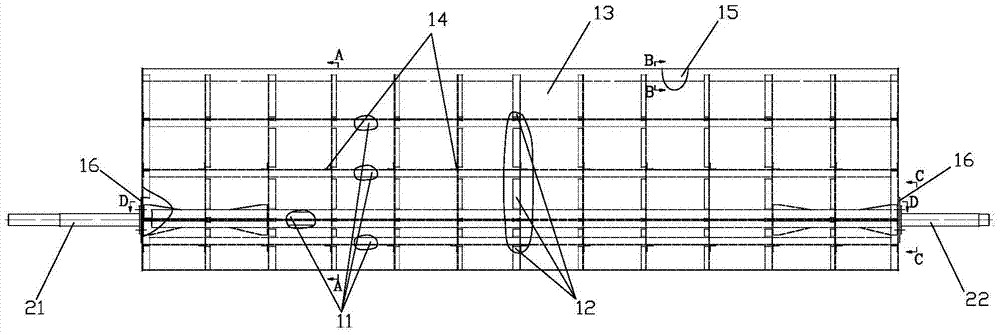
本發(fā)明涉及一種船用空氣舵舵葉的制造安裝工藝。
背景技術(shù):舵設(shè)備是用以改變和保持船舶航向的設(shè)備,由舵和操舵裝置組成。船舶航行時(shí),通過操舵裝置轉(zhuǎn)動(dòng)舵葉,使水流(氣流)在舵葉上產(chǎn)生橫向作用力,為船舶提供回轉(zhuǎn)力矩,從而使船舶保持航向或回轉(zhuǎn)。舵轉(zhuǎn)動(dòng)時(shí)產(chǎn)生的回轉(zhuǎn)力矩的大小取決于舵角,即轉(zhuǎn)舵后舵葉與正舵位置的夾角。當(dāng)舵角為0°或90°時(shí),回轉(zhuǎn)力矩等于零,當(dāng)舵角達(dá)到最大舵角值時(shí),回轉(zhuǎn)力矩達(dá)到最大值。氣態(tài)墊升船舶設(shè)計(jì)有四只空氣舵,空氣舵的舵葉結(jié)構(gòu)為鈦合金骨架、鋁合金肋板及蒙皮混合鉚接結(jié)構(gòu),舵葉兩端的上舵軸、下舵軸為鍛鋼。舵軸與舵葉頂板之間采用鉸制螺栓連接,舵葉蒙皮與鈦合金骨架、鋁合金肋板之間以及鈦合金骨架與鋁合金肋板之間都采用鉚接形式。舵葉通過舵軸安裝在導(dǎo)管空氣螺旋槳尾端的上、下舵承上,左、右舷導(dǎo)管各安裝兩只空氣舵。由于鈦合金、鋁合金的材料特性,舵葉在制造過程中極易產(chǎn)生焊接變形,其焊接及變形控制要求極高;另外,舵葉蒙皮與鈦合金骨架、鋁合金肋板之間以及鈦合金骨架與鋁合金肋板之間的鉚接要求也很高,因而對(duì)舵葉的制造也提出了更高的要求。為了達(dá)到設(shè)計(jì)技術(shù)要求及精度要求,本發(fā)明嘗試提供一種實(shí)用的適合于空氣舵舵葉的制造安裝工藝,首先保證舵葉結(jié)構(gòu)本身的質(zhì)量及強(qiáng)度可靠、滿足制造精度要求,進(jìn)而保證實(shí)船安裝的準(zhǔn)確性、滿足安裝精度要求,為實(shí)船空氣舵的正常、安全運(yùn)轉(zhuǎn)提供技術(shù)基礎(chǔ)保障。
技術(shù)實(shí)現(xiàn)要素:鑒于以上所述現(xiàn)有技術(shù)的缺點(diǎn),本發(fā)明的目的在于提供一種船用空氣舵舵葉的制造安裝工藝,用于解決現(xiàn)有技術(shù)中舵葉在制造過程中極易產(chǎn)生焊接變形,以及舵葉蒙皮與鈦合金骨架、鋁合金肋板之間以及鈦合金骨架與鋁合金肋板之間的鉚接要求高的問題。為實(shí)現(xiàn)上述目的及其他相關(guān)目的,本發(fā)明提供一種船用空氣舵舵葉的制造安裝工藝,舵葉的兩端分別裝有上舵軸、下舵軸,舵葉包括舵葉內(nèi)部框架和蒙皮,舵葉內(nèi)部框架由縱橫交錯(cuò)的鈦合金骨架、鋁合金肋板鉚接而成,蒙皮分為位于舵葉兩側(cè)的上蒙皮、下蒙皮,舵葉的制造安裝工藝包括以下步驟:一)在安裝平臺(tái)上進(jìn)行胎架的制造,胎架設(shè)有胎架模板,胎架模板的表面與舵葉橫剖面型線樣板相適應(yīng);二)制作多根鈦合金骨架,每根鈦合金骨架的槽型主梁采用三段熱模加工成型后的型材進(jìn)行拼接;三)制作多個(gè)鋁合金肋板,每個(gè)鋁合金肋板由鋁合金板采用模壓加工成型;四)根據(jù)舵葉的線型數(shù)據(jù),由鋁合金型材加工出截面為錐形的燕尾刃;五)蒙皮與燕尾刃連接處的線型需按樣板加工,蒙皮的后緣線型放置在胎架模板內(nèi)壓制自然成型;六)舵軸的加工,舵軸的外部端面設(shè)有沿徑向向外延伸的舵軸安裝面,舵軸安裝面上設(shè)有將舵軸安裝面與舵葉加強(qiáng)板安裝在一起的舵軸安裝孔,舵軸插入舵葉內(nèi)部的一端設(shè)有與舵葉內(nèi)部框架配合的鍵槽,舵軸插入舵葉內(nèi)部的端面沿軸線設(shè)有向內(nèi)延伸的定位孔;七)將鈦合金骨架和鋁合金肋板通過連接耳板進(jìn)行鉚接,形成舵葉內(nèi)部框架,將鈦合金骨架、鋁合金肋板、下蒙皮在胎架模板內(nèi)定位,進(jìn)行劃線并配鉆;八)將舵葉內(nèi)部框架、上蒙皮在胎架模板內(nèi)定位,并對(duì)上蒙皮進(jìn)行劃線并配鉆;九)對(duì)舵葉的舵葉內(nèi)部框架進(jìn)行檢查,合格后按圖紙要求將舵葉內(nèi)部框架、上蒙皮、下蒙皮、舵軸進(jìn)行鉚接及裝配。優(yōu)選的,步驟一)具體包括以下步驟:1)胎架制造前先在安裝平臺(tái)上劃出“十”字基準(zhǔn)線,打好標(biāo)記,再按舵葉的圖紙劃出舵軸的中心線、舵葉的外形線以及胎架模板的安裝位置線;2)胎架由豎支撐、斜支撐及水平角鋼平臺(tái)焊接組成,水平角鋼平臺(tái)由縱向水平角鋼、橫向水平角鋼相互交叉焊接而成,豎支撐、斜支撐固定在安裝平臺(tái)和水平角鋼平臺(tái)之間,水平角鋼平臺(tái)上表面與胎架模板用螺栓、螺母固定連接;3)在胎架模板上劃出水平基準(zhǔn)線,并根據(jù)舵葉橫剖面型線樣板劃線、切割,切割邊緣打磨光順;4)胎架制造完工后進(jìn)行檢查,檢查胎架的胎架模板安裝的牢固性,按舵葉橫剖面型線樣板檢查胎架模板的型線的準(zhǔn)確性,檢查舵葉橫剖面型線樣板上的水平線與胎架模板上的水平線的吻合度。優(yōu)選的,步驟七)具體包括以下步驟:1)將舵葉的下蒙皮在胎架模板上鋪設(shè)、定位,在下蒙皮上劃出縱、橫向構(gòu)架線以及首、尾端部肋位線;2)鈦合金骨架事先在胎架模板上預(yù)裝后劃出鉚釘孔位置并在鉆床上鉆出;3)在胎架模板上安裝鈦合金骨架、鋁合金肋板,下蒙皮、鈦合金骨架、鋁合金肋板與胎架模板之間用L型耳板通過螺栓、螺母臨時(shí)固定,再將鈦合金骨架、鋁合金肋板之間通過連接耳板進(jìn)行鉚接,形成舵葉內(nèi)部框架,舵葉的兩端面安裝有用于安裝舵軸的舵葉加強(qiáng)板,在安裝舵葉加強(qiáng)板時(shí)檢查垂直度、水平度;4)將鈦合金骨架上的鉚釘孔在下蒙皮上的對(duì)應(yīng)位置在下蒙皮上標(biāo)出;5)將下蒙皮與胎架模板之間的定位螺栓拆開后翻身,根據(jù)定位孔對(duì)鋁合金肋板與下蒙皮的鉚釘孔進(jìn)行劃線并配鉆;6)將下蒙皮與舵葉內(nèi)部框架拆離,再將下蒙皮上的與鈦合金骨架相配合的鉚釘孔鉆出。優(yōu)選的,步驟八)具體包括以下步驟:1)將上蒙皮在胎架模板上鋪設(shè)、定位,在上蒙皮上劃出縱、橫向構(gòu)架線以及首、尾端部肋位線;2)在上蒙皮上安裝舵葉內(nèi)部框架,上蒙皮、舵葉內(nèi)部框架與胎架模板之間用L型耳板通過螺栓、螺母臨時(shí)固定,將鈦合金骨架上的鉚釘孔在上蒙皮上的對(duì)應(yīng)位置在上蒙皮上標(biāo)出,以便拆開框架后在上蒙皮上鉆孔;3)上蒙皮、舵葉內(nèi)部框架與胎架模板之間的定位螺栓拆開后,將上蒙皮、舵葉內(nèi)部框架翻身,根據(jù)定位孔對(duì)鋁合金肋板與上蒙皮的鉚釘孔進(jìn)行劃線并配鉆;4)將上蒙皮與舵葉內(nèi)部框架拆離,再將上蒙皮上的與鈦合金骨架相配合的鉚釘孔鉆出。優(yōu)選的,步驟九)具體包括以下步驟:1)先將下蒙皮與舵葉內(nèi)部框架進(jìn)行鉚接;2)在舵葉的兩端安裝上舵軸、下舵軸;3)舵葉的內(nèi)表面油漆;4)將上蒙皮與舵葉內(nèi)部框架進(jìn)行鉚接;5)舵葉的上蒙皮、下蒙皮的前緣與燕尾刃焊接。進(jìn)一步的優(yōu)選,步驟2)具體包括以下步驟:ⅰ)檢查位于舵葉的兩端的舵葉加強(qiáng)板表面平整度和垂直度;ⅱ)以拉線定位尺寸為基準(zhǔn),用工裝將舵軸定位,將舵軸插入舵葉內(nèi)部,鍵槽、定位孔與舵葉內(nèi)部框架配合,然后在舵軸的舵軸安裝面與舵葉加強(qiáng)板之間進(jìn)行加工和拂配中間墊片,拂配完成后再配鉸舵軸安裝孔和配制緊固螺栓,并加螺栓防松裝置;ⅲ)舵軸安裝完成后,檢查舵軸的中心線偏差。如上所述,本發(fā)明船用空氣舵舵葉的制造安裝工藝,具有以下有益效果:該船用空氣舵舵葉的制造安裝工藝,零部件加工制造方式合理,裝配方法和順序得當(dāng),易于操作,便于掌握,滿足了空氣舵舵葉結(jié)構(gòu)的設(shè)計(jì)要求及精度要求,實(shí)船安裝后經(jīng)受住了試驗(yàn)、試航的考驗(yàn),因此,本發(fā)明可以廣泛運(yùn)用到船用空氣舵舵葉的制造安裝中。附圖說明圖1顯示為本發(fā)明船用空氣舵舵葉的制造安裝工藝的所制造的舵葉與導(dǎo)管的安裝示意圖。圖2顯示為本發(fā)明船用空氣舵舵葉的制造安裝工藝的所制造的舵葉的結(jié)構(gòu)示意圖。圖3顯示為圖2所示的舵葉的放大示意圖。圖4顯示為圖2所示的舵葉的A-A向示意圖。圖5顯示為圖2所示的舵葉的B-B向示意圖。圖6顯示為圖2所示的舵葉的C-C向示意圖。圖7顯示為圖2所示的舵葉的D-D向示意圖。圖8顯示為本發(fā)明船用空氣舵舵葉的制造安裝工藝中安裝在舵葉兩端的舵軸的結(jié)構(gòu)示意圖。圖9顯示為圖8所示的舵軸的E-E向示意圖。圖10顯示為圖8所示的舵軸的F-F向示意圖。圖11顯示為圖8所示的舵軸的G-G向示意圖。圖12顯示為本發(fā)明船用空氣舵舵葉的制造安裝工藝中所用胎架的結(jié)構(gòu)示意圖。元件標(biāo)號(hào)說明1舵葉11鈦合金骨架12鋁合金肋板13蒙皮131上蒙皮132下蒙皮14連接耳板15燕尾刃16舵葉加強(qiáng)板2舵軸21上舵軸22下舵軸23舵軸安裝孔24舵軸安裝面25鍵槽26定位孔3舵承31上舵承32下舵承4導(dǎo)管41導(dǎo)管尾緣5胎架51豎支撐52斜支撐53橫向水平角鋼54胎架模板6安裝平臺(tái)具體實(shí)施方式以下通過特定的具體實(shí)例說明本發(fā)明的實(shí)施方式,本領(lǐng)域技術(shù)人員可由本說明書所揭露的內(nèi)容輕易地了解本發(fā)明的其他優(yōu)點(diǎn)與功效。本發(fā)明還可以通過另外不同的具體實(shí)施方式加以實(shí)施或應(yīng)用,本說明書中的各項(xiàng)細(xì)節(jié)也可以基于不同觀點(diǎn)與應(yīng)用,在沒有背離本發(fā)明的精神下進(jìn)行各種修飾或改變。請(qǐng)參閱圖1至圖12。需要說明的是,本實(shí)施例中所提供的圖示僅以示意方式說明本發(fā)明的基本構(gòu)想,遂圖式中僅顯示與本發(fā)明中有關(guān)的組件而非按照實(shí)際實(shí)施時(shí)的組件數(shù)目、形狀及尺寸繪制,其實(shí)際實(shí)施時(shí)各組件的型態(tài)、數(shù)量及比例可為一種隨意的改變,且其組件布局型態(tài)也可能更為復(fù)雜。如圖1所示,舵軸2包括上舵軸21和下舵軸22,舵承3包括上舵承31和下舵承32,上舵軸21、下舵軸22分別裝在舵葉1的兩端,上舵軸21、下舵軸22同軸設(shè)置,上舵軸21套在上舵承31中,上舵承31固定在導(dǎo)管4的尾緣41上,下舵軸22套在下舵承32中,下舵承32也固定在導(dǎo)管4的尾緣41上,舵葉1能繞舵軸2的軸線轉(zhuǎn)動(dòng)。如圖2所示,舵葉1的舵葉內(nèi)部框架由縱橫交錯(cuò)的鈦合金骨架11、鋁合金肋板12鉚接而成,然后在舵葉內(nèi)部框架上蒙上蒙皮13形成舵葉1。由于鈦合金、鋁合金的材料特性,舵葉1在制造過程中極易產(chǎn)生焊接變形,其焊接及變形控制要求極高;另外,蒙皮13與舵葉內(nèi)部框架之間以及鈦合金骨架11與鋁合金肋板12之間的鉚接要求也很高,因而對(duì)舵葉1的制造也提出了更高的要求。為解決上述技術(shù)問題,本發(fā)明船用空氣舵舵葉的制造安裝工藝,采用如下技術(shù)方案:一)胎架5的制造1)胎架5在平整的安裝平臺(tái)6上制造,胎架5制造前先在安裝平臺(tái)6上劃出“十”字基準(zhǔn)線,打好標(biāo)記,再按舵葉1的圖紙劃出舵軸2的中心線、舵葉1的外形線以及胎架模板54的安裝位置線,劃線偏差不大于±0.5mm。2)胎架5由豎支撐51、斜支撐52及水平角鋼平臺(tái)焊接組成,水平角鋼平臺(tái)由縱向水平角鋼、橫向水平角鋼53相互交叉焊接而成,豎支撐51、斜支撐52固定在安裝平臺(tái)6和水平角鋼平臺(tái)之間,水平角鋼平臺(tái)上表面與胎架模板54用螺栓、螺母固定連接。其中豎支撐51豎直固定在水平角鋼平臺(tái)的下方;斜支撐52的一端固定在安裝平臺(tái)6上,一端固定在豎支撐51上,斜支撐52從豎支撐51的側(cè)面支撐豎支撐51。3)在胎架模板54上劃出水平基準(zhǔn)線(即舵葉1的中心線),并根據(jù)舵葉橫剖面型線樣板劃線、切割,切割邊緣打磨光順。4)胎架5制造完工后進(jìn)行檢查,確認(rèn)相關(guān)尺寸無誤;檢查胎架5的胎架模板54安裝的牢固性;按舵葉橫剖面型線樣板(該樣板包含蒙皮13的厚度)檢查胎架模板54的型線的準(zhǔn)確性,檢查舵葉橫剖面型線樣板上的水平線(即舵葉1的中心線)與胎架模板54上的水平線的吻合度。二)鈦合金骨架11的制造每根鈦合金骨架11的槽型主梁采用3段熱模加工成型后的型材進(jìn)行拼接,在熱模加工成型時(shí)確保型材成型尺寸、形狀,型材在熱模加工成型后整體進(jìn)行著色檢驗(yàn),拼接時(shí)采用專用工裝,嚴(yán)格控制對(duì)接焊焊接變形。三)鋁合金肋板12的制造根據(jù)舵葉1的設(shè)計(jì)型線數(shù)據(jù)制作專用模具,鋁合金肋板12由鋁合金板采用模壓加工成型,加工時(shí)鋁板折彎角不小于3mm,鋁板加熱溫度控制在150℃-200℃。四)燕尾刃15的加工根據(jù)舵葉1的線型數(shù)據(jù),由鋁合金型材采用铇、銑等工序加工出截面為錐形的燕尾刃15。五)上蒙皮131、下蒙皮132的線型加工蒙皮13分為位于舵葉1兩側(cè)的上蒙皮131、下蒙皮132,蒙皮13與燕尾刃15連接處(即蒙皮13的前緣)的線型需按樣板加工,蒙皮13的后緣線型放置在胎架模板54內(nèi)壓制自然成型。六)舵軸2的加工檢查舵軸2的鍛件尺寸及表面情況后進(jìn)行機(jī)加工,包括車各端面、外圓、圓角、倒角,铇端面四個(gè)直邊,銑腰圓鍵槽,鉆攻螺孔等步驟,舵軸2機(jī)械加工后進(jìn)行調(diào)質(zhì)處理。其中,舵軸2的外部端面設(shè)有沿徑向向外延伸的舵軸安裝面24,舵軸安裝面24上設(shè)有將舵軸安裝面24與舵葉加強(qiáng)板16安裝在一起的舵軸安裝孔23,舵軸2插入舵葉1內(nèi)部的一端設(shè)有與舵葉內(nèi)部框架配合的鍵槽25,舵軸2插入舵葉1內(nèi)部的端面沿軸線設(shè)有向內(nèi)延伸的定位孔26。七)鈦合金骨架11、鋁合金肋板12和下蒙皮132的裝配1)舵葉1的下蒙皮132在胎架模板54上鋪設(shè)、定位,在下蒙皮132上劃出縱、橫向構(gòu)架線以及首、尾端部肋位線。2)鈦合金骨架11事先在胎架模板54上預(yù)裝后劃出鉚釘孔位置并在鉆床上鉆出。3)在胎架模板54上安裝鈦合金骨架11、鋁合金肋板12,下蒙皮132、鈦合金骨架11、鋁合金肋板12與胎架模板54之間用L型耳板通過螺栓、螺母臨時(shí)固定,再將鈦合金骨架11、鋁合金肋板12之間通過連接耳板14進(jìn)行鉚接,形成舵葉內(nèi)部框架,舵葉1的兩端面安裝有用于安裝舵軸2的舵葉加強(qiáng)板16,在安裝舵葉加強(qiáng)板16時(shí)需檢查垂直度、水平度。4)將鈦合金骨架11上的鉚釘孔在下蒙皮132上的對(duì)應(yīng)位置在下蒙皮132上標(biāo)出,以便將舵葉內(nèi)部框架拆離下蒙皮132后在下蒙皮132上鉆孔。5)將下蒙皮132與胎架模板54之間的定位螺栓拆開后翻身,根據(jù)定位孔對(duì)鋁合金肋板12與下蒙皮132的鉚釘孔進(jìn)行劃線并配鉆。6)將下蒙皮132與舵葉內(nèi)部框架拆離,再將下蒙皮132上的與鈦合金骨架11相配合的鉚釘孔鉆出。八)上蒙皮131的裝配1)將上蒙皮131在胎架模板54上鋪設(shè)、定位,在上蒙皮131上劃出縱、橫向構(gòu)架線以及首、尾端部肋位線。2)在上蒙皮131上安裝舵葉內(nèi)部框架,上蒙皮131、舵葉內(nèi)部框架與胎架模板54之間用L型耳板通過螺栓、螺母臨時(shí)固定,將鈦合金骨架11上的鉚釘孔在上蒙皮131上的對(duì)應(yīng)位置在上蒙皮131上標(biāo)出,以便拆開框架后在上蒙皮131上鉆孔。3)上蒙皮131、舵葉內(nèi)部框架與胎架模板54之間的定位螺栓拆開后,將上蒙皮131、舵葉內(nèi)部框架翻身,根據(jù)定位孔對(duì)鋁合金肋板12與上蒙皮131的鉚釘孔進(jìn)行劃線并配鉆。4)將上蒙皮131與舵葉內(nèi)部框架拆離,再將上蒙皮131上的與鈦合金骨架11相配合的鉚釘孔鉆出。九)舵葉1的整體安裝對(duì)舵葉1的舵葉內(nèi)部框架進(jìn)行自檢、專檢,合格后按圖紙要求進(jìn)行鉚接及裝配,主要工序順序:1)先將下蒙皮132與舵葉內(nèi)部框架進(jìn)行鉚接。2)在安裝上舵軸21、下舵軸22。舵軸2的安裝具體包括以下步驟:ⅰ)檢查位于舵葉1的兩端的舵葉加強(qiáng)板16表面平整度和垂直度,如有缺陷進(jìn)行修復(fù)。ⅱ)以拉線定位尺寸為基準(zhǔn),用工裝將舵軸2定位,將舵軸2插入舵葉1內(nèi)部,鍵槽25、定位孔26與舵葉內(nèi)部框架配合,然后在舵軸2的舵軸安裝面24與舵葉加強(qiáng)板16之間進(jìn)行加工和拂配中間墊片,拂配完成后再配鉸舵軸安裝孔23和配制緊固螺栓,并加螺栓防松裝置。ⅲ)舵軸2安裝完成后,檢查舵軸2的中心線偏差。3)舵葉1的內(nèi)表面油漆。4)將上蒙皮131與舵葉內(nèi)部框架進(jìn)行鉚接。5)舵葉1的上蒙皮131、下蒙皮132的前緣與燕尾刃15焊接。舵葉1制造完成后進(jìn)行檢驗(yàn),應(yīng)滿足制造公差要求。綜上所述,本發(fā)明船用空氣舵舵葉的制造安裝工藝,零部件加工制造方式合理,裝配方法和順序得當(dāng),易于操作,便于掌握,滿足了空氣舵舵葉結(jié)構(gòu)的設(shè)計(jì)要求及精度要求,實(shí)船安裝后經(jīng)受住了試驗(yàn)、試航的考驗(yàn),因此,本發(fā)明可以廣泛運(yùn)用到船用空氣舵舵葉的制造安裝中。所以,本發(fā)明有效克服了現(xiàn)有技術(shù)中的種種缺點(diǎn)而具高度產(chǎn)業(yè)利用價(jià)值。上述實(shí)施例僅例示性說明本發(fā)明的原理及其功效,而非用于限制本發(fā)明。任何熟悉此技術(shù)的人士皆可在不違背本發(fā)明的精神及范疇下,對(duì)上述實(shí)施例進(jìn)行修飾或改變。因此,舉凡所屬技術(shù)領(lǐng)域中具有通常知識(shí)者在未脫離本發(fā)明所揭示的精神與技術(shù)思想下所完成的一切等效修飾或改變,仍應(yīng)由本發(fā)明的權(quán)利要求所涵蓋。