāo)準(zhǔn)一般在最小爆破壓力的75%至95%之間。鋁高壓氣體圓筒通常被設(shè)計(jì)成使得處于工作壓力下的圓柱形側(cè)壁中的應(yīng)力不會(huì)超過合金屈服應(yīng)力的一半,且圓筒爆破壓力為操作壓力的至少2.5倍。因此,在具有例如450MPa的屈服應(yīng)力的AA7XXX系列鋁合金圓筒中,設(shè)計(jì)應(yīng)當(dāng)使得壁應(yīng)力不超過225MPa。表1至3中的信息清楚示出了根據(jù)本發(fā)明的方法和設(shè)備制造的箍包壓力容器也得益于自緊法和噴丸,與等效的常規(guī)壓力容器相比提供失效性能的驚人改進(jìn)。這使得根據(jù)本發(fā)明的方法和設(shè)備的壓力容器能夠在較低自緊法壓力下帶來至少等效且潛在改進(jìn)的失效性能。使用上述方法和設(shè)備制造的箍包壓力容器的有限元分析(FEA)已經(jīng)揭示了根據(jù)本發(fā)明的壓力容器的封閉末端的內(nèi)部型面與在封閉末端具有常規(guī)內(nèi)部型面的壓力容器相比帶來顯著更低的最大應(yīng)力。通過FEA,將結(jié)構(gòu)(在此情況下為壓力容器的封閉末端)劃分為具有各種類型、大小和形狀的許多小片(有限數(shù)目的元素)。所述元素假定為具有簡(jiǎn)化的變形模式(線性或二次等等),且在通常位于元素的拐角或邊緣處的‘節(jié)點(diǎn)’處連接。隨后使用結(jié)構(gòu)力學(xué)的基本規(guī)則(即,力平衡和位移連續(xù)性)以數(shù)學(xué)方式組合所述元素,從而帶來大的聯(lián)立方程組。通過求解聯(lián)立方程組,可以獲得在負(fù)載下的結(jié)構(gòu)的變形形狀,且可以從變形形狀計(jì)算內(nèi)部應(yīng)力和應(yīng)變。有限元模型(FEM)是基于7060鋁合金襯里和具有ID=88.5的碳復(fù)合套筒,與用于壓力容器的內(nèi)表面型面的4組不同尺寸組合:分析1,分析2,分析3以及分析4。FEA使每一分析經(jīng)受以下加載步驟:自緊法壓力=600BAR;工作壓力=300BAR;測(cè)試壓力=450BAR且最小設(shè)計(jì)爆破=752BAR,以識(shí)別在自緊法之后在450BAR的測(cè)試壓力下的第一主應(yīng)力和VonMises應(yīng)力,其結(jié)果在以下表4中陳述;分析1對(duì)應(yīng)于被調(diào)整成并入三個(gè)同心相交半徑的常規(guī)壓力容器,而分析4對(duì)應(yīng)于使用上述方法和設(shè)備制造的壓力容器,分析4是尤其優(yōu)選的實(shí)施方案。包含分析2和3僅用于比較性目的。表4圖5a和5b示出了分析1的主應(yīng)力和VonMises應(yīng)力,且圖6a和6b示出了分析4的主應(yīng)力和VonMises應(yīng)力。圖5和6示出了關(guān)節(jié)區(qū)中的最大應(yīng)力的位置對(duì)于分析1和分析4保持基本上相同(對(duì)于分析2和分析3也是一樣,未圖示)。圖5和6還示出了對(duì)于使用上述方法和設(shè)備制造的II型壓力容器,即使在自緊法之后,最大VonMises應(yīng)力也保持于壓力容器的內(nèi)表面處。然而,表4中的結(jié)果清楚示出了分析4的第一主應(yīng)力和VonMises應(yīng)力的絕對(duì)值顯著低于其它分析中的任一者。而且FEA示出了貢獻(xiàn)于最大應(yīng)力的降低的主要因素是H和Rc的值。以上方法和設(shè)備尤其適合于(但不限于)AA6XXX和AA7XXX系列鋁合金(根據(jù)AluminumAssociationInc.注冊(cè)2009)的壓力容器的冷擠壓制造,以及分別滿足箍包壓力容器標(biāo)準(zhǔn)(例如EN12257和ISO11119-1)以及世界其它地區(qū)中的對(duì)應(yīng)標(biāo)準(zhǔn)的疲勞要求的I型圓筒和II型圓筒襯里。而且,通過以上方法和設(shè)備,可以使用自緊法在較低壓力下制造至少匹配且經(jīng)常超過等效常規(guī)圓筒的失效性能的II型圓筒。應(yīng)了解,上文描述的實(shí)施方案僅是選定的優(yōu)選示例性實(shí)施方案。在不脫離所附權(quán)利要求書中要求的本發(fā)明的范圍的情況下,可以對(duì)上文描述的制造方法、制造設(shè)備和通過所述方法和設(shè)備制作的壓力容器做出改變。當(dāng)前第1頁(yè)1 2 3