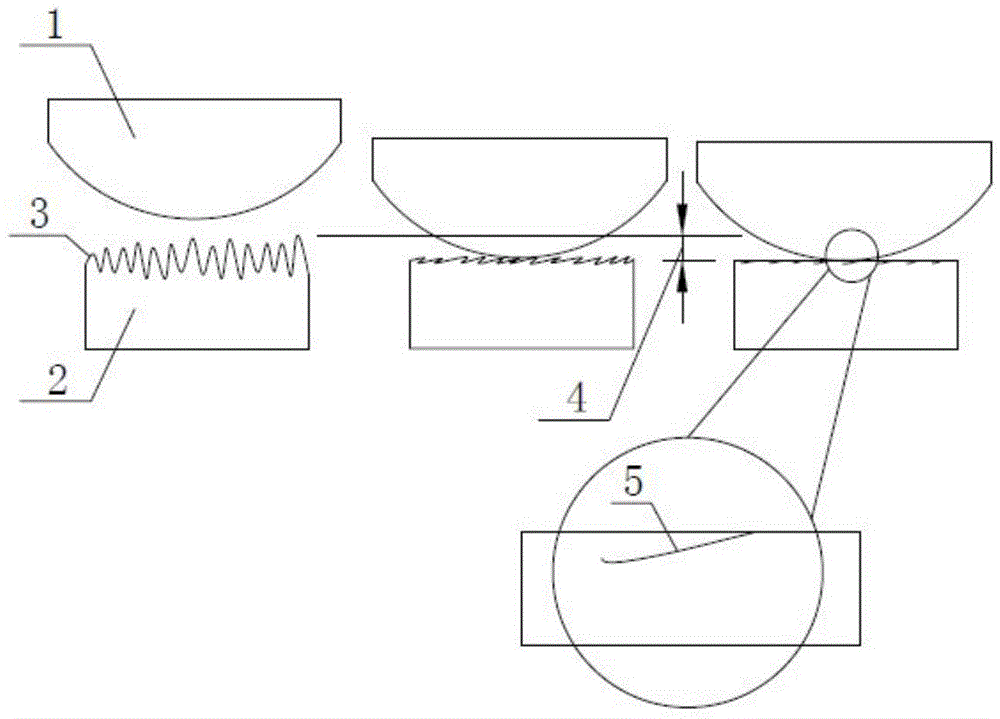
本發(fā)明屬于材料加工領域,更加具體地說,涉及一種利用超聲沖擊和光飾相結合來提高金屬部件超聲沖擊處理后表面性能(例如粗糙度、疲勞強度)的方法。
背景技術:
:超聲沖擊的原理是超聲振動發(fā)生器驅動沖擊針產生機械振動,沖擊針快速撞擊工件表面,引起工件表面得到強化并產生變形,從而達到使金屬表面產生一定深度的殘余壓應力層,使金屬零件的強度、耐腐蝕性和疲勞壽命得到明顯提高。超聲沖擊處理會使工件的表面粗糙度發(fā)生改變。因為在超聲沖擊過程中,沖擊針與試樣表面不斷撞擊接觸,留下沖擊處理的加工痕跡取代了工件原有的表面粗糙度,對工件的原始表面粗糙度有明顯的影響。通常在沖擊處理后,工件的粗糙度較低不能達到使用的要求。技術實現(xiàn)要素:本發(fā)明的目的在于克服現(xiàn)有技術的不足,立足于超聲沖擊處理方法,提供一種利用超聲沖擊和光飾相結合來提高金屬部件超聲沖擊處理后表面性能(例如粗糙度、疲勞強度)的方法。本發(fā)明的技術目的通過下述技術方案予以實現(xiàn):一種利用超聲沖擊和光飾相結合來提高金屬部件超聲沖擊處理后表面性能的方法,按照下述步驟進行:步驟1,采用機械加工方法加工并控制工件的表面粗糙度,以使其表面粗糙度Ra<1.6μm,所述機械加工方法為銑或者磨;步驟2,利用超聲沖擊槍對加工后的工件進行表面沖擊處理;步驟3,超聲沖擊后需要去毛刺和拋光的工件和拋磨塊、水、研磨劑配制好放進容器中進行光飾處理,即依靠容器的規(guī)律性振動,使工件與拋磨塊產生相對運動,相互摩擦,把凸出于工件表面和周邊的毛刺磨掉,并使銳邊倒圓和表面拋光處理。在本發(fā)明的技術方案中,所述超聲沖擊處理是指利用超聲沖擊槍對加工后的工件進 行表面沖擊處理。要求使用工裝卡具將工件固定在操作臺上,將超聲沖擊槍固定在自動行走裝置上。通過控制超聲沖擊槍的行走速度、行間偏移量、振幅、頻率等來控制超聲沖擊的效果。超聲沖擊后工件表面易出現(xiàn)如下問題:工件的原始表面粗糙度會影響超聲沖擊后工件表面“疊形”缺陷的尺寸。圖1為超聲沖擊后工件表面形成疊形缺陷。即工件的原始表面粗糙度越大,沖擊后缺陷的尺寸就越大。若工件原始表面粗糙度較小,沖擊后形成的缺陷尺寸也會相對較小。這是由于疊形缺陷形成的方式所決定的,圖2是疊形缺陷形成示意圖,即超聲沖擊對工件表面的超聲沖擊加工,以使工件表面產生塑性形變。在這一問題下,首先在超聲沖擊之前進行工件的加工準備,采用機械加工的方法加工控制工件的原始表面粗糙度,以減少超聲沖擊處理后工件表面的“疊形”缺陷。“疊形”缺陷是由于在沖擊過程中工件的表面塑性變形形成的微小裂紋,從而縮短工件的使用壽命。其次在超聲沖擊之后進行工件的光飾,利用光飾對材料表面進行處理,使工件與拋磨塊產生相對運動,相互摩擦,把凸出于工件表面和周邊的毛刺磨掉,并使銳邊倒圓和表面拋光處理,同時去除超聲沖擊帶來的疊形缺陷。超聲沖擊時要求工件固定裝卡在操作臺上,至少使用4個卡具固定工件以確保在超聲沖擊過程中工件停留在原位置。若使用單針進行超聲沖擊則針頭的直徑r≥3mm,若使用多排針進行超聲沖擊則針頭直徑r<3mm。在振動光飾處理時為保證正常良好的光飾效果及效率,磨料和工件的容積比應控制在3:(1—2)。比例過大則生產效率低,比例過小則光飾效果差。本發(fā)明在進行材料的表面處理,成型及矯形過程中能有效的減小沖擊后工件表面微小缺陷的尺寸,減小受沖擊后材料的表面粗糙度,從而提高材料的表面抗腐蝕能性,疲勞性能及抗動載荷能力。附圖說明圖1是工件在超聲沖擊作用后形成的疊形缺陷的SEM圖。圖2是疊形缺陷形成的原理示意圖,其中1為沖擊針;2為工件;3為工件表面形貌曲率半徑ρ;4為塑性變形高度差Δh;5為疊形缺陷。具體實施方式下面結合具體實施例進一步說明本發(fā)明的具體技術方案。實施例1同一超聲沖擊處理參數(shù)下不同原始表面粗糙度對超聲沖擊處理后金屬表面粗糙度的影響DH36鋼(DH36化學成分如表1)利用機械加工(銑床)成4個不同的粗糙度,編號為A、B、C、D。其中由A至D粗糙度依次減小,即為A最粗糙,D最光滑。這四種表面粗糙度的工件都經過同樣的超聲沖擊工藝處理,超聲沖擊具體參數(shù)表2所示。經過超聲沖擊后的工件還要經過振動光飾機的加工以便去除毛刺減小粗糙度,振動光飾在LMP60型振動光飾機上進行,裝入工件數(shù)量每次不大于10件,磨料為剛玉(斜三角,120°),磨液型號為LM10,振動頻率為2800/min,振動時間為1.5~2小時。工件的原始粗糙度的測量值及超聲處理2次以后工件表面的粗糙度測量值和經過振動光飾后的粗糙度值如表3所示。表中A0、B0、C0、D0表示未處理工件,A2、B2、C2、D2表示工件經過2次超聲沖擊后工件,Az、Bz、Cz、Dz表示振動光飾后工件。從表3可以看出,經過這一系列的加工后,工件的表面粗糙度越來越小且趨于平緩,粗糙度值提高甚至接近10倍。通常在同樣的工況下工件的疲勞壽命與粗糙度成正比,即粗糙度越小疲勞壽命越長。這一套加工過程能有效地延長工件的使用壽命。加工后的工件進行疲勞試樣,實驗結果如表4所示。由疲勞試驗結果可以看出,由于原始工件表面粗糙度較大,表面缺陷較多導致疲勞壽命很短。但是經過超聲沖擊處理后,隨著粗糙度的減小,疲勞壽命有了顯著的提高,疲勞壽命較原始工件提高了至少20倍。在經過振動光飾加工后,疲勞壽命由于粗糙度的減小繼續(xù)升高,較超聲沖擊后的工件疲勞壽命提高了近2倍。表1DH36化學成分(%)CSiMnPSNbVTiAl0.1300.1801.400<0.0050.0010.0190.0490.0120.026表2超聲沖擊工藝參數(shù)沖擊區(qū)域(mm)沖擊針半徑(mm)振幅(μm)沖擊速度(mm/s)沖擊次數(shù)40×40525202表3不同工件粗糙度值Ra(μm)Rz(μm)A017.5488.05A25.1341.18Az1.3420.09B016.3468.36B23.0131.35Bz1.1218.74C07.8643.05C23.2613.40Cz0.948.79D00.9718.42D20.958.57Dz0.161.77表4不同工件的疲勞壽命原始工件UITUIT+振動光飾工件A14339924000545021145工件B23435430362025341007工件C43442640543245314405工件D53240142015045537508注:UIT為超聲沖擊處理實施例2同一金屬原始表面粗糙度下使用不同超聲沖擊處理參數(shù)處理后金屬表面粗糙度的區(qū)別對同一粗糙的DH36鋼進行超聲沖擊,沖擊的次數(shù)為1至4次(其他沖擊參數(shù)如表2),沖擊后進行振動光飾加工,加工后的粗糙度值如表5所示。疲勞試驗結果如表6所示。結合粗糙度和疲勞試驗可得出同一粗糙度的工件經過不同的沖擊處理工藝和振動光飾處理后,疲勞壽命有了顯著的提高,本發(fā)明創(chuàng)新對于粗糙的減小有顯著效果。表5工件粗糙度值Ra(μm)Rz(μm)A017.5488.05A112.9450.86A25.1341.18A32.9128.77A42.0920.72Az1.0812.03表6工件疲勞強度粗糙度測定:使用Sneox非接觸式高性能光學三維輪廓儀測量工件表面,得到工件表面三維輪廓。Sneox將共聚焦影像輪廓技術和光學干涉測量技術結合在一個沒有任何移動部件的探測部頭(SensorHead),能夠可靠的、準確的測量毫米級至亞納米級尺度樣品表面形貌細節(jié)后經由軟件計算得出工件的表面粗糙度。測量位置大小為1.67x1.25mm2,測量深度為160μm,目鏡大小為20X。以上對本發(fā)明做了示例性的描述,應該說明的是,在不脫離本發(fā)明的核心的情況下,任何簡單的變形、修改或者其他本領域技術人員能夠不花費創(chuàng)造性勞動的等同替換均落入本發(fā)明的保護范圍。當前第1頁1 2 3